分享:預(yù)拉伸變形對欠時效7N01鋁合金板材疲勞斷裂的影響
田妮,1,2, 石旭1, 劉威1, 劉春城3, 趙剛1,2, 左良2,4
1.
2.
3.
4.
針對工業(yè)化生產(chǎn)的7N01鋁合金板材,采用拉伸實驗、疲勞實驗和微觀組織結(jié)構(gòu)表征等手段研究了預(yù)拉伸變形對欠時效態(tài)7N01鋁合金板材疲勞性能和疲勞斷裂特征的影響。結(jié)果表明,預(yù)拉伸變形量增大至20%,欠時效態(tài)7N01鋁合金板材中合金相粒子的形狀、尺寸、數(shù)量、分布以及薄帶狀晶粒的尺寸和形狀基本保持不變。然而,板材表現(xiàn)出明顯的加工硬化效應(yīng),其屈服強(qiáng)度、抗拉強(qiáng)度和顯微硬度分別由181 MPa、233 MPa和95 HV增大至254 MPa、271 MPa和117 HV,延伸率從23.2%降低至5.2%。在應(yīng)力175 MPa、應(yīng)力比R = 0的疲勞循環(huán)加載條件下,隨預(yù)拉伸變形量的增加,欠時效態(tài)7N01鋁合金板材的疲勞壽命呈現(xiàn)出先縮短再延長又縮短的趨勢。未預(yù)拉伸變形試樣的疲勞壽命為6.06 × 105 cyc,5%預(yù)拉伸變形可將鋁板的疲勞壽命延長75%,達(dá)到了1.06 × 106 cyc,而3%和20%的預(yù)拉伸變形將鋁板的疲勞壽命分別縮短至4.21 × 105和2.89 × 105 cyc。5%~16%預(yù)拉伸變形使欠時效態(tài)7N01鋁合金板材基體中形成均勻分布的高密度位錯或位錯胞的顯微組織,可將合金板材的疲勞壽命延長23%以上。
關(guān)鍵詞:
中強(qiáng)可焊7N01鋁合金不但具有較高的強(qiáng)度、塑性和韌性,同時具有良好的焊接性和熱加工性,其作為關(guān)鍵承力結(jié)構(gòu)材料被廣泛應(yīng)用于軌道車輛和航天飛行器等領(lǐng)域[1~3]。材料在生產(chǎn)和裝配過程中通常會產(chǎn)生一定程度的預(yù)變形,預(yù)變形會影響材料服役過程中的循環(huán)塑形行為,從而影響材料的耐久性[4~6]。然而,目前有關(guān)預(yù)變形對金屬材料疲勞性能的影響結(jié)論不盡相同。針對鋼鐵材料,Gustavsson和Melander[7]認(rèn)為高預(yù)變形(15%以上)有利于提高鐵素體-馬氏體雙相鋼的疲勞強(qiáng)度,但Uemura[8]認(rèn)為預(yù)變形對低碳鋼的低周疲勞壽命不利而對其中高周疲勞壽命無明顯影響。對于鋁合金而言,較多研究結(jié)果表明預(yù)拉伸變形會惡化其疲勞性能。Al-Rubaie等[9]發(fā)現(xiàn),1%~7%的預(yù)拉伸變形在7050-T7451鋁合金中形成的滑移晶粒和駐留滑移帶(persistent slip band,PSB)對合金的疲勞性能不利,合金的疲勞壽命(S-N)曲線隨預(yù)變形量增大而整體下移。Schijve[10]對2024-T3 鋁合金施加3%的拉伸變形,發(fā)現(xiàn)合金的屈服強(qiáng)度由428 MPa提高到480 MPa,但是根據(jù)近似公式
本工作針對欠時效態(tài)7N01鋁合金板材,研究了預(yù)拉伸變形對其高周疲勞性能及疲勞斷裂行為的影響,旨在揭示預(yù)拉伸變形引入的位錯與鋁合金晶界、析出相(precipitate)粒子協(xié)同作用對7N01鋁合金板材疲勞裂紋萌生、疲勞裂紋擴(kuò)展的影響規(guī)律及作用機(jī)制,為最終改善7N01鋁合金疲勞性能提供實驗數(shù)據(jù)和理論依據(jù)。
1 實驗方法
實驗材料為工業(yè)化生產(chǎn)的12.5 mm厚7N01鋁合金熱軋板,其化學(xué)成分(質(zhì)量分?jǐn)?shù),%)為:Zn 4.67,Mg 1.04,Mn 0.28,Cu 0.13,Zr 0.17,Cr 0.17,Fe 0.13,Si 0.03,Ti 0.05,Al余量。沿板材軋制方向按照圖1所示的尺寸切取拉伸和疲勞試樣。所有試樣在循環(huán)風(fēng)熱處理爐中進(jìn)行470℃、90 min固溶處理后水淬,室溫停放1 h后在空氣爐中進(jìn)行120℃、1 h人工時效處理(欠時效態(tài))。分別采用Shimadzu AG-X型250 kN電子萬能試驗機(jī)和QBG-100高頻疲勞試驗機(jī)進(jìn)行室溫拉伸和室溫疲勞實驗。預(yù)拉伸變形量分別為3%、5%、8%、12%、16%以及20%,應(yīng)變速率為0.001 s-1。疲勞加載應(yīng)力為175 MPa,應(yīng)力比R = 0,載荷波為正弦波。拉伸和疲勞實驗的平行試樣均為3個。
