分享:SUS316不銹鋼馬鞍形管-管接頭的殘余應力數值模擬及高效計算方法開發
基于MSC. Marc有限元軟件平臺,針對SUS316馬鞍形管-管焊接頭的焊接殘余應力預測,開發了2種能同時兼顧精度與效率的計算方法。第1種方法建立了與實際接頭尺寸一致的全模型,采用移動熱源與瞬間熱源混合使用的方法,即采用移動熱源模擬打底與蓋面焊道的熱輸入,采用瞬間熱源模擬填充焊道熱輸入;第2種方法利用接頭幾何形狀的對稱性,建立了1/4局部模型,并采用瞬間熱源模擬全部焊道的熱輸入。由于SUS316加工硬化效應顯著,在材料模型中采用各向同性硬化準則來考慮加工硬化,同時采用階躍式退火模型來模擬材料的退火軟化。比較計算結果和實驗結果可知,不論是典型位置的焊接熱循環還是接頭的殘余應力分布,數值模擬結果與實驗結果均吻合較好。采用全模型既可以得到整個接頭的殘余應力分布也可以獲得始終端位置應力分布特征。局部模型也能準確預測穩定區域應力的大小和分布,并可以大幅節省計算時間和存儲空間。
關鍵詞:
奧氏體不銹鋼具有優越的綜合力學性能與抗腐蝕性能,因此成為核電裝備中關鍵部件的最主要結構材料之一。在制造過程中,奧氏體不銹鋼部件通常采用熔焊方法進行連接。近年來,國際原子能機構IAEA (International Atomic Energy Agency)的調查結果表明,在現有運行的400余套核電機組中,為數不少的焊接接頭(包括奧氏體不銹鋼接頭)中檢測出了應力腐蝕裂紋[1,2]。已有研究[3~5]表明,除了材料敏化和腐蝕環境外,拉伸應力被認為是導致奧氏體不銹鋼接頭產生應力腐蝕裂紋的重要因素之一。應力腐蝕裂紋的產生會給核電設備的安全穩定運行帶來嚴重的威脅。焊接制造過程局部的快速加熱和冷卻會產生很高的殘余應力,其峰值在焊縫及熱影響區往往會達到甚至超過材料的屈服極限,這會導致這些區域更易產生應力腐蝕裂紋。到目前為止,盡管有10多種實驗方法(包括無損檢測方法、半有損法和有損檢測法)可以用于獲得焊接接頭與結構的殘余應力,但是由于實驗手段自身的局限性,采用這些方法只能獲得有限位置的應力分布情況,很難全面地獲得整個焊接接頭或結構的殘余應力分布。1971年,Ueda和Yamakawa[6]首次提出了熱-彈-塑性有限元方法來計算焊接殘余應力,基于熱-彈-塑性有限元方法的數值模擬技術彌補了實驗手段的不足,這種方法可以獲得整個焊接接頭或結構的殘余應力分布與大小。進入21世紀后,該方法已經廣泛應用于實際工程結構中焊接接頭和結構的殘余應力預測[7~9]。但是,由于焊接過程具有非穩態、非線性以及多物理場交互作用的特點,若再加上焊接結構的接頭數量多、結構復雜以及尺寸厚大等特點,在采用熱-彈-塑性有限元方法計算焊接殘余應力時需要耗費更多的計算資源和更長的計算時間,很多情況下甚至會超出計算硬件能力范圍而不能實施計算。
針對如何以現有商用有限元軟件為平臺來高效、高精度地計算焊接殘余應力的工程需求,一些學者對此展開了研究。戴培元等[10]采用三維全尺寸模型和二維軸對稱模型分別計算了管-管對接接頭的焊接殘余應力,通過對比發現,二維軸對稱模型也能較高精度地預測焊接殘余應力,且能大幅節約計算時間和存儲空間。Pu等[11]分別采用瞬間熱源和移動熱源對厚大平板對接接頭進行了焊接殘余應力的數值模擬,計算結果表明,瞬間熱源除了具備耗時少的優點外,其殘余應力的計算結果與移動熱源的計算結果也有較好的吻合度。胡興等[12]在對厚大板材進行多層多道焊時,采用合并焊道的方法來計算接頭的焊接殘余應力,該方法不僅可以節約計算時間,而且得到的殘余應力與實驗結果也吻合較好。
在實際工程中如果遇到厚大復雜結構,且不能進行降維(如:由三維簡化為二維)簡化時,往往需要在具體問題具體分析的基礎上提出能兼顧計算時間與精度的方法來獲取焊接結構的殘余應力。本工作的研究對象是SUS316馬鞍形管-管接頭,這種結構是壓水堆核電站中第二水循環系統中的典型結構。該接頭具有尺寸大、管壁厚和焊道多的特點,且馬鞍形焊縫的坡口大小及局部拘束條件隨位置的不同而發生變化。理論上,這類馬鞍形接頭不適合采用降維簡化法來計算焊接殘余應力。到目前為止,關于馬鞍形管-管復雜接頭的殘余應力數值模擬的研究并不多見,以往研究者們研究的馬鞍形管-管焊接接頭尺寸都相對較小,且焊道數量較少。張敏等[13]采用生死單元方法對6道焊的馬鞍形管-管接頭進行了數值計算,但是該研究對結果的報道相對簡略,甚至未給出整個焊接接頭的應力分布云圖。Katsuyama等[14]采用移動熱源對尺寸較小的馬鞍形管-管接頭進行了數值模擬,但在該研究中,作者并未考慮材料的加工硬化與退火軟化效應,也沒有將計算結果與實測值進行比較。從所能查閱的公開文獻來看,對于厚大的馬鞍形管-管接頭焊接殘余應力的數值模擬和實驗測量的比較未見報道。
