分享:粉末粒徑對AlSi10Mg合金選區激光熔化成形的影響
王孟, 楊永強, Trofimov Vyacheslav, 宋長輝, 周瀚翔, 王迪,
通過模擬仿真與實驗結合研究粉末粒徑對選區激光熔化(SLM)可加工性的影響。以3種粒徑AlSi10Mg粉末為對象,基于離散元和流體力學數值模擬方法研究SLM鋪粉和粉末熔化/凝固介觀行為,并對成形樣品進行宏觀成形質量檢測。結果表明,鋪粉過程中,粒徑小于20 μm的粉末劇烈團聚形成大量空隙,粒徑大于53 μm粉末易形成少量大的空隙,中等粒徑粉末床相對密度比細粒徑和大粒徑分別高7.69%和3.17%。單層粉末床熔融時,鋪粉質量不均勻,細粒徑與粗粒徑熔道不規則。但經歷多層熔化后,細粒徑熔道缺陷部分緩解。隨著粒徑的增加,熔道表面平整度下降,細粒徑粉末樣品存在較多孔隙,粗粒徑粉末存在少量未熔合缺陷。中等粒徑粉末SLM可加工性最好,樣品相對密度達到99.8%,比細粒徑和粗粒徑分別高1.4%和0.4%。
關鍵詞:
選區激光熔化(SLM)是一種高精度增材制造技術,通過激光束定向熔化鋪設在基板上的粉末床,實現高自由度構件成形[1]。由于鋪粉工藝特性以及激光光斑小,SLM通常使用直徑15~53 μm的粉末,粒徑15 μm以下的粉末少有使用,53 μm以上的粉末則在定向能量沉積中應用廣泛。
微米級粉末流動缺少合適的觀察手段。離散元方法(DEM)通過Newton定律顯式計算顆粒間相互作用力和運動,為研究粉末流動提供了重要手段,學者們[2~5]借助DEM模擬了介觀尺度顆粒流動過程。Si等[2]在DEM模型中引入了堆積密度、結構均勻性、歸一化層厚和表面均勻性來定量表征粉末床質量。Han等[6]分析了單層和多層粉末沉積過程中粉末厚度對粉末床特性的影響。Chen等[7]基于DEM系統研究鋪粉過程中團聚、壁面、滲透效應,揭示了粉末床鋪粉密度變化機理。Yao等[8]研究了鋪粉工藝參數、粉輥形狀、粉末尺寸對粉末床質量的影響。
對于不同粒徑SLM鋪粉差異,文獻[9,10]采用DEM分析了細粒徑粉末團聚效應與幾何效應的競爭機制,指出適當的團聚黏附可改善粉末床均勻性。文獻[11,12]通過實驗測量了不同粒徑粉末擴散密度、吸濕性、表面能、內聚功等粉末屬性,采用粉體流變儀(FT4)、漫反射光譜(DRS)方法定量描述粉末床流動性、激光吸收率差異,系統研究了粒徑對實際層厚、成形致密度、尺寸精度、顯微硬度、組織演變的影響,指出粗粉更利于SLM成形。將鋪粉過程和粉末熔化過程相結合,可以研究粉末床質量對SLM成形的影響。Gu等[13]采用DEM對多種粒徑粉末鋪設固定層厚粉末床,并將粉末床導入流體模型進行熔化/凝固模擬,結果表明粒徑25 μm的粉末能夠形成更加平滑和致密的熔道。然而不同的粉末粒徑具有不同的鋪粉密度,導致實際層厚存在顯著差異,激光熔化/凝固過程也存在差異。
為此,本工作以3種粒徑(0~20 μm (PSD1)、20~53 μm (PSD2)、53~105 μm (PSD3)) AlSi10Mg粉末為對象,基于DEM的內聚模型建立SLM鋪粉模型,考慮粉末層厚僅與粒徑相關,研究不同粒徑的鋪粉行為差異。通過建立DEM與計算流體力學(CFD)模型單向耦合,研究單層粉末床質量對熔道溫度、形貌的影響,揭示粒徑對于熔化/凝固的影響規律。并開展相關實驗驗證,進一步研究粉末粒徑對SLM成形的影響規律。
