分享:淬火速率對7136鋁合金應力腐蝕開裂敏感性的影響
馬志民1,2,3, 鄧運來1,3, 劉佳2, 劉勝膽,1,3, 劉洪雷4
1.
2.
3.
4.
針對7xxx系鋁合金的抗應力腐蝕性能對淬火速率敏感的問題,通過浸入式末端淬火和慢應變速率拉伸實驗研究了淬火速率對7136鋁合金應力腐蝕開裂(SCC)敏感性的影響規律。結果顯示,隨著淬火速率的減小,合金的SCC敏感性先增高后降低,淬火速率約為5.3℃/s時的SCC敏感性最高;SCC裂紋擴展方式由穿晶擴展轉變為沿晶擴展。淬火速率越小淬火析出相越多,尺寸越大,晶界和亞晶界附近的無沉淀析出帶越寬。淬火速率大于5.3℃/s時,晶界析出相中Zn、Mg元素含量隨淬火速率減小迅速增加,而淬火速率小于5.3℃/s后,Cu元素含量迅速增加。晶界和亞晶界析出相形貌特征以及晶界析出相化學成分的變化是SCC敏感性隨淬火速率減小先增加后降低的主要原因。
關鍵詞:
Yuan等[9]通過評價裂紋擴展速率發現7xxx系鋁合金的SCC敏感性在淬火速率8~150℃/s區間內隨著淬火速率的減小而降低。Xie等[7]采用分級淬火的方法發現淬火速率越小,7097鋁合金的SCC敏感性越低,認為隨著淬火速率減小,晶界附近的無沉淀析出帶(PFZ)增寬,晶界析出相(GBP)中Cu含量的增加,均會降低裂紋擴展速率。Jiang等[10]對比了7046鋁合金在空氣淬火(1.4℃/s)與水淬火(80℃/s)條件下的SCC敏感因子,發現隨淬火速率減小SCC敏感性增高,認為這是隨淬火速率減小晶界PFZ增寬后更容易被溶解造成的。Chen等[11]通過對比伸長率的損失發現7085鋁合金的SCC敏感性在淬火速率1~150℃/s區間內隨淬火速率減小先降低再升高,認為淬火速率大于50℃/s時,GBP的尺寸和間距增大降低了SCC敏感性;而淬火速率小于50℃/s后,GBP中Cu含量的降低提高了SCC敏感性。Xiao等[12]通過評價強度的損失發現過時效態7xxx鋁合金的SCC敏感性在淬火速率5~130℃/s區間內隨淬火速率減小先降低再升高,而峰時效態合金的SCC敏感性隨淬火速率的減小而降低,認為GBP的面積分數起了決定性作用,GBP面積分數小于22.3%時SCC敏感性隨淬火速率減小而降低,高于22.3%后則隨淬火速率減小而升高。
本工作以7136鋁合金為對象,通過浸入式末端淬火的方法獲得大范圍連續變化的淬火速率,結合慢應變速率拉伸(SSRT)實驗中獲得的強度、伸長率和斷裂時間等數據綜合研究淬火速率對該合金SCC敏感性的影響規律,并探討微觀組織特征對SCC的影響機理。這可以深化人們對7xxx系鋁合金SCC敏感性的理解,為調控材料性能提供參考。
1 實驗方法
實驗材料為16 mm厚的7136鋁合金擠壓板材,實測化學成分(質量分數,%)為Al-9.10Zn-2.18Mg-2.07Cu-0.13Zr,Fe < 0.08,Si < 0.05。為準確表述實驗過程及試樣位置,建立三維坐標系,定義板材的擠壓方向(ED)為x軸,橫向(TD)為y軸,法向(ND)為z軸。從板材上沿ED切取長度和寬度分別為360和170 mm的試樣置于SX-4-10型箱式電阻爐中進行雙級固溶,制度為450℃、1 h + 470℃、0.5 h。