分享:回火溫度對含 δ 鐵素體高鋁中錳鋼力學性能和顯微組織的影響
研究了回火溫度對含15% δ鐵素體(體積分數)的熱軋高鋁中錳鋼顯微組織和力學性能的影響。結果表明,鋼中長300 μm的δ鐵素體經熱軋再結晶可被細化分割至大量長3 μm左右竹節狀晶粒,且在回火溫度高達700℃時尺寸不變。400~500℃回火后,馬氏體基體依然維持較高的位錯密度且析出細小滲碳體和納米級VC粒子,屈服強度最高;同時C由馬氏體向奧氏體的大量配分提高了奧氏體穩定性,獲得了相對持久的加工硬化,最終獲得了屈服強度約1500 MPa、抗拉強度1800 MPa和斷后延伸率14%的最佳力學性能組合。該鋼δ鐵素體相一方面由于析出強化、晶粒細化和位錯強化而得到顯著硬化;另一方面δ鐵素體體積分數不高且呈孤島狀嵌在馬氏體基體中,這些特征導致該鋼屈服強度由馬氏體基體而非δ鐵素體所決定,因此相比于其他類似Al含量的含δ鐵素體中錳鋼,屈服強度大幅度提高。
關鍵詞:
在汽車中應用先進高強鋼和低密度材料可實現汽車輕量化,進而同時提高燃油效率、降低CO2排放和提高碰撞安全性。截至目前,先進高強鋼已經發展到力學性能更為優異的第三代先進高強鋼,代表性鋼種包括中錳鋼、淬火配分鋼(Q&P鋼)、輕質鋼等[1~3]。其中中錳鋼因其優良的綜合力學性能和較低成本而廣受關注。中錳鋼獲得優良力學性能的關鍵工藝是兩相區臨界退火,通過溶質元素在所形成的奧氏體和鐵素體兩相間的配分,增強了奧氏體穩定性并在最終組織中引入殘余奧氏體,進而在變形過程中通過馬氏體相變貢獻額外加工硬化,可同時提高強度和塑性。尤其是Al含量較高的中錳鋼,既可以通過提高相變溫度縮短臨界退火時間,進而更適合工業連續退火工藝,還可以降低鋼的密度,同時實現高強和輕量化目標,因而廣受關注。但提高Al含量導致相變點顯著升高,晶粒粗化且形成δ鐵素體,使得屈服強度明顯降低,如Li等[4]報道的熱軋0.2C-3Al-6Mn (質量分數,%,下同)鋼在700℃退火1 h后,屈服強度低至600 MPa;Lee等[5]開發的熱軋0.3C-10Mn-6Al鋼在700~1000℃之間退火10 min后,屈服強度降至400 MPa。
通過V、Nb微合金化進行強化可以提高中錳鋼的屈服強度,如Zhu等[6]在9Mn鋼中添加0.3%(V + Nb),兩相區退火后屈服強度提高到950 MPa,并且表現出1230 MPa的抗拉強度和40%的延伸率。另外,通過低溫回火保留初始組織中的位錯、維持馬氏體硬度可以更經濟地提高屈服強度,如Sugimoto等[7]開發出0.2C-1.5Si-3Mn熱軋中錳鋼,經280℃回火1.5 h后屈服強度和延伸率同時達到1035 MPa和14%;Lee等[8]開發的熱軋0.1C-1Si-10Mn-0.3Mo-0.5V鋼,在400℃回火1 h后屈服強度達1012 MPa,并且兼具20.7%的延伸率。He等[9]開發出的10Mn-V鋼,經過溫軋、冷軋和回火熱處理后,屈服強度達到2.2 GPa,同時表現出16%的均勻延伸率。然而,回火對含Al中錳鋼力學性能影響的研究還很少,尤其是Al含量高導致形成粗大高溫鐵素體時,回火工藝將如何影響馬氏體、δ鐵素體和殘余奧氏體以及相對應的力學性能,還尚未見系統的研究。本工作研究了回火溫度對含δ鐵素體高鋁中錳鋼力學性能和顯微組織的影響。
1 實驗方法