1 數值模擬方法
1.1 鋪粉數值模擬
通過DEM建立小尺度粉末鋪設物理模型。本工作中,直徑0~5 μm的AlSi10Mg粉末會帶來極大的計算消耗,因此舍去,其余粒徑與實際粒徑分布一致,此外細粒徑顆粒間存在的Van der Waals力不可忽略[9]。因此采用DEM中Hertz-Mindlin with Johnson-Kendall-Roberts (JKR)模型[14],通過對鄰近區域顆粒施加法向引力來考慮Van der Waals力的影響,有效模擬顆粒團聚現象。JKR法向引力(FJKR)由表面能密度(γ)、粒子間臨界距離(δ)決定[14]:
式中,E為等效Young's模量,R為Hertz-Mindlin定義的等效半徑,a為粒子間接觸半徑。
DEM模型中,粉末顆粒間恢復系數(rs)、滑動摩擦系數(μs)和滾動摩擦系數(μr)均影響鋪粉動態行為。受實驗條件限制,僅對部分參數進行標定。金屬顆粒具有較高的強度、硬度和球形度,滾動過程中阻力非常小[15],因此μr設置為0.09。采用休止角(粉末堆積斜面與底面夾角,AOR[16])方法對rs、μs和γ進行參數標定,休止角標定模型如圖1a所示。
圖1
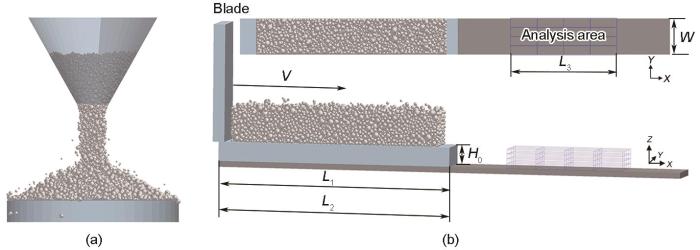
圖1 休止角和鋪粉離散元方法(DEM)物理模型
Fig.1 Physical model of discrete element method (DEM) for angle of repose (AOR) (a) and powder spreading (b) (V—speed of blade, W—width of substrate, H0—height of layer thickness, L1—length of powder platform, L2—length of substrate, L3—length of analysis area)
鋪粉物理模型如圖1b所示。初始粉末堆在粉末平臺生成,刮板沿X方向鋪粉,臺階處高H0為鋪粉層厚。不同粉末粒徑所需層厚不同,實際鋪粉層厚一般為設置層厚的1倍以上[17]。提取分析區域粉末堆積形貌、堆積密度作為分析對象。為了減小時間步長,將Young's模量縮小了100倍,在DEM模擬領域是可以接受的,對結果影響較小[3]。
1.2 粉末熔化/凝固數值模擬
采用CFD方法建立高能激光束作用下單層粉末顆粒熔化/凝固介觀模型,分析粉末粒徑對SLM過程成形輪廓、溫度的影響規律。熔池流動遵循質量守恒、動量守恒和能量守恒定律,考慮金屬固/液轉變,控制方程見文獻[18]。激光束采用Gaussian分布的等效熱源模型[19]:
式中,Slaser為吸收的激光能量,A為激光吸收率,P為激光功率,r為激光束半徑,t為時間,vlaser為激光掃描速率,(xi, yi )為激光焦點中心的初始位置。熱源直接施加于粉末上表面,通過有限體積(VOF)方法捕獲該界面。激光只發生一次吸收,不考慮激光反射、折射和透射。
熔池內溫度超過液相溫度甚至蒸發溫度,且上、下區域存在保護氣、基板,因此需要考慮熔池對外圍區域的能量損失(Eloss)邊界條件[20,21]:
式中,Evap為蒸發熱損失,Erad為輻射熱損失,Ecov為對流熱損失。
