分享:選區激光熔化AlSi10Mg-Er-Zr合金微觀組織及力學性能強化
采用氣霧化制粉技術原位合金化制備了AlSi10Mg-Er-Zr粉末,研究了選區激光熔化(SLM)成形AlSi10Mg-Er-Zr試樣的相對密度、微觀組織和力學性能。結果表明,SLM成形AlSi10Mg-Er-Zr試樣的相對密度為99.20%,顯微硬度為156.5 HV,室溫抗拉強度達到461 MPa,屈服強度為304 MPa,相對于常規AlSi10Mg試樣顯微硬度提升了25.8%,抗拉強度和屈服強度分別提高了22.6%和26.7%。這是由于Er、Zr元素的加入,細化了SLM成形AlSi10Mg-Er-Zr試樣的晶粒尺寸,并且使α-Al基體中Si元素的固溶度增加,由細晶強化和固溶強化機制共同作用提高了AlSi10Mg-Er-Zr合金的力學性能。
關鍵詞:
選區激光熔化(selective laser melting,SLM)技術作為近十年發展最快的金屬高精度增材制造(additive manufacturing,AM)技術之一,有著極高的冷卻速率(105~108 K/s),成形合金晶粒極為細小,可顯著強化成形件的力學性能,其AM件具有尺寸精度高、表面質量好、性能優異[1]等特點,在航空航天[2]、醫學研究[3]及醫療器械[4]中得到了一定的應用,同時在藝術設計[5]、汽車工業[6]、國防安全[7]等國民經濟和國家安全核心領域也具有重要的應用前景。
SLM成形AlSi10Mg合金密度小、比強度高、耐腐蝕性好[8],在航空航天、汽車輕量化制造中有廣闊的工程應用需求。相對于其他鋁基合金, AlSi10Mg合金SLM成形性較好,目前SLM件的相對密度可達99.0%以上,抗拉強度可達300~420 MPa,屈服強度達150~270 MPa,延伸率在1.5%~6.0%之間[9~12],可見,SLM成形AlSi10Mg合金力學性能顯著高于傳統鑄造Al-Si合金,因而受到了廣泛的重視。然而,航空航天領域的實際應用對鋁合金的強度有更高要求,所以目前已有的SLM成形AlSi10Mg合金難以滿足對高強鋁合金的需求。因此,進一步提高SLM成形AlSi10Mg合金的力學性能成為國內外的研究熱點,學者們進行了大量的探索研究,包括添加納米碳管[13]、石墨烯[14]以及陶瓷顆粒如:TiB2[15~17]、TiC[18]、TiN[19,20]、WC[21]、SiC[22,23]等強化方法均有報道。不同粉末有不同的強化效果,其成形試樣力學性能均有一定程度的提高。然而,這些復合粉末一般采用機械混粉方法制備,要對復合粉末進行二次加工,而在加工過程中會對粉末的形貌產生一定的影響,導致粉末球型度和粒徑遭到破壞,難以制備出致密和無裂紋的成形件,SLM成形工藝困難,工藝條件要求極為苛刻,難以滿足實際工程應用的需求。