針對SUS316馬鞍形管-管厚大焊接接頭,為了提高計算精度和計算效率,本工作以商用有限元軟件MSC. Marc為平臺,開發了2種焊接殘余應力的計算方法。第1種方法建立與實際接頭尺寸一致的尺寸全相同的模型,采用移動熱源與瞬間熱源混合使用的方法,兼顧效率與精度——即采用移動熱源模擬打底與蓋面焊道的熱輸入,采用瞬間熱源模擬填充焊道熱輸入;第2種方法則利用接頭模型幾何形狀的對稱性,簡化模型為1/4局部模型,并采用瞬間熱源模擬全部焊道的熱輸入。本工作在得到SUS316馬鞍形管-管接頭整體殘余應力分布的同時,對比了這2種方法計算得到的典型位置的焊接熱循環和殘余應力分布,同時,將計算結果與實驗測量結果進行比較,并驗證了所開發計算方法的可靠性。此外,還分析了這2種計算方法各自的優缺點及它們的工程適用性。
1 實驗方法
1.1 焊接實驗
SUS316馬鞍形管-管垂直相貫接頭(下稱馬鞍形管-管接頭)由臺管(圖1a)和母管(圖1b) 2個部分組成。兩構件間的坡口為U形坡口,該U形坡口形狀會隨著構件位置變化發生變化,但是坡口的間距相差不大,在打底完成后,上表面坡口寬度范圍在33.6~35.2 mm之間。馬鞍形管-管接頭的照片如圖1c所示,其整體管尺寸如圖1d所示。馬鞍形管-管接頭的特征尺寸如下:母管的長度為850.0 mm,內徑為609.6 mm,壁厚為38.9 mm,臺管上端面與母管的距離為296.1 mm,臺管的外徑為184.1 mm,壁厚為46.0 mm,鞍型焊道最外端部距母管端面距離為284.2 mm。臺管為鍛造結構件,它與母管的材料均為SUS316奧氏體不銹鋼,焊接填充材料為Y316L,它們的化學成分如表1所示。圖2是U形坡口實際焊接時的焊道布置,焊道布置為16層51道,焊接方法為鎢極惰性氣體保護焊,焊接參數如表2所示。焊接時,層間溫度控制在100℃以下。在圖2中,A、B、C和D 4個點是用于測量焊接過程溫度循環的熱電偶位置,其中A、B位置在母管的內表面上,它們分別與第一道焊縫中心線的距離為10和15 mm,C、D位置在母管的外表面上,它們與第46道焊趾的距離分別為5和10 mm。
圖1
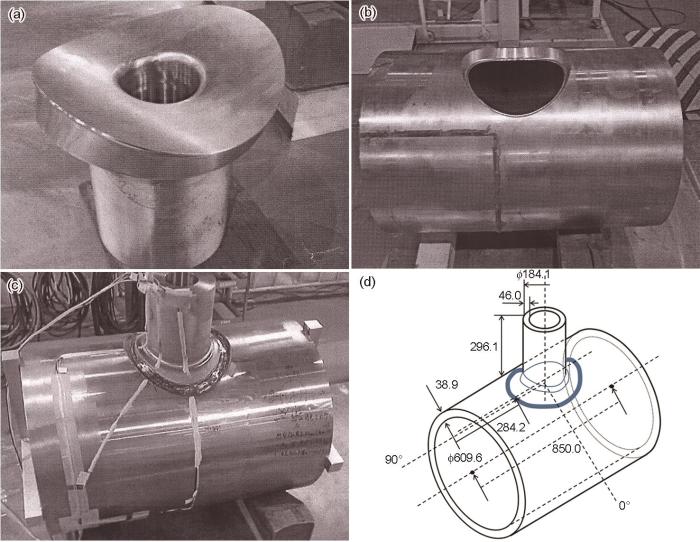
圖1 SUS316臺管、母管、管-管接頭的照片及特征尺寸示意圖
Fig.1 Photographs of a vice-tube (a), a circular pipe (b), and a saddle tube-pipe joint (c), the dimension diagram of the tube-pipe welded joint (unit: mm) (d)
表1 SUS316母材及Y316L焊材的化學成分 (mass fraction / %)
Table 1
Material | C | Si | Mn | P | Ni | Cr | Mo | S | Fe |
---|---|---|---|---|---|---|---|---|---|
SUS316 | 0.08 | 1.00 | 2.00 | 0.045 | 12-14 | 16-18 | 2-3 | < 0.002 | Bal. |
Y316L | 0.04 | 0.33 | 1.88 | < 0.019 | 12.70 | 19.30 | 2.26 | < 0.002 | Bal. |
圖2

圖2 焊道布置及熱電偶位置示意圖
Fig.2 Schematic of an arrangement of weld passes and locations of thermo-couples
表2 各焊道焊接速率、熱輸入及電弧效率
Table 2
Layer number | Bead number | Welding speed / (mm·min-1) | Heat input / (kJ·cm-1) | Arc efficiency |
---|---|---|---|---|
1 | 1 | 48.5 | 7.2 | 0.57 |
2, 3 | 2-5 | 103.4-127.6 | 7.1-12.1 | 0.7 |
4-11 | 6-28 | 151.5-192.6 | 15.7-16.7 | 0.7 |
12-14 | 29-40 | 216.1-216.6 | 13.5-13.7 | 0.7 |
15, 16 | 41-51 | 225.5-249.7 | 11.8-12.9 | 0.7 |
1.2 應力測量方法及位置
焊接完成后,采用切片法[15]來獲取馬鞍形管-管接頭90°與180°截面上、下表面的焊接殘余應力。采用切片法測量殘余應力時,需先將應變片貼于工件表面,然后采用線切割方法將貼片處附近的材料切成小片(本實驗為4 mm × 4 mm × 4 mm),來獲取釋放的彈性應變,最后再通過理論計算得到殘余應力[15]。應變片位置布置示意圖如圖3所示,圖3a為俯視示意圖,圖3b為90°與180°橫截面應變片布置示意圖。為了方便后續討論,90°上下表面測量位置與180°上下表面測量位置,分別用line 1、line 2、line 3和line 4表示,如圖3b所示。
圖3

