分享:高Cr鐵素體耐熱鋼與奧氏體耐熱鋼的異種材料擴(kuò)散連接接頭組織演變及力學(xué)性能
開展了高Cr鐵素體耐熱鋼與TP347H奧氏體耐熱鋼的異種材料真空擴(kuò)散連接實驗,研究了擴(kuò)散連接時間及焊后熱處理工藝對擴(kuò)散影響區(qū)組織演變和力學(xué)性能的影響。結(jié)果表明,隨著擴(kuò)散連接時間的延長,界面結(jié)合率逐漸增加。變形儲存能差異與位錯滑移的相互作用下,在擴(kuò)散連接界面處發(fā)生動態(tài)再結(jié)晶形成了細(xì)小晶粒,最終演化成鋸齒狀的界面結(jié)合形態(tài)。擴(kuò)散連接區(qū)晶界與晶粒內(nèi)部析出細(xì)小彌散的MX、M23C6相。焊后熱處理之后擴(kuò)散連接區(qū)的晶粒進(jìn)一步細(xì)化,位錯相對穩(wěn)定化,位錯密度減少,小角度晶界增多,元素擴(kuò)散更加充分。對獲得的擴(kuò)散連接試樣進(jìn)行不同溫度的拉伸實驗,斷裂位置均位于基體中,說明獲得了高質(zhì)量的異種材料擴(kuò)散連接接頭。
關(guān)鍵詞:
火力發(fā)電量在世界總發(fā)電量中占有重要的主導(dǎo)地位[1]。長期以來,我國電源結(jié)構(gòu)中火電發(fā)電量超過80%,在未來相當(dāng)長的時間內(nèi)火電將繼續(xù)成為我國的主體能源[2,3]。但是,火力燃煤發(fā)電不僅需要消耗大量煤炭資源,而且會排放出大量的SO2、CO2、NO x 等污染環(huán)境的氣體[4],不僅會造成我國的經(jīng)濟(jì)損失,而且嚴(yán)重影響著國民的身體健康。因此,采用更先進(jìn)的技術(shù)以提高燃煤發(fā)電機組的工作效率成為我國電力發(fā)展的緊迫任務(wù)。為了迎合以上發(fā)展需求,高效節(jié)能的超超臨界機組己成為電力工業(yè)的研發(fā)方向。目前,各國紛紛開展大量的研發(fā)工作,不斷突破火電站機組的運行參數(shù),電廠的熱效率隨著蒸汽壓力和蒸汽溫度的升高而得到不斷提升,同時蒸汽參數(shù)的升高對火力發(fā)電機組鍋爐管道用鋼的使用性能提出了更高的要求[5,6]。
超超臨界火電機組內(nèi)部溫度略有差異,高溫區(qū)域需要高溫性能較好的奧氏體耐熱鋼。從經(jīng)濟(jì)角度出發(fā),溫度較低的部分可以采用價格便宜、高溫性能稍弱的高Cr鐵素體耐熱鋼,因此,超超臨界火電機組中不可避免地會存在諸如高Cr鐵素體耐熱鋼與奧氏體耐熱鋼異種材料連接接頭。
高Cr鐵素體耐熱鋼與奧氏體耐熱鋼部件之間的異種連接方式多種多樣。如許鴻吉等[7]采用熔化極活性氣體保護(hù)電弧焊(MAG)獲得1.4003不誘鋼/0Cr18Ni9不銹鋼異種鋼焊接接頭,其接頭的抗拉強度高于母材,彎曲性能良好。但鐵素體不銹鋼一側(cè)熱影響區(qū)的沖擊性能較差,且隨著溫度的降低,其沖擊性能顯著降低。Muthupandi等[8]報道了利用電子束焊接(EBW)及鎢極氣體保護(hù)焊技術(shù)(GTAW)獲得鐵素體-奧氏體耐熱鋼異種接頭,但焊接熔合區(qū)在枝晶內(nèi)出現(xiàn)元素偏析,導(dǎo)致接頭的耐蝕性和機械性能下降。Jang等[9]報道了利用GTAW與電弧焊技術(shù)(AW)獲得低合金鋼與316不銹鋼異種接頭,但金屬焊縫中枝晶組織發(fā)達(dá),枝晶區(qū)域內(nèi)觀察到明顯的偏析和二次相沉淀。同時,傳統(tǒng)的熔焊技術(shù)獲得的焊縫厚度不均勻,造成了拉伸性能及顯微強度的差異。Thakare等[10]報道了利用GTAW獲得了P91馬氏體鋼與SS304L奧氏體鋼異種材料焊接接頭,焊縫熔合區(qū)析出物不均勻,存在明顯的粗晶,并且沿焊接接頭的硬度分布不均勻。因此,利用傳統(tǒng)的熔焊技術(shù)獲得的異種材料擴(kuò)散連接接頭在組織和性能方面存在一定的不足[11]。