研究[24]發現,SLM成形Al-Mg合金中添加稀土元素取得了很好的強化效果,其中最具代表性的就是添加Sc的Scalmalloy®合金。經過熱處理后,Scalmalloy®合金的抗拉強度可達520 MPa,屈服強度為480 MPa,延伸率為13%。然而,稀土Sc的價格十分昂貴,在大規模生產應用的成本非常高,為此尋求與Sc具有相似的強化效果且價格低廉的稀土元素以實現SLM成形AlSi10Mg合金的強化具有重要的應用價值。稀土Er元素在常規鋁合金中的強化作用已經證實與Sc相似[25]。
為進一步提高SLM成形AlSi10Mg合金的力學性能,采用氣霧化制粉技術原位合金化制備了AlSi10Mg-Er-Zr粉末,研究了SLM成形AlSi10Mg-Er-Zr合金試樣的相對密度、微觀組織和力學性能,并探討了添加Er、Zr元素對SLM成形AlSi10Mg-Er-Zr合金的強化機理。
1 實驗方法
AlSi10Mg-Er-Zr合金粉末采用氣霧化原位合金化方法制備,粉末粒徑為20~53 μm,采用Agilent OES 730電感耦合等離子體發光光譜儀對制備的合金粉末成分進行了分析。為了對比強化的效果,同時進行了常規AlSi10Mg合金粉末的SLM成形,2種粉末的化學成分如表1所示。
表 1 AlSi10Mg-Er-Zr及AlSi10Mg合金粉末化學成分 (mass fraction / %)
Table 1
Alloy | Cu | Fe | Mg | Mn | Ni | Si | Zn | Er | Zr | Al |
---|---|---|---|---|---|---|---|---|---|---|
AlSi10Mg-Er-Zr | ≤ 0.05 | 0.11 | 0.30 | 0.37 | ≤ 0.05 | 9.11 | ≤ 0.10 | 0.64 | 0.41 | Bal. |
AlSi10Mg | ≤ 0.05 | 0.15 | 0.35 | 0.45 | ≤ 0.05 | 9.76 | ≤ 0.10 | - | - | Bal. |
采用M100型金屬選擇性激光熔化3D打印機,基板選用Al基板,在高純度Ar氣保護下進行打印。對于SLM工藝參數進行優化,獲得優化的激光能量密度在46~76 J/mm3之間,研究了激光能量密度對試樣相對密度的影響,在優化的SLM成形工藝參數條件下對添加Er、Zr元素的新型AlSi10Mg-Er-Zr合金以及常規AlSi10Mg合金粉末進行SLM打印成形。
分別采用金相法和Archimedes排水法測試了試樣的相對密度,金相法即選取同一試樣的20張不同位置金相照片,通過Image-Pro plus6.0圖形軟件對照片進行分析,確定SLM成形試樣的相對密度平均值。Archimedes排水法即通過Archimedes原理對試樣的相對密度進行測量,分別測量試樣的干重(g)、濕重(g)以及環境溫度下水的密度(g/cm3)。Archimedes法測得的相對密度值均高于金相法,因此,相對密度數值以金相法測試所得結果進行研究。