熔池匙孔處蒸發氣體對熔體產生反作用力,熔池表面的高溫度梯度導致Marangoni效應,同時熔體表面存在表面張力等,考慮熔池的力邊界條件[22,23]:
式中,Fdrive為熔池驅動力總和,Fpr為蒸汽反沖壓力,Fst為表面張力,Fm為Marangoni力,Fdamp為凝固糊狀區的曳力,G為重力,Fbuo為浮力。
提取DEM模擬的粉末床幾何信息,包括顆粒中心坐標和顆粒直徑,初始化該幾何區域為金屬相,實現DEM至CFD單向耦合[23]。激光照射至粉末床的深度有限,為了綜合考慮3種粒徑粉末熔化過程,統一設置流體模型的粉末床厚度80 μm,模擬單層粉末熔化過程。計算域尺寸為600 μm × 300 μm × 160 μm,包括50 μm厚基板,粉末床和110 μm厚保護氣區域。PSD1采用2.5 μm網格,PSD2和PSD3為3 μm網格,時間步長1 × 10-7 s。AlSi10Mg物性參數參考文獻[24]。
2 實驗方法
采用與仿真相同的參數開展相關SLM實驗,進一步驗證和分析仿真結果。實驗使用配備500 W光纖激光器的DiMetal-100H金屬3D打印機。實驗材料為氣霧化法制備的3種不同直徑AlSi10Mg粉末,其化學成分如表1所示,采用LA960S激光粒度儀測量粉末粒徑分布,結果如圖2a所示。其中D10、D50和D90分別為累積粒度分布達到10%、50%和90%的顆粒直徑,該分布信息直接用于DEM顆粒生成。通過實測獲得3種粒徑粉末PSD1、PSD2和PSD3休止角分別為36°、33°和32°,休止角標定DEM參數范圍及最終使用參數見表2。
表1 不同粒徑AlSi10Mg粉末的化學成分 (mass fraction / %)
Table 1
Powder | Zn | Si | Ni | Fe | Mn | Mg | Al |
---|---|---|---|---|---|---|---|
PSD1 | 0.011 | 10.24 | 0.022 | 0.14 | 0.01 | 0.35 | Bal. |
PSD2 | 0.010 | 9.66 | 0.020 | 0.10 | 0.20 | 0.42 | Bal. |
PSD3 | 0.009 | 9.74 | 0.003 | 0.10 | 0.03 | 0.28 | Bal. |
圖2

圖2 3種粒徑AlSi10Mg粉末粒徑分布及SEM像
Fig.2 Particle size distribution (a) and SEM images of PSD1 (b), PSD2 (c), and PSD3 (d) (D10, D50, and D90 indicate 10%, 50%, and 90% cumulative particle sizes, respectively)
表2 DEM模型使用參數及參數范圍
Table 2
Parameter | Unit | Value | Variable |
---|---|---|---|
range | |||
Particle density ρ | kg·m-3 | 2680 | - |
Poisson's ratio ? | 0.3 | - | |
Young's modulus E | MPa | 750 | - |
Rolling friction coefficient μr | 0.09 | - | |
