分享:V-N微合金鋼在線快速感應(yīng)回火工藝中V(C, N)析出強(qiáng)化機(jī)制
李曉林
摘要
利用SEM、TEM以及三維原子探針(3DAP)等分析方法,研究了V-N微合金鋼在線快速感應(yīng)回火過程中,不同保溫時(shí)間對(duì)力學(xué)性能以及析出強(qiáng)化機(jī)理的影響。結(jié)果表明,未經(jīng)回火組織為粒狀貝氏體;經(jīng)過600 ℃回火后,組織為粒狀貝氏體+鐵素體。試樣在600 ℃回火,保溫300 s,硬度和屈服強(qiáng)度出現(xiàn)峰值,分別為330.45 HV和815 MPa,與未回火試樣相比,屈服強(qiáng)度增加了173 MPa。屈服強(qiáng)度的增加主要依靠V或者VN原子團(tuán)簇,團(tuán)簇中V、N原子的分布近似單原子層,類似析出相的GP區(qū),其內(nèi)部總的原子數(shù)量在20~100個(gè)之間,這些細(xì)小的納米團(tuán)簇與位錯(cuò)有較強(qiáng)的相互作用,與V(C, N)析出相相比,V或VN團(tuán)簇具有更佳的強(qiáng)化效果。
關(guān)鍵詞:
低碳貝氏體鋼是近年來發(fā)展起來的新鋼種,其以較高的強(qiáng)度,優(yōu)良的塑、韌性和良好的焊接性等優(yōu)點(diǎn),被廣泛應(yīng)用于管線鋼、大型工程機(jī)械用鋼、海洋船舶用鋼以及壓力容器用鋼板等領(lǐng)域[1]。在成分設(shè)計(jì)上,自20世紀(jì)80年代以后,國際上主要發(fā)展了2類低碳貝氏體鋼:一類是以日本為代表的Fe-Mn-Nb-B系列鋼,這類鋼中加入了少量的Mo和B,在較寬的冷速范圍內(nèi)便可以得到貝氏體組織[2];另一類是以美國和加拿大為代表的Fe-Cu-Nb-B系列的鋼,以HSLA-80鋼為典型鋼種,成分中添加了較高的Cu,在對(duì)韌塑性沒有明顯損害的條件下,依靠Cu的時(shí)效強(qiáng)化作用獲得高強(qiáng)度[3]。國內(nèi)超低碳貝氏體鋼成分體系多數(shù)為Mn-Mo-Nb-B系,并由賀信萊等[4]研究開發(fā)的弛豫-析出-相變(RPC)工藝對(duì)細(xì)化中溫貝氏體組織有顯著的作用,使強(qiáng)度級(jí)別達(dá)到800 MPa,此種鋼已廣泛用于工程機(jī)械、石油管線、采挖設(shè)備等方面,并在鞍鋼、武鋼等大型鋼鐵企業(yè)實(shí)現(xiàn)了產(chǎn)業(yè)化。近年來,V-N微合金化技術(shù)在鐵素體-珠光體鋼中的應(yīng)用已日漸成熟[5],鋼中加V并增N,形成的V(C,N)粒子,可以同時(shí)細(xì)化晶粒和產(chǎn)生析出強(qiáng)化作用,但V-N微合金化技術(shù)在低碳貝氏體鋼方面的應(yīng)用研究較少。
通常,低碳貝氏體鋼經(jīng)過傳統(tǒng)離線調(diào)質(zhì)工藝處理改善鋼板的強(qiáng)韌性。但是,離線調(diào)質(zhì)工藝生產(chǎn)高強(qiáng)鋼能耗高、周期長。隨著熱處理工藝設(shè)備的不斷發(fā)展,尤其是2004年,日本JFE新日鐵超快冷生產(chǎn)線(Super-OLAC)和在線熱處理工藝(heat-treatment on-line process,簡稱HOP)生產(chǎn)線的投產(chǎn),實(shí)現(xiàn)了在線的淬火與回火工藝,該工藝大大提高了生產(chǎn)率和產(chǎn)品的性能[6]。