對制備好的試樣進行機械研磨、拋光和腐蝕,制備金相試樣,采用的腐蝕劑是Keller試劑(1%HF + 1.5%HCl + 2.5%HNO3 + 95%H2O,體積分數)。采用LEXT OLS4100激光共聚焦顯微鏡以及配有能譜儀(EDS)的GeminiSEM 300場發射掃描電鏡(SEM)對試樣的微觀組織形貌及元素分布進行分析,采用D8 Advance型X射線衍射儀(XRD)對試樣進行物相分析,采用S3400N SEM和NordlysNano的電子背散射衍射(EBSD)設備對試樣進行測試,并使用Channel 5軟件對晶粒尺寸、微觀織構以及Schmid因子進行分析。采用Talos F200X型透射電鏡(TEM)對試樣進行觀察分析,并通過高角環狀暗場(HAADF)探測器對試樣進行進一步分析,采用Gatan 691型離子減薄儀制備TEM試樣。
對于SLM成形AlSi10Mg-Er-Zr及AlSi10Mg試樣以顯微硬度和拉伸性能進行表征。采用HVS-1000型顯微硬度計對SLM成形試樣進行顯微硬度測試,加載載荷為0.980 N,保荷時間為10 s,每個試樣測10個點,通過計算均值得到Vickers顯微硬度。拉伸測試依據ASTM E8M《金屬材料拉伸試驗標準試驗方法》制備室溫拉伸試樣,試樣厚度為3 mm。采用MTS810型拉伸試驗機,在室溫下以拉伸速率1 mm/min進行拉伸測試,每種合金試樣進行3次拉伸實驗,取3次結果的平均值為拉伸性能的數值。
2 實驗結果
2.1 能量密度對成形試樣相對密度的影響
SLM成形AlSi10Mg-Er-Zr試樣的相對密度與激光能量密度的關系如圖1所示。激光能量密度與SLM工藝參數由如下關系:
圖1
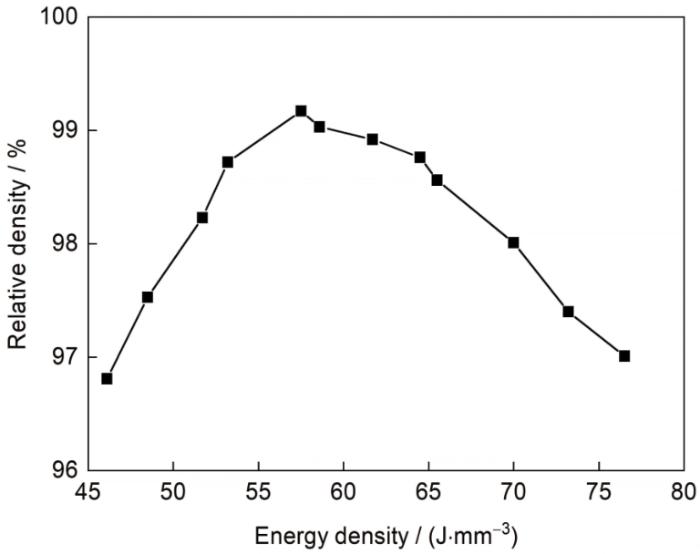
圖1 AlSi10Mg-Er-Zr試樣相對密度與激光能量密度的關系
Fig.1 Relationship between the relative density and the laser energy density of AlSi10Mg-Er-Zr sample
式中,E為能量密度,P為激光功率,v為掃描速率,d為層厚度,h為掃描間距。由圖可見,在能量密度46~76 J/mm3范圍內,SLM成形試樣的相對密度在96.81%~99.20%之間,相對密度隨激光能量密度的增大先增加后減少,在能量密度為57.5 J/mm3時,獲得最高的相對密度為99.20%。這是由于在較低的激光能量密度下,粉末無法獲得足夠的能量,使粉末熔化不充分,SLM成形試樣中存在未熔粉末顆粒,熔池流動性降低,試樣成形質量較差;隨著能量密度的增加,粉末獲得了更高的能量,粉末充分熔化,且熔池內溫度升高,增加了其內部液態金屬的流動性,SLM成形質量提高;然而,隨著激光能量密度的繼續增加,過高的能量密度則會使粉末中的低熔點元素燒損,并且因為熱輸入過高導致SLM成形過程中易產生裂紋、變形等問題[11]。由成形試樣最佳相對密度可知,最佳激光能量密度為57.5 J/mm3,此激光能量密度對應的SLM成形AlSi10Mg-Er-Zr試樣的工藝參數為:P = 92 W,v = 1600 mm/s,h = 0.05 mm,d = 0.02 mm。