圖1

圖1 拉伸及疲勞試樣尺寸
Fig.1 Specimen size for tensile and fatigue tests (unit: mm)
采用Wilson MH-500型數(shù)顯Vickers硬度計測定顯微硬度,外加載荷25 g,加載時間10 s,每個試樣均測試10個點,取平均值。采用JSM-6510A型掃描電子顯微鏡(SEM)觀察疲勞斷口表面形貌。采用GX71光學(xué)顯微鏡(OM)和JEM-2100F透射電鏡(TEM)進(jìn)行顯微組織觀察,觀察位置為板材厚度中心層。TEM樣品制備先用砂紙減薄至65~70 μm厚,隨后進(jìn)行電解雙噴減薄,雙噴液是體積比為1∶3的硝酸甲醇溶液,電壓為10~15 mV,電流50~60 mA,溫度控制在-30~-25℃。
2 實驗結(jié)果
2.1 顯微組織
圖2所示為欠時效態(tài)7N01鋁合金板材金相顯微組織三維立體圖和未經(jīng)預(yù)變形、分別經(jīng)3%~20%預(yù)拉伸變形后板材的縱截面顯微組織的OM像。可見,經(jīng)不同程度預(yù)拉伸變形后的鋁板中均存在許多沿軋向呈碎鏈狀分布的微米級深灰色條塊狀過剩結(jié)晶相粒子,以及大量尺寸細(xì)小且彌散分布的淺灰色點狀合金相(constituent)粒子。結(jié)合板材三維立體金相組織照片(圖2a)以及Hodgson等[13]和Adrien等[14]的研究結(jié)果可知,微米級合金相粒子空間形貌為不規(guī)則顆粒狀,其主要是α-Al (FeMn)Si不可溶過剩結(jié)晶相粒子(圖2b箭頭所示);尺寸極其細(xì)小的合金相粒子主要是AlZnMg(Si)彌散相(dispersoid)粒子(圖2d圓形框內(nèi))。經(jīng)不同程度預(yù)拉伸變形后的鋁板中合金相粒子的形狀、尺寸、分布和數(shù)量無明顯差異,說明預(yù)拉伸變形對欠時效態(tài)7N01鋁合金板材中過剩結(jié)晶相粒子和彌散相粒子組態(tài)無明顯影響。圖3所示為欠時效態(tài)7N01鋁合金板材晶粒組織三維立體圖和未經(jīng)預(yù)變形、分別經(jīng)3%~20%預(yù)拉伸變形后鋁板的縱截面晶粒組織。可見,經(jīng)470℃、90 min固溶水淬及120℃、1 h人工時效處理后,鋁板的晶粒仍具有明顯的纖維狀特征,結(jié)合未經(jīng)預(yù)拉伸變形的鋁板晶粒組織三維立體圖可知,鋁板的晶粒組織為長薄帶狀(圖3a),說明鋁板未發(fā)生再結(jié)晶。經(jīng)3%預(yù)拉伸變形后,鋁板薄帶狀晶粒的厚度略有減薄,繼續(xù)增大預(yù)拉伸變形量至20%,鋁板的晶粒未出現(xiàn)繼續(xù)減薄拉長的現(xiàn)象。說明僅當(dāng)預(yù)拉伸變形程度較小時可使欠時效態(tài)7N01鋁合金板材薄帶狀晶粒厚度略微減薄。
圖2

圖2 欠時效態(tài)7N01鋁合金板材及其經(jīng)不同程度預(yù)拉伸變形后顯微組織的OM像(縱截面,未腐蝕)
Fig.2 OM images of under-aged 7N01 aluminum alloy plate and after different pre-tensile deformations (along longitudinal section, non-etched)
(a) three-dimensional diagram, undeformed(b) undeformed (c) 3% (d) 5% (e) 8% (f) 12% (g) 16% (h) 20%
圖3

圖3 欠時效態(tài)7N01鋁合金板材及其經(jīng)不同程度預(yù)拉伸變形后的晶粒OM像(縱截面)
Fig.3 OM images of grains of under-aged 7N01 aluminum alloy plate and after different pre-tensile deformations (along longitudinal section) that were observed by polarized light microscope
(a) three-dimensional diagram, undeformed
(b) undeformed (c) 3% (d) 5% (e) 8% (f) 12% (g) 16% (h) 20%
