運(yùn)用實(shí)驗(yàn)和模擬仿真相結(jié)合的方法研究了B4C/6061Al復(fù)合材料的熱壓縮斷裂行為,確定了損傷模型及損傷參數(shù)。建立了單向多尺度有限元模型,分析了B4C/6061Al復(fù)合材料的細(xì)觀損傷機(jī)理。結(jié)果表明,由于B4C/6061Al復(fù)合材料內(nèi)部不均勻的細(xì)觀結(jié)構(gòu),剪切損傷模型不能預(yù)測(cè)其斷裂行為,而GTN損傷模型能準(zhǔn)確預(yù)測(cè)B4C/6061Al復(fù)合材料的熱壓縮斷裂行為。通過與實(shí)驗(yàn)結(jié)果的比較,確定了31%B4C/6061Al (質(zhì)量分?jǐn)?shù))復(fù)合材料的GTN模型損傷參數(shù),從而使模擬和實(shí)驗(yàn)獲得的裂紋深度和載荷-位移曲線高度一致。此外,利用單向多尺度有限元法準(zhǔn)確地分析了B4C/6061Al復(fù)合材料熱壓縮過程的細(xì)觀損傷機(jī)理,即熱壓縮過程中出現(xiàn)的宏觀裂紋是由顆粒的脆性斷裂、基體和界面的脫黏以及基體的延性損傷導(dǎo)致的。
關(guān)鍵詞:
B4C/Al復(fù)合材料除具有高比強(qiáng)度、高比剛度、良好的耐磨性能及低的熱膨脹系數(shù)等金屬基復(fù)合材料的優(yōu)點(diǎn)外[1,2],由于B4C具有良好的中子吸收能力, 是近幾年來備受關(guān)注的一種中子吸收材料,已經(jīng)被成功運(yùn)用在乏燃料水池和燃料運(yùn)輸容器中[3,4]。
B4C/Al復(fù)合材料的制備方法主要有擠壓鑄造、攪拌鑄造、熔體浸滲和粉末冶金等[5,6,7]。為了提高復(fù)合材料的致密度、改善微觀組織均勻性、增加材料的力學(xué)性能并形成最終產(chǎn)品,需要對(duì)復(fù)合材料進(jìn)行塑性變形加工,如軋制、鍛壓或擠壓等。由于大量硬脆陶瓷顆粒的加入嚴(yán)重阻礙了基體的塑性流動(dòng),而且提高了變形抗力,使B4C/Al復(fù)合材料的變形加工非常困難。若加工工藝參數(shù)控制不當(dāng),擠壓和軋制條件下很容易導(dǎo)致型材的邊緣開裂或內(nèi)部損傷[8]。
對(duì)一種材料可加工性的完整描述,需要了解變形過程中加工參數(shù)(如溫度、應(yīng)變速率和應(yīng)變)對(duì)流動(dòng)應(yīng)力的影響、材料的失效行為以及組織演化機(jī)制的轉(zhuǎn)變。已有文獻(xiàn)[9,10,11,12,13]研究了B4C/Al復(fù)合材料熱變形中的流變行為及相應(yīng)的微觀結(jié)構(gòu)變化,分析了溫度和應(yīng)變速率對(duì)流變應(yīng)力的影響[9]。通過對(duì)高應(yīng)變率下的流變應(yīng)力修正,修正后的Arrhenius雙曲正弦本構(gòu)模型可以很好地預(yù)測(cè)B4C/6061Al復(fù)合材料的熱變形行為[11]。賀瑋等[12]采用不同的二次加工方法獲得了抗拉強(qiáng)度高、組織分布均勻的B4C/Al復(fù)合材料。李德富等[13]研究了B4C/2009Al 復(fù)合材料熱加工變形中發(fā)生動(dòng)態(tài)再結(jié)晶的臨界條件。但關(guān)于B4C/Al復(fù)合材料熱變形中材料的斷裂行為還少有研究。Li等[14]和Opelt等[15]分別對(duì)陶瓷和聚合物基復(fù)合材料熱壓縮條件下的斷裂機(jī)理進(jìn)行了研究。不同復(fù)合材料具有不同的細(xì)觀結(jié)構(gòu),但研究結(jié)果表明,在熱壓縮條件下,變形溫度對(duì)基體內(nèi)的微孔洞、微裂紋和界面的演化等有顯著影響,而且宏觀上表現(xiàn)出的斷裂形貌是由其細(xì)觀組織決定的。