圖3 應變片位置俯視圖及各截面應變片位置示意圖
Fig.3 Schematics of strain gauge locations in top view (a), and strain gauge locations in 90° and 180° cross-section (b)
2 有限元計算方法
基于MSC. Marc軟件平臺,本工作建立了2種計算馬鞍形管-管接頭殘余應力的有限元方法,為了方便后續討論,這2種有限元計算模型分別用Model 1和Model 2表示。第1種方法(Model 1)建立了與實際焊接工件尺寸完全一致的三維有限元網格模型,如圖4a所示。在模擬焊接熱輸入時,坡口下部打底焊道(第1條焊道)和緊接著的第2、3焊道及上部的第46~51蓋面焊道采用移動熱源模型,其余填充焊道均采用瞬間熱源模型。第2種方法(Model 2)為了更進一步提高計算效率與節省計算儲存空間,根據該接頭幾何形狀的對稱性簡化為1/4局部模型,如圖4b所示,并在對稱面上設置絕熱邊界條件與對稱位移拘束,所有焊道均采用瞬間熱源進行溫度場計算。Model 1與Model 2的焊道布置如圖5所示。焊道采用“生死單元”的方式進行激活。采用移動熱源模型時,當熱源移動到當前材料位置時,對應的單元被依次激活;當采用瞬間熱源時,當前焊道對應的所有單元同時被激活。
圖4
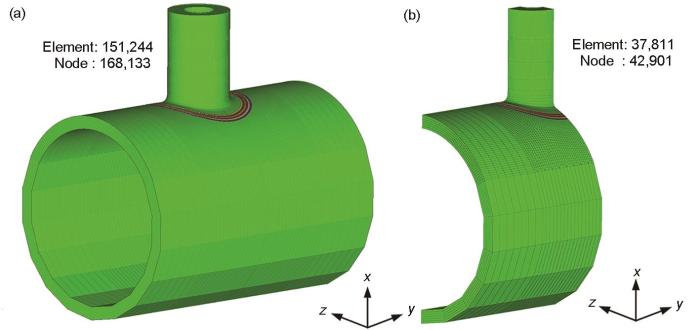
圖4 全尺寸(Model 1)和1/4尺寸(Model 2)有限元網格模型
Fig.4 Schematic finite element models of full size model (Model 1) (a) and a quarter model (Model 2) (b)
圖5
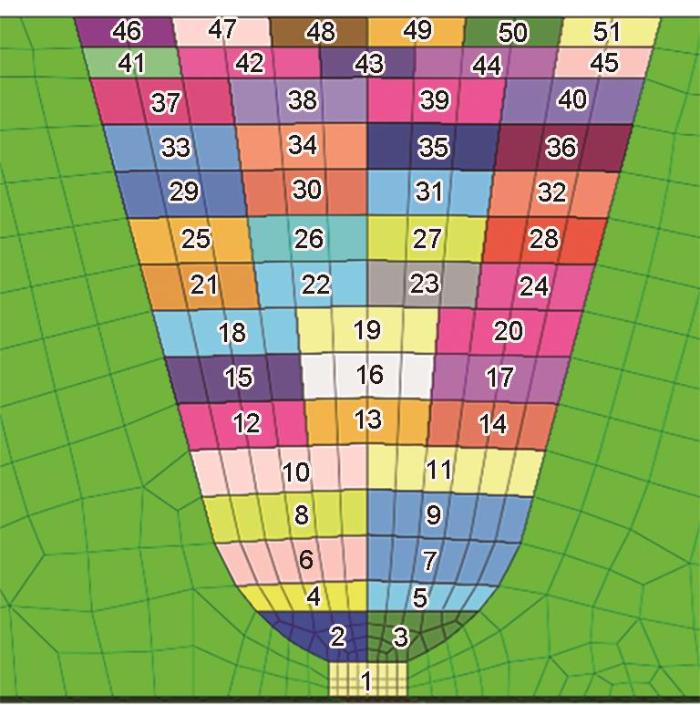
圖5 有限元模型中焊道布置
Fig.5 Arrangement of weld beads in the finite element models
2.1 溫度場計算
在Model 1中采用移動熱源來計算打底焊道和蓋面焊道的溫度場,本工作采用了Goldak雙橢球熱源模型[16]來模擬焊接熱輸入。在該模型中,前、后半部分的熱流密度(qf和qr)分布分別定義為[16]:
式中,Q = ηUI (其中,Q為電弧功率(W),η為電弧熱效率,U為電弧電壓(V),I為焊接電流(A));af、ar、b和c為橢球形狀參數;ff和fr為前、后橢球熱量分配系數,且ff + fr = 2,在本研究中,取ff = 0.6,fr = 1.4。
理論上而言,對于多層多道的焊接構件,所有焊道采用移動熱源模型來模擬熱輸入可以獲得更接近于實際情況的溫度場、殘余應力和變形。但是,本工作中的馬鞍形管-管接頭具有焊接道數多和焊道軌跡復雜的特點,如果全部采用移動熱源需要消耗大量的計算資源和冗長的計算時間。為了解決上述矛盾,本研究在可變長度熱源模型[17]的基礎上,提出了“移動熱源+瞬間熱源”混合計算法,即采用移動熱源模型來模擬打底焊道和蓋面焊道的熱輸入,采用瞬間熱源模型來模擬中間填充焊道的熱輸入。這樣的處理方式,既可以大幅節省計算時間和存儲空間,也可以兼顧計算精度。
本工作采用的“瞬間熱源模型”是一個等密度體積熱源[18],其熱源長度為整條焊道的長度,橫截面積與對應的焊道截面面積相等,加熱方式為把整條焊道定義為內部熱源并同時加熱。該熱源模型是在保證每條焊道的總熱量與實際的總熱量不變的情況下,通過調整加熱時間th (s)和熱流密度qv (J/(mm3·s2)),使得焊接熔池的最高溫度控制在一個合理的范圍以及熔池截面控制在一定面積內[19]。th為整條焊縫的假定加熱時間,一般設定在數秒的時間范圍內[20],qv由
式中,L為整條焊縫的長度(mm),v為移動熱源焊接速率(mm/s),V為該整條焊道的體積(mm3)。
2.2 應力場計算
應力與變形計算采用熱-彈-塑性有限元計算法,即計算各個節點溫度場后,再將其以熱載荷加載到結構分析有限元模型中,從而求解整個焊接過程的位移、應變和應力,本工作采用的SUS316材料高溫熱物理性能和高溫力學性能參數見文獻[10]。
金屬材料在焊接過程中熱-冶金-力學的耦合行為非常復雜,在焊接熱循環作用下,理論上材料的應變包括彈性應變、塑性應變、熱應變、相變應變(固態組織轉變引起的應變)和蠕變應變等成分。由于本工作采用的母材和焊接填充材料均為奧氏體不銹鋼,不需要考慮固態相變問題。此外,焊接過程中加熱和冷卻速率都較快,這樣在高溫停留的累積時間相對較短,所以蠕變應變的影響也可以忽略不計[21]。對于SUS316鋼,材料的總應變增量(Δεtotal)可以表達為:
式中,Δεe為彈性應變增量,Δεth為熱應變增量,Δεp為塑性應變增量。
