分享:新型Ni-Co基高溫合金塑性變形連接中界面組織演化及愈合機制
任少飛1,2, 張健楊2, 張新房,1, 孫明月
,2,3, 徐斌2,3, 崔傳勇4
1.
2.
3.
4.
為解決鎳基高溫合金的焊接難題,以新型Ni-Co基高溫合金為實驗材料,采用塑性變形連接的新方法,實現了新型Ni-Co基高溫合金的連接。通過OM、EBSD、TEM等分析手段探究了界面的再結晶行為及界面的愈合機制。結果表明,1150℃進行塑性變形連接時,合金的變形抗力小,不易開裂。不同變形量的連接實驗表明,在40%的變形量下,合金可以實現界面的完全愈合,其力學性能達到基體同等水平。在塑性變形過程中,界面附近的粗大晶粒首先發生細化,隨著變形量的增加,細化的晶粒在連續動態再結晶的輔助作用下,通過界面晶界的遷移消除了原始連接界面,實現界面的愈合。
關鍵詞:
新型Ni-Co基高溫合金作為一種Al + Ti含量高達7.5%以上的難變形沉淀硬化型合金,傳統的鎢極氬弧焊(TIG)和惰性氣體保護焊(MIG)由于焊接接頭存在較大的裂紋敏感性并不適用于新型合金的焊接[13]。隨著航空發動機熱端關鍵部件結構越來越復雜,尺寸越來越大,電子束焊、摩擦焊、擴散焊等焊接技術在實際應用過程中也存在一定的局限性,已不能滿足高溫合金部件的制備需求。Han等[14]和Osoba等[15]分別研究了K465和Haynes282鎳基高溫合金的電子束焊接接頭組織,發現接頭焊縫中均存在Ti和Al元素的偏析,被認為是K465接頭產生裂紋的主要原因,嚴重影響了合金的力學性能。Ravisankar等[16]研究了SU263鎳基高溫合金固態擴散焊的接頭組織,表明界面孔洞和第二相的存在抑制了合金界面的愈合,接頭的機械性能遠低于母材。Sah等[17]和Zhang等[18]的研究也發現了相同的現象。Xiong等[19]對GH4099擴散焊接頭連接行為的研究表明,焊接界面析出的碳化物阻礙了界面的愈合,導致界面存在大量孔洞。此外,固態擴散焊需要進行長時間的保溫以保證焊接質量。旋轉摩擦焊只適用于形狀規則合金的焊接,對于異形構件的焊接存在一定的困難,同時旋轉摩擦焊在焊接過程中存在界面受熱不均勻現象,不適合大體積合金的焊接[20]。因此需要探索一種新的焊接方法解決鎳基高溫合金在焊接領域存在的問題。
塑性變形連接作為一種新型的焊接方法,主要應用于不銹鋼、鋁合金的焊接,并取得了良好的連接效果[21,22]。塑性變形連接是在固態擴散焊的基礎上對合金施加大變形,在熱力耦合的作用下,通過界面原子的互擴散實現合金的連接[23,24]。Zhou等[25]研究了14YWT合金的塑性變形連接,表明提高溫度和增加變形量有利于合金界面的愈合。Zhang等[26]研究了Cu的塑性變形連接過程,結果表明界面晶界的遷移有利于消除連接界面,實現Cu的連接,且界面不存在有害相。Xie等[27]研究了316LN不銹鋼在塑性變形連接過程中界面氧化物對不銹鋼連接質量的影響,表明界面形成的氧化膜在后續保溫過程中發生分解,界面的氧最終以納米級的Al2O3氧化物顆粒形式彌散分布于界面附近,對界面的愈合沒有明顯的影響。上述結果表明塑性變形連接作為一種新型焊接方法可用于Ni-Co基高溫合金的焊接。