其中,在線回火采用高頻感應(yīng)加熱,由于其加熱速率快,可以準(zhǔn)確地控制加熱速率和加熱溫度,通過改變這些參數(shù)可以實(shí)現(xiàn)對(duì)析出物的大小、形貌和分布等的控制,使其均勻、彌散、細(xì)小地分布于基體中,從而獲得具有優(yōu)良的強(qiáng)韌性組合的材料[7]。近年來,關(guān)于感應(yīng)加熱回火對(duì)材料組織性能的影響研究越來越多。例如:Nagao等[7]和Xing等[8]研究了快速回火過程中滲碳體的析出機(jī)制;武會(huì)賓等[9]研究了加熱速率對(duì)X80管線鋼中馬氏體/奧氏體(M/A)島含量和分布的影響規(guī)律;張杰等[10]和房玉佩等[11]研究了快速回火不同溫度對(duì)Nb-Ti及Nb-V復(fù)合析出機(jī)制的影響。而快速回火過程中V-N復(fù)合添加對(duì)析出強(qiáng)化機(jī)制影響的研究尚未見報(bào)道。
隨著原子探針技術(shù)的發(fā)展,三維原子探針(3DAP)越來越多地應(yīng)用到納米級(jí)析出相的研究中。3DAP可在納米空間觀察原子的分布和析出相中成分的變化,是研究鋼鐵材料中相的析出和元素偏聚的最為精確的方法[12]。析出相形成之前,它會(huì)經(jīng)歷團(tuán)簇的過程,團(tuán)簇對(duì)于析出相的形核起著非常重要的作用[13,14]。有研究[15]表明,這些團(tuán)簇形成了柔軟的彈性網(wǎng)絡(luò)并阻礙位錯(cuò)運(yùn)動(dòng),因此提高了強(qiáng)度并保持了良好韌性,由于團(tuán)簇的尺寸較小,給研究帶來不少困難,三維原子探針(3DAP)可以對(duì)不同元素的原子逐個(gè)進(jìn)行分析,并給出納米空間中不同元素原子的分布圖[16,17,18]。本工作采用C-Mo-Cr-V-N復(fù)合成分體系,研究了快速感應(yīng)回火過程中V(C, N)析出強(qiáng)化機(jī)制。
實(shí)驗(yàn)用鋼采用50 kg的真空冶煉爐冶煉,其主要化學(xué)成分(質(zhì)量分?jǐn)?shù),%)為:C 0.043,Si 0.25,Mn 1.7,Mo+Cr 1.1,V≤0.1,N≤0.020,Fe余量。鋼錠鍛為80 mm×80 mm×80 mm的方坯,在電阻式加熱爐內(nèi)加熱到1150 ℃,保溫2 h。粗軋溫度為1000 ℃,鋼坯經(jīng)再結(jié)晶區(qū)和未再結(jié)晶區(qū)2階段軋制成10 mm厚鋼板。終軋溫度控制在900 ℃。終軋后經(jīng)過層流冷卻設(shè)備,以40 ℃/s的冷速冷卻至450 ℃后,一組試樣空冷到室溫,作為參考試樣;另一組試樣模擬直接淬火+快速加熱回火,快速加熱回火在FP93可編程PID調(diào)節(jié)器控制的高頻感應(yīng)加熱爐中進(jìn)行。以30 ℃/s加熱到600 ℃,分別保溫50、100、300、600和1800 s,然后出爐空冷至室溫,熱軋工藝示意圖如圖1所示。
圖1 熱軋工藝示意圖
Fig.1 Schematic of hot rolling process