材料模型中,假定彈性行為遵循各向同性Hook定律[22],塑性行為遵循Von Mises屈服準則[22]。以往的研究[23]表明,SUS316奧氏體不銹鋼是一種加工硬化較顯著的材料,若不考慮加工硬化效應,得到的殘余應力將遠低于實際水平;若采用各向同性硬化準則考慮不銹鋼的加工硬化,但不考慮退火軟化效應,焊接數值模擬得到的應力結果會高于實驗結果。因此本工作中,同時采用各向同性加工硬化模型和“階躍式”退火軟化模型考慮SUS316不銹鋼的加工硬化和退火軟化計算焊接殘余應力。各向同性硬化法則中,流變應力與塑性應變(εp)有關,在模擬殘余應力時,本工作采用的SUS316奧氏體不銹鋼不同溫度與不同塑性應變對應的流變應力如表3[24]所示。采用“階躍式”模型來考慮退火軟化效應時,退火溫度設置為900℃[25]。
表3 SUS316不銹鋼各向同性硬化準則模型參數[24]
Table 3
T / oC | σs | σ0.01 | σ0.05 | σ0.1 | σ0.3 |
---|---|---|---|---|---|
920 | 216.5 | 295.6 | 398.9 | 441.8 | 500.5 |
275 | 158.0 | 223.6 | 320.9 | 363.0 | 422.1 |
550 | 131.5 | 188.2 | 280.7 | 321.3 | 378.9 |
750 | 105.9 | 147.9 | 207.0 | 226.4 | 248.9 |
900 | 93.1 | 103.7 | 107.0 | 107.5 | 107.5 |
1000 | 31.8 | 31.8 | 31.8 | 31.8 | 31.8 |
1100 | 19.7 | 19.7 | 19.7 | 19.7 | 19.7 |
1400 | 2.1 | 2.1 | 2.1 | 2.1 | 2.1 |
1500 | 2.1 | 2.1 | 2.1 | 2.1 | 2.1 |
3 結果與分析
3.1 焊接熱循環
為了比較分別由數值模擬和實驗手段獲得的焊接熱循環,選取母管上4個代表位置(圖2中A、B、C和D點)來輸出熱循環曲線,這4個位置均在母管的90°截面上。A、B位置在第1道焊接過程中的溫度循環曲線如圖6a所示,C、D位置在第46道焊接過程中的溫度循環如圖6b所示。從圖6可以看出,盡管計算值與實驗值在局部有些許差異,但整體而言,不論是各點的峰值溫度還是升溫和降溫過程都與實驗結果比較吻合。從數值模擬結果與實測值的比較可知,不管是移動熱源模型+瞬間熱源模型的Model 1,還是采用純瞬間熱源的Model 2計算得到的溫度循環與實驗結果均吻合較好。因此,可以推測,采用瞬間熱源也能較高精度預測焊接殘余應力,而且能大幅節約計算時間。
圖6

圖6 焊接溫度循環結果和實驗結果的比較
Fig.6 Comparison between simulated and experimental results for the welding temperature as a function of time
(a) the 1st pass (the measurement locations at points A and B (inset))
(b) the 46th pass (the measurement locations at points C and D (inset))
3.2 焊接殘余應力
為了與實驗結果進行定量比較和便于分析殘余應力的分布特征,對殘余應力計算結果進行了坐標變換,即將直角坐標系(x, y, z)轉換為圓柱坐標(r, θ, z1) (其中,r方向為徑向方向(應力實驗中橫向應力方向),θ方向為周向方向(應力實驗中縱向應力方向),z1方向為軸向方向(為徑向與周向共同決定平面的法向方向))。坐標變換及柱坐標原點位置如圖7所示。柱坐標轉化后,沿著r方向的應力為徑向殘余應力,沿著θ方向的殘余應力為周向殘余應力,z1方向的殘余應力為軸向殘余應力。
圖7

圖7 殘余應力結果坐標系變換(直角坐標轉柱坐標)
Fig.7 Schematic showing the transformation from the coordinate to cylindrical coordinate for the residual stress (r—direction of transverse residual stress, θ—direction of longitudinal residual stress, z1—the axial direction)
3.2.1 周向殘余應力