實驗用鋼的化學成分為0.4C-7Mn-1.3Si-3Al-0.4(V + Nb),通過Thermo-Calc軟件計算相圖可知相變平衡溫度A1和A3分別為654和894℃。用50 kg真空感應爐熔煉鋼水并澆鑄成鋼錠,鍛成60 mm厚鍛坯,然后加熱至1150℃均勻化2 h,在1100~900℃之間熱軋至5 mm厚,空冷至室溫。熱軋鋼板在300、400、500、600和700℃回火處理1 h后空冷至室溫。為便于討論,以上不同溫度回火后的樣品和熱軋板分別記為T300、T400、T500、T600、T700和HR。
使用WDW-200C萬能試驗機進行室溫拉伸力學性能測試,拉伸速率1 mm/min。拉伸試樣寬6 mm,標距長25 mm,拉伸方向與軋制方向平行。利用JSM-6701F掃描電子顯微鏡(SEM)、PHI 710型Auger電子能譜儀上配置的電子背散射衍射儀(EBSD)、D8 DISCOVER A25 X射線衍射儀(XRD)和JEM-2200FS透射電子顯微鏡(TEM)測試樣品的顯微組織和殘余奧氏體分數。通過配置在SEM和TEM上的能譜儀(EDS)檢測顯微組織基體和析出相的化學成分。SEM測試的樣品首先采用2000號砂紙磨平,然后進行機械拋光,最后在4% (體積分數)硝酸酒精溶液中腐蝕。XRD和EBSD檢測樣品經磨光在20% (體積分數)高氯酸酒精溶液中電解拋光,電解電壓為20 V,溫度25℃。TEM樣品首先機械減薄至50 μm左右,沖壓成直徑3 mm的圓片,然后在-20℃下經8% (體積分數)高氯酸酒精溶液雙噴電解。殘余奧氏體體積分數的計算基于馬氏體(200)、(211)衍射峰和奧氏體(200)、(220)和(311)衍射峰的積分強度[10]。奧氏體中的平均C含量利用XRD中(200) γ 峰,采用如下公式計算[11]:
式中,Cγ 是奧氏體中的C含量(質量分數,%),aγ 是奧氏體的平均晶格常數,通過如下公式計算[12]:
式中,λ是Co靶的波長(λ = 0.178897 nm);θ是Bragg衍射角;h、k和l是(200) γ 晶面的Miller指數。
另外利用XRD衍射數據,采用位錯密度計算模型計算bcc相的位錯密度[13,14]:
式中,ρ和β分別是位錯密度和馬氏體(211)衍射峰的半高寬(FWHM);b是Burgers矢量模(b = 0.248 nm)。由于δ鐵素體晶粒熱軋時被軋扁并沿著軋制方向展長,故可以在熱軋板垂直于橫向的縱截面上直接觀察和測量δ鐵素體晶粒的長度和厚度,并利用Image-Pro plus進行統計。
2 實驗結果
2.1 拉伸性能
不同溫度回火后的工程應力-應變曲線見圖1a,對應的力學性能指標總結于表1。300和400℃回火后的拉伸曲線相似,抗拉強度均在1800 MPa左右,但回火溫度300℃時的頸縮后延伸率和斷后延伸率較高而屈服強度較低;回火溫度升至500℃時,均勻延伸率提升至9.2%,顯著高于400℃回火樣品而屈服強度略降80 MPa,但斷后延伸率和抗拉強度基本不變;回火溫度升至600℃后,屈服強度、抗拉強度、均勻延伸率和斷后延伸率相比于500℃均降低;回火溫度升高至700℃時,屈服強度和抗拉強度與600℃回火樣品相比分別大幅降低了300 MPa和450 MPa,雖然均勻延伸率和斷后延伸率均顯著提高到11.6%和26.6%,但加工硬化率明顯很低,屈服后強度只增加85 MPa。