B4C/6061Al復(fù)合材料熱變形應(yīng)力、應(yīng)變及損傷存在多尺度和多相性的特點(diǎn),宏觀尺度上(毫米級(jí)別以上)可視為均勻連續(xù)介質(zhì);細(xì)觀尺度上(微米級(jí)別)則區(qū)分為性能差異巨大的合金基體和增強(qiáng)相兩相材料。多尺度有限元法是一種既能在大尺度上求解問題、又能反映小尺度信息的方法,可以顯著提高計(jì)算精度并在宏觀和細(xì)觀尺度上較好地預(yù)測(cè)非均質(zhì)材料的力學(xué)特性。文獻(xiàn)[16,17]采用單向多尺度方法建立了局部細(xì)觀模型,利用子模型方法將宏觀響應(yīng)量傳遞給細(xì)觀模型進(jìn)行應(yīng)力及損傷分析,可用較小的計(jì)算量獲得較高精度的局部應(yīng)力。
本工作運(yùn)用實(shí)驗(yàn)和模擬計(jì)算分析了31%B4C/6061Al (質(zhì)量分?jǐn)?shù))復(fù)合材料熱壓縮過程中的斷裂損傷模型,考慮了溫度和應(yīng)變率對(duì)裂紋開裂的影響,確定了GTN (Gurson-Tvergaard-Needleman)損傷模型中的材料常數(shù),并采用單向多尺度有限元法分析了裂紋開裂的細(xì)觀機(jī)制。
通過模擬仿真方法研究材料的斷裂損傷行為時(shí),損傷模型的選取是至關(guān)重要的,只有恰當(dāng)?shù)剡x取損傷模型,才能保證材料斷裂后計(jì)算結(jié)果的正確性。通常情況下,材料壓縮過程中的斷裂模型主要有剪切斷裂(shear fracture)[18,19,20,21]、J-C (Johnson-Cook) 斷裂[22]和GTN斷裂[23,24]模型。J-C損傷模型適用于高應(yīng)變率切削仿真,因此,本工作主要考慮剪切損傷和GTN損傷模型。
剪切損傷是由材料變形過程中內(nèi)部剪切帶的滑移引起的,因此剪切損傷模型在熱壓縮模擬過程中是值得考慮的。塑性變形單調(diào)遞增的狀態(tài)變量(WD)表示為[25]:
式中,
1 損傷模型
1.1 剪切損傷模型
1.2 GTN損傷模型
GTN損傷模型是基于Gurson[26]提出的多孔材料理論演變而來的。Gurson[26]提出,在塑性變形過程中,材料的微觀組織會(huì)出現(xiàn)很多隨機(jī)分布的小孔洞,在材料加工變形中,這些小孔洞會(huì)不斷的生長(zhǎng)、變大,最后聚集形成大孔洞直到材料斷裂。Needleman和Tvergaard[27]考慮了材料變形過程中孔洞之間的相互作用對(duì)材料斷裂的影響,改進(jìn)了多孔材料理論,從而形成了GTN損傷模型。其中材料的屈服函數(shù)(Φ)如下[27]:
式中,σy為材料的屈服應(yīng)力,q1、q2和q3為反映孔洞相互作用的常數(shù),σm為平均應(yīng)力,f *為孔洞合并時(shí)失去應(yīng)力承載能力的函數(shù),是關(guān)于孔洞體積分?jǐn)?shù)(f)來進(jìn)行定義:
式中,fc為臨界孔洞體積分?jǐn)?shù),ff為完全失效時(shí)的孔洞體積分?jǐn)?shù),fu為平衡系數(shù)。
在塑性變形過程中,
式中,
2 熱壓縮實(shí)驗(yàn)
實(shí)驗(yàn)材料為粉末冶金方法制備的31%B4C/6061Al復(fù)合材料,B4C顆粒平均尺寸為5~20 μm,其初始顯微組織如圖1所示。6061Al合金的主要化學(xué)成分(質(zhì)量分?jǐn)?shù),%)為:Fe 0.70,Si 0.80,Mn 0.15,Cr 0.35,Mg 1.20,Zn0.25,Al 余量。熱壓縮實(shí)驗(yàn)試樣尺寸為直徑8 mm×12 mm的圓柱體,實(shí)驗(yàn)溫度分別為375、425、475和525 ℃,應(yīng)變率為0.01、0.1、1和10 s-1。壓縮實(shí)驗(yàn)在Gleeble 3800 熱力模擬試驗(yàn)機(jī)上進(jìn)行,在壓縮實(shí)驗(yàn)過程中,Gleeble 3800熱模擬機(jī)微處理器利用標(biāo)準(zhǔn)的方程自動(dòng)采集實(shí)驗(yàn)數(shù)據(jù)和曲線。熱壓縮后在線切割機(jī)上將試樣沿垂直加載軸方向切割,并利用MEF4A型萬能光學(xué)顯微鏡(OM)觀察并測(cè)量裂紋長(zhǎng)度。
圖1
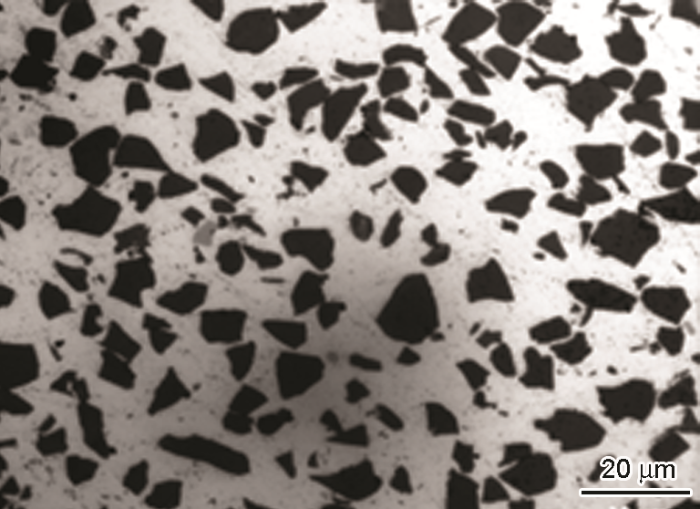
圖1 31%B4C/6061Al 復(fù)合材料的初始顯微組織的OM像
Fig.1 OM image of initial microstructure of 31%B4C/6061Al composite
3 有限元模擬
為保證有限元仿真與實(shí)驗(yàn)結(jié)果的一致性,在ABAQUS有限元軟件中建立了與實(shí)驗(yàn)試樣尺寸相同的三維非線性熱力耦合有限元模型,如圖2所示。模型中上下模具定義成解析剛體,仿真計(jì)算選用動(dòng)態(tài)顯式(ABAQUS/Explicit)求解器,網(wǎng)格類型采用三維八節(jié)點(diǎn)六面體減縮積分單元C3D8RT。熱壓縮模擬試樣的材料常數(shù)見表1,本構(gòu)關(guān)系見文獻(xiàn)[11],上下模具與試樣之間的摩擦系數(shù)為0.3[28]。解析剛體的約束和載荷通過參考點(diǎn)(reference point)定義。由于在實(shí)驗(yàn)中采用的是單向壓縮,因此,將下模具采用完全固定的約束,而在上模具施加不同應(yīng)變率所對(duì)應(yīng)的速率(v)為:
圖2
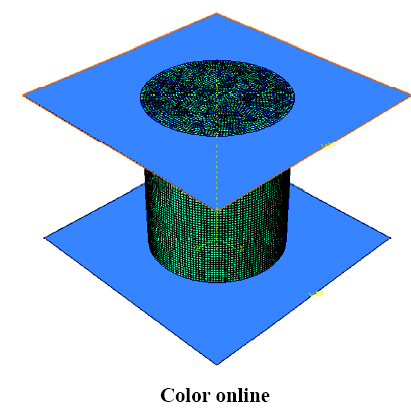
圖2 熱壓縮有限元模型
Fig.2 Finite element model for hot compression
表1 31%B4C/6061Al復(fù)合材料熱物理性能
Table 1
Thermo-physical parameter | Value | Unit |
---|---|---|
Young's modulus (E) | 136 | GPa |
Shear modulus of elasticity (G) | 52.3 | GPa |