圖8為Model 1與Model 2的整體周向殘余應力(類似平板接頭的縱向殘余應力)分布云圖。總體上而言,這2個模型計算得到的周向殘余應力的分布形態十分相似。在Model 1 (圖8a)的外表面焊縫始終端位置(0°)可以清晰地看到該處的應力分布與其他位置有較顯著的差異。而在Model 2 (圖8b)中,由于全部焊道采用瞬間熱源模型及對稱的熱邊界和力學邊界條件,因此沿著焊縫周向方向的殘余應力,不會像Model 1在0°處出現不連續現象,故而呈現出光滑的連續分布特征。圖9為Model 1在0°、90°、180°和270°截面上焊縫及其附近區域的周向殘余應力分布云圖。從4個截面上應力分布云圖可以看到,焊縫及其附近的周向殘余應力都為拉應力,最后一道焊縫位置及其附近區域的殘余應力最大,該處峰值應力達到甚至超過600 MPa。由于蓋面焊道采用了移動熱源,加之各個截面處的內拘束不同,4個截面上的應力分布也有所不同,不過分布形態基本相似,峰值應力的大小和所在位置也基本相同。
圖8
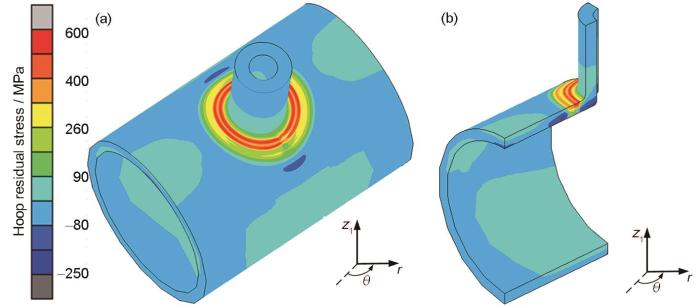
圖8 焊接完成后Model 1與Model 2整體周向殘余應力分布云圖
Fig.8 Overall hoop residual stress distributions after welding for Model 1 (a) and Model 2 (b)
圖9

圖9 Model 1典型截面上的周向殘余應力云圖
Fig.9 Hoop residual stress distributions in the characteristic cross-sections for Model 1
(a) 0° (b) 90° (c) 180° (d) 270°
圖10中的Model 2在90°和180°截面上的周向殘余應力分布與圖9b (Model 1的90°截面)和圖9c (Model 1的180°截面)的周向殘余應力的分布基本一致,這說明采用1/4部分模型也能較高精度地獲得周向殘余應力。
圖10
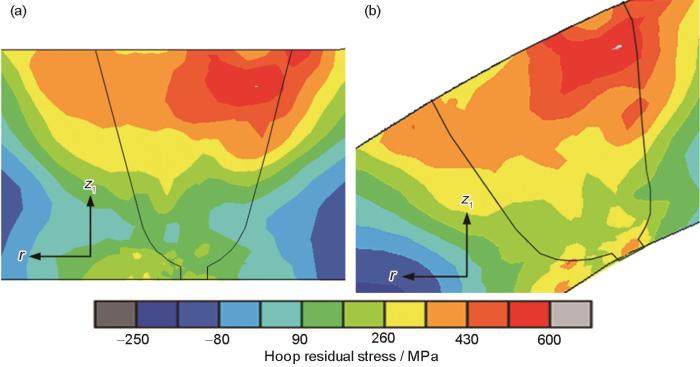
圖10 Model 2典型截面上的周向殘余應力云圖
Fig.10 Hoop residual stress distributions in the characteristic cross-sections for Model 2
(a) 90° (b) 180°
圖11為管-管接頭在90°截面的上表面(line 1)和下表面(line 2)的周向殘余應力分布,該圖比較了數值模擬結果與實驗測量結果。在line 1上的應力分布如圖11a所示,在-20~0 mm范圍內,2種模型的計算結果與實驗測量結果吻合很好。在-10 mm附近,周向殘余應力達到最大值,2種模型計算得到的最大值和實驗測量得到的最大值分別為534、547和506 MPa。Model 1的計算結果在0~15 mm范圍內低于實驗值,平均低了約40 MPa。Model 2的計算結果在15~25 mm范圍內高于實驗測量結果,平均高了約50 MPa;應力分布形態與測量結果基本一致。總體上來看,在line 1上數值模擬結果得到的應力分布與實驗值一致。line 2上的周向殘余應力分布如圖11b所示,從此圖可知,整體上而言實驗值與計算值具有較高的吻合度。
圖11

圖11 90°處上(line 1)下(line 2)表面周向殘余應力實驗值與計算值
Fig.11 Experimental and numerical results of the hoop residual stress in 90° cross-section, located at line 1 (a) and line 2 (b) (Insets show the measuring directions)
圖12為180°截面的上表面(line 3)和下表面(line 4)的周向殘余應力分布,此圖比較了數值模擬結果與實驗測量結果。位于line 3上的應力分布如圖12a所示,在-15~0 mm的區間,數值模擬結果與實驗測量值吻合良好,而在0~15 mm的范圍內實驗值要明顯高于數值模擬結果,而且Model 2的預測結果與實驗值更接近一些。在line 3上,實驗、Model 1和Model 2的最大值分別為529、543和530 MPa,3者的峰值非常接近。位于line 4上的周向殘余應力分布如圖12b所示,Model 1與Model 2的計算結果與測量結果的分布形態及數值的大小都吻合良好。
圖12
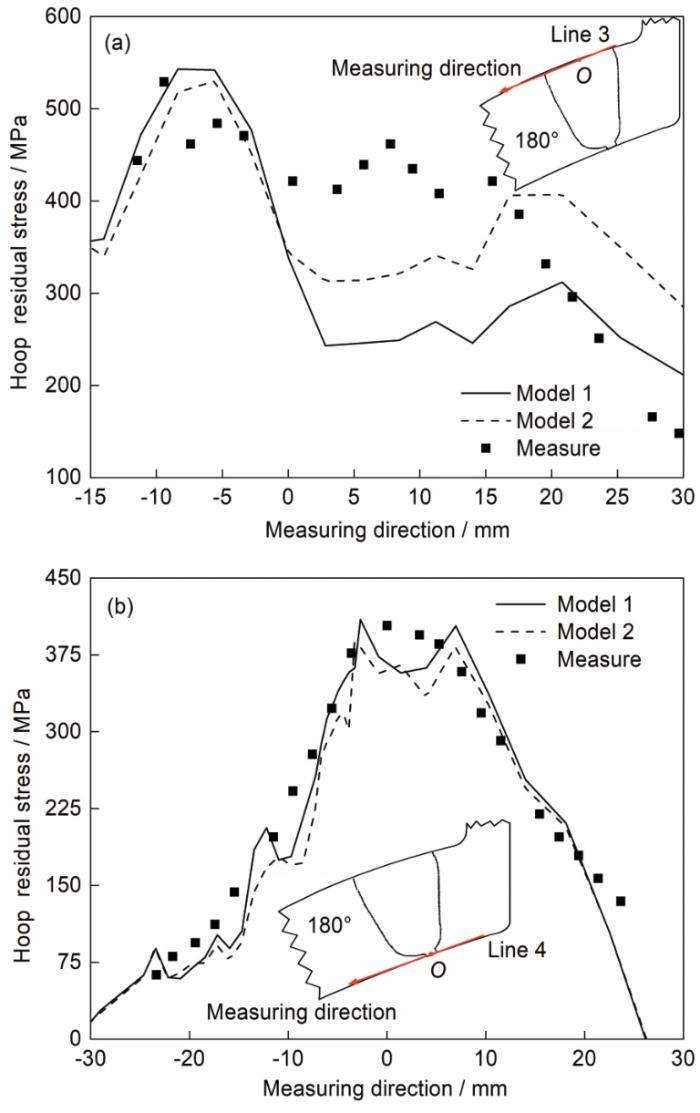
圖12 180°處上(line 3)下(line 4)表面周向殘余應力實驗值與計算值
Fig.12 Experimental and numerical results of the hoop residual stress in 180° cross-section, located at line 3 (a) and line 4 (b) (Insets show the measuring directions)
圖11和12中的周向殘余應力實驗測量結果與數值計算結果存在一定程度的差異,但在應力峰值、最小值及分布形態上基本一致,整體上而言,實驗測量結果驗證了Model 1與Model 2周向殘余應力計算的準確性。上述的比較表明,采用Model 2的方法,也能較高精度地模擬厚大管-管接頭的周向殘余應力。