2.2 微觀組織
圖2為SLM成形AlSi10Mg-Er-Zr試樣的宏觀組織形貌。可以看出,SLM成形AlSi10Mg-Er-Zr試樣的組織致密,無氣孔、裂紋等缺陷(圖2a)。SLM成形AlSi10Mg-Er-Zr試樣的上表面(X-Y面)組織呈現了“軌道狀”微熔池形貌,如圖2b所示。而試樣側面組織(X-Z和Y-Z面)均呈現了典型的“魚鱗狀”微熔池,但熔池間的深度存在明顯的差異,如圖2c和d所示。這種三維宏觀形貌與文獻[26]報道的SLM成形AlSi10Mg合金組織形貌一致。
圖2
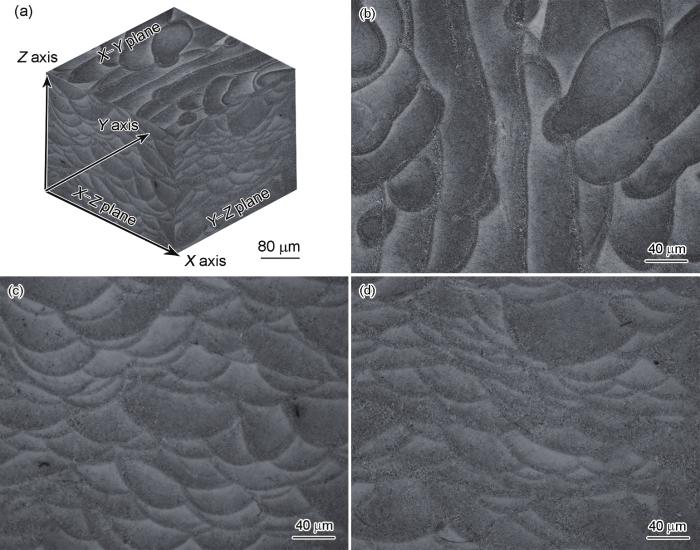
圖2 選區激光熔化(SLM)成形AlSi10Mg-Er-Zr試樣宏觀組織形貌
Fig.2 Macrostructures of AlSi10Mg-Er-Zr sample fabricated by selective laser melting (SLM)
(a) three dimension macrostructure (b) X-Y plane (c) X-Z plane (d) Y-Z plane
SLM成形AlSi10Mg-Er-Zr及AlSi10Mg試樣微觀組織的SEM像如圖3所示。由圖可見,與常規AlSi10Mg試樣相同,SLM成形AlSi10Mg-Er-Zr組織也是由灰色α-Al基體和白色共晶Si相組成,且呈網狀均勻分布。此外,2種合金試樣的組織均呈現了熔池中心、熱影響區及重熔區3個不同區域,但SLM成形AlSi10Mg-Er-Zr試樣的組織更均勻、細小。可見,添加Er、Zr元素有效細化了AlSi10Mg-Er-Zr合金組織。
圖3
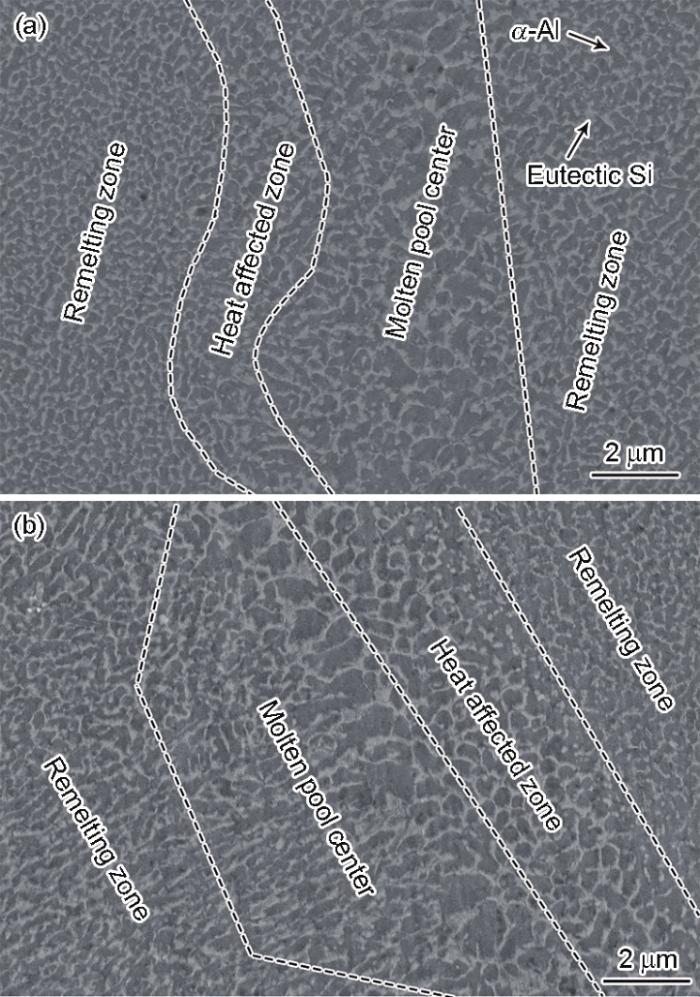
圖3 SLM成形AlSi10Mg-Er-Zr及AlSi10Mg試樣的SEM像
Fig.3 SEM images of AlSi10Mg-Er-Zr (a) and AlSi10Mg (b) samples fabricated by SLM
2.3 物相分析
圖4為SLM成形AlSi10Mg-Er-Zr與AlSi10Mg試樣的XRD譜。由圖可見,2種SLM成形試樣均由α-Al和Si相組成。由于在AlSi10Mg-Er-Zr試樣中Er、Zr元素含量較少,未能達到XRD檢測的最低標準含量5%,因此未能測出含有Er、Zr元素的物相;此外,Mg元素的含量也較少,AlSi10Mg合金的強化相Mg2Si相也未能測出。
圖4
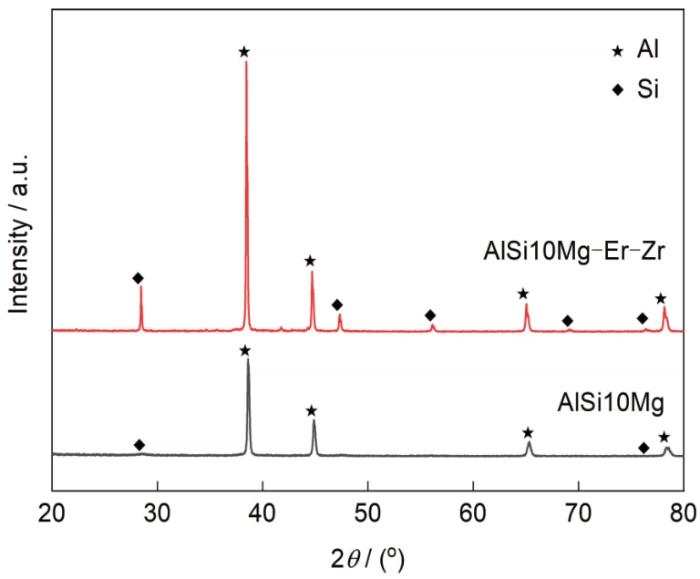
圖4 SLM成形AlSi10Mg-Er-Zr及AlSi10Mg試樣的XRD譜
Fig.4 XRD spectra of AlSi10Mg-Er-Zr and AlSi10Mg samples fabricated by SLM