固溶后在2 s內將試樣轉移至室溫(約25℃)水槽中進行浸入式末端淬火,TD垂直于水面,試樣浸入水中深度為25 mm,其余部分位于空氣中。圖1為浸入式末端淬火示意圖,圖中藍色表示水中的部分,灰色表示空氣中的部分。在試樣TD-ND面z = 8 mm處沿y軸的不同位置鉆出8個直徑為1.5 mm、深度為10 mm的小孔預埋熱電偶。使用QT-6-K高精度測溫儀采集末端淬火過程中的時間-溫度曲線,數據采集頻率為20 Hz。待試樣完全冷卻至室溫后,立即在SX2-9-12TP箱式電阻爐中進行120℃、24 h的人工時效。
圖1
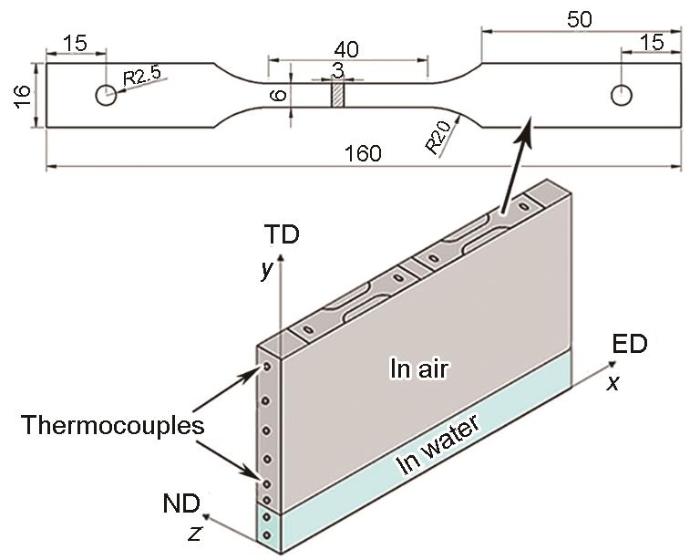
圖1 末端淬火示意圖及慢應變速率拉伸試樣尺寸
Fig.1 Schematic of end quenching and drawing of slow strain rate tensile sample (unit: mm; ED—extruded direction, ND—normal direction, TD—transverse direction; blue indicates the part in the water, gray indicates the part in the air)
按照HB 7235-95標準在YYF-100型慢應變速率應力腐蝕試驗機上執行SSRT實驗。在板材ND-ED面沿y軸連續切取厚度為3 mm的試樣,具體尺寸見圖1。取試樣中心位置所對應的y軸淬火速率作為名義淬火速率。每組平行樣為3個,應變速率為1 × 10-6 s-1,腐蝕介質為3.5%NaCl (質量分數)溶液,惰性介質為硅油。通過試驗機自帶的加熱裝置將介質溫度控制在(50 ± 2)℃。實驗結束后,分析不同試樣的應力-應變曲線、斷裂時間等數據。
使用EVO MA10掃描電子顯微鏡(SEM,加速電壓20 kV)觀察試樣的斷口形貌,再在斷口處取樣,觀察和分析斷裂位置附近(ED-TD面)的腐蝕裂紋特征,并統計腐蝕裂紋數量,測量最大腐蝕深度。在板材不同位置切取試樣觀察第二相特征,并使用X-MaxN能譜分析儀(EDS)對第二相粒子進行成分分析。電子背散射衍射(EBSD)分析在配有EBSD探頭的EVO MA10 SEM上進行。試樣經過機械拋光后進行電解拋光,電解電壓為15 V,時間約為10 s,拋光液為10%HClO4 + 90%C2H5OH (體積分數)的混合溶液。使用HKL Channel 5軟件處理EBSD數據。使用Titan G2 60-300掃描透射電子顯微鏡(STEM)在高角環形暗場像(HAADF)模式下觀察微觀組織特征,重點觀察晶界(GB)和亞晶界(SGB)上析出相等特征,使用Super-X型EDS檢測GBP的化學成分,束斑尺寸為2 nm,加速電壓300 kV。STEM樣品預磨至80 μm厚后,使用沖孔器沖成直徑為3 mm的圓片后進行雙噴減薄,雙噴液為20%HNO3 + 80%CH3OH (體積分數),使用液氮將溫度控制在-20℃以下。
2 實驗結果
2.1 時間-溫度曲線與淬火速率
圖2