鎳基高溫合金作為一種低層錯能材料,在塑性變形過程中,合金中以位錯形式存儲的應變儲能會以動態再結晶形式消除。而由于塑性變形的引入,推測在合金的塑性變形連接過程中也存在動態再結晶現象。然而,由于塑性變形連接過程中連接界面的存在,可能會使合金的再結晶行為變得復雜。因此有必要對塑性變形連接過程界面組織的演化行為進行研究,探究新型Ni-Co基高溫合金在塑性變形連接過程中界面的再結晶行為,并闡述界面愈合機制。
本工作以新型Ni-Co基高溫合金為研究對象,采用光學顯微鏡(OM)、電子背散射衍射(EBSD)、透射電子顯微鏡(TEM)等手段研究了不同變形參數下界面的再結晶行為,對塑性變形過程中的再結晶機制進行了探究,同時采用室溫拉伸實驗評估了界面的結合強度,并對界面的愈合機制進行探討,為后續的工程化應用奠定基礎。
1 實驗方法
1.1 實驗材料
實驗材料為經真空感應熔煉+電渣重熔熔煉+真空自耗熔煉制備的新型Ni-Co基高溫合金鑄錠,化學成分(質量分數,%)為:Co 25.3,Cr 13.93,Al + Ti 7.7,Mo + W 3.8,C + B + Zr 0.04~0.11,Ni余量。為改善合金的變形能力,對合金鑄錠進行高溫均勻化處理(1160℃、3 h + 1200℃、1.5 h)。
1.2 塑性變形連接實驗
首先采用電火花線切割從均勻化態的合金上切取8 mm × 8 mm × 6 mm的方形試樣,然后將2個待連接試樣的表面進行機械磨拋和超聲清洗處理,以消除表面的氧化膜和污染物。隨后將2個試樣采用銅膠帶固定并放置于Gleeble 3500熱模擬機中,將K型熱電偶焊在試樣界面的中心部位,如圖1a所示。塑性變形連接的應變速率為0.001 s-1,變形溫度為1000~1200℃,變形量為5%~40%,真空度為0.133 Pa。試樣以5℃/s的加熱速率升溫至目標溫度后保溫5 min,以使試樣受熱均勻,隨后進行塑性變形連接。為減少試樣與機器接觸面的摩擦力,在試樣兩端分別放置了鉭片、高溫潤滑脂和石墨片。
圖1
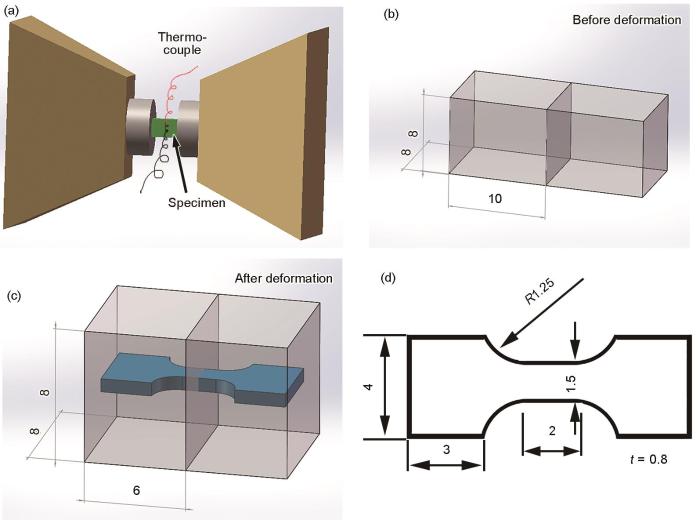
圖1 實驗原理示意圖
(a) schematic of plastic deformation bonding (b, c) schematics and location of tensile specimen processing (unit: mm) (d) dimensions of the tensile test specimen (t—thickness) (unit: mm)
Fig.1 Schematic representation of the experiment