2.4 力學性能分析
表2為SLM成形AlSi10Mg-Er-Zr與AlSi10Mg試樣的力學性能對比。SLM成形AlSi10Mg-Er-Zr和AlSi10Mg試樣的顯微硬度分別為(156 ± 7)和(124 ± 5) HV。可見,相對于AlSi10Mg合金,SLM成形AlSi10Mg-Er-Zr的顯微硬度提高了25.8%。SLM成形AlSi10Mg-Er-Zr試樣的抗拉強度(UTS)、屈服強度(YS)分別為(461 ± 4)和(304 ± 3) MPa,而常規SLM成形AlSi10Mg試樣的UTS和YS分別為(376 ± 4)和(240 ± 3) MPa。因此,相對于AlSi10Mg合金,SLM成形AlSi10Mg-Er-Zr合金的抗拉強度和屈服強度分別提高了22.6%和26.7%。AlSi10Mg-Er-Zr試樣及AlSi10Mg試樣的延伸率分別為(2.5 ± 0.1)%及(2.6 ± 0.2)%,2者的差別不大,塑性均較低。較低的塑性與已有的SLM成形AlSi10Mg合金報道結果[27]一致。
表2 SLM成形AlSi10Mg-Er-Zr與AlSi10Mg試樣的力學性能
Table 2
Sample | UTS | YS | Hardness |
---|---|---|---|
MPa | MPa | HV | |
AlSi10Mg-Er-Zr | 461 ± 4 | 304 ± 3 | 156 ± 7 |
AlSi10Mg | 376 ± 4 | 240 ± 3 | 124 ± 5 |
3 力學性能強化機理分析
3.1 添加Er、Zr元素對晶粒尺寸的影響
圖5為SLM成形AlSi10Mg-Er-Zr及AlSi10Mg試樣組織的反極圖及晶粒尺寸分布。由圖5a和b可見,2種SLM成形試樣的組織大部分為等軸晶,晶粒取向隨機分布,AlSi10Mg-Er-Zr試樣的晶粒尺寸更為細小。由圖5c可知,AlSi10Mg-Er-Zr試樣組織中85%以上的晶粒尺寸集中在0~2.0 μm之間,平均晶粒尺寸為1.3 μm,而AlSi10Mg試樣組織的晶粒尺寸在0~2.0 μm之間僅占57.4%,平均晶粒尺寸為2.4 μm。這表明添加Er、Zr元素顯著細化了SLM成形AlSi10Mg-Er-Zr試樣的晶粒組織,晶粒尺寸減小了45.8%。圖6為AlSi10Mg-Er-Zr試樣的TEM像和HRTEM像。由圖6a可見,在α-Al晶粒內部有球狀及短棒狀納米粒子析出,由圖6b和c對應的HRTEM像證實其分別為Al3(Er, Zr)相和Mg2Si相。因此,AlSi10Mg-Er-Zr試樣組織晶粒細化的原因是由于添加Er、Zr元素與Al形成納米級Al3(Er, Zr)相,促進α-Al異質形核,并提高鋁合金的再結晶溫度,使其有著很好的熱穩定性[28]。由Hall-Petch公式可知,隨著材料晶粒尺寸的減小,材料的屈服強度提高,因而AlSi10Mg-Er-Zr合金試樣會具有更高的屈服強度及抗拉強度[29]。
圖5