圖1b總結了現有類似Al含量的中錳鋼屈服強度和延伸率[15~22]??芍姸榷嘣?00~700 MPa且不超過1 GPa,這是由于Al含量高導致中錳鋼存在粗大高溫δ鐵素體,且在后續熱處理過程中難以細化,因此硬度低、屈服強度低。相比之下,本工作鋼雖然也含有δ鐵素體(見下文實驗結果),但屈服強度高達1370~1560 MPa,遠遠高于類似Al含量的中錳鋼,同時延伸率依然保持在10%以上,力學性能優勢明顯。
圖1
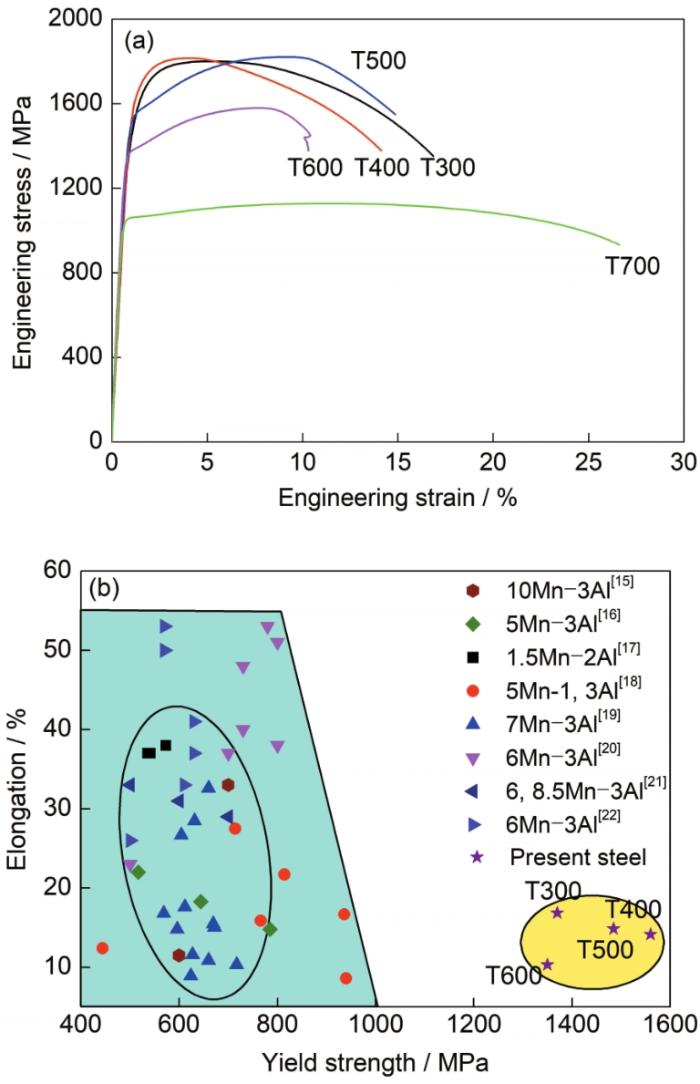
圖1 不同溫度回火后拉伸試樣的工程應力-應變曲線及其與文獻所報道類似Al含量中錳鋼力學性能[15~22]的對比
Fig.1 Engineering stress-strain curves of tensile samples after tempering at different temperatures (T300, T400, T500, T600, and T700 represent tempering of hot-rolled plate at 300, 400, 500, 600, and 700℃, respectively) (a) and the comparison of the resultant yield strength and other medium Mn steels having the similar Al contents in Refs.[15-22] (b)
表1 不同回火樣品的力學性能
Table 1
Sample |
YS MPa |
UTS MPa |
UEL % |
TEL % |
WHI MPa |
---|---|---|---|---|---|
T300 | 1370 | 1800 | 5.3 | 16.7 | 430 |
T400 | 1560 | 1815 | 4.0 | 14.1 | 255 |
T500 | 1485 | 1820 | 9.2 | 14.9 | 335 |
T600 | 1350 | 1580 | 7.6 | 10.3 | 230 |
T700 | 1045 | 1130 | 11.6 | 26.6 | 85 |
圖2a是熱軋試樣變形前殘余奧氏體體積分數和不同拉伸試樣變形前后的殘余奧氏體體積分數、奧氏體轉化量,圖2b為變形前奧氏體中的C含量,圖2c為bcc相的位錯密度在變形前后的變化及位錯密度增量。熱軋樣品經300℃回火后,殘余奧氏體體積分數保持在19%不變,600℃回火后,殘余奧氏體體積分數由19%下降至14%;拉斷樣品殘余奧氏體體積分數隨回火溫度升高亦降低,但500和600℃回火樣品變形后奧氏體體積分數減少得較多,且以500℃回火樣品變形時轉變量最多;當回火溫度達到700℃時,殘余奧氏體體積分數達到最高至33%,但變形時殘余奧氏體轉變量最低。另外,T700樣品拉伸塑性最高,而T500和T600樣品塑性最低,但是這2個樣品在拉伸變形中奧氏體轉變分數最高,相反T700轉變最少,這說明T500和T600樣品中殘余奧氏體在最小拉伸應變下依然轉變最多,因此力學穩定性最差;而T700樣品在最大拉伸應變下殘余奧氏體轉變最少,因此力學穩定性最好。