Sliding friction coefficient μs | 0.6 | 0.4-0.8 | |
Restitution coefficient rs | 0.64 | - | |
Surface energy density γ | mJ·m-2 | 1.2 | 0-15 |
L1 | mm | 2 | - |
L2 | mm | 4 | 2-6 |
W | 10D50 | 2D50-10D50 | |
H0 | 5D50 | 1D50-5D50 | |
L3 | mm | 1 | - |
V | mm·s-1 | 50 | - |
實驗成形10 mm × 10 mm × 10 mm方塊樣件,P為200、230、260和290 W,vlaser為800、1050、1300和1550 mm/s,掃描間距(d)為0.08 mm,實際打印層厚(H1)為0.03 mm。應用Quanta250環境掃描電鏡(SEM)觀察成形樣品表面形貌;采用VHX-5000超景深三維顯微鏡進行成形表面輪廓和粉末樣品表征,觀測面為樣品上表面。3種粒徑粉末的SEM像見圖2b~d。拋光后通過DMi8光學顯微鏡(OM)觀察上表面和豎直成形面的孔隙分布。采用Archimedes排水法測量方塊密度。激光能量密度(Ev)采用下式計算[12]:
3 結果與討論
3.1 SLM鋪粉動態行為
如圖3所示,當鋪粉層厚為5D50,粉末在基板上前進時,斜坡與基板形成動態堆積角α。α可表征顆粒流動性,α越小,表明顆粒間相互作用力越小,流動阻力小,具有更好的流動性[25]。根據
圖3

圖3 DEM模擬鋪粉過程的動態堆積角
Fig.3 Dynamic packing angles of PSD1 (a), PSD2 (b), and PSD3 (c) during powder spreading by DEM simulation
3.2 粉末床鋪粉質量
鋪粉完成后,得到DEM模擬的3種粒徑粉末床切片和俯視圖,如圖4所示。提取粉末床中心區域作為分析區域,x方向長度1 mm,切片厚度為2D50,鋪粉層厚為5D50。由于PSD1粒徑過小,對PSD1粉末床放大1倍以便清晰展示,如圖4a1和a2所示。
圖4

圖4 DEM模擬的3種粒徑粉末床切片圖和俯視圖
Fig.4 Slices (a1-c1) and top views (a2-c2) of powder bed for PSD1 (magnified) (a1, a2), PSD2 (b1, b2), and PSD3 (c1, c2) by DEM simulation
對比3種粒徑粉末床形貌可以發現,PSD1具有非常多的表層空缺和內部空隙,PSD2鋪粉質量最好,PSD3鋪粉存在少量空隙。從圖4a1可見,PSD1中尺寸小于20 μm的粉末發生嚴重團聚現象,大于20 μm的顆粒未團聚。可見20 μm以下的粒徑Van der Waals力主導了顆粒間相互作用力,低流動性抑制了顆粒的平動和轉動,刮板刮過的區域均勻性較差,且小顆粒隨之團聚,進一步降低了鋪粉質量。團聚作用下,粉末床底部和頂部平整度非常差,z方向高度差達到(2~3)D50,不利于下層粉末穩定鋪設。當團聚發生在粉末床內部時,將產生大量內部空隙,鋪粉不均勻。從圖4a2可知,不僅豎直平面存在空隙,水平面也存在大空隙。