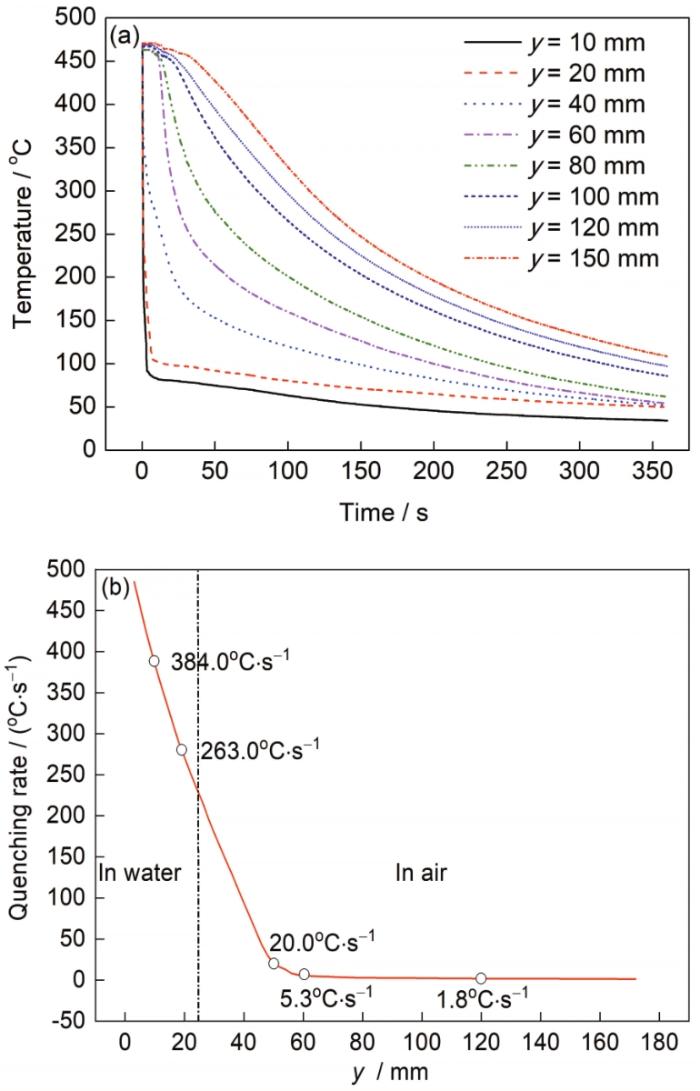
圖2 7136鋁合金試樣不同位置的時間-溫度曲線與平均淬火速率
Fig.2 Cooling curves and average quenching rates at different positions of the 7136 aluminum alloy sample
(a) time-temperature curve
(b) average quenching rate
2.2 SSRT實驗結果
實驗結果表明,7136鋁合金試樣的強度隨著淬火速率的減小而降低,伸長率則升高。作為代表給出淬火速率為263.0、5.3和1.8℃/s時7136鋁合金試樣的應力-應變曲線,如圖3所示。淬火速率為263.0℃/s試樣的強度最高,硅油和NaCl溶液中的強度分別約為537.0和523.1 MPa,而伸長率最低,分別約為15.1%和13.4%。淬火速率為5.3℃/s試樣的強度和伸長率居中,硅油和NaCl溶液中強度分別為478.2和458.3 MPa,伸長率分別為15.7%和14.2%。淬火速率為1.8℃/s試樣的強度最低,而伸長率最高,硅油和NaCl溶液中的強度分別為395.0和391.5 MPa,伸長率分別為24.5%和22.3%。
圖3
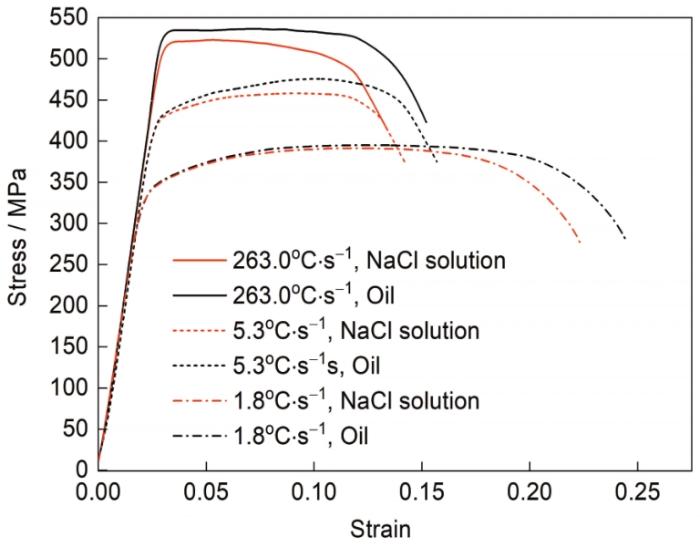
圖3 淬火速率為263.0、5.3和1.8℃/s時7136鋁合金試樣的應力-應變曲線
Fig.3 Stress-strain curves of the 7136 aluminum alloy samples under quenching rates of 263.0, 5.3, and 1.8oC/s
由此可知,試樣在硅油中的拉伸性能均高于NaCl溶液中,為評價各性能的損失情況,引入性能下降率KN,計算公式如下:
圖4

圖4 不同淬火速率下7136鋁合金試樣的強度、伸長率及斷裂時間及相應的下降率(KR、KA、Kt)
Fig.4 The strength, elongation, and fracture time of 7136 aluminum alloy samples under different quenching rates, and corresponding reduction rate
(a) strength (RmOil is the strength in silicone oil, and RmNaCl is the strength in NaCl solution) and strength reduction rate (KR)
(b) elongation (AOil is the elongation in silicone oil, and ANaCl is the elongation in NaCl solution) and elongation reduction rate (KA)