金相樣品、掃描電鏡(SEM)樣品經(jīng)磨制、機(jī)械拋光,再用4% (體積分?jǐn)?shù),下同)的硝酸酒精溶液侵蝕,利用Ultra55場發(fā)射SEM進(jìn)行組織形貌觀察。利用JEM-2100透射電鏡(TEM)觀察析出物形貌、尺寸以及分布,利用其配備的能譜儀(EDS)對(duì)析出相進(jìn)行成分分析。薄膜樣品用5% (體積分?jǐn)?shù))高氯酸無水乙醇電解液,在-20 ℃、30 V下電解雙噴減薄至穿孔。在金相磨面上制備C膜萃取復(fù)型。用兩步電解拋光的方法制備3DAP分析用針尖狀樣品[19],為避免脫C層的影響,采用等離子切割方式在試樣的中心部位切出邊長為0.5 mm 的方形細(xì)棒,棒長20 mm,第一步用25% (體積分?jǐn)?shù))高氯酸乙酸拋光,第二步用2%(體積分?jǐn)?shù))高氯酸乙二醇丁醚進(jìn)行顯微拋光,以獲得曲率半徑小于100 nm的針狀樣品。然后用原子探針層析成像(atom probe tomography,APT)進(jìn)行分析。APT方法是在分析逐個(gè)原子種類的基礎(chǔ)上構(gòu)建納米空間中不同元素原子的分布,可以精確測定納米空間中合金的化學(xué)成分。用LEAP 3000HR型三維原子探針對(duì)針尖樣品進(jìn)行APT采集數(shù)據(jù)時(shí),樣品冷卻至-223 ℃,脈沖頻率為2 MHz,脈沖分?jǐn)?shù)為20%。分析成分時(shí)所取層間距為0.1 nm,所得數(shù)據(jù)由專門的Posap軟件分析。分析納米團(tuán)簇的析出一般采用最大間隔包絡(luò)法(maximum separation envelope method,MSEM)[20],這種方法需要設(shè)置2個(gè)基本參數(shù):一個(gè)是納米團(tuán)簇中某溶質(zhì)原子之間的最大距離dmax;另一個(gè)是某溶質(zhì)原子在滿足dmax時(shí)最少的原子數(shù)目Nmin。溶質(zhì)原子若滿足這個(gè)2個(gè)基本參數(shù)所設(shè)定的值,則團(tuán)簇即被確定。利用MSEM分析碳化物時(shí),設(shè)定dmax=1 nm、Nmin=10[21]。
圖2為試樣快速加熱回火至600 ℃、保溫不同時(shí)間時(shí)顯微硬度及屈服強(qiáng)度變化的曲線??梢钥闯?未回火態(tài)的樣品硬度為291.77 HV,回火經(jīng)不同保溫時(shí)間后,硬度呈先上升后下降的趨勢。保溫時(shí)間300 s為分界點(diǎn),之前硬度上升到最大值330.45 HV,比未回火試樣硬度增加了38 HV,隨著保溫時(shí)間的延長,硬度又逐漸下降,當(dāng)保溫時(shí)間為1800 s時(shí),硬度為308.00 HV。材料的屈服強(qiáng)度隨保溫時(shí)間的變化趨勢與硬度基本一致。在保溫300 s時(shí),屈服強(qiáng)度達(dá)到最大值,為815 MPa,比未回火試樣屈服強(qiáng)度提高了173 MPa。
圖2 試樣快速加熱回火至600 ℃保溫時(shí)間對(duì)硬度和屈服強(qiáng)度的影響
Fig.2 Effects of holding time on the hardness and yield strength of the samples with rapid induction tempered at 600 ℃