圖13為焊縫中心線line 5上周向殘余應力的分布。圖中5條曲線分別表示了第2、6、9、12和16層焊接完成時的周向殘余應力分布。從此圖可以看到一個有趣的周向應力的演化過程,即隨著焊接進行,焊道的增加,沿著焊縫中線的周向應力的大小和分布在不斷發生變化。也就是說,后焊焊道對先焊焊道產生的應力分布有顯著的影響。對于下表面焊縫中心位置的周向應力而言,隨著焊道數增加,其值有不斷減小的趨勢。產生這種變化趨勢主要是因為接頭本身板厚較厚,加之焊道數和焊接層數較多,周向應力分布除了在與焊縫中線垂直方向(橫向方向)上產生平衡外,在厚度方向也產生平衡。
圖13

圖13 周向殘余應力沿中心線分布(90°截面上不同焊層完成后)
Fig.13 Hoop residual stress distributions along the welding centerline in 90° section after welding at different layers (Inset shows the measuring direction)
3.2.2 徑向殘余應力結果
圖14a和b分別為Model 1與Model 2整體徑向殘余應力(類似平板接頭的橫向殘余應力)分布云圖。整體上而言,Model 1與Model 2殘余應力分布形態非常相似,但在Model 1的外表面焊縫始終端位置(0°)可以清晰地看到徑向殘余應力分布與周向殘余應力呈現相似的不光滑的局部區域。而Model 2中,由于全部焊道采用瞬間熱源模型及對稱的熱邊界和力學邊界條件,故徑向方向的殘余應力呈現出光滑連續的分布特征。
圖14

圖14 焊后Model 1與Model 2整體徑向殘余應力分布云圖
Fig.14 Overall radial residual stress distributions for Model 1 (a) and Model 2 (b)
圖15為Model 1在0°、90°、180°和270°截面上焊縫及其附近區域的徑向應力分布云圖。徑向殘余應力在焊縫上表面為拉應力,且呈現出離焊縫越近拉應力越高的特征。根據Dong[26]的研究,管-管對接環焊縫在軸向方向(與子母線平行的方向)應力(在本工作中為徑向應力)的分布,可分為彎曲型(bending-type)和自平衡型(equilibrating-type) 2種類型。本工作雖然是馬鞍型接頭,但它也有類似于環焊縫的一些特征,其沿厚度方向上的徑向殘余應力呈現拉-壓-拉的分布特征,類似于厚大尺寸環焊縫自平衡類型[10]。對0°、90°、180°和270°不同截面位置的徑向應力分布比較可知,90°與270°截面的徑向殘余應力大小與分布均非常相似,同時0°與180°截面的徑向殘余應力大小與分布也非常相似;而90°與180°截面位置徑向殘余應力有顯著的差異。因此可以推測,對于該馬鞍形管-管接頭而言,采用從90°至180°截面區域的1/4模型即可描述整體結構的徑向殘余應力分布。
圖15

圖15 Model 1典型截面上的徑向殘余應力云圖
Fig.15 Radial residual stress distributions in the characteristic cross-sections for Model 1
(a) 0° (b) 90° (c) 180° (d) 270°
圖16a和b分別為Model 2在90°和180°截面上焊縫及其附近區域的徑向殘余應力分布云圖。與圖15b中的90°截面和圖15c中的180°截面上的徑向殘余應力分布比較可以看出,Model 1與Model 2的徑向殘余應力分布及大小基本一致。
圖16
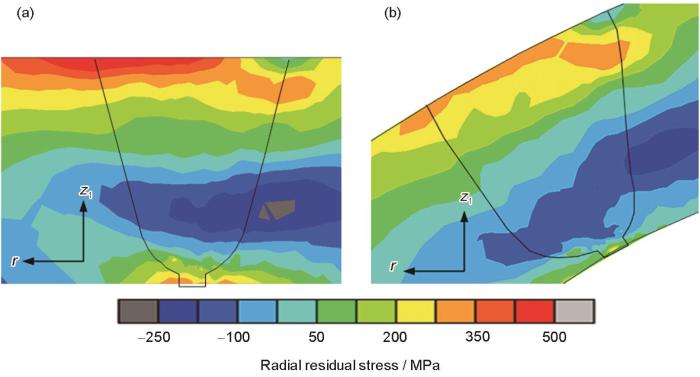
圖16 Model 2典型截面上的徑向殘余應力云圖
Fig.16 Radial residual stress distributions in 90° (a) and 180° (b) cross-sections for Model 2
圖17為90°截面的上表面(line 1)和下表面(line 2)上徑向殘余應力分布。圖17a為line 1上的徑向殘余應力分布,整體上看2者的分布形態基本一致,2者的峰值拉伸應力位置也很接近。實驗測量的最大值為448 MPa,相同位置Model 1的值為451 MPa,Model 2的值為484 MPa;在-20 mm處實驗測量的最小值為128 MPa,相同位置上Model 1與Model 2的值分別為41和25 MPa。在90°截面位置的下表面line 2上的徑向殘余應力分布如圖17b所示,可以看到,無論是應力分布形態還是大小,數值模擬結果與實驗結果吻合良好。整體上而言,實驗值略高于計算值。在line 2上,實驗測量最大值為393 MPa,而Model 1與Model 2對應的計算值分別為367和348 MPa,實驗與計算得到的殘余應力峰值和分布吻合較好。