固相擴(kuò)散連接技術(shù)是解決異種金屬高強度連接的有效方法,被作為關(guān)鍵新材料技術(shù)開發(fā)領(lǐng)域的熱點在新材料制備中發(fā)揮著關(guān)鍵和核心作用[12]。Solonin等[13]通過擴(kuò)散連接技術(shù)實現(xiàn)不銹鋼/鋁合金之間的連接,獲得的焊接接頭具有很高的焊接強度。Balasubramanian等[14]通過擴(kuò)散連接技術(shù)實現(xiàn)了鋁合金和鎂合金有效擴(kuò)散連接,建立了鎂合金中Al含量與優(yōu)化擴(kuò)散連接參數(shù)之間的關(guān)系,以獲得高質(zhì)量的鋁、鎂合金焊接接頭。Huang等[15]通過擴(kuò)散連接技術(shù)成功地將W和低活化鐵素體馬氏體鋼(RAFM鋼)與Fe中間層擴(kuò)散連接,W/Fe/RAFM鋼接頭在剪切實驗中表現(xiàn)出較高的結(jié)合強度(> 240 MPa)和延展性。
綜上所述,當(dāng)采用傳統(tǒng)熔化焊技術(shù)(如激光焊、氬弧焊等)時,由于冷卻速率過快經(jīng)常導(dǎo)致形成脆性組織甚至出現(xiàn)裂紋,同時也會引入N、O、H等雜質(zhì)元素,從而降低接頭的性能,而固相擴(kuò)散連接更易獲得室溫和高溫強度良好的接頭,并且連接接頭能夠在保證良好質(zhì)量的前提下,保持均質(zhì)母材或者合金原有的主要性能。在合適的參數(shù)條件下,擴(kuò)散連接接頭鄰近區(qū)域都具有高的強度和優(yōu)良的塑性。因此,擴(kuò)散連接是一種相對理想的焊接方法,目前對于高Cr鐵素體耐熱鋼/奧氏體耐熱鋼異種材料固相連接方面的研究尚不夠成熟。同時,電站焊接施工大多數(shù)情況是在現(xiàn)場執(zhí)行,真空擴(kuò)散連接工作很難得到開展,如果車間或工廠采用擴(kuò)散連接的方式將高Cr鐵素體耐熱鋼與奧氏體耐熱鋼異種材料連接接頭焊好,那么現(xiàn)場異種鋼焊接將變成同種鋼連接(高Cr鐵素體耐熱鋼/高Cr鐵素體耐熱鋼和奧氏體耐熱鋼/奧氏體耐熱鋼焊接),會大大降低施工難度。
因此,本工作開展了高Cr鐵素體耐熱鋼與TP347H奧氏體耐熱鋼的異種材料真空擴(kuò)散連接實驗,研究了擴(kuò)散連接時間及焊后熱處理工藝對擴(kuò)散連接區(qū)組織與力學(xué)性能的影響。通過澄清擴(kuò)散連接區(qū)組織演化規(guī)律及界面結(jié)合行為,為高Cr鐵素體耐熱鋼/奧氏體耐熱鋼異種材料擴(kuò)散連接工藝優(yōu)化提供理論指導(dǎo)與實驗支撐。
1 實驗方法
實驗用高Cr鐵素體耐熱鋼與TP347H奧氏體耐熱鋼的實際成分如表1所示。取直徑為15 mm、高度為25 mm的高Cr鐵素體耐熱鋼與TP347H奧氏體耐熱鋼的圓柱樣品若干。真空擴(kuò)散連接前,用磨床將所有試樣的連接表面進(jìn)行磨削,以獲得均勻的表面粗糙度(Ra = 0.912 μm)。用丙酮超聲脫脂30 min,乙醇清洗30 min,然后用20%HNO3 + 5%HF + 75%H2O (體積分?jǐn)?shù))的混合溶液對圓柱形樣品進(jìn)行酸洗,去除氧化膜。采用最高真空度為1.33 × 10-3 Pa的Gleeble 3500熱模擬試驗機進(jìn)行真空擴(kuò)散連接,升溫與降溫速率均為150℃/min。已知真空擴(kuò)散連接溫度通常控制在(0.6~0.8)Tm (Tm為母材熔點)范圍內(nèi),高Cr鐵素體耐熱鋼熔點為1312~1745℃,TP347H奧氏體耐熱鋼熔點為1398~1427℃,因此將擴(kuò)散連接溫度設(shè)定為1050℃,擴(kuò)散連接時間分別為5、15、30、60和120 min,施加15 MPa單軸壓力以保證連接界面緊密接觸,擴(kuò)散連接工藝曲線如圖1a所示。焊后熱處理工藝為1050℃正火30 min,750℃回火90 min,升溫速率為10℃/min,工藝曲線如圖1b所示。
表1 實驗用材料的化學(xué)成分 (mass fraction / %)
Table 1
Material | C | Cr | W | Mn | Si | V | Ta | P | Mo | Ni | Nb | N | Fe |
---|---|---|---|---|---|---|---|---|---|---|---|---|---|
High Cr F | 0.092 | 8.87 | 1.71 | 0.28 | 0.01 | 0.19 | 0.002 | < 0.005 | - | - | - | - | Bal. |
TP347H | 0.059 | 17.6 | - | 1.59 | - | - | - | 0.024 | 0.116 | 10.71 | 0.54 | 0.013 | Bal. |
圖1
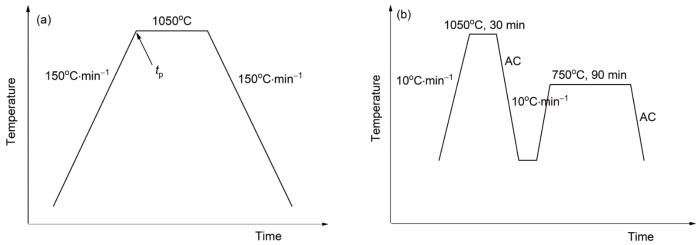