(c) fracture time (tOil is the fracture time in silicone oil, and tNaCl is the fracture time in NaCl solution) and fracture time reduction rate (Kt)
由圖4b可知,硅油中的試樣伸長率在淬火速率大于5.3℃/s時基本不變,淬火速率小于5.3℃/s后迅速增高。NaCl溶液中試樣的伸長率在淬火速率大于5.3℃/s時隨淬火速率的減小先出現明顯降低再逐漸升高,淬火速率小于5.3℃/s后迅速升高。KA隨淬火速率減小呈“M”狀變化。
由圖4c可知,淬火速率大于100℃/s時,硅油中試樣的斷裂時間變化不大,之后隨淬火速率減小逐漸升高,最終穩定在68 h左右;NaCl溶液中試樣的斷裂時間在淬火速率大于100℃/s時隨淬火速率減小緩慢降低,淬火速率在20~100℃/s時斷裂時間幾乎不變,之后迅速升高并穩定在63 h左右。Kt隨淬火速率的減小迅速增加到16.6%,之后緩慢增大,在淬火速率為5.3℃/s時達到峰值(19.5%)后迅速降低。
可見,KR、KA和Kt表現出的規律并不一致,說明采用單一的性能損失很難準確地評價材料的SCC敏感性。為綜合評估材料SCC的敏感性,引入SCC敏感指數(ISSRT),計算公式如下[4]:
式中,RmNaCl為NaCl溶液中的斷裂強度(MPa),RmOil為硅油中的斷裂強度(MPa),ANaCl為NaCl溶液中的伸長率(%),AOil為硅油中的伸長率(%)。ISSRT越大表示SCC敏感性越高。
圖5給出不同淬火速率下7136鋁合金試樣的ISSRT。隨著淬火速率的減小,ISSRT呈先升高再降低的趨勢,淬火速率為5.3℃/s時的
圖5

圖5 不同淬火速率下7136鋁合金試樣的應力腐蝕敏感指數(ISSRT)
Fig.5 Stress corrosion sensitivity index (ISSRT) of 7136 aluminum alloy samples under different quenching rates
2.3 斷口SEM像
圖6

圖6 在NaCl溶液中的不同淬火速率下7136鋁合金試樣斷口形貌的SEM像
Fig.6 Low (a-c) and locally high (a1-c1) magnified fracture SEM images of 7136 aluminum alloy samples in NaCl solution under quenching rates of 263.0oC/s (a, a1), 5.3oC/s (b, b1), and 1.8oC/s (c, c1)
為更好地分析試樣的斷裂行為,圖7給出NaCl溶液中不同淬火速率下7136鋁合金試樣斷口附近(ED-TD面)的SEM像。淬火速率為263.0℃/s試樣的表層存在一些腐蝕裂紋,密度約為12 mm-1;裂紋比較尖銳,最大深度約為71.0 μm,如圖7a1所示。將試樣用Graff Sargent試劑(1 mL HF + 16 mL HNO3 + 3 g CrO3 + 83 mL H2O)腐蝕后,可以觀察到裂紋主要是穿過晶粒向試樣內部擴展,如圖7a2所示;晶粒內存在一些白色初生相,EDS分析顯示其成分(原子分數,下同)為:(76.15~85.68)%Al、(2.87~7.90)%Fe、(5.31~13.26)%Cu和少量Zn元素,應該為Al7Cu2Fe相[15,16]。