圖4為欠時效態(tài)7N01鋁合金板材經(jīng)不同程度預(yù)拉伸變形后顯微組織的TEM像。可見,鋁板中存在許多尺寸約100 nm的彌散相粒子,晶界及晶內(nèi)均未觀察到明顯的析出相粒子。未經(jīng)預(yù)拉伸變形時Al基體中位錯很少(圖4a),隨預(yù)拉伸變形量增大,Al基體中位錯密度逐漸增大。值得注意的是,經(jīng)3%預(yù)拉伸變形后Al基體中位錯分布非常不均勻,位錯或阻滯于彌散相粒子前沿,或阻滯于晶界前沿,形成排列成墻的位錯塞積群(圖4b箭頭所示),而在晶內(nèi)其他區(qū)域幾乎沒有觀察到位錯。Branco等[4]在經(jīng)過一定程度預(yù)拉伸變形后的7050鋁合金中也觀察到了這種位錯分布不均勻的現(xiàn)象,位錯主要出現(xiàn)在滑移帶上,導(dǎo)致滑移線密度增大。經(jīng)受5%、8%以及12%預(yù)拉伸變形后的鋁板晶內(nèi)位錯密度逐漸增大,位錯整體呈均勻的網(wǎng)狀分布,并出現(xiàn)位錯纏結(jié),形成了位錯胞(圖4c~e)。當(dāng)預(yù)拉伸變形量達(dá)到16%時,鋁板中位錯密度進(jìn)一步增大,并形成了尺寸約200 nm的胞狀亞結(jié)構(gòu)(圖4f)。預(yù)拉伸變形進(jìn)一步增加至20%,鋁板晶內(nèi)位錯密度極高,位錯胞狀亞結(jié)構(gòu)尺寸細(xì)化(圖4g)。
圖4

圖4 欠時效態(tài)7N01鋁合金板材經(jīng)不同程度預(yù)拉伸變形后組織的TEM像
Fig.4 TEM images of under-aged 7N01 aluminum alloy plate and after different pre-tensile deformations
(a) undeformed (b) 3% (c) 5% (d) 8% (e) 12% (f) 16% (g) 20%
2.2 力學(xué)性能
圖5是欠時效態(tài)7N01鋁合金板材的力學(xué)性能隨預(yù)拉伸變形量的變化曲線。可見,隨預(yù)拉伸變形程度增加,鋁板的顯微硬度、抗拉強(qiáng)度和屈服強(qiáng)度均呈單調(diào)遞增的趨勢,而延伸率隨預(yù)拉伸變形量增加而逐漸降低。說明室溫拉伸變形時,欠時效態(tài)7N01鋁合金板材表現(xiàn)出明顯的加工硬化效應(yīng)。未預(yù)拉伸變形時,鋁板的顯微硬度、屈服強(qiáng)度、抗拉強(qiáng)度和延伸率分別為95 HV、181 MPa、233 MPa和23.2%;當(dāng)預(yù)拉伸變形量增大至8%時,鋁板的屈服強(qiáng)度和抗拉強(qiáng)度迅速增大至237和263 MPa,板材的延伸率降低至15.2%。繼續(xù)增加預(yù)拉伸變形量時,鋁板的屈服強(qiáng)度和抗拉強(qiáng)度增速變緩。當(dāng)預(yù)拉伸變形量增大至20%時,鋁板的抗拉強(qiáng)度和屈服強(qiáng)度分別為271和254 MPa,延伸率顯著降低至5.2%。當(dāng)預(yù)拉伸變形量小于8%或大于12%,鋁板的顯微硬度增速較緩慢,但是,當(dāng)預(yù)拉伸變形量從8%增大至12%時,鋁板的顯微硬度迅速增大,從104 HV增大至113 HV。
圖5

圖5 欠時效態(tài)7N01鋁合金板材經(jīng)不同程度預(yù)拉伸變形量后的力學(xué)性能
Fig.5 Mechanical properties of under-aged 7N01 aluminum alloy plate after different pre-tensile deformations
(a) microhardness
(b) yield strength, tensile strength, and elongation
2.3 疲勞壽命
圖6是欠時效態(tài)7N01鋁合金板材經(jīng)不同程度預(yù)拉伸變形后,在最大應(yīng)力為175 MPa (低于未預(yù)拉伸變形的欠時效態(tài)鋁板屈服強(qiáng)度181 MPa)、R = 0條件下的疲勞壽命。可見,隨預(yù)拉伸變形程度增大,鋁板的疲勞壽命呈現(xiàn)出先縮短后延長再縮短的趨勢。未經(jīng)預(yù)拉伸變形時鋁板的平均疲勞壽命約6.06 × 105 cyc,經(jīng)3%預(yù)拉伸變形后鋁板的平均疲勞壽命縮短至4.21 × 105 cyc;承受5%預(yù)拉伸變形的鋁板平均疲勞壽命最長,達(dá)到1.06 × 106 cyc,是未預(yù)拉伸變形鋁板的疲勞壽命的1.75倍;繼續(xù)增大預(yù)拉伸變形量,鋁板的平均疲勞壽命逐漸縮短,當(dāng)預(yù)拉伸變形量達(dá)到20%時,鋁板的平均疲勞壽命最短,僅為2.89 × 105 cyc。值得注意的是,承受5%~16%預(yù)拉伸變形板材的平均疲勞壽命比未預(yù)拉伸變形板材的疲勞壽命延長了23%以上,說明適當(dāng)程度的預(yù)拉伸變形有利于延長欠時效態(tài)7N01鋁合金板材的疲勞壽命,這與目前大部分學(xué)者[4,9,10]得出的預(yù)拉伸變形對鋁合金疲勞性能不利的研究結(jié)果并不一致。