相對應地,T500和T600樣品變形前其C含量較低,殘余奧氏體體積分數最高的T700樣品奧氏體中C含量較高,也即低C含量降低了奧氏體的穩定性,導致T500和T600樣品在變形過程中殘余奧氏體轉變分數更多。回火溫度和變形對bcc相位錯密度的影響如圖2c所示,回火溫度從300℃增加至700℃,bcc相中的位錯密度始終在降低,這符合預期;而拉斷后,T400和T500樣品的位錯密度與T300樣品相差不大,因此T500樣品的位錯增量最大,加工硬化能力最好;而溫度升高至600和700℃時,拉斷樣品的位錯密度依然隨溫度逐漸下降。
圖2
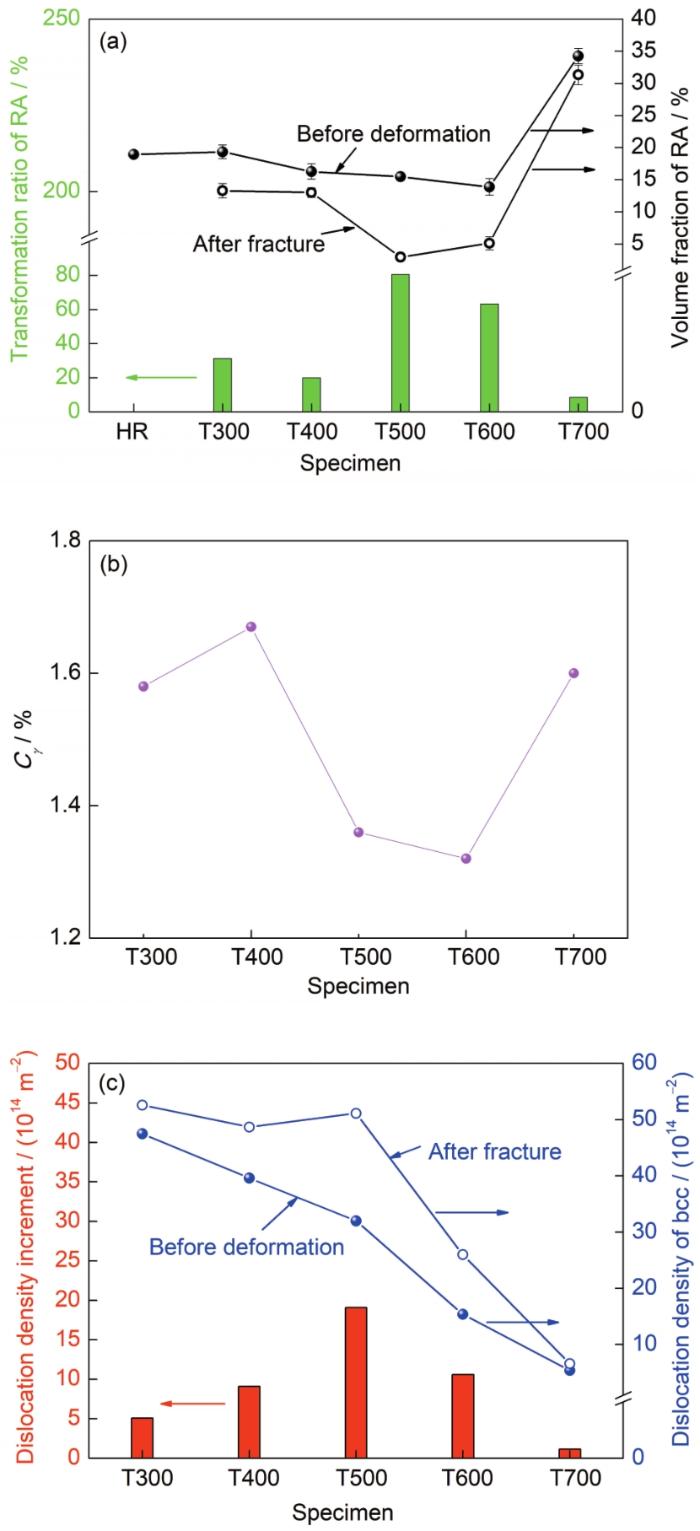
圖2 不同溫度回火試樣變形前后殘余奧氏體體積分數和奧氏體轉化量、變形前奧氏體中C含量以及bcc相位錯密度的變化和增量
Fig.2 Variation of volume fraction of retained austenite (RA), transformation ratio of RA (HR—hot rolling) (a), carbon content in austenite (Cγ ) before deformation (b), and dislocation density of bcc phase and its increment (c) in T300, T400, T500, T600, and T700 samples
2.2 顯微組織演變
圖3是熱軋板、不同溫度回火樣品顯微組織的EBSD和SEM像。熱軋板的顯微組織主要由馬氏體基體、殘余奧氏體和δ鐵素體組成,細小的微米尺寸(約1 μm)的殘余奧氏體晶粒鑲嵌在馬氏體基體中(圖3a),δ鐵素體沿軋向伸長,如圖3b所示類似層狀鑲嵌在馬氏體基體中,平均長度300 μm左右,在δ鐵素體與馬氏體相界面的垂直方向所測量出的δ鐵素體片層的厚度為2~3 μm (圖3b),更細致地觀察發現δ鐵素體被大角晶界分割成長3 μm左右的竹節狀晶粒,其內還存在小角度亞晶界(< 15°) (圖3c),推測是由于熱軋過程中發生動態再結晶及再結晶后的變形和動態回復的緣故。當在300~600℃回火時,隨著回火溫度升高至300~600℃,滲碳體開始在回火馬氏體基體和馬氏體/δ鐵素體相界面析出(圖3d和g),并且隨回火溫度升高析出數量增加,而在相界面析出的滲碳體優先粗化(圖3h和i)。當回火溫度提升至600℃時,大量滲碳體析出導致Cγ 和奧氏體穩定性下降,部分大塊殘余奧氏體發生轉變,留下的殘余奧氏體更為細小(圖3j)。同時由于部分馬氏體發生再結晶和晶粒長大而形成大塊狀鐵素體。相比之下,δ鐵素體沒有變化。回火溫度為700℃時,回火馬氏體中滲碳體數量明顯降低,殘余奧氏體體積分數顯著提高,且殘余奧氏體由單一等軸狀轉變為等軸和片層2種形貌,塊狀鐵素體數量進一步增多,如圖3k和l所示。
圖3
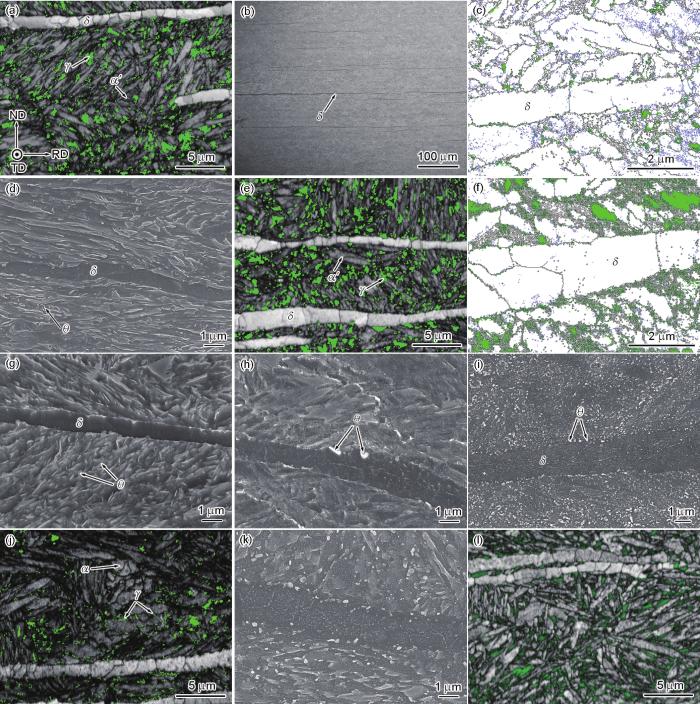
圖3 熱軋和不同溫度回火后試樣顯微組織的EBSD和SEM像