圖1 實驗工藝曲線示意圖
(a) diffusion-bonding (tp—the time to apply pressure) (b) post weld heat treatment (PWHT) (AC—air cooling)
Fig.1 Sketch diagrams for the process curves
將不同擴(kuò)散連接時間獲得的接頭垂直于連接界面進(jìn)行機械加工。采用DMI8光學(xué)顯微鏡(OM)、S4800掃描電子顯微鏡(SEM)和JEM-2100F透射電子顯微鏡(TEM)對擴(kuò)散連接區(qū)的微觀組織進(jìn)行表征,計算擴(kuò)散連接界面結(jié)合率。為觀察金相組織,依次使用400~2500號的SiC砂紙進(jìn)行機械拋光,用2 g CuCl2 + 40 mL HCl + 80 mL C2H5OH混合溶液腐蝕試樣。對TEM樣品進(jìn)行機械拋光,然后進(jìn)行離子束減薄。用20%HClO4 + 10%C3H5(OH)3 + 70%C2H5OH (體積分?jǐn)?shù))的混合溶液電解拋光制備電子背散射衍射(EBSD)樣品,并用MTEX軟件分析EBSD數(shù)據(jù)。使用能譜儀(EDS)對擴(kuò)散連接區(qū)的元素分布進(jìn)行定性分析。采用Instron 5565雙立柱電子萬能試驗機在25和600℃下進(jìn)行小尺寸拉伸實驗,拉伸試樣尺寸示意圖如圖2所示。采用OM和SEM對試樣的宏觀及微觀斷口形貌進(jìn)行觀察。
圖2

圖2 25和600℃拉伸試樣示意圖
(a) 25oC (b) 600oC
Fig.2 Schematics of tensile specimen (unit: mm, Ra—roughness)
2 實驗結(jié)果與討論
2.1 實驗用原材料顯微組織
高Cr鐵素體耐熱鋼顯微組織由δ-鐵素體和板條馬氏體組成,其中δ-鐵素體面積分?jǐn)?shù)為6%左右,如圖3a所示。室溫下抗拉強度為1215~1230 MPa。TP347H奧氏體耐熱鋼顯微組織為單相奧氏體組織,如圖3b所示。室溫下抗拉強度為610~615 MPa。
圖3
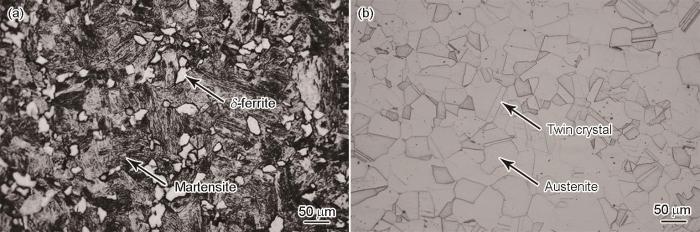
圖3 擴(kuò)散連接試樣母材的OM像
(a) high Cr heat-resistant steel sample
(b) TP347H austenitic heat-resistant steel sample
Fig.3 OM images of the parent metals for diffusion-bonding
2.2 擴(kuò)散連接接頭的界面結(jié)合與孔洞閉合行為
圖4顯示了在1050℃、15 MPa壓力下,在不同擴(kuò)散連接時間下擴(kuò)散連接接頭的OM和SEM像。真空擴(kuò)散連接時間為5 min時,界面處可以明顯看到只有少量界面緊密結(jié)合在一起,如圖4a1~a3所示。這一階段為塑性變形階段[16,17]。由于連接表面存在粗糙度,凹凸不平的表面第一次接觸以及外部載荷集中作用,導(dǎo)致大的應(yīng)力集中,從而誘發(fā)材料發(fā)生塑性變形,隨著變形繼續(xù),接觸面積增加,最終降低了局部應(yīng)力,減緩了塑性變形。連接界面所受的壓力小于材料屈服強度時,塑性變形停止。塑性變形階段實際接觸界面要比名義上的接觸面積小很多,是塑性變形的瞬間作用,與擴(kuò)散連接的時間無關(guān)[18]。擴(kuò)散連接時間延長至15和30 min時,接頭處的孔洞形狀變得越來越趨近于圓形,如圖4b3和c3所示,此為表面源擴(kuò)散階段[19]。由于界面孔洞曲率存在差異,孔洞表面的化學(xué)勢不同,使得原子能夠很快沿著孔洞表面進(jìn)行遷移,大曲率處的物質(zhì)流向小曲率處,導(dǎo)致孔洞形狀發(fā)生變化。當(dāng)孔洞的表面曲率相同,即為圓形時,表面源機制停止。由此可見,表面源擴(kuò)散階段作用的驅(qū)動力為孔洞表面所存在的曲率差,這一階段可以忽略孔洞的體積變化。擴(kuò)散連接時間進(jìn)一步延長至60 min時孔洞數(shù)量減少,逐漸形成良好的擴(kuò)散連接接頭,如圖4d1~d3所示,此為界面源擴(kuò)散階段[20,21]。