1.3 組織及性能表征
采用電火花線切割沿平行于壓縮方向從試樣中心剖開,試樣經過機械磨、拋處理后,采用Lab. A1 OM進行組織觀察,金相組織的腐蝕劑為CuSO4 (4 g) + HCl (20 mL) + CH3CH2OH (100 mL)。枝晶組織采用電解腐蝕,腐蝕液為CrO3 (15 g) + H3PO4 (150 mL) + H2SO4 (10 mL),腐蝕電壓為5 V,腐蝕時間為15 s。采用MIRA3型SEM及其附帶的EBSD探頭對試樣界面組織進行表征,EBSD試樣采用電解拋光,電解拋光液為CH3OH (80 mL) + H2SO4 (20 mL),電解電壓為25 V,拋光時間為25 s。EBSD掃描步長視晶粒尺寸采用1.5~2.5 μm,后續數據處理均采用Channel 5軟件。采用Tecnai G2 20 TEM對塑性變形連接后的試樣界面進行觀察,TEM試樣采用離子減薄制備,首先采用5 keV、8°參數減薄2 h,隨后采用3 keV、4°參數減薄4 h,以保證在連接界面處存在可供觀察的薄區。
為評估塑性變形連接試樣的界面結合強度,采用Z2.5 TH型帶有激光引伸計的小尺寸拉伸試驗機對試樣進行力學性能檢測。值得注意的是,拉伸試樣為8 mm × 8 mm × 10 mm的方形試樣,同時為比較不同變形量下接頭的力學性能,制備了8 mm × 8 mm × 20 mm的對照組,2類試樣的變形量分別為20%和40%。變形后的接頭經過固溶和時效處理后(1100℃、1 h + 760℃、4 h)采用電火花線切割進行拉伸試樣的制備,取樣位置及拉伸試樣尺寸如圖1b~d所示,拉伸試樣取樣位置為連接試樣的中心部位,即大變形區域。
2 實驗結果及分析
圖2
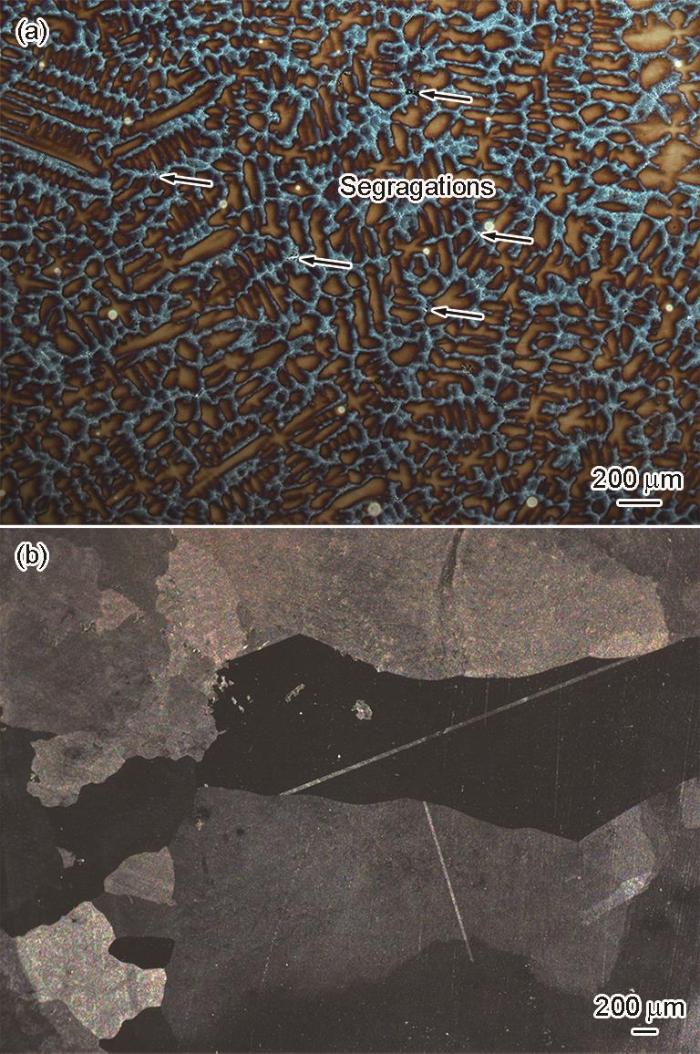
圖2 Ni-Co基高溫合金鑄態組織及均勻化態顯微組織的OM像
Fig.2 OM images of microstructures of as-cast (a) and homogenized (b) Ni-Co base superalloy
2.1 塑性變形連接工藝對界面組織的影響
2.1.1 不同變形溫度下界面的演變
圖3為Ni-Co基合金在應變速率為0.001 s-1時不同變形溫度下顯微組織的OM像及其流變應力曲線。當變形溫度較低時,合金中的原始晶粒被拉長,合金的原始連接界面清晰可見,趨于平直,如圖3a和b所示。隨著溫度升至1100℃時,在連接界面附近沿原始晶界出現了部分動態再結晶晶粒,但連接界面沒有明顯的變化,如圖3c所示。然而當變形溫度提高到1150℃,原本平直的界面發生彎曲,且在合金的連接界面附近發生了晶界遷移,部分界面被再結晶晶粒取代,如圖3d所示。值得注意的是,當變形溫度較低時,在變形合金中可以觀察到部分沿晶界開裂的現象。