Fig.3 EBSD (a, c, e, f, j, l) and SEM (b, d, g, h, i, k) images of microstructure for specimens HR (a-c), T300 (d-f), T400 (g), T500 (h), T600 (i, j), and T700 (k, l) observed along the transverse direction (TD) (α', γ, α, δ, and θ represent martensite, austenite, ferrite, δ-ferrite, and cementite, respectively; the green and white colors in EBSD images represent austenite and martensite/ferrite, respectively; the blue and black lines represent low angle boundary (< 15°) and high angle boundary (> 15°), respectively; ND and RD are normal and rolling directions, respectively)
由于600℃回火樣品強度、塑性均明顯偏低,所以重點研究了600℃回火樣品脆性來源。圖4a為T600樣品斷后的宏觀形貌,圖4b~g是T600拉伸試樣斷口形貌及裂紋沿拉伸方向傳播路徑的SEM像。由圖4b可以看出,樣品斷口形貌由大量解理面組成,韌窩數量少,斷裂形式主要為沿晶斷裂。通過觀察裂紋沿拉伸方向的傳播路徑發現,裂紋主要沿原奧氏體晶界和馬氏體/δ鐵素體相界傳播(圖4c和d)。圖4e~g分別為圖4c和d中A、B和C區域的放大圖。觀察發現,裂紋擴展所經過的原奧氏體晶界和馬氏體/δ鐵素體相界上均存在大量較粗大的滲碳體顆粒,尺寸在200~500 nm之間。相比之下,回火馬氏體各種亞結構(packet、block、lath)界面上析出的滲碳體更加彌散細小,尺寸在50~100 nm之間;且滲碳體中Mn元素富集程度高于鋼中平均含量(圖4h)。在回火馬氏體板條內也析出更為細小的短棒狀滲碳體和VC,VC尺寸在15~20 nm,如圖4i和j所示。另外,回火馬氏體板條界面和板條內存在大量位錯,如圖4i所示。
圖4
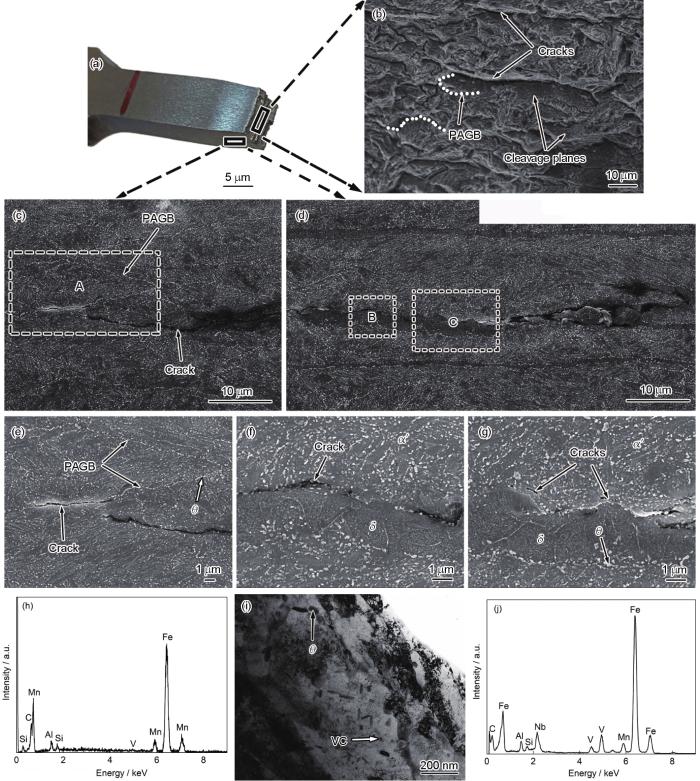
圖4 T600樣品拉斷后宏觀形貌及其中裂紋擴展的SEM像和TEM像及EDS
(a) fractured specimen
(b) fracture SEM images after tensile test (PAGB—prior austenite grain boundary) (c, d) cracks propagation along the rolling direction (e-g) magnification views of areas marked by A, B, and C in Figs.4c and d, respectively (h) EDS on the cementite from the particle marked by white arrow in Fig.4e (i) TEM image exhibiting the distribution of cementite and VC inner martensite lath (j) EDS on the VC from the particle marked by white arrow in Fig.6i