圖3為試樣經(jīng)快速加熱至600 ℃回火、不同保溫時(shí)間后的SEM像。與未回火組織(圖3a)相比,當(dāng)保溫時(shí)間為50和100 s時(shí)(圖3b和c),2種狀態(tài)試樣的組織差別不大,可以看到粒狀貝氏體的數(shù)量減少,組織也出現(xiàn)了粗化的現(xiàn)象。當(dāng)保溫時(shí)間增加至300 s時(shí),粒狀貝氏體進(jìn)一步粗化,組織中出現(xiàn)了少量的準(zhǔn)多邊形鐵素體;M/A組元的數(shù)量比軋態(tài)減少,但個(gè)體尺寸明顯增大,且大部分分布在晶界上(圖3d)。當(dāng)保溫時(shí)間增加到600 s時(shí),試樣中的粒狀貝氏體數(shù)量明顯減少,多邊形鐵素體數(shù)量相應(yīng)提高,M/A組元的尺寸減小,并呈顆粒狀或者球狀(圖3e)。當(dāng)保溫時(shí)間增加至1800 s時(shí),試樣中出現(xiàn)了數(shù)量較多的準(zhǔn)多邊形鐵素體,且鐵素體的尺寸較大(圖3f)??傮w來說,隨著保溫時(shí)間的延長,由于貝氏體組織是一種亞溫組織,體自由能高,這些細(xì)小的組織有通過粗化而降低界面能的趨勢,具有自發(fā)地向平衡組織演變的傾向,所以試樣在回火過程中組織不斷向平衡態(tài)轉(zhuǎn)變[4]。
圖3 試樣快速加熱至600 ℃回火、不同保溫時(shí)間的SEM像
Fig.3 SEM images of samples rapid induction tempered at 600 ℃ with different holding time (GB—granular bainite, F—ferrite, M/A—martensite/austenite)
圖4給出了不同回火保溫時(shí)間,析出相在基體中的分布情況。當(dāng)回火保溫時(shí)間較短時(shí)(50 s),微合金元素V和C只發(fā)生短程擴(kuò)散,故碳氮化物析出相在基體中沿位錯(cuò)線析出,由于保溫時(shí)間較短,析出相尺寸和體積分?jǐn)?shù)較小(圖4a);隨著保溫時(shí)間的增加,析出物在基體中析出的數(shù)量開始增加,除了沿位錯(cuò)線析出外,基體中彌散分布的細(xì)小析出物顆粒逐漸增加,析出相呈碟片狀或者橢球形,如圖4b和c所示。當(dāng)保溫時(shí)間為1800 s時(shí),基體中析出相尺寸明顯變大,析出相呈長條形,由于保溫時(shí)間的增加,C和V元素的擴(kuò)散比較充分,析出相開始粗化,析出相由與基體的共格或者半共格關(guān)系轉(zhuǎn)變?yōu)榉枪哺?span style="margin: 0px; padding: 0px; box-sizing: border-box; font-size: 10.5px; line-height: 0; position: relative; vertical-align: baseline; top: -0.5em;">[22], 崔陽
1 實(shí)驗(yàn)方法
2 實(shí)驗(yàn)結(jié)果
2.1 力學(xué)性能
2.2 顯微組織
(a) untempered (b) 50 s (c) 100 s (d) 300 s (e) 600 s (f) 1800 s
2.3 析出相TEM分析
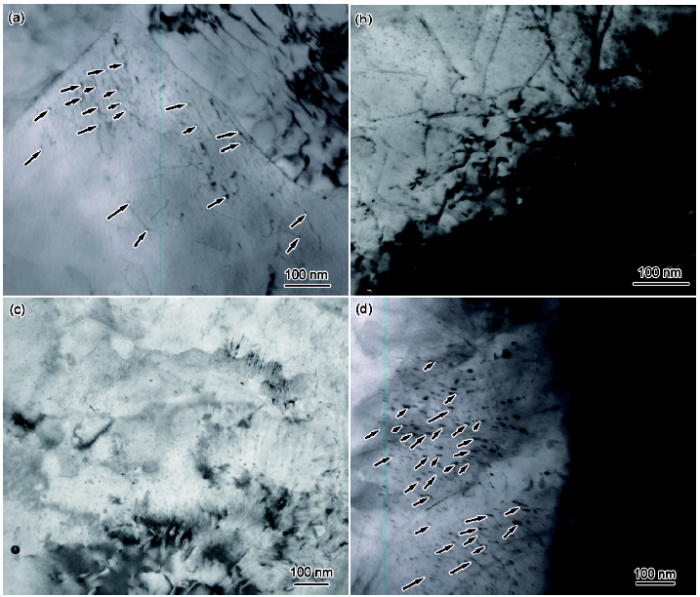
圖4 試樣快速加熱至 600 ℃回火、不同保溫時(shí)間薄膜試樣的TEM像
Fig.4 TEM images of precipitates in V-N microalloyed steel rapid induction tempered at 600 ℃ with different holding time (Arrows show precipitated phases)
(a) 50 s (b) 300 s (c) 600 s (d) 1800 s