這可能是因為合金初始晶粒尺寸比較大(圖2b所示),粗大的晶粒導致合金各部分受力不均勻,從而導致合金的變形能力較差,容易發生開裂現象[28~31]。當變形溫度達到1200℃時,合金發生了嚴重的沿晶界開裂現象(圖3e),這是因為變形溫度過高,強化相溶解,原本粗大的晶粒進一步長大,晶粒變形協調能力變差,導致變形過程沿晶界開裂,Liu等[29]在研究新型Ni-Co基高溫合金的熱變形行為時也發現了合金沿晶界開裂現象。圖3f為不同溫度下的流變應力-應變曲線,隨著溫度逐漸升高,流變應力不斷減小,且峰值應力對應的峰值應變也逐漸降低,這表明溫度升高有利于促進合金中原子的熱激活運動,提高晶界的遷移速率,從而促進合金的動態軟化,并將再結晶過程提前。同時,可以注意到當變形溫度超過1150℃時,合金變形抗力明顯減少,這是因為合金中γ'強化相發生溶解(γ'的初溶溫度為1141℃)[29],位錯運動的阻力降低。上述結果表明,當塑性變形連接溫度為1150℃時,連接界面處晶界易發生弓彎現象,原始連接界面被再結晶晶粒取代,有利于界面的愈合。
圖3

圖3 應變速率為0.001 s-1,不同變形溫度下Ni-Co基高溫合金顯微組織的OM像及其流變應力-應變曲線
Fig.3 OM images of microstructures at deformation temperatures of 1000oC (a), 1050oC (b), 1100oC (c), 1150oC (d), and 1200oC (e), and the true stress-strain curves (f) of the Ni-Co base superalloy at the strain rate of 0.001 s-1
2.1.2 不同變形量下界面的演變
圖4a~e所示為塑性變形溫度為1150℃時不同變形量下Ni-Co基合金顯微組織的OM像??梢钥闯觯S著變形量的增加,原始粗大的合金晶粒得到細化,這表明在塑性變形過程中合金組織發生了動態再結晶。如圖4a和b所示,變形量較小時,原始連接界面保持平直,界面清晰可見。隨著變形量增加,連接界面的部分晶界開始變得彎曲,原始連接界面逐漸模糊,如圖4c所示,這通常被認為是應變誘導晶界遷移[32]。當變形量增加到30%,原始連接界面的晶界彎曲現象更加明顯,原始連接界面難以辨認,如圖4d所示。隨著變形量繼續增加,原始連接界面被再結晶晶粒取代,界面實現愈合,如圖4e所示。圖4f為采用截線法統計的Ni-Co基合金平均晶粒尺寸??梢钥闯?,隨著變形量不斷增加,平均晶粒尺寸逐漸減小。合金原始粗大的晶粒在10%的變形量下快速細化,但此時的晶粒尺寸不均勻。隨著變形的不斷進行,合金晶粒尺寸沒有明顯變化,但晶粒分布趨于均勻。合金平均晶粒尺寸的減小是塑性變形過程中動態再結晶細化晶粒的緣故[33]。
圖4

圖4 塑性變形溫度為1150℃,不同變形量下Ni-Co基高溫合金顯微組織的OM像以及平均晶粒尺寸統計