圖5 SLM成形AlSi10Mg-Er-Zr及AlSi10Mg試樣組織反極圖及晶粒尺寸分布圖
Fig.5 Inverse pole figure maps of AlSi10Mg-Er-Zr (a) and AlSi10Mg (b) samples fabricated by SLM and grains size distribution of SLM sample (c)
圖6

圖6 SLM成形AlSi10Mg-Er-Zr試樣TEM像及HRTEM像
Fig.6 TEM image and HRTEM images of AlSi10Mg-Er-Zr sample fabricated by SLM
(a) TEM image of AlSi10Mg-Er-Zr sample
(b) HRTEM image and fast fourier transform (inset) of Al3(Er, Zr) phase
(c) HRTEM image and fast fourier transform (inset) of Mg2Si phase
3.2 添加Er、Zr元素對固溶強化的影響
固溶強化也是SLM成形AlSi10Mg合金的主要強化方式之一,本工作研究了添加Er、Zr元素對α-Al基體中Si含量的影響。SLM成形AlSi10Mg-Er-Zr及AlSi10Mg試樣組織中α-Al基體中Si元素含量的EDS分析結果如圖7所示。AlSi10Mg-Er-Zr合金試樣中Si元素在α-Al中的平均含量為12.17% (質量分數),而AlSi10Mg合金中只有10.93% (質量分數),相對于未添加Er、Zr元素的平均Si含量提高了1.24%,這增加了Si在α-Al相中的固溶強化效果。因此,添加Er、Zr元素后,SLM成形AlSi10Mg-Er-Zr試樣中Si元素在α-Al中的含量增加,提高了AlSi10Mg-Er-Zr合金的固溶強化效果。
圖7

圖7 SLM成形AlSi10Mg-Er-Zr及AlSi10Mg試樣高倍SEM照片及EDS結果
Fig.7 High magnification SEM images and EDS results (mass fraction) of AlSi10Mg-Er-Zr (a) and AlSi10Mg (b) samples fabricated by SLM
為進一步分析SLM成形AlSi10Mg-Er-Zr試樣組織中合金元素的分布,采用TEM對SLM成形AlSi10Mg-Er-Zr試樣組織進行面掃描分析,結果如圖8所示。由HAADF像可知,SLM成形AlSi10Mg-Er-Zr合金組織由網狀分布的共晶Si和顆粒狀的第二相粒子組成。由Al、Si、Mg、Er、Zr元素的分布可知,Si在晶界處富集;而Mg元素彌散分布,但在晶界處有較高的含量,Er元素主要在晶界處富集,少量分布在晶粒內部的第二相粒子處。進一步證實了添加Er、Zr元素與Al形成納米級Al3(Er, Zr)相在晶內析出,且數量相對較多,而Mg2Si相在晶界或晶內少量析出。