圖7

圖7 在NaCl溶液中不同淬火速率下7136鋁合金試樣斷口附近的SEM像
Fig.7 SEM images near the fracture surface of 7136 aluminum alloy in NaCl solution under quenching rates of 263.0oC/s (a, a1, a2), 5.3oC/s (b, b1, b2), and 1.8oC/s (c, c1, c2)
(a-c) low magnification
(a1-c1) locally magnified images of box regions in Figs.7a-c, respectively
(a2-c2) locally magnified images of box regions in Figs.7a1-c1, respectively (GB—grain boundary, GBP—precipitate at grain boundary, SGB—sub-grain boundary)
綜合以上結果可知,隨淬火速率減小,腐蝕裂紋的最大深度先增大后減小,腐蝕裂紋的數量逐漸增多。
2.4 微觀組織
2.4.1 EBSD像
圖8
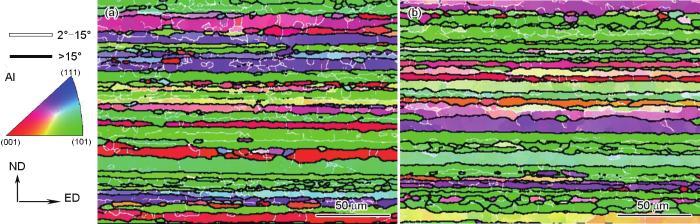
圖8 不同淬火速率7136鋁合金試樣縱截面晶粒取向分布圖
Fig.8 Grain orientation maps of 7136 aluminum alloy samples under quenching rates of 263.0oC/s (a) and 1.8oC/s (b)
2.4.2 SEM像
圖9a給出淬火速率為263℃/s 7136鋁合金試樣的SEM像??梢杂^察到大量尺寸為1.6~9.1 μm的白色第二相沿ED方向呈鏈狀分布,EDS分析其成分為(75.22~86.32)%Al、(3.11~7.70)%Fe、(5.61~15.81)%Cu和少量Zn元素,應該為Al7Cu2Fe相。這些相形成于熔鑄過程,在擠壓等變形過程中會破碎。固溶時,它們容易引起其周圍晶粒發生再結晶[18]。在腐蝕環境中,它們通常充當陰極引起電偶腐蝕[16,19]。淬火速率為1.8℃/s試樣的SEM像如圖9b所示。除Al7Cu2Fe相以外,晶界和晶內均出現大量η淬火相。晶界上的η相襯托出晶粒形貌。在晶界附近可以觀察到明顯的PFZ。
圖9
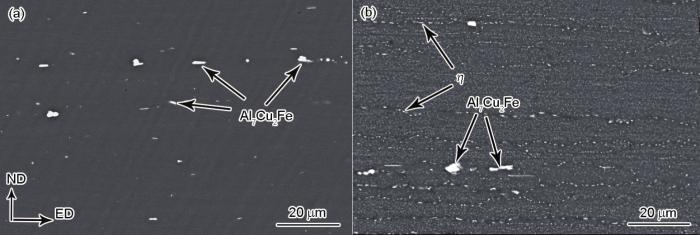
圖9 不同淬火速率7136鋁合金試樣的SEM像
Fig.9 SEM images of 7136 aluminum alloy samples under quenching rates of 263.0oC/s (a) and 1.8oC/s (b)
2.4.3 STEM-HAADF像
圖10