Fig.4 OM images of microstructures at true strains of 5% (a), 10% (b), 20% (c), 30% (d), and 40% (e), and statistics of mean grain size (f) of the Ni-Co base superalloy at the deformation temperature of 1150℃
2.2 界面性能
2.2.1 界面結合強度
上述結果表明,當變形溫度為1150℃、變形量達到40%時,Ni-Co基高溫合金塑性變形連接可取得良好的連接效果。為進一步評估接頭的結合強度,對不同變形量下接頭的室溫拉伸強度進行測試,結果如圖5所示。為了便于比較不同變形量下接頭的結合強度,采用了相同變形量的母材作為對照。變形量為20%的接頭的屈服強度僅有614 MPa,延伸率只有0.7%,力學性能遠不及變形量為20%的母材。這表明即使界面已發生部分連接,但由于界面依然存在未愈合的部分,從而導致界面強度不能達到母材水平。而對于變形量為40%的接頭,其屈服強度和抗拉強度可以達到同等變形條件下的母材水平,延伸率略低于母材。這表明隨變形量的增加,合金的結合強度顯著提高。一方面,變形量較低時,變形初期形成的氧化膜阻礙界面的接觸,導致界面的結合強度和延伸率不理想;隨著變形量的不斷增加,界面氧化膜在應力的作用下發生破碎,且由于局部氧分壓的降低,破碎的氧化物部分發生分解[27],促進了界面的相互接觸,有利于界面的愈合。另一方面,由于應力的持續作用,界面處發生應變誘導晶界遷移[34],促進了界面晶界的弓彎和遷移,提高了界面的結合強度。
圖5
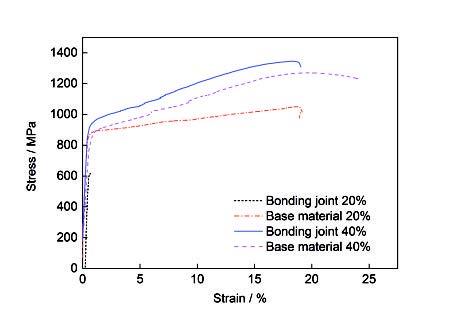
圖5 不同變形量下接頭的室溫拉伸曲線
Fig.5 Tensile curves of the joints at room temperature under different deformations
2.2.2 接頭拉伸斷口形貌
圖6所示為不同變形量下接頭和母材的拉伸斷口形貌。圖6a和c分別為變形量20%和40%的母材斷口形貌,可見在斷面上存在大量小而淺的韌窩(圖6a和c中的紅色箭頭),且在部分韌窩中存在γ'相(圖中黑色箭頭所示),可以判斷這2種不同變形量的母材斷裂方式均為韌性斷裂。對于變形量為20%的接頭,其斷裂位置在界面連接處。如圖6b中的矩形框所示,在斷面上存在大量未連接的區域。而部分連接區域由于已經發生晶界遷移(圖4c),從而在斷口上呈現出彎曲、短小的撕裂棱,如圖6b中的黑色箭頭所示。這些表明該條件下接頭的斷裂模式為韌性斷裂和脆性斷裂的混合。Zhou等[25]的研究表明,塑性變形連接過程中彎曲的晶界可以部分阻礙裂紋的擴展,改善合金的結合強度。但由于20%變形量下,界面依然存在未愈合的區域,這意味著裂紋容易沿著未連接區域擴展,從而導致合金的結合強度明顯降低。圖6d為變形量40%的接頭斷口形貌,在斷面上也存在與圖6c相似的淺而小的韌窩,呈現韌性斷裂的特征。這表明界面連接區域面積增加,顯著提高了合金的阻礙裂紋擴展的能力,從而使接頭強度達到了母材水平。