這一階段主要受隨后的擴(kuò)散和晶界遷移控制。沿連接界面觀察到新生成的細(xì)小晶粒,導(dǎo)致晶粒細(xì)化。這些細(xì)化的晶粒通過提供許多界面促進(jìn)晶界遷移,從而導(dǎo)致擴(kuò)散連接過程中的擴(kuò)散率增加,進(jìn)而提高了擴(kuò)散連接界面結(jié)合率。當(dāng)擴(kuò)散連接時間達(dá)到120 min時,在連接界面幾乎看不到孔洞的存在,說明在擴(kuò)散連接過程中獲得了良好的擴(kuò)散連接接頭,如圖4e1~e3所示,此階段為冪定律蠕變機制控制階段[22]。擴(kuò)散連接過程中,金屬的微觀蠕變對孔洞的閉合也有影響。隨著孔洞尺寸的變化,擴(kuò)散連接界面附近的應(yīng)力與應(yīng)變速率也隨之發(fā)生變化,孔洞在應(yīng)力的作用下消失,形成可靠的擴(kuò)散連接界面。因此,隨著保溫時間的延長,連接界面變得越來越模糊,有利于孔洞閉合,形成牢固的連接界面。
圖4

圖4 連接溫度1050℃、連接壓力15 MPa,不同擴(kuò)散連接時間條件下擴(kuò)散連接試樣接頭微觀組織的低倍和高倍OM像及SEM像
(a1-a3) 5 min (b1-b3) 15 min (c1-c3) 30 min (d1-d3) 60 min (e1-e3) 120 min
Fig.4 Low (a1-e1) and high (a2-e2) magnified OM images and SEM images (a3-e3) showing the microstructures of the diffusion-bonding joints with the bonding temperature of 1050oC and bonding stress of 15 MPa, for the different bonding time
為了定量評估擴(kuò)散連接接頭的質(zhì)量,圖5給出了擴(kuò)散連接時間與擴(kuò)散連接界面結(jié)合率之間的關(guān)系。擴(kuò)散連接界面結(jié)合率的計算公式為:
式中,ε為擴(kuò)散連接界面結(jié)合率,L為界面總長度(μm),ΣLi 為未連接部分長度之和(μm)。結(jié)果表明,當(dāng)擴(kuò)散連接時間為5 min時,擴(kuò)散連接界面結(jié)合率較低,隨著擴(kuò)散連接時間的延長,擴(kuò)散連接界面結(jié)合率增大。當(dāng)擴(kuò)散連接時間為120 min時,擴(kuò)散連接界面結(jié)合率高達(dá)98.32%。同時,由圖5可以看出,擴(kuò)散連接速率隨擴(kuò)散連接時間延長呈現(xiàn)降低的趨勢,其原因為:(1) 真空擴(kuò)散連接過程先經(jīng)歷表面源擴(kuò)散機制,再經(jīng)歷界面源擴(kuò)散機制,表面擴(kuò)散克服勢壘所需的能量要小些,元素擴(kuò)散速率較快;(2) 真空擴(kuò)散連接進(jìn)行至一定的階段,2種基體之間元素濃度差減小,降低了元素擴(kuò)散速率。
圖5
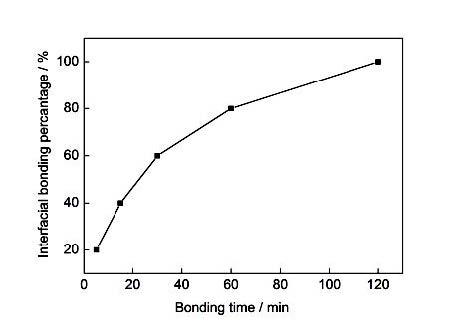
圖5 不同擴(kuò)散連接時間的界面結(jié)合率
Fig.5 Interfacial bonding percentage as a function of the diffusion-bonding time
2.3 擴(kuò)散連接區(qū)的組織與演化
合適的焊后熱處理工藝可以改善擴(kuò)散連接接頭的組織和力學(xué)性能,消除焊接接頭的內(nèi)應(yīng)力,有利于獲得優(yōu)質(zhì)的擴(kuò)散連接接頭[23,24]。圖6顯示了擴(kuò)散連接時間為120 min時擴(kuò)散連接試樣擴(kuò)散連接區(qū)焊后熱處理后的SEM像。與圖4e3對比可以看出,經(jīng)焊后熱處理后,試樣擴(kuò)散影響區(qū)組織晶粒更加細(xì)小,這是由于焊后熱處理使得元素擴(kuò)散更加充分,母材中含有Nb等強碳氮化物形成元素,它們和C、N都有極強的親和力,與之形成相應(yīng)的極為穩(wěn)定的化合物彌散分布在試樣中,對位錯起到釘扎作用,從而達(dá)到一定的晶粒細(xì)化作用[25]。
圖6