圖6

圖6 欠時效態(tài)7N01鋁合金板材經(jīng)不同程度預(yù)拉伸變形后的疲勞壽命
Fig.6 Fatigue life of under-aged 7N01 aluminum alloy plate after different pre-tensile deformations
2.4 疲勞斷口形貌
圖7是欠時效態(tài)7N01鋁合金板材經(jīng)不同程度預(yù)拉伸變形后,在應(yīng)力級別為175 MPa、R = 0條件下疲勞斷口表面疲勞源處的SEM像。可見,經(jīng)不同程度預(yù)拉伸變形后,鋁板的疲勞裂紋均萌生于試樣表面或近表面粗大過剩結(jié)晶相粒子處,說明預(yù)拉伸變形程度對疲勞裂紋萌生位置無明顯影響。斷口表面疲勞裂紋源處均可觀察到大尺寸過剩結(jié)晶相粒子或明顯的孔洞,這是由于在循環(huán)載荷作用下,位錯滑移至粗大過剩結(jié)晶相粒子界面前沿塞積形成應(yīng)力集中,導(dǎo)致過剩結(jié)晶相粒子與基體的結(jié)合面分離而形成孔洞。未經(jīng)預(yù)拉伸變形的鋁板裂紋源處的過剩合金相粒子尺寸相對較小,斷口表面較粗糙(圖7a)。經(jīng)5%和8%預(yù)拉伸變形鋁板的疲勞裂紋源區(qū)域過剩結(jié)晶相粒子尺寸相對粗大、斷口表面起伏程度較大,裂紋具有明顯的放射狀特征(圖7c和d)。經(jīng)3%和16%預(yù)拉伸變形后的合金疲勞斷口表面與裂紋源緊鄰的疲勞裂紋擴(kuò)展區(qū)域凹凸不平且存在大量高低不平的結(jié)晶學(xué)平面和撕裂棱,但是經(jīng)3%拉伸變形后試樣的疲勞斷口表面中裂紋源處的結(jié)晶學(xué)平面特征相對于經(jīng)16%拉伸變形后試樣的疲勞斷口表面中裂紋源處的結(jié)晶學(xué)平面特征更顯著(圖7b和e)。經(jīng)20%預(yù)拉伸變形的鋁板疲勞斷口表面裂紋源區(qū)域的形貌較為平滑,可觀察到明顯的疲勞輝紋,輝紋寬度約為0.9 μm (圖7f),并且每隔數(shù)條小輝紋還存在類似臺階狀的寬大輝紋。
圖7
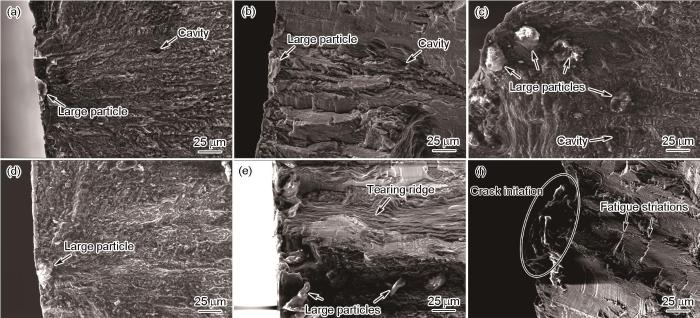
圖7 欠時效態(tài)7N01鋁合金板材經(jīng)不同程度預(yù)拉伸變形后的疲勞斷口表面裂紋源處SEM像
Fig.7 SEM images of fatigue sources of under-aged 7N01 aluminum alloy plate after different pre-tensile deformations
(a) undeformed (b) 3% (c) 5% (d) 8% (e) 16% (f) 20%
圖8是欠時效態(tài)7N01鋁合金板材經(jīng)不同程度預(yù)拉伸變形后,在應(yīng)力175 MPa、R = 0條件下疲勞斷口表面疲勞裂紋擴(kuò)展區(qū)形貌的SEM像。可見,未預(yù)拉伸變形以及分別經(jīng)5%和8%預(yù)拉伸變形的鋁板疲勞斷口擴(kuò)展區(qū)表面形貌較為粗糙,表面主要由極其細(xì)小的波浪狀條紋和撕裂棱構(gòu)成,具有明顯的河流花樣特征,且存在多條長犁溝狀二次裂紋,斷口表面起伏明顯,其中經(jīng)5%和8%預(yù)拉伸變形后試樣疲勞斷口裂紋擴(kuò)展區(qū)中存在大量較長的分布式二次裂紋(圖8c和d),表明疲勞裂紋在擴(kuò)展過程中發(fā)生了多次偏轉(zhuǎn)。經(jīng)受3%預(yù)拉伸變形試樣的疲勞斷口裂紋擴(kuò)展區(qū)表面形貌雖然也具有河流花樣特征,但同時可以清楚地觀察到許多曲折的疲勞輝紋和少量二次裂紋(圖8b)。這種光滑的疲勞斷口形貌不同于承受較小預(yù)拉伸變形量的鋁板,也不同于在7085、7175和7050鋁合金材料中觀察到的疲勞裂紋擴(kuò)展區(qū)粗糙的表面形貌特征[15,16]。經(jīng)16%和20%預(yù)拉伸變形后的鋁板疲勞斷口疲勞裂紋擴(kuò)展區(qū)表面比較光滑,擴(kuò)展路徑中可觀察到大量平直的疲勞輝紋和疲勞臺階,并伴有聚集型孔洞(圖8e和f),疲勞輝紋間互相平行且具有規(guī)則的間距寬度,疲勞輝紋條帶的法線方向幾乎與該區(qū)域的裂紋擴(kuò)展方向一致。