圖6
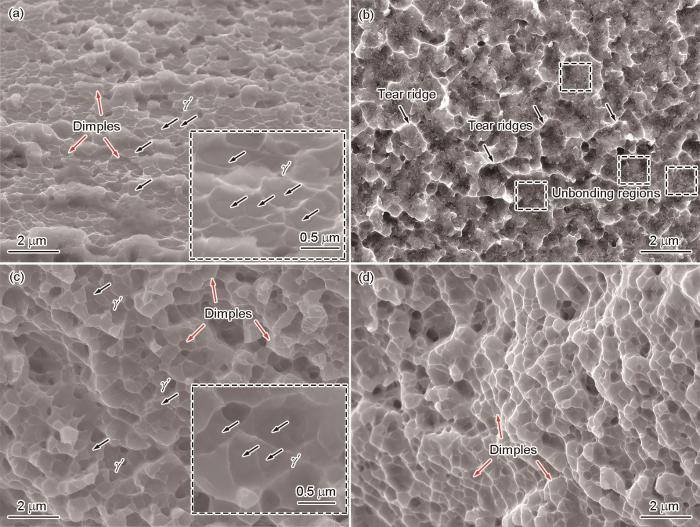
圖6 不同變形量下接頭和母材的拉伸斷口形貌
Fig.6 Tensile fracture morphologies of base material (a, c) and joints (b, d) at different deformations of 20% (a, b) and 40% (c, d)
2.3 塑性變形過程合金的再結晶行為
2.3.1 不連續動態再結晶行為
Ni-Co基高溫合金作為一種低層錯能的合金,由于其擴展位錯寬度很寬,難以通過交滑移和刃型位錯的攀移進行動態回復[35],因此在合金塑性變形過程中動態再結晶是主要的軟化機制。圖7a和c顯示了變形量分別為5%和10%的連接界面的反極圖(IPF)。可以看出,初始晶體學取向隨機分布的2個界面在小變形量的條件下,由于界面的局部接觸形成結合界面,這種結合界面可以被認為是一種由復雜位錯堆積形成的非穩定的大角度晶界,此時的連接界面由于未發生明顯的塑性變形而保持平直。反觀非連接界面區域的晶界則存在褶皺、彎曲的現象,有的晶界甚至嵌入了其相鄰的晶粒,這通常被認為是應力誘導晶界遷移[32],即在變形初始,由于晶粒間變形的不協調性,以位錯形式存儲于變形合金內部的形變儲能,會在晶界兩側產生位錯密度梯度,如圖7b和d所示,這種應變梯度會驅動晶界向位錯密度較高的一側移動,在宏觀上表現為晶界的弓彎,而這些弓彎區域則為合金的再結晶提供形核質點,這是典型的不連續動態再結晶[36]。隨著變形量增加到20%,原本平直的連接界面開始變得彎曲,界面處的晶界開始向對側的晶粒弓出,如圖7e所示。從圖7f可知,連接界面兩側存在的應變梯度是界面晶界遷移的驅動力。同時也注意到,連接界面晶界的弓彎行為與非界面處的晶界遷移行為相比,存在一定的滯后性,這可能是因為平直晶界的遷移需要更高的能量,即需要較大的變形量為其提供驅動力。隨著變形量增加到30% (圖7g),原始的連接界面幾乎已經消失,取而代之的則是通過不連續動態再結晶形核、長大的晶粒。結合圖7h可知,連接界面處的晶粒僅存在少量的應變梯度,可認為在30%的變形量下,界面處發生了完全再結晶。當變形量增加到40%時,原始界面已完全消失,如圖7i所示。結合圖7h可以發現,在已發生再結晶晶粒的內部依然存在較高的應變梯度,這可能是因為由于應力的持續作用,在再結晶晶粒內部發生了二次應變集中現象,Xie等[36]在研究鑄造鎳基高溫合金的再結晶行為過程中也發現了類似的現象。
圖7
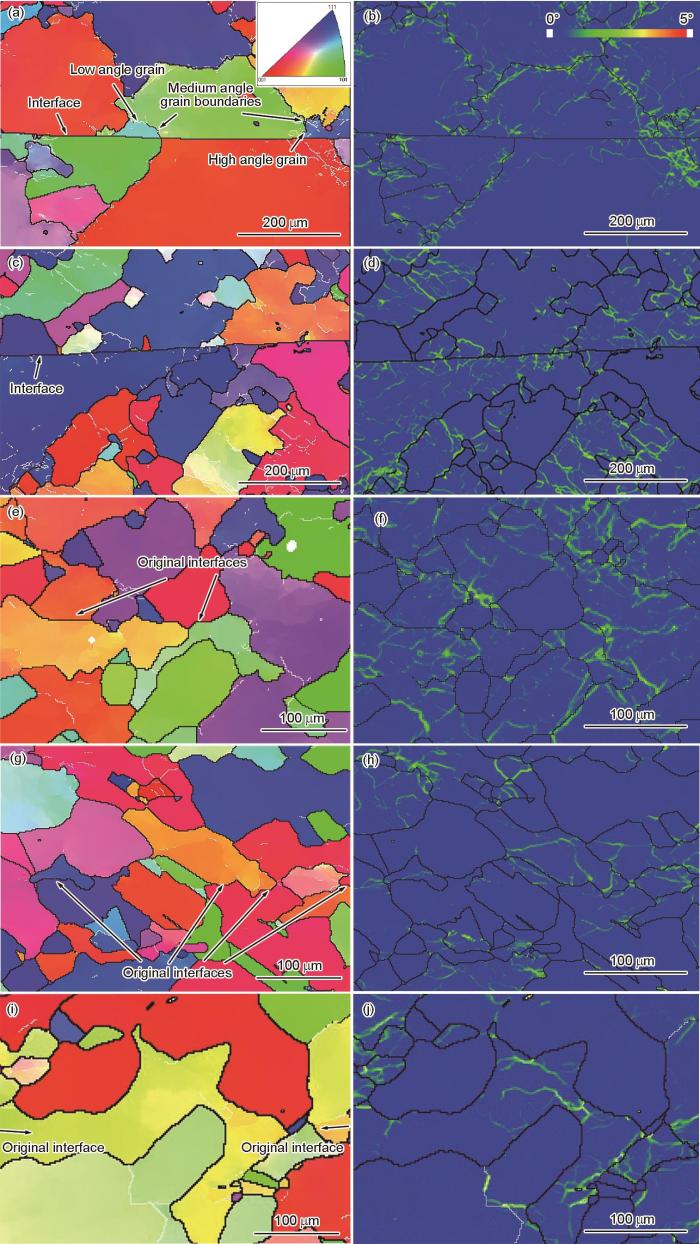