粒徑增加到20~53 μm,Van der Waals力減弱,粉末流動性加強,粉末床均勻,也為下層鋪粉提供了平整的基材環境。當然,由于刮板與顆粒間的壁面效應[7],SLM鋪粉過程中刮板與粉末床之間必定存在表層空缺,即圖4b1切片上方空缺區域,經過多層鋪粉后,該空缺能夠得到緩解。隨著粒徑增加至53 μm以上,Van der Waals力對顆粒間作用力可忽略不計。但球體形狀導致相鄰大顆粒存在50 μm以內幾何間隙,由于PSD3粉末中直徑小于50 μm的顆粒較少,大的幾何間隙無法填充,如圖4c1和c2所示,粉末床內部產生較大的空隙,降低了鋪粉質量。
DEM模擬的3種粒徑AlSi10Mg鋪粉的相對密度如圖5所示。由于團聚作用,PSD1在鋪粉層厚為(1~4)D50時,團聚形成的小塊粉末團厚度接近4D50,無法形成有效粉末床,鋪粉相對密度為0,這與實驗觀察結果一致。僅在5D50厚度時形成粉末床(圖4a),團聚導致的大量鋪粉缺陷使其密度最低。鋪粉層厚從1D50增加至3D50時,PSD2鋪粉相對密度略低于PSD3,可能是由于中等粒徑的AlSi10Mg顆粒質量輕,受壁面效應影響較強,表層空缺占比略大。4D50層厚時,層厚的增加使得空缺得到彌補,PSD2鋪粉密度穩定增加并超過PSD3。5D50層厚時,PSD2鋪粉相對密度為32.97%,比PSD1高7.69%,比PSD3高3.17%。AlSi10Mg粉末粒徑低于20 μm時,Van der Waals力作用下,鋪粉難以形成均勻粉末床。粒徑介于20~53 μm的顆粒有良好流動性,但壁面效應降低了鋪粉密度。粒徑介于53~105 μm的顆粒能夠弱化壁面效應,卻存在較大的球體幾何間隙。因此可以考慮在20~105 μm顆粒中定制粒徑分布,以弱化壁面效應和減小幾何間隙,實現高密度鋪粉。
圖5
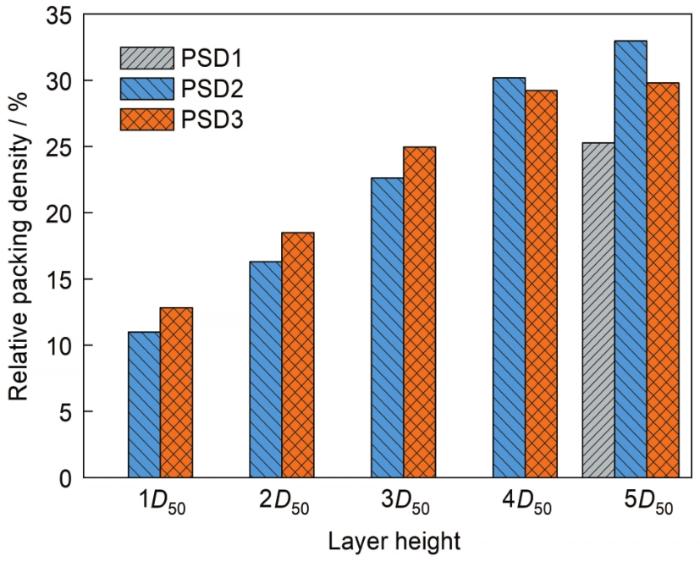
圖5 DEM模擬的3種粉末床相對密度
Fig.5 Relative packing densities of powder bed by DEM simulation
3.3 SLM熔道輪廓與溫度分布
圖6a1~c1為80 μm鋪粉厚度,激光功率290 W,掃描速率1300 mm/s的單層粉末熔化/凝固后熔道輪廓及溫度分布。圖6a1中PSD1熔道形狀不規則,沿激光掃描方向呈現出“偽魚鱗紋”,寬度變化較大。熔池內高溫蒸汽對熔池內壁產生反沖壓力,迫使熔融液體向熔池后部流動至熔道[26],同時,由于沿熔道方向及垂直方向溫度梯度不同,冷卻速率不同,熔融液體會形成錐形凝固形態,即魚鱗紋。而AlSi10Mg熱導率高達130 W/(m·K),黏度低且熔點低,實際熔道中魚鱗紋較淺且間距大,非圖6a1所示。PSD1中“偽魚鱗紋”是由于粉末床不均勻導致的,顆粒團聚形成的粉團松散分布,激光掃描粉團區域時充分熔化并堆積,空腔區域只能通過液體流動填充,形成了凹凸不平的熔道。粉末床的團聚與空缺導致熔融液體體積發生變化,形成的熔道寬度不均勻。如圖6b1所示,粒徑增加至20 μm以上時,粉末床致密度高,表面平坦,內部空隙少,使得熔池表面平坦,熔寬變化小,熔池呈現良好的拖尾現象,可見鋪粉質量對熔道形貌至關重要。當粉末粒徑為53 μm以上時,圖6c1中PSD3熔道產生欠熔合現象。由于激光掃描速率快,大顆粒熔液尚未完全流動便凝固,形成堆積形式的欠熔。顆粒間大的間隙分布不均勻,會被熔融液體填充,同時熔液也受大顆粒分布影響,因此PSD3熔道前進方向并不一定與激光掃描方向一致,熔道方向不穩定。此外激光掃描大粒徑顆粒區域時,無法完全照射多個顆粒,并且Gaussian光束邊緣能量密度低,導致熔道邊緣存在部分未熔化大顆粒,不利于熔道搭接。