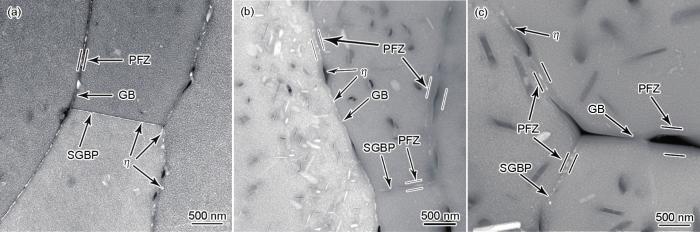
圖10 不同淬火速率7136鋁合金試樣的STEM-HAADF像
Fig.10 STEM-HAADF images of 7136 aluminum alloy samples under quenching rates of 263.0oC/s (a), 5.3oC/s (b), and 1.8oC/s (c) (SGBP—precipitate at sub-grain boundary, PFZ—precipitate free zone)
淬火速率減小至5.3℃/s時,試樣的晶內和晶界上都出現了大量的淬火相,如圖10b所示。一些淬火相在雙噴時脫落,形成黑色的孔洞。淬火速率減小,試樣在高溫下的時間更長,有利于溶質原子擴散,因而在晶界、亞晶界及Al3Zr粒子等界面能高的地方形成粗大的η相[20]。因此GBP的尺寸差異很大,尺寸大的長度為(453.8 ± 130.3) nm,尺寸小的為(57.4 ± 22.0) nm,與淬火速率為263℃/s試樣中的相當。晶界附近的PFZ寬度差別也更大,寬的達(223.0 ± 49.2) nm,窄的僅為(125.9 ± 10.7) nm,平均約174.5 nm。SGBP尺寸增加至(101.5 ± 34.7) nm,分布較連續,亞晶界附近的PFZ寬度為(70.6 ± 12.7) nm。
淬火速率繼續減小至1.8℃/s時,晶界和亞晶界上的淬火相進一步長大,附近的PFZ明顯更寬,如圖10c所示。尺寸大的GBP可達1000 nm,尺寸小的GBP長度增加至80.0 nm左右,晶界附近的PFZ寬度為(303.0 ± 35.0) nm。SGBP的長度為(101.5 ± 34.7) nm,其附近的PFZ寬度為(139.0 ± 7.7) nm,一部分已經超過淬火速率為5.3℃/s試樣中部分晶界PFZ的寬度。
綜合圖7b2和c2、圖9以及圖10的觀察,發現淬火相的尺寸和數量隨著淬火速率的減小而增加。這些淬火相幾乎沒有強化作用,且消耗了大量的溶質原子,減少了時效后η'強化相的數量,降低了試樣的強度(圖4a)。由于PFZ內沒有強化相,因此寬度增加后,也降低了試樣的強度[12]。因此,如圖4a所示,拉伸強度隨淬火速率減小而降低。統計晶界及亞晶界析出相形貌特征參數如圖11所示??梢?GBP尺寸、相間距及PFZ寬度均隨淬火速率減小而增加,在其他7xxx合金中發現了相似的規律。這是因為淬火速率減小后,更多的溶質原子擴散到晶界和亞晶界上,時效后形成尺寸和相間距更大的GBP,同時導致了PFZ寬度的增加[7,21]。
圖11
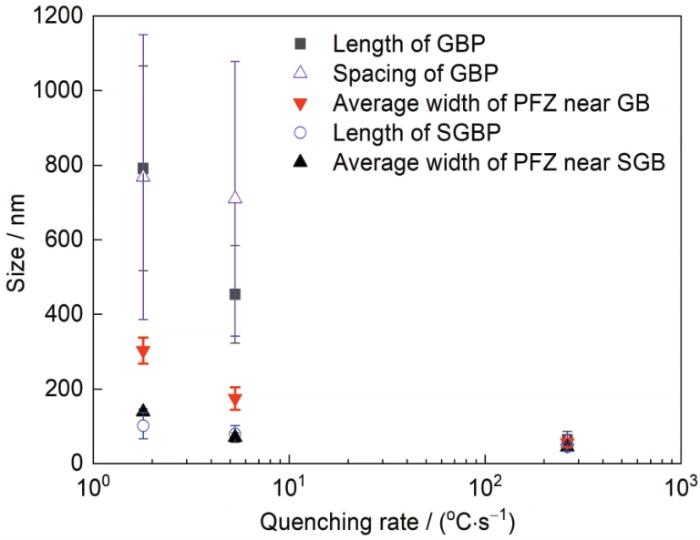
圖11 不同淬火速率7136鋁合金試樣晶界和亞晶界上析出相的特征參數
Fig.11 Parameters of GBP, SGBP, and PFZ in 7136 aluminum alloy samples under different quenching rates
圖12

圖12 淬火速率為263.0℃/s時7136鋁合金試樣晶界處的STEM-HAADF像和EDS面掃描圖