Fig.4 Macrostructure of fractured specimen, SEM and TEM images of the fracture morphology and crack propagation, and corresponding EDS for T600 specimen
3 分析討論
3.1 回火溫度對屈服強度的影響
由圖3可知,回火溫度由300℃增加至700℃,δ鐵素體形貌和尺寸均未發生變化,且檢測到的bcc相整體位錯密度下降(圖2c),但同時屈服強度卻由1370 MPa顯著增加至1560 MPa,然后逐漸降至1045 MPa。因此,該鋼的屈服強度不應主要由δ鐵素體決定,這可能是該鋼屈服強度遠遠高于類似Al含量中錳鋼的原因(圖1b)。因為圖1b中所歸納鋼中的δ鐵素體不僅體積分數高,而且尺寸粗大,易于優先屈服,導致屈服強度一般在600~700 MPa之間(圖1b)。要使本來較軟的δ鐵素體不首先屈服,則必須使δ鐵素體被顯著強化。
T300樣品的回火溫度較低,此時δ鐵素體的強度最高。因此以T300樣品為研究對象,通過和文獻[15,23]中報道的鋼種對比,探究本研究鋼中δ鐵素體被強化的機理。表2對比了2種鋼的成分、顯微組織和軋制工藝。相比于文獻報道的對比鋼種,T300樣品中δ鐵素體的晶粒尺寸通過熱軋中動態再結晶被顯著細化至2~3 μm,而對比鋼中δ鐵素體體積分數和尺寸均數倍、數十倍于本研究鋼。根據Hall-Petch公式[24],晶粒細化的強化增量(ΔσG)按如下公式計算:
表2 本研究鋼和文獻[15,23]中研究鋼的化學成分、δ相體積分數、平均晶粒尺寸、熱軋溫度和軋制壓下率對比
Table 2
Specimen |
Composition (mass fraction / %) |
Volume fraction of δ phase / % |
Grain size of δ / μm |
Finishing rolling temperature oC |
Rolling reduction ratio / % |
---|---|---|---|---|---|
T300 | 0.4C-7Mn-3Al-1.3Si-0.4(V + Nb) | 15.0 | 2.63 ± 0.48 | 900 | 92.0 |
Steel in Refs.[15,23] | 0.2C-9.7Mn-3.2Al-3.4Si | 52.4 | 25.1 | 750 | 91.6 |
式中,σE和σL分別是本研究鋼和文獻中對比鋼的摩擦力,K是強化系數,DE和DL分別是本研究鋼和文獻中對比鋼δ鐵素體晶粒尺寸(μm)。由于2種鋼Al含量幾乎相同,所以摩擦應力大致相同(σE = σL)。對于鐵素體,K = 551.2~640 MPa·μm-1/2[24,25],因此細晶強化增量經估算在230~270 MPa。
T300樣品中δ鐵素體的內部組織的SEM像和TEM像及EDS如圖5所示。可以看出,δ鐵素體的內部在熱軋過程中高溫析出的VC尺寸在30~50 nm (圖5a和c)。而對比鋼不含V、Nb等合金化元素,所以T300樣品的析出強化增量(ΔσP)通過Orowan-Ashby公式[26]計算如下:
圖5
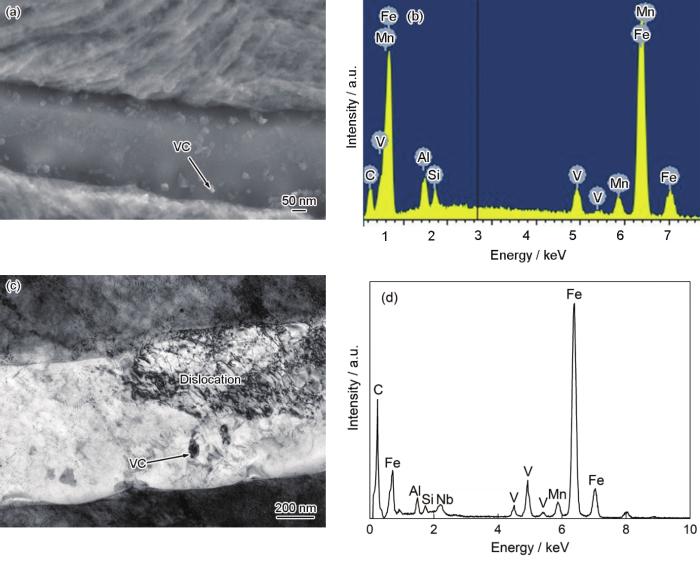
圖5 T300樣品中VC在δ鐵素體中分布的SEM像和TEM像及EDS
Fig.5 SEM (a) and TEM (c) images of VC distribution inner δ-ferrite of T300 specimen and the corresponding EDS on VC (b, d)
式中,μ是鐵素體剪切模量(μ = 81600 MPa[27]);b取0.248 nm[28];f是析出相的體積分數(0.587% ± 0.005%);x是VC的直徑(30~50 nm)。由此計算出析出強化增量在77~114 MPa。
由
當回火溫度由300℃提升至400℃時,馬氏體中析出更多細小的滲碳體(圖3d和g)。細小滲碳體的析出強化作用導致馬氏體基體的強度提升,因此T400試樣的屈服強度由1370 MPa提高到1560 MPa。隨回火溫度提升至500℃,雖然bcc相中位錯密度繼續下降,但是滲碳體繼續大量析出,只有在相界和原奧氏體晶界處的部分滲碳體粗化,同時因為VC在600℃回火時已經在馬氏體和δ鐵素體大量析出(圖4i),且一般VC在回火馬氏體的析出溫度在400~750℃之間,析出峰值溫度在600~650℃區間[31~34],因此推測500℃回火時納米尺度的VC粒子也開始析出,導致對位錯的釘扎作用較400℃增強,因此導致屈服強度僅略微下降75 MPa?;鼗饻囟壬咧?00℃,滲碳體在相界、原奧氏體晶界處顯著粗化,部分馬氏體再結晶導致位錯密度大幅降低,且馬氏體中的C大量配分至奧氏體和滲碳體而部分轉變成塊狀鐵素體,導致在較低屈服強度就沿相界開裂且快速失效;回火溫度至700℃時,已經處于兩相區,此時滲碳體大量溶解且馬氏體經逆相變轉變為奧氏體和大量塊狀鐵素體,導致位錯密度顯著降低和C大量配分至奧氏體,屈服強度繼續顯著下降。
3.2 T600樣品產生回火脆性的原因
所有樣品中T600樣品的斷后延伸率最低。由圖4可知,其斷口形貌主要由剪切面組成,包含很少的韌窩,斷裂形式為沿晶斷裂,表明試樣的斷裂屬于脆性斷裂。裂紋主要沿原奧氏體晶界和δ鐵素體相界萌生并擴展。這是由于大量尺寸較大的滲碳體(200~500 nm)沿原奧氏體晶界和δ鐵素體相界呈網狀密集分布,弱化晶界結合力[35,36]。相比之下,在回火馬氏體亞結構界面上分布的滲碳體尺寸在50~100 nm之間,且分布更加均勻。因此,原奧氏體界面和δ鐵素體/馬氏體相界面更易于裂紋的萌生。另外,大量滲碳體的析出降低了奧氏體的穩定性,冷卻過程中可形成新鮮馬氏體(圖3j),其是斷裂敏感性高的脆性相。另外,殘余奧氏體由于穩定性較低,在第2階段形變過程中快速轉變成形變誘導相變馬氏體,隨殘余奧氏體在變形過程中快速轉變殆盡,在原奧氏體晶界和馬氏體/δ鐵素體相界等界面結合力差的位置發生了應力集中而萌生裂紋,然后經脆性馬氏體相快速擴展,最終導致斷裂。
3.3 回火溫度對加工硬化行為的影響