圖7 塑性變形溫度為1150℃時,不同變形量下界面組織的反極圖(IPF)及對應的局部取向差(LAM)圖
(a, b) 5% (c, d) 10% (e, f) 20% (g, h) 30% (i, j) 40%
Fig.7 Inverse pole figure (IPF) maps (a, c, e, g, i) and local average misorientation (LAM) maps (b, d, f, h, j) of the interface microstructure under different deformations at 1150℃
2.3.2 連續動態再結晶
連續動態再結晶通常以亞晶的旋轉為特征,從而促進小角度晶界之間的取向差不斷增加,進而轉變為大角度晶界[37]。圖7中可以發現存在著一些不連續的大角度晶界,即大角度晶界和中等角度晶界相連或者小角度晶界和中等角度晶界相連,這些現象表明隨著變形量的不斷增加,亞晶不斷發生轉動,在變形的過程存在連續動態再結晶的行為[38]。為了更好地理解變形過程中連續動態再結晶機制,不同變形量下局部取向差分布如圖8所示。從圖8a可以看出,當變形量為5%時,小角度晶界的數量相對較高,而中等角度晶界的數量幾乎為零。隨著變形量的增加,小角度晶界的數量開始下降,大角度晶界的數量明顯增加,而中等角度晶界的數量也有所增加,這表明在這個過程中存在著連續動態再結晶過程。此外,當變形量為40%時,依然存在許多小角度晶界,這是二次應力集中發生所致,與局部取向差(LAM)圖的分析相一致。
圖8
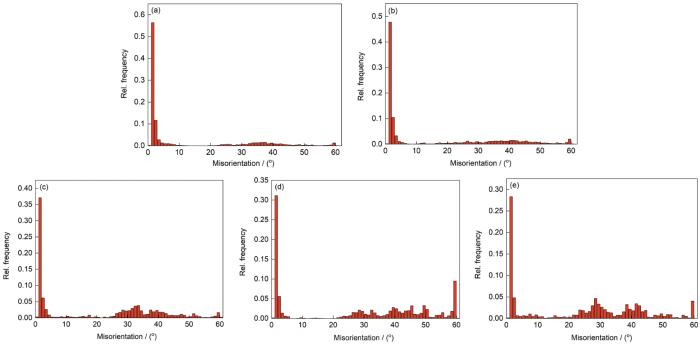
圖8 塑性變形溫度為1150℃,不同變形量下界面組織的取向差分布
(a) 5% (b) 10% (c) 20% (d) 30% (e) 40%
Fig.8 Misorientation distributions of the interface microstructures under different deformations at 1150℃
2.3.3 界面微觀組織演化
圖9
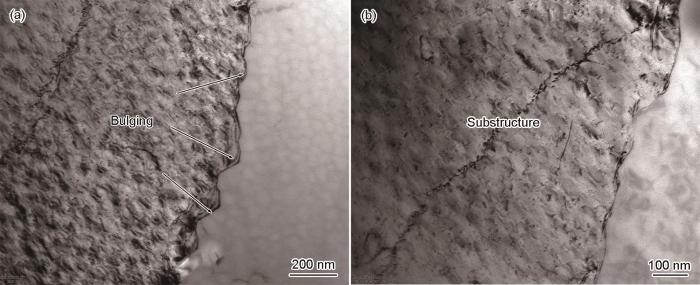
圖9 變形溫度為1150℃,20%變形量下界面組織的TEM像
Fig.9 TEM images of bulging of interfacial grain boundaries (a) and interfacial substructure (b) at a deformation temperature of 1150℃ and 20% deformation
2.4 界面愈合機制