Specific heat (cp) | 1.381 | J·g−1·K−1 |
Thermal diffusivity | 31.42 | m2·s−1 |
Coefficient of thermal expansion (φ) | 16.9×10−6 | K−1 |
Poisson's ratio (μ) | 0.3 | |
Density (ρ) | 2.64 | g·m−3 |
式中,S為試樣的壓縮量,t為壓縮時(shí)間,ε和
4 結(jié)果與分析
4.1 裂紋形貌分析
圖3所示為31%B4C/6061Al復(fù)合材料在應(yīng)變率10 s-1、壓下量為75%時(shí),不同溫度下的熱壓縮實(shí)驗(yàn)所得的裂紋形貌。從圖中可以看出,熱壓縮后的試樣出現(xiàn)了不同深度和寬度的裂紋,而且裂紋都是沿著平行于加載方向分布的。隨著實(shí)驗(yàn)溫度的升高,裂紋的深度和寬度有所下降,這也進(jìn)一步驗(yàn)證了隨著熱變形溫度的升高,31%B4C/6061Al復(fù)合材料的可加工性提高。
圖3
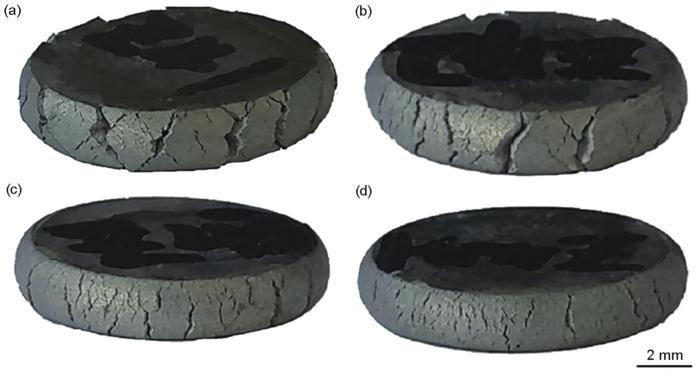
圖3 應(yīng)變率10 s-1、壓下量為75%時(shí),31%B4C/6061Al復(fù)合材料熱壓縮后不同溫度下的裂紋形貌
Fig.3 Crack morphologies of 31%B4C/6061Al composite after hot compression at 375 ℃ (a), 425 ℃ (b), 475 ℃ (c) and 525 ℃ (d) under strain rate of 10 s-1 and reduction of 75%
圖4所示為采用剪切損傷模型模擬計(jì)算得到的應(yīng)變率為10 s-1、壓下量為27%時(shí),不同溫度下31%B4C/6061Al復(fù)合材料熱壓縮后的裂紋形貌??梢钥闯?,當(dāng)熱壓溫度為375 ℃時(shí),圓柱試樣上出現(xiàn)了2條約45°方向的斜裂紋。由于上下模具與試樣的摩擦作用,試樣在壓縮過程中除了受與加載方向成45°方向的剪應(yīng)力外,還有較小的正壓力,因此,試樣出現(xiàn)了沿45°方向的剪切斷裂和沿壓縮方向的局部斷裂。通過與圖3的實(shí)驗(yàn)結(jié)果比較,可以發(fā)現(xiàn)剪切損傷模型計(jì)算所得的裂紋形貌與實(shí)驗(yàn)完全不符,說明剪切損傷模型不能預(yù)測(cè)31%B4C/6061Al復(fù)合材料熱壓過程的斷裂。
圖4

圖4 應(yīng)變率10 s-1、壓下量為27%時(shí),由剪切損傷模型計(jì)算所得不同溫度下31%B4C/6061Al復(fù)合材料的裂紋形貌
Fig.4 Crack morphologies of 31%B4C/6061Al composite calculated by shear fracture model at 375 ℃ (a), 425 ℃ (b), 475 ℃ (c) and 525 ℃ (d) under strain rate of 10 s-1 and reduction of 27%