通過C復(fù)型的方法制取包含析出相的C膜,采用HRTEM觀察600 ℃快速回火保溫300 s時(shí)試樣中的析出相尺寸,并對(duì)基體中10 nm左右的析出相進(jìn)行EDS分析以及逆Fourier變換,如圖5所示。結(jié)果顯示,析出相中含有V和C元素(Cu為Cu網(wǎng))。對(duì)析出相進(jìn)行二維Fourier變換分析可知,析出相具有NaCl結(jié)構(gòu)。通過反Fourier變換得到析出相的晶格常數(shù)為0.416 nm,在VN (晶格常數(shù)a0=0.4136 nm[23])和VC (a0=0.4182 nm[23])晶格常數(shù)之間,即析出相為具有fcc結(jié)構(gòu)的V(C, N)復(fù)合析出相。
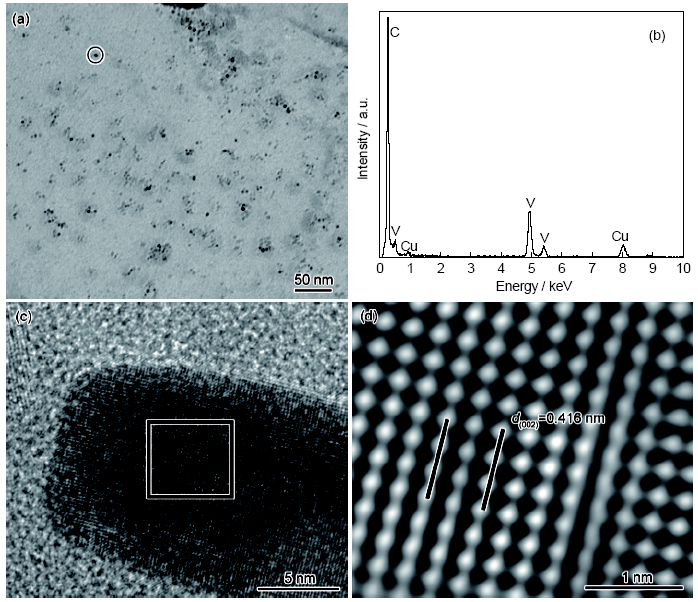
圖5 600 ℃回火保溫300 s時(shí)試樣中析出相復(fù)型HRTEM像、EDS分析、單個(gè)V(C, N)析出粒子和析出相反Fourier變換后的晶格像
Fig.5 Extraction-replica HRTEM image of the fine carbides in tested steel tempered at 600 ℃ for 300 s (a), corresponding EDS analysis of fine carbides (b), the HRTEM image of single V(C, N) precipitate (c) and inverse Fourier transforms lattice image of precipitate (d)
2.4 析出相APT分析
利用APT分析了快速加熱至600 ℃保溫300 s的試樣,結(jié)果如圖6所示。由圖可見,Cr和Mo原子在基體中分布較為均勻,C原子出現(xiàn)了輕微的偏聚現(xiàn)象。V和VN在三維空間的相同位置出現(xiàn)了較為明顯的偏聚,在析出相形成的早期階段,溶質(zhì)原子的偏聚形成的是納米團(tuán)簇,非碳化物。根據(jù)實(shí)驗(yàn)觀察和數(shù)據(jù)分析,溶質(zhì)原子數(shù)小于100時(shí)定義為納米團(tuán)簇,大于100時(shí)定義為析出相。納米團(tuán)簇具有一定的形狀、化學(xué)成分,但沒有一定的晶體結(jié)構(gòu),并不是嚴(yán)格意義上的碳化物。當(dāng)V原子的濃度大于1%時(shí)為納米團(tuán)簇或析出相(基體中V原子的濃度為0.1%),過濾掉基體中固溶的原子,可以清楚地看到納米團(tuán)簇在基體中的分布??梢?納米團(tuán)簇在基體中主要是沿位錯(cuò)線分布(虛線),在變形時(shí),納米團(tuán)簇能夠阻礙位錯(cuò)線的移動(dòng),起到明顯的強(qiáng)化效果。

圖6 試樣快速加熱至600 ℃保溫300 s后C、Cr、Mo和V原子、VN團(tuán)簇和V原子濃度1%時(shí)團(tuán)簇的三維空間分布
Fig.6 3DAP images of tested steels with rapid induction tempered at 600 ℃ for 300 s
(a) C (b) Cr (c) Mo (d) V (e) a VN cluster
(f) the cluster of corresponding 1%V (atomic fraction) iso-concentration surface