Fig.12 STEM-HAADF image (a) and EDS element maps of Al (b), Zn (c), Mg (d), and Cu (e) for 7136 aluminum alloy sample under quenching rate of 263.0oC/s
在不同淬火速率7136鋁合金試樣中統計了大量GBP中Zn、Mg、Cu元素含量,如圖13所示。隨著淬火速率的減小,GBP中Zn、Mg、Cu元素的含量均呈增加的趨勢,但是3種元素的增加率不同。淬火速率從263.0℃/s減小至5.3℃/s時,Zn、Mg和Cu元素含量的增加率分別為44.9%、47.8%和28.9%;當淬火速率從5.3℃/s減小至1.8℃/s時,它們的增加率分別為11.0%、9.8%和88.4%。淬火速率大于5.3℃/s時,Zn、Mg元素的增加率明顯高于Cu元素,而淬火速率小于5.3℃/s后Cu元素的增加率比Zn、Mg元素的更高。
圖13
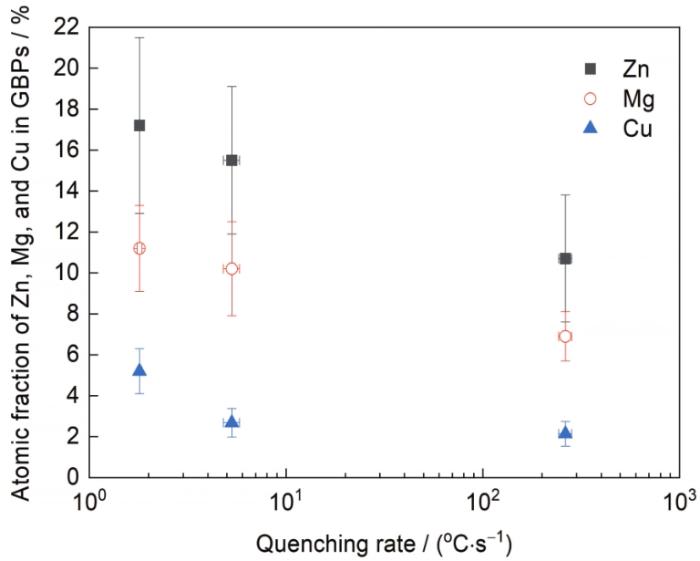
圖13 不同淬火速率7136鋁合金試樣晶界析出相中Zn、Mg、Cu元素的含量
Fig.13 Contents of Zn, Mg, and Cu in GBPs of 7136 aluminum alloy samples under different quenching rates
3 分析討論
圖14

圖14 不同淬火速率下7136鋁合金應力腐蝕開裂裂紋擴展示意圖
Fig.14 Schematics of crack propagation of stress corrosion cracking (SCC) in 7136 aluminum alloy under quenching rates of 263.0oC/s (a), 5.3oC/s (b), and 1.8oC/s (c)
淬火速率為263.0℃/s時,試樣晶內、晶界和亞晶界沒有淬火相出現,晶界和亞晶界附近的PFZ很窄。NaCl溶液中試樣的斷口處未觀察到晶界和亞晶界被明顯腐蝕的特征,說明此時沒有沿晶界和亞晶界發生陽極溶解。試樣表面的Al7Cu2Fe相等引起其周圍基體發生腐蝕并形成腐蝕坑[10,16],在外加應力的作用下,腐蝕坑底部形成應力集中,進而引發SCC裂紋的萌生[24~26]。腐蝕過程中產生的H會擴散到基體中,并沿著位錯運動到裂紋尖端,降低了晶格結合力,導致SCC裂紋不斷擴展[24]。擴展過程中,因為晶界和亞晶界附近狹窄的PFZ抑制了陽極溶解通道的形成[13,27],裂紋選擇在晶內不斷擴展,如圖14a所示。此時SCC以氫脆為主,裂紋主要穿晶擴展,強度、伸長率和斷裂時間的損失不大,試樣的SCC敏感性并不高。
