分享:計(jì)算輔助高性能增材制造鋁合金開(kāi)發(fā)的研究現(xiàn)狀與展望
高建寶1, 李志誠(chéng)1, 劉佳1, 張金良2, 宋波,2, 張利軍
,1
增材制造技術(shù)為高強(qiáng)鋁合金復(fù)雜零部件的制造帶來(lái)了前所未有的機(jī)遇,但目前增材制造鋁合金體系仍局限于可鑄造和可焊接的Al-Si系合金,制約了高性能增材制造鋁合金的快速發(fā)展。近年來(lái),不同尺度的計(jì)算方法逐步用于輔助高性能增材制造鋁合金的開(kāi)發(fā)。本文詳細(xì)綜述了國(guó)內(nèi)外學(xué)者在計(jì)算輔助增材制造鋁合金設(shè)計(jì)與制備領(lǐng)域的研究成果,列舉了原子、介觀和宏觀尺度計(jì)算模擬及機(jī)器學(xué)習(xí)等計(jì)算方法輔助增材制造鋁合金設(shè)計(jì)的代表性案例,分析了不同計(jì)算方法輔助合金設(shè)計(jì)的策略,并指出其不足。最后,針對(duì)如何推動(dòng)多尺度計(jì)算在高性能增材制造鋁合金開(kāi)發(fā)中的應(yīng)用進(jìn)行了展望,并指出其發(fā)展方向。
關(guān)鍵詞:
鋁合金具有密度低,比強(qiáng)度高,塑性好,導(dǎo)電性、導(dǎo)熱性和抗腐蝕性優(yōu)良等特點(diǎn),是實(shí)現(xiàn)結(jié)構(gòu)輕量化的首選材料,廣泛應(yīng)用于航空航天、交通運(yùn)輸?shù)阮I(lǐng)域[1]。隨著“雙碳”政策對(duì)輕量化需求的進(jìn)一步提升,高強(qiáng)鋁合金復(fù)雜零部件在航天航空、汽車等領(lǐng)域應(yīng)用更加廣泛,但傳統(tǒng)的鋁合金加工存在鑄態(tài)強(qiáng)度較低、制造周期長(zhǎng)、復(fù)雜結(jié)構(gòu)難以成形和材料浪費(fèi)等問(wèn)題,無(wú)法滿足航空航天對(duì)鋁合金構(gòu)件制造技術(shù)高效、快速的要求,缺乏生產(chǎn)復(fù)雜精密結(jié)構(gòu)的靈活性以及隨設(shè)計(jì)變化的快速響應(yīng)能力[2,3]。增材制造(additive manufacturing,AM,又稱3D打印)技術(shù)是基于分層制造原理,采用材料逐層累加的方法,直接將數(shù)字化模型制造為實(shí)體零件的一種新型制造技術(shù)[4]。與傳統(tǒng)制造技術(shù)相比,增材制造技術(shù)具有柔性高、無(wú)模具、周期短、不受零件結(jié)構(gòu)限制等一系列優(yōu)點(diǎn)。選區(qū)激光熔化(selective laser melting,SLM)成形技術(shù)是最有前途的增材制造技術(shù)之一,為高性能復(fù)雜結(jié)構(gòu)金屬零件制造帶來(lái)了巨大的機(jī)會(huì)[5]。
近年來(lái),鋁合金的SLM成形研究備受關(guān)注,涉及Al-Si、Al-Cu、Al-Mg-Si、Al-Zn和顆粒增強(qiáng)鋁基復(fù)合材料等系列鋁合金。然而,大多數(shù)鋁合金存在激光吸收功率低、熱導(dǎo)率高、易氧化、含大量易燒損元素和熱裂傾向強(qiáng)等問(wèn)題[6],成形難度極大。因此,目前能用于增材制造工藝的鋁合金體系仍局限于可鑄造和可焊接的Al-Si系列合金,如AlSi7Mg[7,8]、AlSi10Mg[9,10]和AlSi12[11,12]等。這些鑄造Al-Si合金的近共晶成分具有非常窄的凝固溫度范圍,從而極大降低了在激光增材制造過(guò)程中產(chǎn)生裂紋的風(fēng)險(xiǎn)。通過(guò)SLM制造的AlSi10Mg和AlSi12合金零件近乎全致密,晶粒細(xì)小,且具有獨(dú)特的介觀結(jié)構(gòu)[9,12]。盡管Al-Si鑄造合金具有優(yōu)異的SLM成形性,但其力學(xué)性能仍偏低(中等強(qiáng)度),無(wú)法取代力學(xué)性能更優(yōu)異的變形鋁合金,如高強(qiáng)系列的7xxx系合金和具有良好耐熱性的2xxx系合金[13]。此外,由于增材制造過(guò)程冷卻速率快、溫度梯度大,導(dǎo)致現(xiàn)有的變形鋁合金在增材制造中經(jīng)常存在柱狀晶和嚴(yán)重的熱裂紋傾向[5,6],且很難通過(guò)優(yōu)化工藝參數(shù)來(lái)抑制其開(kāi)裂[14,15]。與此同時(shí),微熔池快速冷卻過(guò)程中極易產(chǎn)生飛濺、球化、孔隙、燒損等冶金缺陷[16]。這些問(wèn)題都嚴(yán)重制約了當(dāng)前高性能增材制造鋁合金的發(fā)展。