圖7為試樣快速加熱至600 ℃分別保溫300和600 s后,C、V、VN在納米團(tuán)簇中的三維空間的分布。由圖可見,同一樣品中存在不同長大階段的納米團(tuán)簇,團(tuán)簇呈碟片狀或近似碟片狀。根據(jù)3DAP測得數(shù)據(jù),計(jì)算了2種保溫時(shí)間下團(tuán)簇的平均等效半徑rp及數(shù)量密度Nv,保溫300和600 s時(shí)的團(tuán)簇rp分別為(1.8±0.87) nm和(2.4±1.2) nm;Nv分別為4.81×1023 m-3和2.05×1023 m-3;同時(shí),測得納米團(tuán)簇中總的V原子數(shù)量,以及所分析區(qū)域內(nèi)基體中總的V原子的數(shù)量,計(jì)算2者的比值分別為44.1%±1.5%和42.9%±2.4%。可見,隨著保溫時(shí)間的增加,納米團(tuán)簇的等效半徑增大,數(shù)量密度減少,沒有更多的V原子在基體中析出,所以試樣快速加熱至600 ℃保溫300 s后,納米團(tuán)簇已經(jīng)完成了其形核到長大過程,并開始進(jìn)入到熟化階段。這也說明在熟化階段,團(tuán)簇或析出相是以大顆粒吞噬小顆粒的方式長大的。
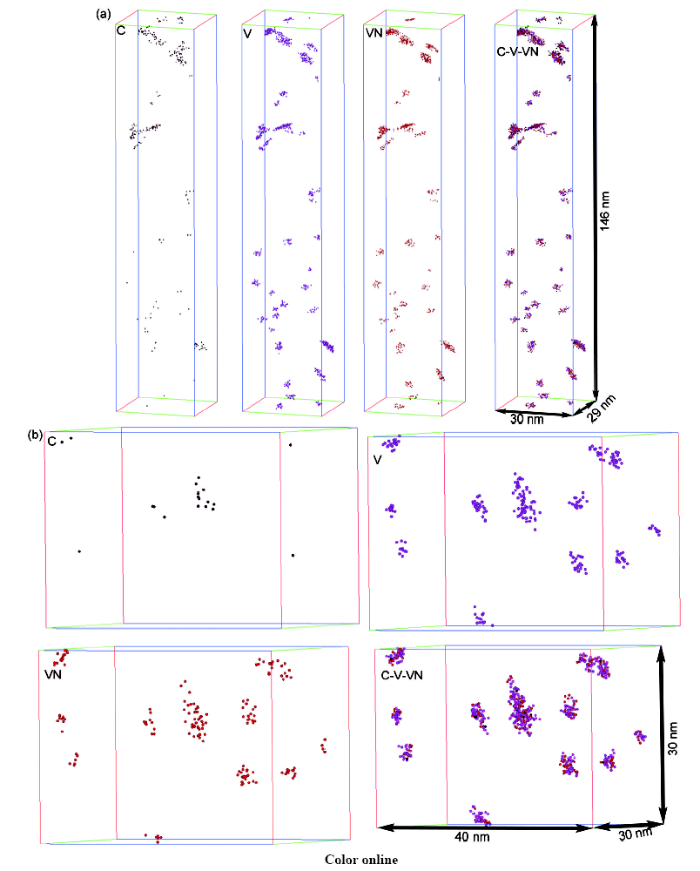
圖7 試樣快速加熱至600 ℃保溫300和600 s時(shí)C、V、VN在團(tuán)簇中的分布
Fig.7 3DAP images of C, V and VN in cluster of samples rapid induction tempered at 600 ℃ for 300 s (a) and 600 s (b)
復(fù)合納米團(tuán)簇或碳氮化物經(jīng)歷形核-長大-粗化過程中,其內(nèi)部的化學(xué)成分會(huì)發(fā)生變化,對(duì)圖7a中的每一個(gè)團(tuán)簇的成分進(jìn)行統(tǒng)計(jì)分析,做出團(tuán)簇大小與成分的關(guān)系,如圖8所示??梢? 600 ℃回火保溫300 s后試樣中團(tuán)簇的尺寸普遍較小,等效半徑多小于2 nm,但也存在尺寸較大的析出相,其等效半徑在4.7~5.0 nm之間。納米團(tuán)簇的主要化學(xué)組分是C-V-N,當(dāng)團(tuán)簇的半徑小于1 nm時(shí),表明團(tuán)簇形核剛剛開始長大,其化學(xué)組分只有V和N;隨著團(tuán)簇或析出相尺寸增加,團(tuán)簇中出現(xiàn)了C和Cr等原子,且團(tuán)簇尺寸越大,各元素的原子含量越趨于平衡,從而形成具有特定晶體結(jié)構(gòu)的穩(wěn)定碳氮化物。這是因?yàn)樵嚇釉诳焖偌訜峄鼗鹎?終軋結(jié)束后快速冷卻至450 ℃,V、C、N元素只在奧氏體中因形變誘導(dǎo)部分析出,所以有較多的V、C、N固溶于基體中;另外,在鐵素體中N原子擴(kuò)散率比C原子高,故在隨后的快速加熱回火過程中,N優(yōu)先與V結(jié)合形成VN復(fù)合團(tuán)簇,而VC與VN同為fcc結(jié)構(gòu),可以無限互溶,VN團(tuán)簇在隨后的長大階段C原子依附于VN形成復(fù)合的V(C, N)析出相,最近有研究者[24]采用模擬的方法得到了這種類似的V(C, N)復(fù)合析出過程。

圖8 試樣快速加熱600 ℃回火保溫300 s時(shí)試樣中團(tuán)簇的溶質(zhì)濃度與團(tuán)簇大小的關(guān)系