淬火速率減小至約5.3℃/s時,淬火相的數量明顯增多,尺寸增大,GBP的相間距有所增大,晶界附近的PFZ寬度比淬火速率為263.0℃/s時明顯增加,亞晶界附近的PFZ寬度增加很小(圖11)。淬火相是H不可逆的陷阱,可以捕獲試樣中的H并使之以氣體的形式排放出去,因而減緩了氫脆[28,29]。然而,淬火相的腐蝕電位比基體和Al7Cu2Fe相更負,因而試樣表面的淬火相在腐蝕溶液中會充當陽極優先被溶解[27],形成腐蝕裂紋源。GBP中Zn、Mg元素含量比淬火速率為263.0℃/s時大幅增加,引起GBP與基體和Al7Cu2Fe相的電勢差增大[15,30],這促進了腐蝕裂紋擴展。晶界附近的PFZ寬度增加有利于裂紋的形成和擴展[10],因而晶界成為快速腐蝕通道,但多數亞晶界對微裂紋的產生和擴展還有較強的抑制作用。此時腐蝕裂紋在氫脆和陽極溶解共同作用下沿晶界迅速擴展到試樣內部更深的地方,導致更大的腐蝕深度,如圖14b所示。因而試樣強度和斷裂時間等的損失更大,試樣的SCC敏感性很高。
淬火速率減小至約1.8℃/s時,淬火相的數量和尺寸、晶界和亞晶界附近的PFZ寬度都很大,如圖11所示。淬火相增多可以捕獲更多的H,因而氫脆進一步被削弱。試樣表面更多的淬火相被溶解并在外力作用下形成裂紋源,裂紋數量比淬火速率為263.0和5.3℃/s時分別增加了141.7%和52.6%,這大幅緩解了應力集中。GBP中Cu元素大量的增加也可有效抑制SCC裂紋擴展[7,8,24,31,32]。圖15是淬火速率為5.3和1.8℃/s時板材的晶界和亞晶界PFZ寬度分布情況。可見,淬火速率為5.3℃/s時,約80%的晶界PFZ寬度在100~200 nm,而淬火速率為1.8℃/s時有約75%的亞晶界PFZ在這個寬度范圍內,即淬火速率為1.8℃/s時許多亞晶界PFZ寬度已經超過了淬火速率為5.3℃/s試樣中晶界PFZ的寬度。更寬的PFZ導致陽極溶解通道更容易形成,這就增加了沿晶界和亞晶界裂紋的數量(圖14c),因而主裂紋被鈍化。微裂紋的產生既釋放了應力又延緩了裂紋擴展的速率。Tanguy等[25]也發現腐蝕裂紋增多可以降低SCC的擴展速率。因此,淬火速率為1.8℃/s時試樣各項性能的損失都很小,試樣的SCC敏感性反而降低。
圖15
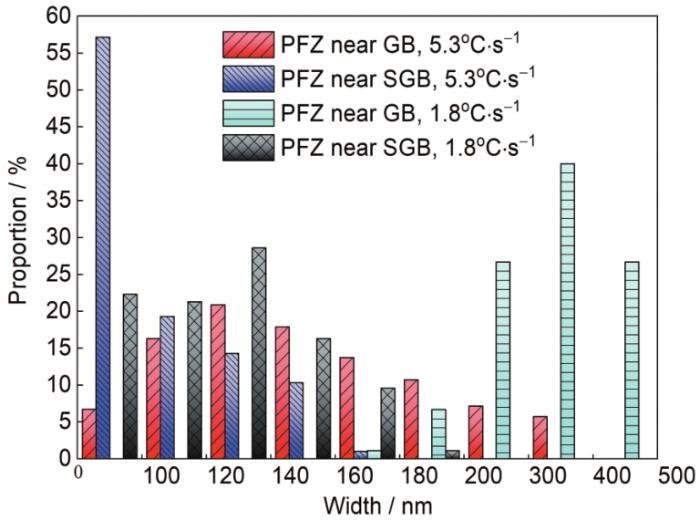
圖15 淬火速率為5.3和1.8℃/s時7136鋁合金試樣中不同無沉淀析出帶寬度的晶界和亞晶界的比例
Fig.15 Proportions of grain boundaries and sub-grain boundaries with different PFZ widths in 7136 aluminum alloy samples under quenching rates of 5.3 and 1.8oC/s
4 結論
(1) 7136鋁合金應力腐蝕開裂敏感性隨著淬火速率的減小先升高再降低,淬火速率約為5.3℃/s時的應力腐蝕開裂敏感性最高。
(2) 隨著淬火速率的減小,晶界析出相增大,相間距增大,PFZ增寬。晶界析出相中Zn、Mg和Cu元素含量隨淬火速率減小而增加。淬火速率大于5.3℃/s時,晶界析出相中Zn、Mg元素的含量迅速增加,Cu元素含量緩慢增加;淬火速率小于5.3℃/s后,Zn、Mg元素含量增速降低,而Cu元素含量迅速增加。
(3) 淬火速率減小,晶界和亞晶界附近的PFZ寬化,能夠充當腐蝕裂紋擴展路徑,應力腐蝕裂紋擴展方式從以穿晶擴展為主轉變為沿晶界和亞晶界擴展。