圖8

圖8 SLM成形AlSi10Mg-Er-Zr試樣中合金元素分布
Fig.8 Alloying element distributions of AlSi10Mg-Er-Zr sample fabricated by SLM
(a) high angle annular dark field (HAADF) image of area scanning region (b) element distribution map
(c) Al element (d) Si element (e) Mg element (f) Er element (g) Zr element
3.3 添加Er、Zr元素對Schmid因子的影響
圖9為SLM成形AlSi10Mg-Er-Zr及AlSi10Mg試樣組織的Schmid因子分布圖,圖中不同顏色對應不同大小的Schmid因子。可以看出,SLM成形AlSi10Mg-Er-Zr和AlSi10Mg試樣組織中大部分晶粒具有較高的Schmid因子,處于軟位向,易發生滑移。在AlSi10Mg-Er-Zr和AlSi10Mg試樣中,Schmid因子在0.4~0.5之間的含量分別為90.4%和94.7%,表明AlSi10Mg-Er-Zr試樣中具有較高Schmid因子的晶粒數量較少。由于Taylor因子與Schmid因子互為倒數,因此,AlSi10Mg-Er-Zr試樣中高Taylor因子的比例高于AlSi10Mg試樣。眾所周知,Taylor因子表明晶體抵抗塑性變形的能力,Taylor因子越大,說明變形需要大量的滑移,消耗大的形變功[30]。因此,AlSi10Mg-Er-Zr試樣能夠抵抗更高的屈服應力和抗拉應力,具有更高的屈服強度和抗拉強度。
圖 9
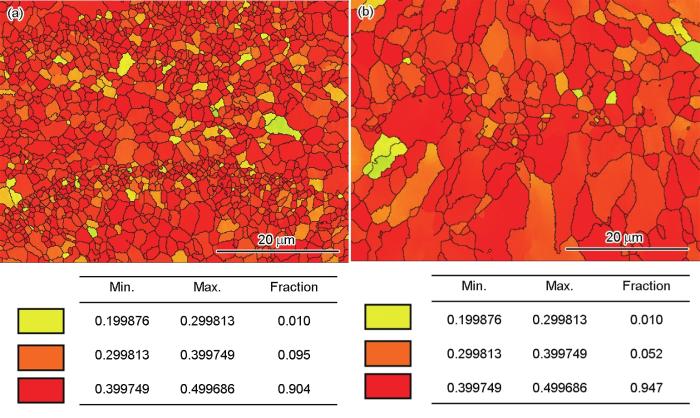
圖 9 SLM成形AlSi10Mg-Er-Zr與AlSi10Mg試樣Schmid因子分布圖
Fig.9 Schmid factor distribution maps of AlSi10Mg-Er-Zr (a) and AlSi10Mg (b) samples fabricated by SLM
3.4 添加Er、Zr元素對微觀織構的影響
圖10為SLM成形AlSi10Mg-Er-Zr及AlSi10Mg試樣的微觀織構分布圖,其中各織構的含量如表3所示。依據文獻[31],對于fcc結構的鋁合金材料而言,Cu織構取向的晶粒發生變形所需的能量最高,即需要更多的外加應力使材料發生塑性變形,而Goss織構和Cube織構取向的晶粒發生變形所需的能量較低,即在較低的外加應力下材料就可以發生塑形變形。對比2種SLM成形試樣的織構及所占含量,發現AlSi10Mg-Er-Zr試樣中Cu織構的比例為3.63% (體積分數),Goss織構和Cube織構占4.04% (體積分數),而AlSi10Mg試樣中Cu織構的比例僅為2.33% (體積分數),Goss織構和Cube織構卻有14.71% (體積分數)。