這主要是由于7N01鋁合金熱軋板經(jīng)固溶欠時效處理后晶粒仍保持薄帶狀特征,疲勞加載方向與薄帶狀晶粒的長軸方向一致,疲勞應(yīng)力法線方向的晶粒厚度較薄,裂紋易沿著晶內(nèi)塞積的高位錯密度區(qū)快速穿透薄帶狀晶粒,因此裂紋擴(kuò)展路徑相對較平滑。另外,合金斷口表面中均未觀察到冰糖塊狀的沿晶斷裂特征,這同樣是與合金板材的晶粒呈薄帶狀有關(guān)。因為疲勞主應(yīng)力與薄帶狀晶粒長軸一致,裂紋無法沿扁長的晶界擴(kuò)展,只能沿著晶內(nèi)某一個剪切面穿晶擴(kuò)展。
圖8

圖8 欠時效態(tài)7N01鋁合金板材經(jīng)不同程度預(yù)拉伸變形后的疲勞斷口表面裂紋擴(kuò)展區(qū)形貌的SEM像
Fig.8 SEM images of fatigue crack propagation of under-aged 7N01 aluminum alloy plate after different pre-tensile deformations
(a) undeformed (b) 3% (c) 5% (d) 8% (e) 16% (f) 20%
3 討論分析
由于預(yù)拉伸應(yīng)力加載方向與薄帶狀晶粒長度方向一致,在預(yù)拉伸變形量較小(小于3%)時Al基體的變形抗力低,晶粒沿應(yīng)力加載方向略微拉長而使得薄帶狀晶粒厚度略有減薄;當(dāng)預(yù)拉伸變形量較大(超過3%)時,由于位錯強(qiáng)化使基體變形抗力顯著提高,塑性變形過程中主要通過晶粒內(nèi)部的位錯滑移釋放形變能,因此當(dāng)預(yù)拉伸變形量超過3%后,欠時效態(tài)7N01鋁合金板材晶粒未出現(xiàn)繼續(xù)減薄拉長的現(xiàn)象。
欠時效態(tài)7N01鋁合金板材中固溶的Zn、Mg溶質(zhì)原子主要以溶質(zhì)原子團(tuán)簇(即GP區(qū))形式存在于基體中,運動位錯大多以切割方式通過GP區(qū)[17]。鋁板在預(yù)拉伸變形過程中,一方面位錯不斷增殖導(dǎo)致位錯數(shù)量逐漸增多(圖4),同時也伴隨著異號位錯相消或位錯滑移至晶體表面湮滅,結(jié)合硬度、強(qiáng)度和延伸率變化規(guī)律,認(rèn)為當(dāng)預(yù)拉伸變形量不超過8%時,位錯的增殖速率遠(yuǎn)大于位錯的相消或湮滅的速率,鋁板中位錯密度快速增大,加工硬化效果顯著,此時鋁板的強(qiáng)度和顯微硬度增幅較大(圖5)。當(dāng)預(yù)拉伸變形量達(dá)到12%時,鋁板中位錯密度非常高(圖4e),鋁板的變形抗力進(jìn)一步增大,其屈服強(qiáng)度增加至244 MPa,塑性流變應(yīng)力劇增。高流變應(yīng)力下位錯重排、相消和湮滅的幾率逐漸增加,大量螺型位錯交滑移或刃型位錯攀移導(dǎo)致鋁板流變應(yīng)力-應(yīng)變曲線進(jìn)入拋物線硬化階段[18],因此鋁板的強(qiáng)度增速減緩。這與王芝秀等[19]研究預(yù)變形對2E12鋁合金屈服強(qiáng)度的影響結(jié)論一致。
由圖2~4結(jié)果可知,預(yù)拉伸變形對欠時效態(tài)7N01鋁合金板材中第二相粒子及晶粒尺寸形貌無明顯影響,其主要改變的是Al基體中的位錯數(shù)量和分布。在疲勞加載條件相同的情況下,鋁板的疲勞壽命或疲勞性能主要決定于Al基體中位錯數(shù)量和分布。未預(yù)拉伸變形時,Al基體內(nèi)位錯很少,疲勞壽命約為6.06 × 105 cyc。承受了3%預(yù)拉伸變形的鋁板疲勞裂紋萌生區(qū)無明顯放射狀特征(圖7b),鋁板經(jīng)歷較少的循環(huán)后即萌生了疲勞裂紋。因為鋁板承受3%的預(yù)拉伸變形時變形不均勻,位錯主要在大尺寸過剩結(jié)晶相粒子與Al基體的界面處萌生且局部塞積(圖4b),疲勞加載過程中這種貫穿晶粒的位錯墻極易成為疲勞微裂紋的萌生位置,并起到橋接主裂紋的作用,使得疲勞裂紋快速穿過晶粒向下一個晶粒繼續(xù)擴(kuò)展。另外,疲勞裂紋擴(kuò)展路徑上存在較多曲折的疲勞輝紋和少量二次裂紋(圖8b),疲勞輝紋越明顯、間距越寬,則疲勞裂紋擴(kuò)展速率越高[20]。綜上可知,經(jīng)3%預(yù)拉伸變形后的鋁板中不均勻分布的低密度位錯不僅促進(jìn)疲勞裂紋萌生,還有利于疲勞主裂紋的橋接和擴(kuò)展,最終導(dǎo)致欠時效態(tài)7N01鋁合金板材在應(yīng)力級別為175 MPa、R = 0條件下的疲勞壽命大幅度縮短(約為4.21 × 105 cyc,鋁板的疲勞壽命比未預(yù)拉伸變形時的疲勞壽命縮短了約31%)。