圖6 連接溫度1050℃、連接壓力15 MPa、連接時間120 min的擴(kuò)散連接試樣擴(kuò)散連接區(qū)經(jīng)焊后熱處理后的SEM像
Fig.6 SEM images of the diffusion-bonding joints with the bonding temperature of 1050oC, bonding stress of 15 MPa, and the bonding time of 120 min after PWHT
為了進(jìn)一步驗證適當(dāng)?shù)暮负鬅崽幚砉に嚳梢约?xì)化晶粒,圖7a顯示了擴(kuò)散連接時間為120 min時未經(jīng)焊后熱處理的擴(kuò)散連接試樣擴(kuò)散連接區(qū)的EBSD像。可見,中間為擴(kuò)散連接界面,上方為fcc結(jié)構(gòu)的TP347H奧氏體耐熱鋼晶粒,主要由單一的等軸奧氏體晶粒組成,靠近擴(kuò)散連接界面的晶粒尺寸較小,遠(yuǎn)離擴(kuò)散連接界面的晶粒尺寸較大。下方為bcc結(jié)構(gòu)的高Cr鐵素體耐熱鋼晶粒,主要由板條馬氏體組成。擴(kuò)散連接界面處晶粒的取向發(fā)生變化,可以觀察到細(xì)小的呈串聯(lián)狀分布的等軸晶粒,說明擴(kuò)散連接過程中試樣擴(kuò)散連接區(qū)發(fā)生了動態(tài)再結(jié)晶。這是因為塑性變形的不斷增加,晶粒內(nèi)由于位錯的交滑移與攀移形成大量亞晶,不同晶粒之間變形儲存能存在差異,原本平直的晶界會產(chǎn)生鋸齒狀凸起。隨著應(yīng)變不斷增加,晶界處凸起部分在位錯滑移的協(xié)助下將會隨之發(fā)生轉(zhuǎn)動;而且隨著應(yīng)變增加,凸起部分與晶粒之間的取向差不斷增加,凸起部分最終成為擁有較大角度晶界的動態(tài)再結(jié)晶晶粒,提高試樣塑性變形后強度[26]。這些晶粒在鐵素體晶界處形核、長大,擴(kuò)散連接界面兩側(cè)相鄰2個不同組織晶粒的晶界有相互連結(jié)的現(xiàn)象,即界面兩側(cè)的fcc結(jié)構(gòu)晶粒與bcc結(jié)構(gòu)晶粒通過晶界連結(jié),最終演變成鋸齒狀的界面結(jié)合形態(tài),如圖7b所示。正是這樣的界面特征,可保證擴(kuò)散連接接頭的結(jié)合質(zhì)量。為了定量地分析晶粒尺寸的變化,繪制出擴(kuò)散影響區(qū)EBSD像,如圖7c所示,利用Image-Pro Plus 軟件計算得到奧氏體平均晶粒尺寸為2.06 μm,鐵素體平均晶粒尺寸為5.48 μm。圖7a方框處擴(kuò)散連接界面位錯密度圖如圖7d和e所示(利用MTEX軟件計算單位時間內(nèi)的位錯密度所得)。可見,高Cr鐵素體耐熱鋼一側(cè)的位錯密度顯著高于TP347H奧氏體耐熱鋼一側(cè),擴(kuò)散連接影響區(qū)的位錯密度高于試樣基體。
圖7

圖7 焊后熱處理之前擴(kuò)散連接試樣擴(kuò)散連接區(qū)的EBSD分析
(a) EBSD image of joint area
(b) grain diagram of diffusion-bonding zone in rectangle area in Fig.7a
(c) phase diagram of diffusion-bonding zone in rectangle area in Fig.7a
(d) dislocation density diagram of diffusion-bonding zone of TP347H austenitic heat-resistant steel in rectangle area in Fig.7a
(e) dislocation density diagram of diffusion-bonding zone of high Cr ferrite heat-resistant steel in rectangle area in Fig.7a
Fig.7 EBSD analyses of the diffusion-bonding joint area before PWHT