Fig.8 Solute concentration of the clusters and particles as a function of the radius in the tested steels rapid induction tempered at 600 ℃ for 300 s
利用APT定量分析了保溫300和600 s后,樣品中不同尺寸的團(tuán)簇中原子數(shù)與團(tuán)簇(分析的團(tuán)簇中原子數(shù)量大于20個(gè))數(shù)量密度及析出的V原子的數(shù)量密度之間的關(guān)系,如圖9所示。由圖9可見,快速加熱至600 ℃保溫300 s時(shí),樣品中原子數(shù)在20~100之間的團(tuán)簇中V原子的數(shù)量明顯高于保溫600 s的樣品。經(jīng)定量計(jì)算,保溫300和600 s后,樣品中小于100個(gè)原子的團(tuán)簇中V原子占總析出的V原子分?jǐn)?shù)分別約為43.93%和20.06%。通過分析納米團(tuán)簇大小(團(tuán)簇中含原子數(shù))與團(tuán)簇?cái)?shù)量密度之間的關(guān)系發(fā)現(xiàn),保溫300 s后,小尺寸的納米團(tuán)簇較多,平均納米團(tuán)簇尺寸中原子數(shù)約為100個(gè),而保溫600 s后,樣品中平均納米團(tuán)簇尺寸中原子數(shù)約為140個(gè)。由此說明,隨著保溫時(shí)間的增加,小尺寸的納米團(tuán)簇減少,大尺寸納米團(tuán)簇增加,而這種增加是以大團(tuán)簇吞噬小團(tuán)簇方式完成的。

圖9 試樣快速加熱600 ℃回火保溫300和600 s時(shí)試樣中團(tuán)簇和析出的V原子數(shù)量與團(tuán)簇大小的關(guān)系
Fig.9 The number of partitioned V atom distribution and the number density of clusters versus cluster size of samples rapid induction tempered at 600 ℃ for 300 and 600 s
3 分析討論
通過實(shí)測數(shù)據(jù)可知,試樣快速加熱至600 ℃保溫300 s后,其屈服強(qiáng)度比回火前增加了173 MPa。屈服強(qiáng)度的增加是基體中析出強(qiáng)化和組織軟化綜合作用的結(jié)果。根據(jù)經(jīng)典的析出強(qiáng)化機(jī)制Ashby-Orowan——位錯(cuò)線繞過機(jī)制,假設(shè)團(tuán)簇為球形,平均半徑約為1.8 nm,選取目前國內(nèi)外比較認(rèn)可的2種計(jì)算模型[25,26]:
式中,σppt 為析出強(qiáng)化增量;f為析出物的體積分?jǐn)?shù);d為實(shí)測析出相的平均直徑。
利用式(1)和(2)計(jì)算了當(dāng)析出強(qiáng)化增量為173 MPa時(shí),所需納米團(tuán)簇的體積分?jǐn)?shù)分別為0.0852%和0.1024%。根據(jù)APT結(jié)果,納米團(tuán)簇主要是V、N原子的聚集而形成,團(tuán)簇的體積分?jǐn)?shù)等于團(tuán)簇中總的V、N原子數(shù)與所分析體積內(nèi)總原子數(shù)的比值[27],由實(shí)驗(yàn)測試數(shù)據(jù)計(jì)算,約為0.0594%??