當(dāng)預(yù)拉伸變形量達(dá)到5%和8%時,欠時效態(tài)7N01鋁合金板材的屈服強(qiáng)度分別達(dá)到222和237 MPa,抗拉強(qiáng)度分別達(dá)到256 和263 MPa,顯微硬度分別為101和104 HV,表現(xiàn)出顯著的應(yīng)變強(qiáng)化特征。基體中位錯分布較均勻,局部位錯纏結(jié),形成了位錯胞(圖4c和d)。這種位錯組態(tài)使合金板材的疲勞壽命分別延長至1.06 × 106和8.63 × 105 cyc,相對于未預(yù)拉伸變形時的疲勞壽命分別提高了75%和42%。研究[21~24]認(rèn)為,由于金屬材料中的第二相粒子與基體在強(qiáng)度、剛度、塑性等均不匹配,疲勞裂紋經(jīng)常萌生于第二相粒子與基體的界面處,相對于第二相粒子而言,Al基體的強(qiáng)度、硬度和剛度都很低,但塑性很高。5%和8%的預(yù)拉伸變形可使Al基體中出現(xiàn)高密度、均勻分布的位錯,使Al基體強(qiáng)度和硬度提高,這在一定程度上弱化了合金相粒子與基體的不匹配程度,使鋁板疲勞承載協(xié)調(diào)性增強(qiáng)。經(jīng)5%和8%預(yù)拉伸變形鋁板的疲勞斷口裂紋源處表面起伏程度較大,具有明顯的放射狀擴(kuò)散特征,塑性變形痕跡明顯(圖7c和d),說明鋁板疲勞裂紋萌生較困難。而且鋁板疲勞斷口疲勞裂紋擴(kuò)展區(qū)中還存在大量較長的分布式二次裂紋(圖8c和d),表明已經(jīng)具有較強(qiáng)位錯強(qiáng)化效應(yīng)的Al基體使得疲勞裂紋在擴(kuò)展過程中發(fā)生了多次偏轉(zhuǎn)。這些二次裂紋在疲勞裂紋擴(kuò)展過程中會消耗主裂紋的擴(kuò)展能量,有效釋放主裂紋尖端應(yīng)力,使疲勞裂紋擴(kuò)展速率降低[25]。因為先經(jīng)受一定程度預(yù)拉伸變形的鋁板在交變載荷作用下,2個相鄰裂紋面會發(fā)生轉(zhuǎn)動,進(jìn)而影響裂紋走向,當(dāng)相鄰晶粒的有利滑移系存在一定的角度,裂紋在擴(kuò)展過程中則會偏轉(zhuǎn)至相鄰晶粒的有利滑移系繼續(xù)擴(kuò)展,也可能終止于晶界處,這樣即造成了疲勞斷口表面的高低起伏、凹凸不平,這與Jian等[26]觀察到的實驗現(xiàn)象一致。綜上可知,均勻分布的高密度位錯弱化了第二相粒子與基體間的不匹配性,不利于疲勞裂紋的萌生,因而起到了顯著改善欠時效態(tài)7N01鋁合金板材疲勞性能的作用。
當(dāng)鋁板承受的預(yù)拉伸變形程度達(dá)到16%時,基體中位錯密度進(jìn)一步增大,并出現(xiàn)明顯的胞狀亞結(jié)構(gòu)(圖4f),鋁板的屈服強(qiáng)度、抗拉強(qiáng)度和顯微硬度進(jìn)一步增大至250 MPa、269 MPa和116 HV,但是板材的延伸率降低至9.6%。雖然拉伸變形程度已經(jīng)很大,位錯強(qiáng)化效應(yīng)非常顯著,但鋁板的疲勞壽命仍然比未經(jīng)受預(yù)拉伸變形時延長了23%。鋁板疲勞斷口表面裂紋源處具有大量高低不平的結(jié)晶學(xué)平面、撕裂棱等形貌特征(圖7e),說明承受了16%預(yù)拉伸變形的Al基體對疲勞裂紋的萌生具有很強(qiáng)的抑制作用。但疲勞斷口裂紋擴(kuò)展區(qū)表面光滑,可明顯觀察到對應(yīng)于每個周次疲勞循環(huán)加載時疲勞裂紋擴(kuò)展所形成的平直的疲勞輝紋,比承受3%預(yù)拉伸變形的鋁板疲勞斷口疲勞裂紋擴(kuò)展區(qū)的疲勞輝紋更平直且輝紋間距更大(圖8e)。說明當(dāng)欠時效態(tài)7N01鋁合金基體中的位錯密度非常高且開始出現(xiàn)明顯的胞狀亞結(jié)構(gòu)時,這種微觀組織對疲勞裂紋擴(kuò)展的阻礙作用很小。鋁板的疲勞壽命相對于未預(yù)變形時仍延長了23%的原因主要是由于疲勞裂紋萌生非常困難,鋁板需承受很多疲勞循環(huán)周次以后才能萌生疲勞微裂紋,而對于無缺口試樣的疲勞裂紋萌生及早期擴(kuò)展所對應(yīng)的疲勞壽命約占材料整個疲勞壽命的90%[20]。