圖8a顯示了擴(kuò)散連接時間為120 min時擴(kuò)散連接試樣擴(kuò)散連接區(qū)經(jīng)焊后熱處理的EBSD像。可見,焊后熱處理之后試樣擴(kuò)散連接區(qū)的相分布與圖7a相一致,不同的是,經(jīng)過熱處理后高Cr鐵素體耐熱鋼一側(cè)晶粒取向更趨向一致化,TP347H奧氏體晶粒更加細(xì)小。圖8c所示為焊后熱處理后擴(kuò)散連接區(qū)的EBSD像,計算得到奧氏體平均晶粒尺寸減小至1.73 μm,鐵素體平均晶粒尺寸減少至2.53 μm。可見,經(jīng)焊后熱處理之后試樣擴(kuò)散連接界面處晶粒得到細(xì)化。原因在于鋼中形成了難溶于奧氏體的碳化物,分布在晶粒邊界上,呈現(xiàn)彌散分布,阻止奧氏體晶粒的長大,對位錯有一定的釘扎作用,從而細(xì)化晶粒。圖8d和e顯示了圖8a方框處擴(kuò)散連接界面位錯密度圖。可以發(fā)現(xiàn),擴(kuò)散連接影響區(qū)位錯相對穩(wěn)定化,位錯密度減少。
圖8
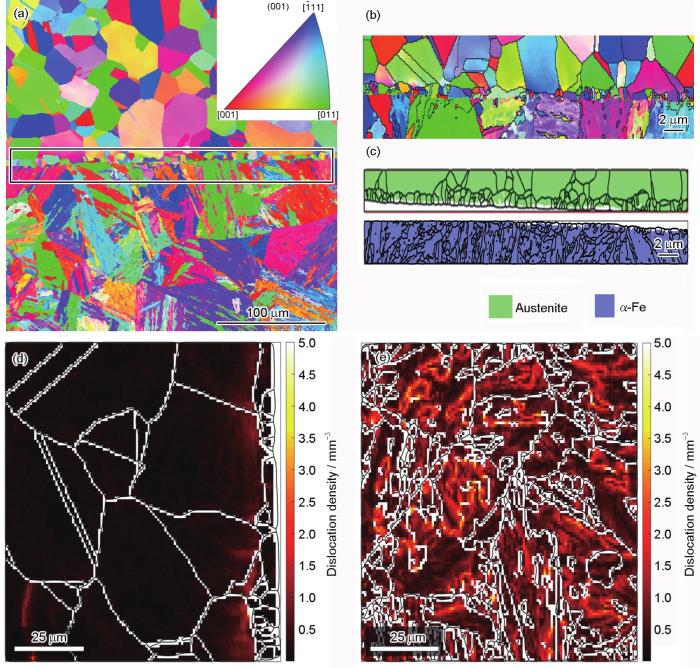
圖8 焊后熱處理之后擴(kuò)散連接試樣擴(kuò)散連接區(qū)的EBSD分析
(a) EBSD image of joint area
(b) grain diagram of diffusion-bonding zone in rectangle area in Fig.8a
(c) phase diagram of diffusion-bonding zone in rectangle area in Fig.8a
(d) dislocation density diagram of diffusion-bonding zone of TP347H austenitic heat-resistant steel in rectangle area in Fig.8a
(e) dislocation density diagram of diffusion-bonding zone of high Cr ferrite heat-resistant steel in rectangle area in Fig.8a
Fig.8 EBSD analyses of the diffusion-bonding joint area after PWHT
圖9a顯示了擴(kuò)散連接時間為120 min時未經(jīng)焊后熱處理的擴(kuò)散連接試樣擴(kuò)散連接區(qū)的TEM像。虛線顯示為擴(kuò)散連接界面。通過選區(qū)電子衍射(SAED)花樣可知,虛線左側(cè)為晶帶軸方向為[
圖9
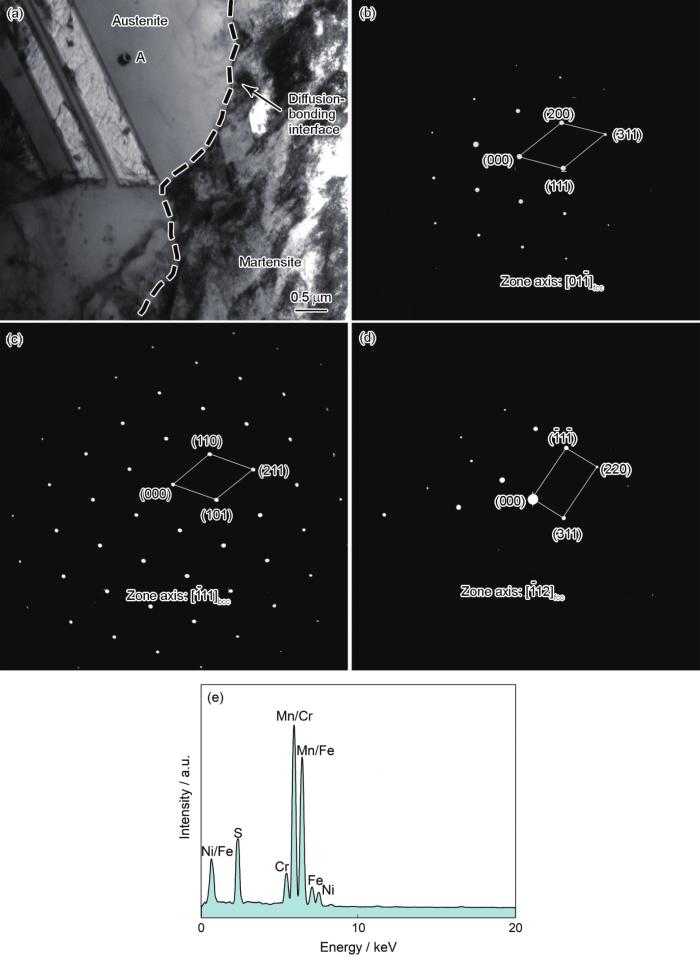
圖9 焊后熱處理之前擴(kuò)散連接試樣擴(kuò)散連接區(qū)的TEM分析
(a) TEM image of the joint (b, c) SAED patterns of the joint for left and right sides of diffusion-bonding interface showed by dash line in Fig.9a, respectively (d) SAED pattern of the precipitate A in Fig.9a (e) EDS of the precipitate A in Fig.9a
Fig.9 TEM analyses of the diffusion-bonding joints before PWHT
圖10a顯示了擴(kuò)散連接時間為120 min時擴(kuò)散連接試樣擴(kuò)散連接區(qū)經(jīng)焊后熱處理的TEM像。與圖9a比較發(fā)現(xiàn),無論熱處理與否,高Cr鐵素體耐熱鋼一側(cè)母材的顯微組織均為板條馬氏體,TP347H奧氏體耐熱鋼一側(cè)母材的顯微組織為奧氏體晶粒。所不同的是,經(jīng)熱處理后得到的板條馬氏體更為細(xì)小,且奧氏體晶界較為清晰。擴(kuò)散連接界面處與晶粒內(nèi)部彌散著大量不同尺寸的碳化物顆粒。經(jīng)SAED花樣標(biāo)定(圖10d)與EDS分析(圖10e)確定為M23C6相,這是因為Cr與Fe發(fā)生置換后,由于Fe與C的結(jié)合力低于Cr與C的結(jié)合力,Cr原子在擴(kuò)散連接界面附近發(fā)生偏聚,如圖11所示,形成富Cr的M23C6相,對擴(kuò)散連接試樣接頭起到彌散強化及位錯強化效果[27~29]。TP347H奧氏體耐熱鋼一側(cè)靠近擴(kuò)散連接界面處晶粒變得細(xì)小,但由于組織遺傳性,仍有少量較為粗大的晶粒存在。