圖6
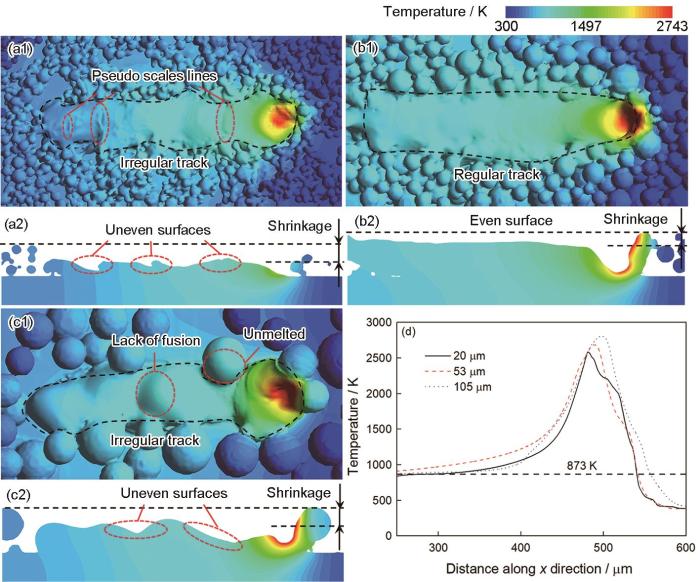
圖6 計算流體力學模擬的選區激光熔化熔道形貌及熔池溫度分布曲線
Fig.6 Molten track and temperature distribution (a1-c1) of PSD1 (a1, a2), PSD2 (b1, b2), and PSD3 (c1, c2); corresponding slices (a2-c2); and temperature distribution curves of molten pool (d)
圖6a2~c2顯示不同粒徑的熔道表面平整度各不相同,與粉末床鋪設質量密切相關。PSD1熔化/凝固后形成了與粉末床相似的大量凸起狀輪廓,如圖6a2所示。PSD1粉末床的低密度意味著粉末總質量小,只能形成較淺的熔池。粒徑上升到20 μm以上時,粉末床表面平整,顆粒分布均勻,大部分顆粒受熱過程穩定,形成了平坦的熔道表面,如圖6b2所示,為下一層鋪粉及熔化提供了較為平整的基材形貌。從圖6c2可見,PSD3熔道表面存在較大的高低起伏。PSD3顆粒間大空隙區域被溶液填充,大顆粒由表至內的熔化產生了液體流動性差異,激光高速掃描導致表面冷卻凝固,困住了內部液體流動,而外部流動液體不足以填充大空隙,形成了凹坑或斜坡輪廓。此外,受大顆粒不規則的空間分布影響,熔池形態與深度均不如PSD2好,導致熔道表面的不規則情況產生。
Gu等[13]在固定層厚下模擬了不同粒徑鎳基復合材料的熔道形貌,發現小粒徑粉末團聚產生的大量空腔以及鋪粉不均勻會導致熔池內金屬蒸氣或保護氣難以從熔池逸出,形成氣孔并保留在凝固基體內。同樣的情況也發生在大粒徑粉末SLM中。而AlSi10Mg具有良好的熱導率、較低的熔點溫度和動態黏度,相同溫度下具有更好的液相流動性及足夠的溶液量[27],使得空隙填充率高于鎳基材料。因此,對于模擬單層AlSi10Mg熔化/凝固產生氣孔的可能性低于鎳基粉末,但是對多層粉末模擬而言,不規則表面形貌以及粉末分布,獲得氣孔分布是可能的。
此外,粉末熔化填充空隙會產生收縮現象,如圖6中shrinkage。當功率密度足夠的情況下,粉末全部熔化并形成實心的基材,空隙得到完全填充。通過收縮高度差(shrinkage)表征3種粉末熔化收縮率,PSD1收縮率最大,PSD3次之,PSD2收縮率最小,說明PSD2粉末具有最低的空隙率。當然,收縮率還受到其他因素影響,Yu等[28]模擬了不同激光功率下AlSi10Mg收縮率差異,發現400 mm/s掃描速率時,存在功率臨界值(250 W),超過該值的功率增長會降低收縮率,低于該值的功率增長會提高收縮率。