當(dāng)預(yù)拉伸變形程度達(dá)到20%,鋁板的塑形很差,延伸率僅為5.2%,晶內(nèi)位錯密度極高且遍布整個變形體內(nèi),并形成了大量尺寸極其細(xì)小的胞狀位錯亞結(jié)構(gòu)(圖4g),造成晶界及合金相粒子界面前沿應(yīng)力集中過大,加速了疲勞裂紋萌生,疲勞斷口表面中疲勞裂紋萌生區(qū)所占面積極小(圖7f圓圈所示),說明承受了20%預(yù)拉伸變形的鋁板在承受175 MPa脈沖疲勞加載時極易萌生疲勞裂紋。另外細(xì)小密集的位錯胞壁在空間貫通橋接成為裂紋擴(kuò)展的通道,有利于疲勞裂紋擴(kuò)展,鋁板疲勞斷口表面中疲勞裂紋擴(kuò)展區(qū)的疲勞臺階平直,疲勞裂紋擴(kuò)展區(qū)域塑性變形痕跡較少(圖8f)。因為當(dāng)鋁板承受的預(yù)拉伸變形程度過大時,位錯強(qiáng)化效應(yīng)使得Al基體硬度進(jìn)一步增大但其塑性明顯下降,疲勞裂紋尖端可越過多個晶粒,沿多個擴(kuò)展面同時或交替進(jìn)行,疲勞裂紋由一個擴(kuò)展面轉(zhuǎn)移至另一個擴(kuò)展面,造成疲勞條帶分布在不同高度的平面上,即形成了類似臺階的形貌[27]。經(jīng)受了20%預(yù)拉伸變形的鋁板疲勞失穩(wěn)斷裂前承受的疲勞循環(huán)周次很少,其疲勞壽命僅為2.89 × 105 cyc,說明極高位錯密度以及極細(xì)小的胞狀位錯亞結(jié)構(gòu)不僅有利于鋁板的疲勞裂紋的萌生,也有利于疲勞裂紋的擴(kuò)展,對鋁板的疲勞性能不利。
由于疲勞裂紋瞬斷撕裂區(qū)所對應(yīng)的疲勞循環(huán)加載周次在板材整個疲勞壽命期內(nèi)的占比極小,因此在粗略估算預(yù)拉伸變形程度對欠時效態(tài)7N01鋁合金板材疲勞斷裂行為的影響時可以忽略不計。則預(yù)拉伸變形對欠時效態(tài)7N01鋁合金板材疲勞壽命的貢獻(xiàn)值(λ)可半定量地由預(yù)拉伸變形量對疲勞裂紋萌生阻力的影響值(λi)及其對疲勞裂紋擴(kuò)展阻力的影響值(λp)表述,即:
總結(jié)前述分析可知,承受16%預(yù)拉伸變形后的鋁板中所具有的高密度位錯形成的尺寸約200 nm的胞狀亞結(jié)構(gòu)微觀組織對疲勞裂紋萌生的阻力最大,承受5%和8%預(yù)拉伸變形后的鋁板疲勞裂紋萌生阻力較大,承受3%預(yù)拉伸變形后的鋁板所具有的分布不均勻的低密度位錯組態(tài)對疲勞裂紋萌生阻力較小,而承受20%預(yù)拉伸變形后的鋁板所形成的極高密度、尺寸極其細(xì)小的胞狀亞結(jié)構(gòu)的微觀組織對疲勞裂紋萌生非常有利。承受5%預(yù)拉伸變形后的鋁板中所具有的均勻分布的適當(dāng)密度的位錯組態(tài)對疲勞裂紋擴(kuò)展阻力最大,承受8%預(yù)拉伸變形后的鋁板對疲勞裂紋擴(kuò)展阻力較大,承受3%尤其是承受16%和20%預(yù)拉伸變形后的鋁板位錯組態(tài)對疲勞裂紋擴(kuò)展起到橋接作用,因此鋁板的疲勞裂紋擴(kuò)展阻力極小。將不同程度預(yù)拉伸變形后欠時效態(tài)7N01鋁合金板材λi、λp以及λ進(jìn)行總結(jié),結(jié)果如表1所示(“+”的數(shù)量越多代表貢獻(xiàn)值越大)。
表1 不同程度預(yù)拉伸變形后,欠時效態(tài)7N01鋁合金板材中疲勞裂紋萌生阻力貢獻(xiàn)值(λi)、疲勞裂紋擴(kuò)展阻力貢獻(xiàn)值(λp)及疲勞壽命貢獻(xiàn)值(λ)的分析結(jié)果
Table 1
Term | 0% | 3% | 5% | 8% | 12% | 16% | 20% |
---|---|---|---|---|---|---|---|
λi | + + + | + + | + + + + | + + + + | + + + + | + + + + + | + |
λp | + + | + + | + + + + + | + + + + | + + + | + | + |
λ | + + + + + | + + + + | + + + + + + + + + | + + + + + + + + | + + + + + + + | + + + + + + | + + |