圖5所示為采用GTN損傷模型計(jì)算得到的應(yīng)變率為10 s-1時(shí),不同溫度下31%B4C/6061Al復(fù)合材料熱壓縮后的裂紋形貌。可以看出,模擬計(jì)算所得裂紋形貌與實(shí)驗(yàn)結(jié)果相同。模擬中發(fā)現(xiàn),采用GTN損傷模型,在壓下量較小時(shí),試樣表面并沒有出現(xiàn)裂紋,這與實(shí)驗(yàn)觀測(cè)到的現(xiàn)象一致。除此之外,可以明顯地發(fā)現(xiàn),隨著熱壓溫度的升高,試樣表面的裂紋變淺、寬度變窄,這也與實(shí)驗(yàn)所得結(jié)果相吻合。因此,GTN損傷模型可以很好地預(yù)測(cè)31%B4C/6061Al復(fù)合材料熱壓縮過程的斷裂行為。
圖5

圖5 應(yīng)變率10 s-1時(shí)由GTN損傷模型計(jì)算所得不同溫度下31%B4C/6061Al復(fù)合材料的裂紋形貌
Fig.5 Crack morphologies of 31%B4C/6061Al composite calculated by GTN model at 375 ℃ (a), 425 ℃ (b), 475 ℃ (c) and 525 ℃ (d) under strain rate of 10 s-1
4.2 GTN損傷模型參數(shù)的確定
為了準(zhǔn)確預(yù)測(cè)31%B4C/6061Al復(fù)合材料熱壓縮過程的斷裂特性,經(jīng)過多次試算發(fā)現(xiàn)GTN模型中損傷參數(shù)εN、SN、fN、fc和ff對(duì)裂紋特性影響較大。f0為復(fù)合材料內(nèi)部的初始孔洞體積分?jǐn)?shù),由于基體和增強(qiáng)相之間界面及基體內(nèi)部的材料缺陷會(huì)使初始孔洞體積分?jǐn)?shù)不為零。因此,比較不同壓縮條件下實(shí)驗(yàn)與模擬結(jié)果,通過對(duì)這些損傷參數(shù)的多次調(diào)整,最終確定了31%B4C/6061Al復(fù)合材料的GTN損傷模型參數(shù)為q1=1.5,q2=1,q3=2.25,f0=0.0025,fc=0.0065,ff=0.0098,fN=0.005,εN=0.3,SN=0.08,其中q1、q2、q3值采用Abendroth等[29]和Benseddiq等[30]的研究結(jié)果,f0值采用文獻(xiàn)[23]的研究結(jié)果。
圖6顯示了應(yīng)變率為10 s-1時(shí)不同溫度下GTN損傷模型計(jì)算與實(shí)驗(yàn)裂紋深度對(duì)比。GTN損傷模型的裂紋形貌通過ABAQUS軟件的視圖切面功能獲得,每一個(gè)圖形都是從熱壓縮試樣中間切開,并用測(cè)量工具測(cè)出裂紋深度,如圖6a~d所示。實(shí)驗(yàn)所得的裂紋是將試樣沿垂直加載方向切開,在OM下測(cè)量裂紋深度,如圖6e~h所示。可以看出,GTN損傷模型計(jì)算與實(shí)驗(yàn)裂紋形貌和深度非常相似,而且,隨著熱壓溫度的升高,裂紋的深度都逐漸減小,模擬的誤差在15%之內(nèi)。
圖6

圖6 應(yīng)變率為10 s-1時(shí)不同溫度下GTN損傷模型計(jì)算與實(shí)驗(yàn)裂紋深度對(duì)比
Fig.6 Comparisons of crack depth calculated by GTN model (a~d) and experimental results (e~h) at 375 ℃ (a, e), 425 ℃ (b, f), 475 ℃ (c, g) and 525 ℃ (d, h) under strain rate of 10 s-1