圖6d顯示了熔池區域沿激光掃描方向溫度分布曲線。可見,粉末床的不均勻導致熔池區域存在溫度差異。PSD1熔池溫度最低,PSD3最高,PSD2介于2者之間。雖然小粒徑粉末具有較大的表面積以吸收更多的激光能量,但是松散的粉末床由于鋪粉密度低,包含的顆粒總量較少,導致能量吸收不足。同時,粉末床中存在的大量空隙使得基板反射了部分能量,導致PSD1整體吸收能量較低,熔池溫度低。PSD3大部分粉末粒徑接近甚至超過光斑直徑80 μm,激光照射顆粒時,大部分能量被單個顆粒吸收,并且AlSi10Mg與保護氣的比熱、熱導率差異使得能量在大的空隙中擴散較慢,熔池溫度高于其余2種粒徑。PSD2粉末床均勻且粒徑為激光光斑一半,其熔池溫度介于2者之間,與AlSi10Mg蒸發溫度相當。此外,沿激光掃描方向,PSD2高于液相線的熔道長度大于PSD1和PSD3,能夠為金屬液體鋪展提供更大的潤濕范圍。因此,熔道形貌與溫度分布對不同粉末粒徑導致的粉末床均勻性較為敏感[26],中等粒徑能夠提供更好的SLM成形性。
3.4 實驗結果
為了進一步分析粉末粒徑對AlSi10Mg多層多道實際成形效果的影響,開展了系列成形實驗。發現PSD1粉末初始鋪粉過程非常不穩定,粉末堆呈現明顯團聚并形成較高粉末堆,與圖4a1和a2及文獻[25]一致。前幾層很少粉末鋪設到基板上,5層之后開始有粉末團塊非常稀疏地鋪展,基板邊緣縫隙的存在降低了粉末在該區域的停留。鋪粉至30層左右,粉末基本鋪設至基板表面。PSD3由于初始幾層層厚小,大粒徑粉末被刮出基板。PSD2和PSD3均在10層鋪粉時達到穩定。SLM成形過程中,20 μm以下AlSi10Mg粉末質量非常輕,DiMetal-100H設備基板邊緣靠近風循環系統的出風口,粉末易被吹走,導致邊緣粉末不均勻,該區域未能進行有效鋪展,易發生激光多次重熔樣品表面,熱量累積使表面發生翹曲,打印失敗。
圖7顯示了通過超景深三維顯微鏡觀察得到的幾組表面質量較好的樣品表面輪廓,其中功率290 W,掃描速率1300 mm/s,粒徑20 μm以下粉末床致密度較低,實際熔化后凝固層厚度小,因此z方向高度差僅為15 μm。對比圖6a1和a2單層熔化,可見多層熔化能夠緩解表面粗糙現象,因為小粒徑粉末實際熔融層厚小,熱量可傳導并熔化多個凝固層,改善表面質量。粒徑增加至20 μm以上,熔融層厚增加,成形表面波動增加,伴隨著飛濺強度同步增加,PSD2表面高度差擴大至35 μm。根據圖6c1、c2與圖7,PSD3由于大顆粒欠熔合,熔融液體擴散不及時,成形表面高度波動顯著增加,達到75 μm。
圖7

圖7 3種粒徑樣品上表面輪廓高度和超景深三維顯微鏡像
Fig.7 Top surface contour heights (a1-c1) and images (a2-c2) of PSD1 (a1, a2), PSD2 (b1, b2), and PSD3 (c1, c2) samples showed by ultra-depth three-dimensional microscope
圖8是未經任何磨樣處理的樣品上表面SEM像。圖8a顯示PSD1樣品表面非常平坦,較小的熔融厚度使得熔道搭接不明顯。PSD2熔融厚度的增加,提高了熔道高度,實驗采用45°正交掃描策略,表面清晰可見交叉疊加的熔道,如圖8b所示。粉末粒徑增大時,PSD3熔道顯著寬于前2種粉末,如圖8c所示,過大的顆粒引導了熔道發展方向,顆粒欠熔導致熔道起伏波動大,粗糙度高。3種粒徑成形樣品上表面均未觀察到明顯的空隙等缺陷,說明AlSi10Mg粉末在自身高熱導率和低熔點影響下,較高的熔融液體流動性使得鋪粉缺陷在多層熔化/凝固后得到部分彌補,這是由粉末屬性決定的。