圖10
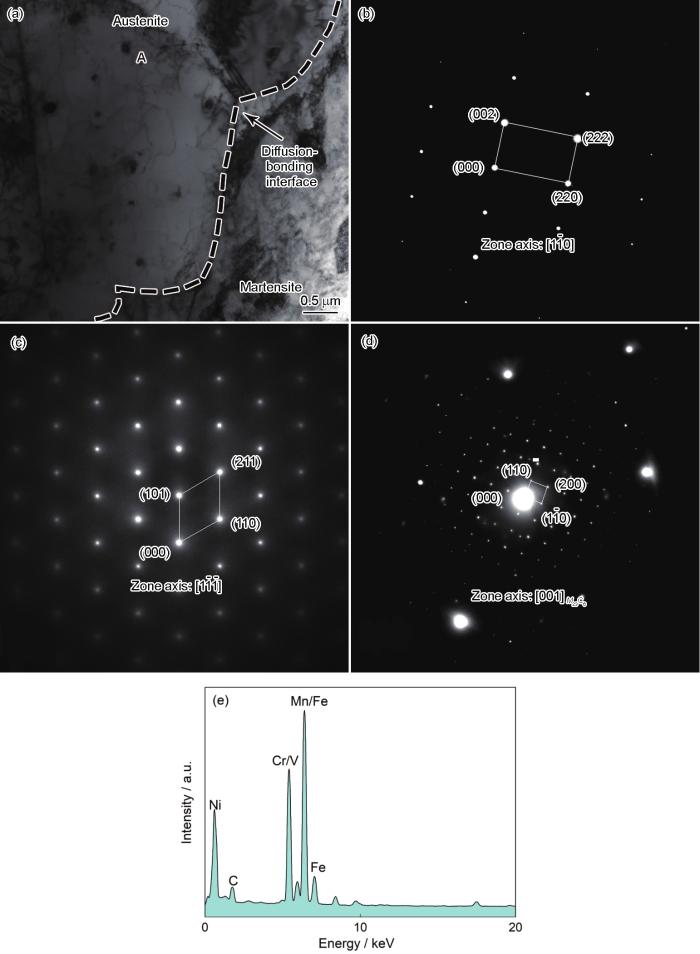
圖10 焊后熱處理之后擴(kuò)散連接試樣擴(kuò)散連接區(qū)的TEM分析
(a) TEM image of the joint (b, c) SAED patterns of the joint for left and right sides of diffusion-bonding interface showed by dash line in Fig.10a, respectively (d) SAED pattern of the precipitate A in Fig.10a (e) EDS of the precipitate A in Fig.10a
Fig.10 TEM analyses of the diffusion-bonding joints after PWHT
圖11
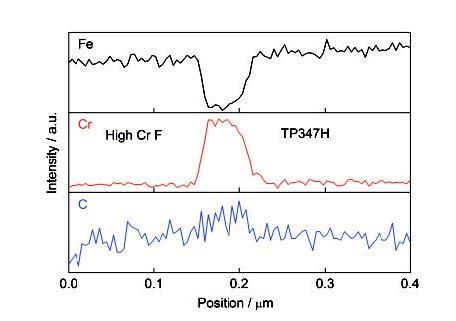
圖11 焊后熱處理之后的擴(kuò)散連接試樣擴(kuò)散連接區(qū)EDS線掃描結(jié)果
Fig.11 EDS line scanning results of the diffusion-bonding joint after PWHT
2.4 擴(kuò)散連接接頭的力學(xué)性能分析
高Cr鐵素體耐熱鋼與TP347H奧氏體耐熱鋼擴(kuò)散連接時間為120 min時擴(kuò)散連接試樣焊后熱處理前后不同溫度拉伸實驗結(jié)果如表2所示,圖12為拉伸試樣斷裂后實物圖。可見,25℃下,不管熱處理與否,試樣拉伸斷裂位置均處于TP347H奧氏體耐熱鋼側(cè)母材。600℃下,焊后熱處理前試樣拉伸斷裂位置處于TP347H奧氏體耐熱鋼側(cè)母材,焊后熱處理后試樣拉伸斷裂位置處于高Cr鐵素體耐熱鋼側(cè)母材。
表2 焊后熱處理前后擴(kuò)散連接試樣接頭的拉伸實驗結(jié)果
Table 2
Specification | Temperature / oC | Average tensile strength / MPa | Rp0.2 / MPa | Elongation / % | Shrinkage / % |
---|---|---|---|---|---|
Before PWHT | 25 | 601.68 | 263.56 | 33.05 | 50.66 |
600 | 322.45 | 153.79 | 21.79 | 47.62 | |
After PWHT | 25 | 558.82 | 249.37 | 24.74 | 31.69 |
600 | 290.45 | 153.38 | 12.26 | 29.34 |
圖12
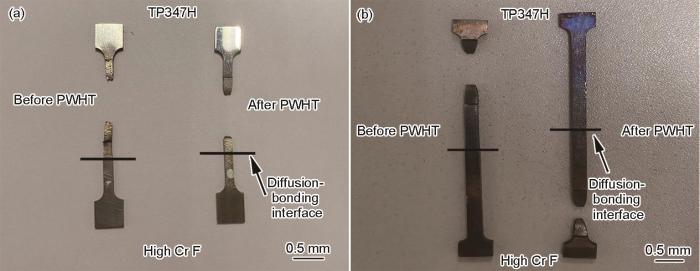
圖12 拉伸斷裂試樣實物圖
(a) 25oC (b) 600oC
Fig.12 Physical drawing of tensile fracture specimen
不同實驗溫度下拉伸斷裂位置均處于母材中,表明實現(xiàn)了異種材料擴(kuò)散連接接頭的可靠連接。通過前文擴(kuò)散影響區(qū)組織分析可知,擴(kuò)散連接接頭強化的原因有3點:(1) 塑形變形的進(jìn)行使得不同晶粒之間變形儲存能存在差異,原本平直的晶界會產(chǎn)生鋸齒狀突起,擴(kuò)散連接界面兩側(cè)相鄰2個不同組織晶粒的晶界有相互連結(jié)的現(xiàn)象,形成了鋸齒狀的界面結(jié)合形態(tài),如圖7b所示;(2) 在晶粒內(nèi)位錯滑移的協(xié)助作用下擴(kuò)散連接界面附近發(fā)生動態(tài)再結(jié)晶,動態(tài)再結(jié)晶晶粒在鐵素體晶界處形核、長大,呈現(xiàn)串聯(lián)狀等軸晶粒分布在擴(kuò)散連接界面上,擴(kuò)散連接界面上的晶粒得以細(xì)化;(3) 試樣內(nèi)Nb、Cr等元素充分?jǐn)U散,與C原子結(jié)合在晶界與晶粒內(nèi)部析出MX、M23C6相,抑制晶粒長大,導(dǎo)致晶粒細(xì)化,可對擴(kuò)散連接界面起到細(xì)晶強化和彌散強化的效果,如圖9和10所示。