圖6為不同溫度回火樣品的加工硬化率隨真應變的變化曲線。隨真應變增加T300和T400樣品的加工硬化率一直在降低,且下降速率逐漸變慢;而T500、T600和T700樣品加工硬化率先快速下降,再升高然后不斷降低直至斷裂?;诖?,將各樣品的加工硬化曲線分為2個階段。第1階段,所有樣品的加工硬化率都隨應變增加逐漸下降,且隨回火溫度升高也逐漸降低,推測是因為此階段加工硬化主要由馬氏體中位錯增殖和交割導致[37],回火溫度升高位錯密度降低,所以加工硬化率減小。第2階段,加工硬化率的變化可以分為2類。對于T300和T400樣品,此階段加工硬化率隨真應變增加雖然下降但速率降低,推測是由于此階段開始發生奧氏體向馬氏體相變轉變貢獻了額外加工硬化。T300樣品中奧氏體轉變量超過T400樣品(圖2a),這是由于400℃回火時C向奧氏體的配分程度超過300℃,因此提高了奧氏體中的C含量和穩定性(圖2b),導致變形時奧氏體轉變更緩慢,因此加工硬化率降低。當回火溫度升高至500℃時,大部分滲碳體依然彌散析出,但部分位于相界處的滲碳體開始粗化(圖3h),殘余奧氏體穩定性略有降低,導致變形過程中殘余奧氏體轉變最多,從而導致持續的加工硬化和較大的均勻延伸率;回火溫度升高至600℃時,馬氏體/δ鐵素體相界和原奧氏體晶界滲碳體析出量顯著增多且粗化(圖3i),導致這些位置在更低屈服強度就開始萌生裂紋,且由于奧氏體中的C含量下降、穩定性繼續降低甚至冷卻后形成馬氏體,雖然奧氏體轉變可貢獻加工硬化率,但裂紋經馬氏體可快速擴展導致很快失效(圖2a、2b和圖6)。700℃回火時,加熱過程中析出的滲碳體大部分在保溫時溶解,溶解的C在高溫下大量配分至奧氏體,導致殘余奧氏體體積分數和穩定性均顯著提高,結果變形過程只有約10%奧氏體發生相變(圖2a)且轉變緩慢,因此加工硬化率最低。
圖6
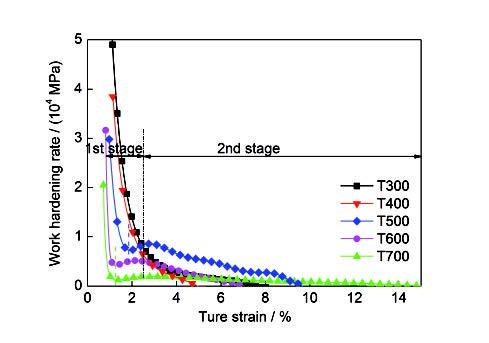
圖6 不同溫度回火樣品的加工硬化曲線
Fig.6 Strain-hardening curves of samples after tempering at different temperatures
4 結論
(1) 所開發的高鋁中錳鋼在400~500℃回火時,馬氏體中位錯密度雖略有下降,但細小滲碳體和VC納米級粒子等析出強化增強,導致屈服強度最高;同時在該溫度區間回火促進了C原子由馬氏體向奧氏體配分,提高了奧氏體穩定性而貢獻了相對持久的加工硬化,最終獲得屈服強度1500 MPa左右、抗拉強度1800 MPa和斷后延伸率14%的最佳綜合力學性能。
(2) 高鋁中錳鋼在600℃回火時的斷后延伸率最低,這是由于此時沿原奧氏體晶界和馬氏體/δ鐵素體相界析出大量粗大滲碳體而易于萌生裂紋。另外,大量滲碳體析出降低了奧氏體穩定性而在冷卻時可轉變為馬氏體,而且變形時穩定性差的殘余奧氏體會快速轉變為馬氏體。結果在原奧氏體晶界和馬氏體/δ鐵素體相界等界面結合力差的位置萌生的裂紋,經脆性馬氏體相快速擴展導致斷裂。
(3) 高鋁中錳鋼中長300 μm的δ鐵素體片層經熱軋過程動態再結晶細化為3 μm左右竹節狀晶粒,其內部存在熱軋過程中析出的VC和大量位錯及亞晶界,導致δ鐵素體顯著強化;另外,由于δ鐵素體體積分數較小,且呈孤島狀嵌在馬氏體基體,導致該鋼屈服強度主要由馬氏體基體決定,因此遠高于文獻中其他Al含量類似的中錳鋼。據此,本研究所采用的合金化策略、組織設計與制備工藝路線為開發含Al輕質高強鋼提供了可行的技術路線。
來源--金屬學報