圖10為塑性變形連接過程中界面愈合機制的示意圖。本工作中采用的是均勻化態試樣,因此初始的晶粒尺寸粗大,如圖10a所示。在塑性變形的初始階段,由于各晶粒間變形不協調,在晶界附近積累了大量位錯,從而導致應變誘導晶界遷移,晶粒發生局部弓彎。根據前述分析,在變形的初始階段存在連續動態再結晶,即小角度晶界通過不斷旋轉,轉變為大角度晶界,如圖10b和c所示。在變形的初期主要是界面附近的粗大晶粒在連續和不連續動態再結晶的協同作用下發生細化。研究[30]表明,較小尺寸的晶粒在變形的過程中由于界面張力的作用更容易在擴散焊過程中發生遷移。因此,細化的晶粒在持續應變的作用下更容易發生弓彎,使得界面晶界發生遷移,促進連接界面的愈合。值得注意的是,在持續應變的作用下,晶界弓彎區域由于不均勻應變的作用,會在此處形成亞晶界,這些亞晶界隨后逐漸轉變為大角度晶界,從而促進弓彎部分從原始晶粒中脫離,成為再結晶晶核[40],占據原始的界面晶界,如圖10d和e所示,鐘茜婷等[41]在研究Incoloy 028合金的再結晶行為過程中也發現了相同的現象。上述分析表明在塑性變形連接過程中,原始粗大晶粒由于動態再結晶的作用首先發生細化,隨后隨著應力的持續作用,界面處細化的晶粒在連續再結晶的輔助作用下,通過界面晶界的遷移(不連續動態再結晶)消除了原始連接界面。最后,隨著變形的進一步增加,原始連接界面完全被再結晶晶粒占據,界面實現完全愈合,如圖10f所示。
圖10
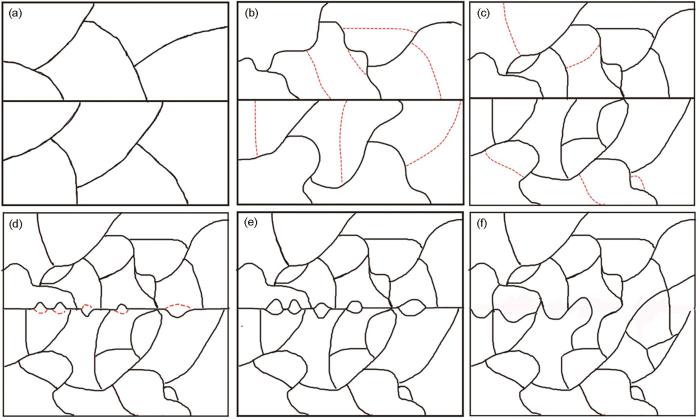
圖10 塑性變形連接界面愈合機制
(a) original coarse grains (b, c) grain refinement near the interface (d, e) bulging of the interfacial grains (Fig.10e shows the recrystallization nucleation of interfacial grains) (f) bonding of the interface
Fig. 10 Interface bonding mechanism during plastic deformation bonding
3 結論
(1) 提高變形溫度有助于Ni-Co基高溫合金連接界面動態再結晶的發生,促進連接界面的愈合。當變形溫度達到1200℃時,合金容易發生開裂現象。隨著變形量不斷增加,原始粗大晶粒發生細化并趨于均勻,同時應變誘導晶界遷移促進界面愈合,界面結合強度也相應提高。
(2) 1150℃是目前最優的塑性變形連接溫度。1150℃變形時,合金的變形抗力小,開裂風險低。同時,為實現新型Ni-Co基高溫合金的塑性變形連接,合金的變形量需達到40%以上,此時界面完全愈合,界面結合強度可達到母材同等水平。
(3) 在塑性變形連接過程中,界面附近原始粗大的晶粒在應力和溫度的耦合作用下首先通過連續動態再結晶和不連續動態再結晶的協同作用使晶粒發生細化。隨后,界面處細小的晶粒在連續動態再結晶的輔助作用下,通過不連續動態再結晶的作用,促使界面晶界發生遷移,消除原始的連接界面,實現界面的愈合。