由表2可知,隨著實驗溫度的上升,試樣抗拉強度下降,這是因為隨著溫度的升高,鋼內(nèi)的原子內(nèi)能增加,促進(jìn)原子運動,降低原子之間的結(jié)合力。試樣斷后伸長率與面積收縮率隨溫度的升高而降低,面積收縮率均大于斷后伸長率。頸縮率越大,其抗頸縮能力越大,這是造成高Cr鐵素體耐熱鋼與TP347H奧氏體耐熱鋼異種鋼擴(kuò)散連接接頭高溫拉伸斷裂方式轉(zhuǎn)變的主要原因。擴(kuò)散連接試樣拉伸應(yīng)力-應(yīng)變曲線如圖13所示。可以看出,測試溫度為600℃時拉伸應(yīng)變降低,這是由于在較高的實驗溫度下,晶界弱化,試樣內(nèi)部析出的二次相阻礙位錯運動,試樣內(nèi)部微孔萌生,優(yōu)先斷裂。圖14和15顯示了高Cr鐵素體耐熱鋼和TP347H奧氏體耐熱鋼擴(kuò)散連接時間為120 min時試樣接頭焊后熱處理前后不同實驗溫度下拉伸斷口形貌。可見,斷口處存在大量的韌窩,屬于典型的韌性斷裂,斷口邊緣處出現(xiàn)頸縮現(xiàn)象,可進(jìn)一步確認(rèn),接頭的斷裂方式為微孔聚集形斷裂,即焊接接頭在拉伸實驗中經(jīng)歷了“微孔形核-微孔聚集-微孔長大”3個斷裂階段。
圖13
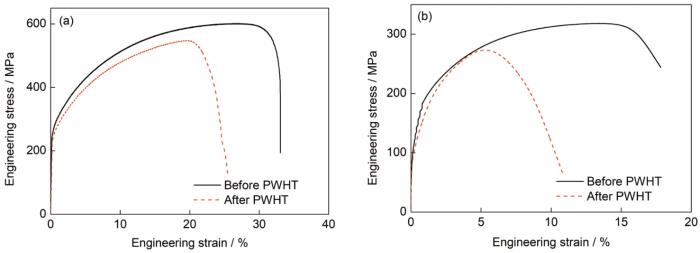
圖13 不同測試溫度下焊后熱處理前后擴(kuò)散連接試樣的工程應(yīng)力-應(yīng)變曲線
Fig.13 Engineering stress-strain curves of the diffusion-bonding joints before and after PWHT under testing temperatures of 25oC (a) and 600oC (b)
圖14
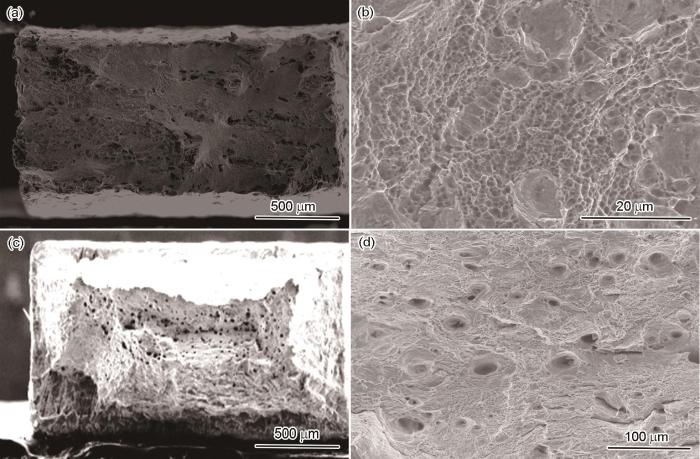
圖14 焊后熱處理前后擴(kuò)散連接試樣接頭在25℃拉伸的斷口形貌
Fig.14 Low (a, c) and high (b, d) magnified tensile fracture morphologies of the diffusion-bonding joints at 25oC before (a, b) and after (c, d) PWHT
圖15
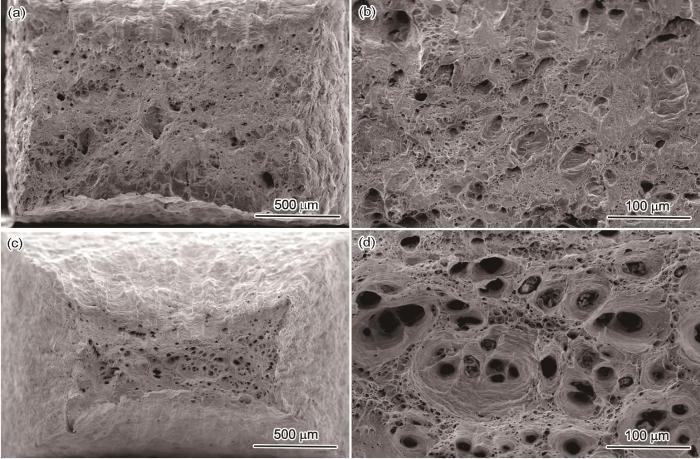
圖15 焊后熱處理前后擴(kuò)散連接試樣接頭在600℃拉伸的斷口形貌
Fig.15 Low (a, c) and high (b, d) magnified tensile fracture morphologies of the diffusion-bonding joints at 600°C before (a, b) and after (c, d) PWHT
3 結(jié)論
(1) 高Cr鐵素體耐熱鋼與TP347H奧氏體耐熱鋼異種鋼擴(kuò)散連接界面處晶粒的取向發(fā)生變化,可以觀察到細(xì)小的呈串聯(lián)狀分布的等軸晶粒,說明擴(kuò)散連接過程中擴(kuò)散影響區(qū)發(fā)生動態(tài)再結(jié)晶。這些晶粒在鐵素體晶界處形核、長大,擴(kuò)散連接界面兩側(cè)相鄰2個不同組織晶粒的晶界有相互連結(jié)的現(xiàn)象,即界面兩側(cè)的fcc結(jié)構(gòu)晶粒與bcc結(jié)構(gòu)晶粒通過晶界連結(jié),最終演變成鋸齒狀的界面結(jié)合形態(tài)。
(2) 將在1050℃、15 MPa、120 min條件下獲得的擴(kuò)散連接試樣進(jìn)行1050℃正火30 min,750℃回火90 min的焊后熱處理,擴(kuò)散影響區(qū)奧氏體平均晶粒尺寸由2.06 μm減小至1.73 μm,鐵素體平均晶粒尺寸由5.48 μm減少至2.53 μm,位錯相對穩(wěn)定化,位錯密度減少,小角度晶界增多,元素擴(kuò)散更加充分。
(3) 由于元素的擴(kuò)散與結(jié)合,在晶界與晶粒內(nèi)部析出MX、M23C6相,但沒有發(fā)現(xiàn)金屬間化合物,析出相進(jìn)一步抑制晶粒長大,從而導(dǎo)致晶粒細(xì)化,可對擴(kuò)散連接界面起到細(xì)晶強化和彌散強化的效果。
(4) 不同實驗溫度下拉伸斷裂位置均處于母材中,說明實現(xiàn)了異種材料擴(kuò)散連接接頭的可靠連接。
來源--金屬學(xué)報