可以看出,SLM成形AlSi10Mg-Er-Zr試樣具有更多的Cu織構以及更少的Goss織構和Cube織構,發生塑性變形所需的外加應力更高。因此,SLM成形AlSi10Mg-Er-Zr試樣組織中晶粒的Cu織構含量增加,減少了Goss織構和Cube織構,從而進一步提高了AlSi10Mg-Er-Zr試樣的力學性能。
圖10

圖10 SLM成形AlSi10Mg-Er-Zr與AlSi10Mg試樣織構分布圖
Fig.10 Texture component distribution mapping of AlSi10Mg-Er-Zr (a) and AlSi10Mg (b) samples
表3 SLM成形AlSi10Mg-Er-Zr與AlSi10Mg試樣織構含量 (volume fraction / %)
Table 3
Sample | Cube | Goss | R | P | Shear | Brass | Copper | S |
---|---|---|---|---|---|---|---|---|
AlSi10Mg-Er-Zr | 2.81 | 1.23 | 7.13 | 5.63 | 3.53 | 3.41 | 3.63 | 1.08 |
AlSi10Mg | 11.70 | 3.01 | 7.62 | 1.40 | 6.10 | 6.41 | 2.33 | 1.83 |
4 結論
(1) 在優化的SLM成形工藝參數條件下,AlSi10Mg-Er-Zr試樣的相對密度最高為99.20%,且無宏觀裂紋、孔隙缺陷,在X-Y面的宏觀組織呈現“軌道狀”微熔池,在X-Z面以及Y-Z面顯示為“魚鱗狀”形貌。
(2) SLM成形AlSi10Mg-Er-Zr試樣微觀組織由島狀分布α-Al基體和網狀均勻分布的共晶Si相組成,相對于常規AlSi10Mg試樣組織更加細小,且添加Er、Zr元素并未造成AlSi10Mg-Er-Zr合金元素的偏析。AlSi10Mg-Er-Zr試樣平均晶粒尺寸為1.3 μm,相對于AlSi10Mg試樣晶粒尺寸減小了45.8%,添加Er、Zr元素細化晶粒的效果顯著。
(3) SLM成形AlSi10Mg-Er-Zr試樣抗拉強度為(461 ± 4) MPa,屈服強度為(304 ± 3) MPa,顯微硬度(156 ± 7) HV,相對于AlSi10Mg合金,分別提高了22.6%、26.7%和25.8%。
(4) SLM成形AlSi10Mg-Er-Zr試樣的Schmid因子在0.4~0.5之間的比例為90.4%,相對于常規SLM成形AlSi10Mg試樣具有更多比例的高Taylor因子,具有更多高形變能量的Cu織構及更少的低形變能量的Goss、Cube織構,在發生塑性變形時需要更高的外加應力,抵抗塑性變形的能力更強,因此SLM成形AlSi10Mg-Er-Zr試樣具有更高的屈服強度和抗拉強度。
來源--金屬學報