圖7a給出了31%B4C/6061Al復(fù)合材料在應(yīng)變率為10 s-1時(shí),不同溫度下GTN損傷模型計(jì)算與實(shí)驗(yàn)載荷-位移曲線的比較,圖7b顯示了525 ℃時(shí)不同應(yīng)變率下GTN損傷模型計(jì)算與實(shí)驗(yàn)載荷-位移曲線的比較??梢钥闯?,隨著溫度的升高和應(yīng)變率的降低,材料的流變應(yīng)力逐漸下降,模擬曲線和實(shí)驗(yàn)曲線吻合很好。在不同熱壓縮條件下, 31%B4C/6061Al復(fù)合材料的載荷-位移曲線變化規(guī)律相似。在變形的初始階段,即彈性階段,載荷隨位移的增加而急劇升高;變形中期,載荷曲線隨位移的增加變化很平緩;當(dāng)位移為6 mm左右(壓下量為試樣高度的二分之一)時(shí),載荷隨位移的增加又快速增大。變形中期載荷變化平緩是由于熱變形過程中,硬化機(jī)理(如應(yīng)變硬化)以及軟化機(jī)理(如動(dòng)態(tài)回復(fù)、動(dòng)態(tài)再結(jié)晶)同時(shí)產(chǎn)生且相互作用[31]。
圖7
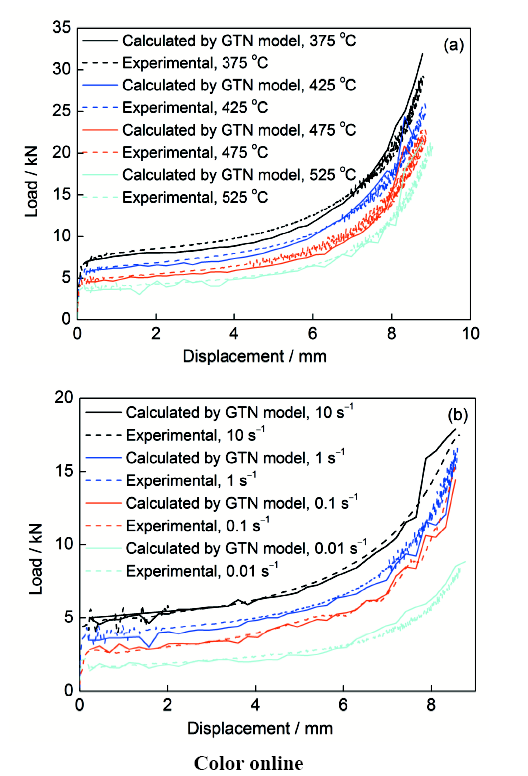
圖7 不同溫度和應(yīng)變率下GTN損傷模型與實(shí)驗(yàn)所得熱壓縮過程中載荷-位移曲線的比較
Fig.7 Comparisons of load-displacement curves be-tween experimental and calculated by GTN model during hot compression at strain rate of 10 s-1 (a) and 425 ℃ (b)
通過比較可以發(fā)現(xiàn),采用GTN損傷模型計(jì)算的31%B4C/6061Al復(fù)合材料熱壓裂紋形貌、尺寸及載荷-位移曲線與實(shí)驗(yàn)所得結(jié)果高度吻合。因此,本工作所求解的31%B4C/6061Al復(fù)合材料GTN損傷模型參數(shù)是準(zhǔn)確可靠的,并且可以應(yīng)用到該材料有限元數(shù)值模擬中。
4.3 多尺度法分析細(xì)觀裂紋形成原因
采用單向多尺度有限元法分析31%B4C/6061Al復(fù)合材料的細(xì)觀斷裂特性時(shí),由于熱壓縮實(shí)驗(yàn)的軸對(duì)稱特性,選取如圖8所示的9個(gè)位置。然后建立包含顆粒和基體的二維細(xì)觀有限元模型,如圖9所示。將上面宏觀模擬得到的有效集合1~9的位移值提取出來輸入到細(xì)觀有限元模型中。
圖8

圖8 有限元模擬中特征位置的選取
Fig.8 Selections of feature positions in finite element simulation
圖9
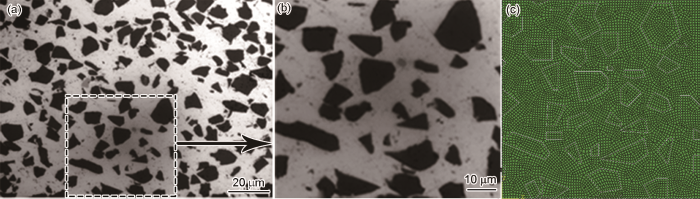
圖9 31%B4C/6061Al復(fù)合材料二維細(xì)觀有限元模型的建立
Fig.9 Establishment of 2D mesoscopic finite element model of 31%B4C/6061Al