圖17
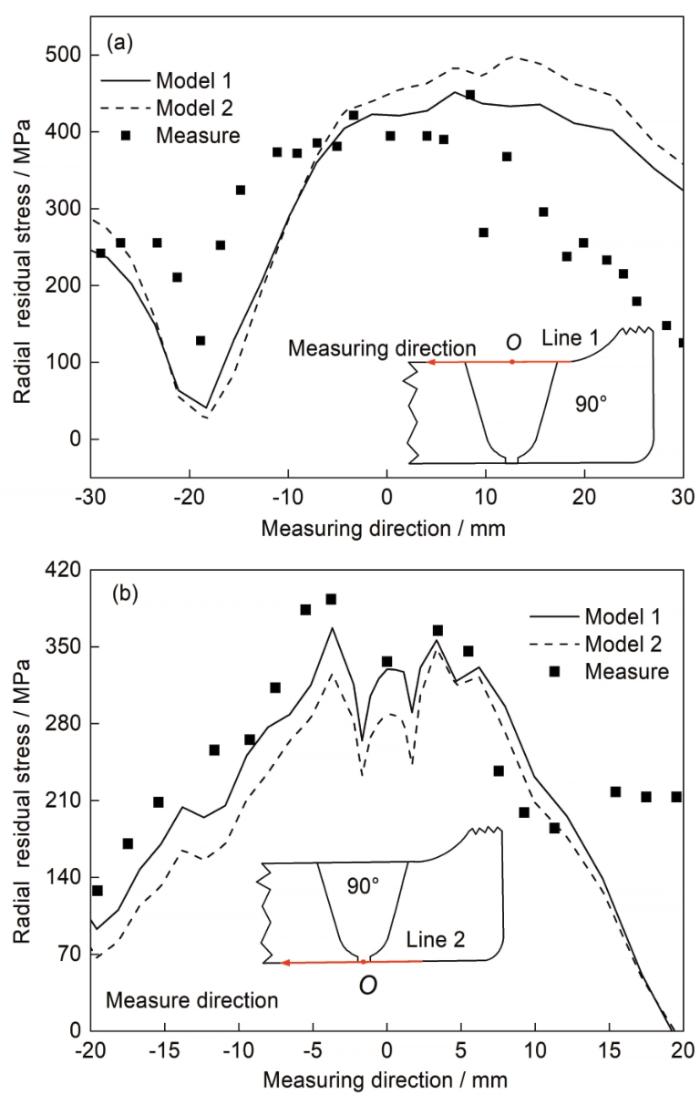
圖17 90°處上(line 1)下(line 2)表面徑向殘余應力實驗值與計算值
Fig.17 Experimental and numerical results of radial residual stress in 90° cross-section, located at line 1 (a) and line 2 (b) (Insets show the measuring directions)
圖18為180°截面的上表面(line 3)和下表面(line 4)上的徑向殘余應力分布圖。line 3上的徑向應力分布如圖18a所示,在-30~0 mm范圍內,數值模擬結果與實驗測量值之間存在較大的差異,但在0~30 mm范圍內,數值模擬結果與實驗值在分布形態和大小上均吻合較好。line 4上的徑向殘余應力分布如圖18b所示,可以看到,計算結果與測量結果吻合很好,整體上而言,實驗值略高于計算值。
圖18

圖18 180°處上(line 3)下(line 4)表面徑向殘余應力實驗值與計算值
Fig.18 Experimental and numerical results of radial residual stress in 180° cross-section, located at line 3 (a) and line 4 (b) (Insets show the measuring directions)
圖17和18中徑向殘余應力的實驗結果與數值模擬結果盡管存在一定程度的差異,但是從應力分布形態和峰值應力大小上看,2者吻合較好,實驗測量結果驗證了Model 1與Model 2徑向殘余應力計算的準確性。上述比較表明,即使采用Model 2也能較準確地獲得管-管接頭的徑向殘余應力大小與分布。
圖19為焊縫中心線line 5上徑向殘余應力的分布。圖中5條曲線分別表示了第2、6、9、12和16層焊接完成時的徑向殘余應力分布。隨著焊接進行,焊層數的增加,沿著焊縫中線的徑向應力的大小和分布不斷發生變化,這說明后焊焊道對先焊焊道產生的徑向應力分布有顯著的影響。隨著焊道數的增加,下表面焊縫中心位置的徑向應力呈現出先減小隨后又增加的趨勢,沿著焊縫中線的徑向應力在焊接過程中的演化過程與周向應力的演化過程有明顯的不同,前者先減小后增大,而后者隨著焊道增加又有一直減小的趨勢。出現這種現象是因為徑向應力分布除了在與焊縫中線垂直方向(橫向方向)上產生平衡外,在厚度方向也產生平衡。
圖19
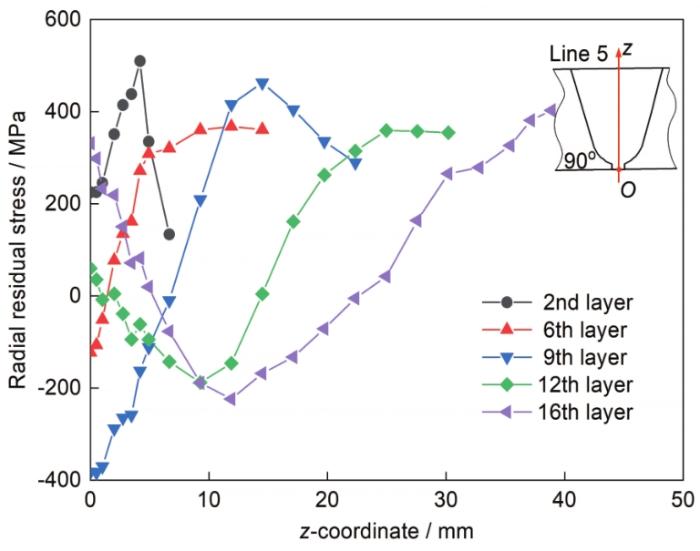
圖19 徑向殘余應力沿中心線分布(90°截面上不同焊層完成后)
Fig.19 Radial residual stress distributions along the welding centerline in 90° section after welding different layers (Inset shows the measuring direction)
3.3 計算時間與儲存空間
下面對2種方法的計算效率進行定量比較。2個模型的計算均在i9-9900K (CPU參數為8核16線程,主頻為4.7 GHz) 的計算機上完成,采用移動熱源模型計算第1道焊的應力時所花費的時間為9.65 h,第2道焊的時間花費9.68 h,第3道焊用時為9.69 h。從數值上看,3個焊道計算時間的差異較小,平均每個焊道的計算時間為9.67 h。根據前3道的所用計算時間可以得到這樣一個推測,全模型+全移動熱源模型,51道全部采用移動熱源模型來計算焊接應力,所需計算時間約為493 h。當采用Model 1來計算焊接應力時,實際花費時間為137 h,而采用Model 2,計算時間僅僅為8.4 h。單純從計算時間上看,采用全模型及全焊道移動熱源模型花費的時間最長;采用Model 1的計算時間居中,所用時間僅為前者的27.7%;而采用Model 2的計算時間最少,以全模型+全移動熱源模型為參照,所用的計算時間僅為它的1.9%。
從所需的存儲空間而言,Model 1與Model 2所需的儲存空間分別為1604和191 GB。比較而言,采取Model 2可大大節約儲存空間?;谟嬎銜r間和儲存空間的比較,Model 2具備更強的工程應用潛力。
3.4 討論
本工作采用Model 1和Model 2計算了厚大馬鞍形管-管焊接接頭的溫度場和殘余應力,并與實驗結果進行了比較。不論是典型位置的焊接熱循環還是焊縫及其附件區域的殘余應力,數值模擬結果與實驗測量值總體上吻合良好。
3.4.1 計算誤差
數值模擬得到的殘余應力與實驗測量結果盡管在峰值應力和分布形態上基本一致,但依然存在一定程度的差異。通過分析,主要的原因如下:
(1) 初始材料狀態難考慮。在實際制備母管和臺管時,材料經過固溶處理、矯正變形及機械加工等焊前的工序,這些工序可能會產生不同程度的塑性變形以及初期殘余應力,在有限元模型中這些焊前材料初始狀態沒有被考慮,從而產生誤差。
(2) 實驗測量殘余應力帶來的誤差。實驗測量采用應力釋放法進行殘余應力測量時,需要在測量位置進行應變片的粘貼。在應變片粘貼前,需要將測量位置打磨平整,由于在180°截面的位置存在一定弧度,故而需要在基體上打磨掉的材料較多,才能達到平整的效果。在這個過程中,打磨較多會對焊縫位置引入額外的塑性應變,使測量結果出現誤差。從位置看,在180°處因打磨造成的誤差可能會更大。
(3) 有限元計算模型誤差。在材料模型中,本工作采用“各向同性硬化模型”和“階躍式退火模型”來分別考慮加工硬化和退火軟化效應,而實際的材料會出現包辛格(Bauschinger)效應,同時軟化效應與時間和溫度都有密切關系。在本工作采用的材料模型中,上述的問題沒有完整地考慮,在今后的研究中,需要開發更高精度的材料模型。
3.4.2 應力峰值
實驗測量結果和計算結果均顯示,在焊接后接頭中存在大于550 MPa的高拉應力區,而SUS316不銹鋼的常溫屈服強度僅為220 MPa,應力峰值遠遠超過了材料的常溫屈服強度。出現如此高的拉伸殘余應力的主要原因如下:
(1) SUS316奧氏體不銹鋼的加工硬化效應顯著。在焊接過程中,焊縫金屬及其附近的母材都要經歷峰值溫度較高的熱循環,由于焊縫及其附近的材料在升溫和降溫過程中產生的熱應變要受到周圍溫度相對較低金屬的拘束作用而發生塑性變形,塑性變形的產生致使材料發生加工硬化而提高流變應力。
(2) 由于本工作中的焊接接頭板厚較厚,而且形狀相對復雜,因此焊縫處的三向內拘束較大。在內拘束大的情況下,焊接過程中容易產生多軸(二軸或三軸)拉伸應力,這樣會導致材料不易屈服。
實驗結果表明,金屬塑性屈服準則中最接近實際條件的是Von Mises屈服準則[27]。在本工作的數值模擬中材料模型也是采用的Von Mises屈服準則。Von Mises屈服準則中規定金屬屈服條件是在第一主應力(σ1)、第二主應力(σ2)和第三主應力(σ3)共同作用下,材料會發生屈服,其遵循
式中,σs為屈服強度。
圖20

圖20 SUS316不銹鋼空間Von Mises屈服面與平面Von Mises屈服面及其擴大示意圖
Fig.20 Schematics of SUS316 Von Mises yield surface in the triaxial stress state (a) and the Von Mises yield surface expansion in the biaxial stress state (b) (σ1—major principal stress, σ2—second principal stress, σ3—third principal stress, σs—yield strength, σ
若只考慮2個應力,可假設σ3 = 0時,
圖21

圖21 Model 1模型90°截面等效Von Mises應力
Fig.21 Equivalent Von Mises stress distributions in 90° cross-section for Model 1
采用的加工硬化及退火軟化模型計算得到殘余應力,與實驗得出的殘余應力接近,驗證了材料模型準確性。從計算結果和實驗結果來看,由于對模型熱源的簡化和對材料模型的近似處理,使該模型占用的計算資源較少,同時計算時間也大幅縮短?;趹Ψ植夹螒B及峰值應力實驗結果有較高吻合度的事實,從面向工程應用的角度出發,本工作開發的2種計算手法具有較高的工程應用價值。
4 結論
(1) 基于通用有限元軟件,針對結構較大、焊道布置復雜的SUS316馬鞍形管-管接頭溫度場和殘余應力的計算,開發了全尺寸有限元網格模型+“移動熱源+瞬間熱源”混合計算模型(Model 1)以及1/4部分網格有限元模型+全焊道瞬間熱源模型(Model 2)。計算結果與實驗結果吻合較好,驗證了2種模型的可行性和妥當性。
(2) Model 1能計算出整體結構焊接時的殘余應力,并且也能抓住始終端位置的應力分布特征;Model 2雖然不能模擬始終端位置的應力,但可以較準確地獲得除始終端位置及其附近以外區域的殘余應力,而且計算時間可大幅縮短,存儲空間也能大幅減少。在實際的工程應用中,對于厚大焊接接頭或結構的焊接殘余應力,若不重點考慮始終端位置的應力特征,可以利用結構的對稱性簡化模型,同時采用瞬間熱源模型來模擬焊接熱輸入,這種方法可以兼顧計算精度并能大幅提高計算效率。
(3) 從數值模擬結果和實驗測量結果來看,焊縫及其附近的殘余應力呈現出多軸拉伸的特征,局部位置的單向(周向)應力達到了600 MPa,遠遠高于材料常溫時的屈服極限。產生如此高的殘余應力的原因主要有兩點,一是SUS316材料有較顯著的加工硬化傾向,另一個是在厚大接頭焊接時內拘束強,而引起的多軸應力效應。
來源--金屬學報