圖8

圖8 3種粒徑樣品上表面形貌的SEM像
Fig.8 Top surface SEM images of PSD1 (a), PSD2 (b), and PSD3 (c) samples
圖9顯示了3種粒徑樣品內部缺陷分布的OM像。Van der Waals力作用下,小粒徑粉末傾向于團聚成團塊,粉末不易在粉末床完全鋪展開,形成較多的空隙。同時,與大粒徑粉末相比,其流動性較低,會在刮刀前方形成陡峭粉末堆,阻礙刮刀鋪粉過程,進一步降低了粉末床致密度。因此,即使PSD1上表面平坦,內部必然存在較多的孔隙。從圖9a1和a2可見,PSD1樣品內部存在較多孔隙,雖然較薄的熔融層厚能夠帶來更多的熱傳導,但是粉末床內大量孔隙仍然受困,難以逸出至熔池表面。圖9b1和b2顯示PSD2樣品內部僅有非常少量的孔隙,因為PSD2粉末床自身僅存在少量空隙,平整且均勻的粉末床為熔液流動和填充提供了良好的滲透環境。如圖9c1和c2所示,PSD3樣品內部存在少量孔隙和尺寸較大的未熔合缺陷。PSD3中粒徑超過激光直徑的大顆粒粉末稀疏分布在粉末床內,激光能量無法完全熔化該顆粒,形成非常不均勻的熔道,下層粉末熔化也未能完全填充該區域,從而降低了成形質量,并且粉末床內部的大空隙導致了樣品孔隙增加。
圖9

圖9 3種粒徑樣品水平和豎直截面孔隙分布的OM像
Fig.9 OM images showing horizontal (a1-c1) and vertical (a2-c2) pore distributions of PSD1 (a1, a2), PSD2 (b1, b2), and PSD3 (c1, c2) samples
圖10統計了幾個不同能量密度下成形樣品的相對密度。經過表面粗磨后,PSD2和PSD3相對密度均超過99%,其中PSD2相對密度可達到99.8%,比PSD3高0.4%,比PSD1高1.4%。PSD1因其內部較多的孔隙,成形密度最低,且能量密度為130 J/mm3時,密度明顯下降,對能量密度變化更為敏感,說明AlSi10Mg粒徑對SLM成形質量影響顯著。
圖10

圖10 不同能量密度下3種粒徑樣品相對密度
Fig.10 Relative densities of samples with different energy densities
4 結論
(1) 開發了基于離散元方法的SLM鋪粉物理模型和基于流體熱力學的粉末熔化/凝固模型。細粒徑粉末Van der Waals力主導了顆粒間相互作用力,粉末團聚程度加劇,流動能力減弱。鋪粉將產生大量不均勻的空隙和空缺,嚴重降低粉末床密度。由于團聚效應,小粒徑粉末鋪粉所需的層厚至少為5D50。大粒徑粉末由于球體間大的幾何間隙無法得到填充,鋪粉穩定后,粉末床致密度略低于中等粒徑粉末。
(2) 不同粒徑粉末床存在的缺陷在多層熔化/凝固過程中通過熔融液體流動擴散,可得到一定緩解。
(3) 細粉末樣品具有最平坦的表面,但由于其粉末床內存在大量空隙,SLM成形時內部氣孔無法全部逸出,形成較多孔隙,致密度最低。而粗粉末由于粒徑接近或超過激光光斑直徑,易產生成未熔,降低了致密度。
(4) SLM成形AlSi10Mg對粉末粒徑敏感性強。中等粒徑粉末SLM可加工性最好,相對密度可達到99.8%,分別比細粒徑和粗粒徑粉末高1.4%和0.4%。
來源--金屬學報