梢?團(tuán)簇的實(shí)際體積分?jǐn)?shù)小于由以上2種模型計(jì)算的理論值,表明V原子的團(tuán)簇對(duì)試樣具有更佳的強(qiáng)化效果。其原因如下:團(tuán)簇中V、N原子的分布近似單原子層,如圖7所示,類似于Al-Cu合金析出相的Guinier-Preston (GP)區(qū)[28]。所謂GP區(qū),即在時(shí)效過程中在過飽和固溶體中脫溶沉淀析出相的最初形態(tài),溶質(zhì)原子偏聚為單原子層,由于與基體完全共格,因此采用傳統(tǒng)的TEM很難觀察到清晰的形貌。關(guān)于GP區(qū)中位錯(cuò)與團(tuán)簇的強(qiáng)化機(jī)制爭論較大,以前的觀點(diǎn)是位錯(cuò)遇到GP區(qū)時(shí)主要是以切過的方式,也即主要強(qiáng)化機(jī)制為切過機(jī)制。最近Singh等[29]采用原子模擬仿真研究了GP區(qū)中團(tuán)簇與位錯(cuò)的相互關(guān)系表明,位錯(cuò)在GP區(qū)的強(qiáng)化方式主要以繞過機(jī)制為主,并非切過機(jī)制占主導(dǎo)。V原子形成的團(tuán)簇或GP區(qū)與具有特定晶體結(jié)構(gòu)的V(C, N)析出相不同,團(tuán)簇為碟片狀,且近似單原子層,具有更大的長寬比。析出相的長寬比越大,其強(qiáng)化效果越好[30]。另外,基體中存在大量細(xì)小的納米團(tuán)簇,其內(nèi)部總的原子數(shù)量在20~100個(gè)之間,這些細(xì)小的納米團(tuán)簇利用TEM無法觀察到,但這些團(tuán)簇與位錯(cuò)有較強(qiáng)的相互作用,對(duì)試樣的強(qiáng)化有較大的貢獻(xiàn)[31,32]。
綜上,試樣快速加熱至600 ℃回火保溫300 s后,基體中存在大量細(xì)小的含V原子的納米團(tuán)簇以及較大尺寸V(C, N)析出相,而納米團(tuán)簇比析出相具有更佳的強(qiáng)化效果。
4 結(jié)論
(1) 采用直接淬火+快速感應(yīng)加熱回火工藝,在600 ℃時(shí)回火,C-Mo-Cr-V-N試樣組織為粒狀貝氏體+準(zhǔn)多邊形鐵素體。當(dāng)保溫時(shí)間為300 s時(shí),試樣的硬度和屈服強(qiáng)度出現(xiàn)極大值,比未回火試樣分別增加了38 HV和173 MPa。
(2) 試樣快速感應(yīng)加熱至600 ℃回火,保溫300 s,基體中存在大量彌散分布的析出相,呈碟片狀或者橢球形,尺寸基本在10 nm以下,經(jīng)過逆Fourier變換得到析出相的晶格常數(shù)為0.416 nm,在VN (a0=0.4136 nm)和VC (a0=0.4182 nm)晶格常數(shù)之間,為具有fcc結(jié)構(gòu)的V(C, N)復(fù)合析出相。
(3) 試樣快速加熱至600 ℃回火保溫300 s,利用3DAP的APT方法分析發(fā)現(xiàn),基體中存在大量細(xì)小的V原子的團(tuán)簇,類似于析出相的GP區(qū),主要沿位錯(cuò)線分布,團(tuán)簇的平均等效半徑為(1.8±0.87) nm、數(shù)量密度為4.81×1023 m-3。V原子的團(tuán)簇強(qiáng)化機(jī)制主要是位錯(cuò)線繞過機(jī)制,其強(qiáng)化效果強(qiáng)于V(C, N)析出相。
來源--金屬學(xué)報(bào)