(a) microstructure (b) local zooming (c) finite element model
通過細(xì)觀子模型的計(jì)算發(fā)現(xiàn),隨著計(jì)算時(shí)間的延長(zhǎng),只有集合6和9二維細(xì)觀有限元模型中出現(xiàn)了裂紋,其它位置只是發(fā)生了不同程度的變形。圖10顯示了沿壓縮方向不同時(shí)刻的等效應(yīng)力圖。從圖10a可以看出,隨著壓下量的增加,B4C顆粒發(fā)生了脆性斷裂,而且斷裂的位置一般出現(xiàn)在顆粒的尖角處,這是由于應(yīng)力集中的緣故。隨著壓下量的增加,基體和顆粒的界面出現(xiàn)了脫黏,如圖10b所示,然后基體也出現(xiàn)了不同程度的損傷,如圖10c所示。小裂紋繼續(xù)擴(kuò)展、合并,最后形成2條長(zhǎng)裂紋,如圖10d所示。這也說明了31%B4C/6061Al復(fù)合材料熱壓縮過程中出現(xiàn)的裂紋是由細(xì)觀結(jié)構(gòu)中顆粒的脆性斷裂、基體和界面的脫黏以及基體損傷導(dǎo)致的。
圖10
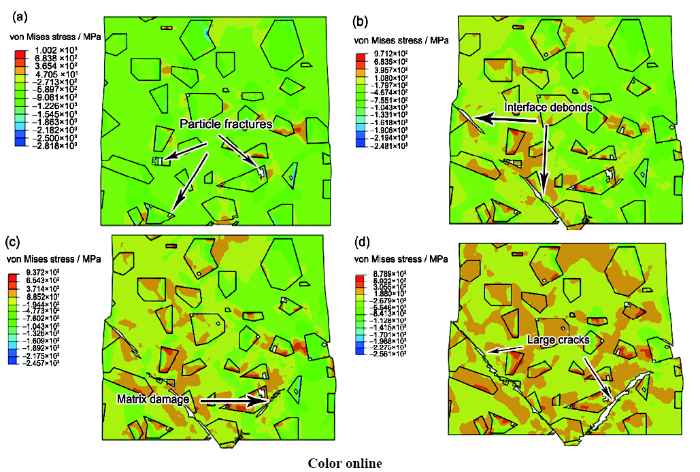
圖10 隨壓縮時(shí)間的延長(zhǎng),細(xì)觀模型中裂紋的形成過程
Fig.10 Crack formation in mesoscopic model at time of 0.06 s (a), 0.062 s (b), 0.065 s (c) and 0.068 s (d)
5 結(jié)論
(1) 通過有限元分析與實(shí)驗(yàn)對(duì)比,剪切損傷模型不能預(yù)測(cè)31%B4C/6061Al復(fù)合材料熱壓縮開裂行為,GTN損傷模型能準(zhǔn)確預(yù)測(cè)31%B4C/6061Al復(fù)合材料熱壓縮斷裂行為。
(2) 通過比較不同壓縮條件下實(shí)驗(yàn)與模擬結(jié)果,分析了壓縮裂紋深度與載荷-位移曲線,確定了31%B4C/6061Al復(fù)合材料的GTN損傷參數(shù),從而為該材料斷裂模擬計(jì)算提供了可靠數(shù)據(jù)。
(3) 運(yùn)用單向多尺度有限元法分析了B4C/6061Al復(fù)合材料熱壓縮過程的細(xì)觀損傷機(jī)理,熱壓縮過程中出現(xiàn)的宏觀裂紋是由細(xì)觀結(jié)構(gòu)中顆粒的脆性斷裂、基體和界面的脫黏以及基體損傷導(dǎo)致的。
來源--金屬學(xué)報(bào)
國(guó)檢檢測(cè)最新產(chǎn)品
同類文章排行
- 分享:B4C/6061Al復(fù)合材料熱壓縮斷裂行為的多尺度研究
- 分享:新型耐磨耐高溫氧化NiCrAlSiC復(fù)合涂層的制備及性能研究
- 分享:GH984G合金在700 ℃水蒸氣中的氧化行為
- 分享:Al-Bi合金凝固過程及微合金化元素Sn的影響
- 分享:Mo元素及熱處理對(duì)Ni2CrFeMox高熵合金在NaCl溶液中耐蝕性能的影響
- 分享:地質(zhì)處置低氧過渡期X65低碳鋼腐蝕行為研究
- 分享:靜水壓力對(duì)超純Fe腐蝕行為的影響
- 分享:電磁旋流水口連鑄技術(shù)對(duì)小方坯凝固組織形貌和宏觀偏析的影響
- 分享:TC11/TC17鈦合金線性摩擦焊接頭界面研究
- 分享:Fe-BTC表面氨基化及對(duì)染料和重金屬離子的吸附性能研究
最新資訊文章
您的瀏覽歷史