綜合上述討論分析,總結(jié)出預(yù)拉伸變形導(dǎo)致的位錯組態(tài)對欠時效態(tài)7N01鋁合金板材疲勞裂紋擴(kuò)展影響示意圖(圖9)。未預(yù)拉伸變形的鋁板中位錯密度極低,幾乎不會出現(xiàn)位錯在粗大第二相粒子前沿或晶界前沿塞積的現(xiàn)象,疲勞裂紋一般容易在鋁板近表面處的微米級過剩結(jié)晶相粒子界面萌生,由于硬度較低、塑性較好的Al基體對疲勞裂紋擴(kuò)展的阻力較小,因此疲勞裂紋沿著最大剪切應(yīng)力方向擴(kuò)展,但是在主裂紋擴(kuò)展路徑上會常常誘發(fā)出偏折的二次裂紋,在一定程度上釋放了主裂紋的能量(圖9a);對于承受了3%預(yù)拉伸變形的鋁板,由于預(yù)拉伸變形量較小,鋁板變形不均勻,導(dǎo)致Al基體中出現(xiàn)許多貫穿薄帶狀晶粒厚度的位錯墻,這些貫穿薄帶狀晶粒厚度并塞積于晶界前沿的位錯墻不僅促進(jìn)疲勞裂紋的萌生,而且還能促進(jìn)疲勞微裂紋的橋接,從而促進(jìn)了疲勞裂紋擴(kuò)展,疲勞主裂紋擴(kuò)展過程中出現(xiàn)的二次裂紋較少,位錯不均勻分布的Al基體對疲勞裂紋擴(kuò)展的阻力較小(圖9b);當(dāng)鋁板承受的預(yù)拉伸變形量達(dá)到5%時,基體中形成了均勻分布的位錯組態(tài)(圖4c),這種位錯組態(tài)對疲勞裂紋萌生的阻力較大,更重要的是這種均勻分布于Al基體中的位錯不僅對Al基體有一定的強(qiáng)化作用,同時基體還具有良好的塑性,因此在疲勞主裂紋擴(kuò)展路徑上容易出現(xiàn)許多二次裂紋,有效釋放了主裂紋前沿的應(yīng)力集中,促進(jìn)了主裂紋尖端鈍化,促使疲勞主裂紋在擴(kuò)展的過程中發(fā)生多次偏折,這種均勻分布于基體的位錯組態(tài)最有利于鋁板韌性的發(fā)揮,因此疲勞壽命最長(圖9c);當(dāng)鋁板承受了8%、12%和16%的預(yù)拉伸變形時,雖然基體中位錯的凈增殖速率變緩,位錯數(shù)量增加速度變緩,但位錯纏結(jié)、交割的程度逐漸增大,逐漸形成明顯的胞狀位錯亞結(jié)構(gòu),由于應(yīng)變強(qiáng)化使Al基體硬度和強(qiáng)度進(jìn)一步增加但同時塑性持續(xù)降低,基體與大尺寸第二相粒子的物理性質(zhì)的匹配程度增大,因此疲勞裂紋萌生的阻力相應(yīng)增大;然而,高密度纏結(jié)的位錯胞胞壁對疲勞裂紋擴(kuò)展的橋接作用逐漸增強(qiáng),因此這種具有高密度纏結(jié)位錯的Al基體對疲勞裂紋擴(kuò)展的阻礙作用逐漸減弱,疲勞主裂紋擴(kuò)展路徑中出現(xiàn)的二次裂紋逐漸減少(圖9d~f)。承受了16%的預(yù)拉伸變形的鋁板疲勞主裂紋沿著薄帶狀晶粒的某一個解理面擴(kuò)展(圖8e),疲勞壽命逐漸縮短,但仍比未承受預(yù)拉伸變形時長。當(dāng)預(yù)拉伸變形量進(jìn)一步增大至20%時,鋁板中存在極高的位錯密度和大量尺寸極其細(xì)小的胞狀亞結(jié)構(gòu)的位錯組態(tài)對疲勞裂紋萌生和擴(kuò)展都非常有利(圖9g),因此疲勞壽命顯著縮短,遠(yuǎn)短于未承受預(yù)拉伸變形時的疲勞壽命。
圖9

圖9 欠時效態(tài)7N01鋁合金板材經(jīng)不同程度預(yù)拉伸變形后的疲勞裂紋擴(kuò)展示意圖
Fig.9 Schematics of fatigue crack propagation of under-aged 7N01 aluminum alloy plate after different pre-tensile deformations
(a) undeformed (b) 3% (c) 5% (d) 8% (e) 12% (f) 16% (g) 20%
4 結(jié)論
(1) 預(yù)拉伸變形量增大至20%對欠時效態(tài)7N01鋁合金板材中合金相粒子形狀、尺寸、數(shù)量、分布以及薄帶狀晶粒的尺寸、形狀無明顯影響。
(2) 隨預(yù)拉伸變形量的增加,欠時效態(tài)7N01鋁合金板材的屈服強(qiáng)度、抗拉強(qiáng)度和顯微硬度分別由未預(yù)拉伸變形的181 MPa、233 MPa和95 HV增大至預(yù)拉伸變形量20%后的254 MPa、271 MPa和117 HV,延伸率由23.2%顯著降低至5.2%,表現(xiàn)出明顯的加工硬化效應(yīng)。
(3) 隨預(yù)拉伸變形程度增大,欠時效態(tài)7N01鋁合金板材的疲勞壽命呈先縮短再延長又縮短的趨勢。未預(yù)拉伸變形鋁板的疲勞壽命為6.06 × 105 cyc,3%的拉伸變形造成的不均勻位錯組態(tài)導(dǎo)致鋁板的疲勞壽命縮短至4.21 × 105 cyc;5%的拉伸變形時基體內(nèi)形成最優(yōu)的位錯組態(tài),導(dǎo)致鋁板的疲勞壽命顯著延長至1.06 × 106 cyc;繼續(xù)增大拉伸變形量,位錯組態(tài)對疲勞裂紋擴(kuò)展的阻力持續(xù)減小,當(dāng)拉伸變形量達(dá)到20%,高密度位錯對疲勞裂紋萌生和擴(kuò)展均非常有利,導(dǎo)致鋁板的疲勞壽命顯著縮短至2.89 × 105 cyc。
來源-金屬學(xué)報