研究人員對(duì)高性能增材制造鋁合金的組織和性能等開(kāi)展了大量的實(shí)驗(yàn)研究工作。當(dāng)前高性能增材制造鋁合金的主要研究方向可概括為:(1) 開(kāi)發(fā)高性能的Al-Si系合金,通過(guò)添加Fe、Ni、Er等元素進(jìn)一步提升合金性能[17~19];(2) 開(kāi)發(fā)適用于增材制造過(guò)程的變形鋁合金及其制備工藝,并進(jìn)一步添加Ti[20,21]、Zr[22~24]、Sc[25]等細(xì)化晶粒,將粗大的柱狀晶變?yōu)榧?xì)小均勻的等軸晶,從而減少熱裂紋的形成,提高合金的力學(xué)性能;(3) 開(kāi)發(fā)顆粒增強(qiáng)鋁基復(fù)合材料,在鋁合金基體中添加TiB2、SiC等陶瓷顆粒,不僅能細(xì)化晶粒,提高激光吸收功率,同時(shí)能在后續(xù)熱處理中起到釘扎晶界的作用,提高合金熱處理后的性能[8, 26,27]。需要指出的是,Plotkowski等[28]構(gòu)建了增材制造Al-Ce合金的“成分-工藝-微結(jié)構(gòu)”實(shí)驗(yàn)圖譜,用于合金成分設(shè)計(jì)和工藝選擇,這為從實(shí)驗(yàn)角度進(jìn)行增材制造鋁合金的設(shè)計(jì)提供了一種高效方法。但截止目前,研究人員主要基于“經(jīng)驗(yàn)試錯(cuò)法”開(kāi)展相關(guān)研究,實(shí)驗(yàn)周期長(zhǎng),耗費(fèi)大量的人力物力,而且很難快速找到性能最優(yōu)的目標(biāo)合金。
隨著集成計(jì)算材料工程(Integrated Computational Materials Engineering,ICME)和材料基因工程(Materials Genome Initiative,MGI)等計(jì)劃的深入實(shí)施,各尺度計(jì)算方法逐步應(yīng)用于輔助增材制造鋁合金的設(shè)計(jì)中。如原子尺度的第一性原理計(jì)算和介觀尺度的相圖計(jì)算(Calculation of Phase Diagrams,CALPHAD)方法作為合金設(shè)計(jì)的重要手段,能有效減少新材料設(shè)計(jì)與開(kāi)發(fā)的時(shí)間和成本,實(shí)現(xiàn)合金的高效設(shè)計(jì),已成功用于高性能鋁合金的設(shè)計(jì)與開(kāi)發(fā)[21,29,30]。再如介觀尺度的相場(chǎng)模擬方法,通過(guò)耦合鋁合金熱/動(dòng)力學(xué)數(shù)據(jù)庫(kù),可實(shí)現(xiàn)鋁合金制備過(guò)程中微結(jié)構(gòu)演化的定量模擬[31]。而宏觀尺度的有限元模擬,能對(duì)鋁合金在增材制造過(guò)程中的熔池溫度場(chǎng)、應(yīng)力場(chǎng)和速度場(chǎng)進(jìn)行數(shù)值模擬,揭示變形鋁合金SLM過(guò)程中球化、孔隙和裂紋的形成與冶金行為演變機(jī)制[32]。此外,通過(guò)機(jī)器學(xué)習(xí)對(duì)實(shí)驗(yàn)數(shù)據(jù)進(jìn)行挖掘,建立制備工藝和力學(xué)性能的關(guān)系,能準(zhǔn)確地預(yù)測(cè)裂紋的形成[33]和開(kāi)發(fā)新型高性能鋁合金[34]。綜上所述,第一性原理計(jì)算、CALPHAD、相場(chǎng)模擬及機(jī)器學(xué)習(xí)等各尺度的計(jì)算方法有望實(shí)現(xiàn)高性能增材制造鋁合金的高效設(shè)計(jì)與開(kāi)發(fā)。
本文將基于近年來(lái)國(guó)內(nèi)外學(xué)者的研究成果,分析不同計(jì)算方法進(jìn)行增材制造鋁合金設(shè)計(jì)的策略,并給出原子、介觀和宏觀尺度計(jì)算及機(jī)器學(xué)習(xí)輔助增材制造鋁合金設(shè)計(jì)的代表性案例,進(jìn)而從成分設(shè)計(jì)、工藝設(shè)計(jì)和組織優(yōu)化等方面總結(jié)各尺度計(jì)算在高性能增材制造鋁合金領(lǐng)域的發(fā)展現(xiàn)狀。最后,針對(duì)加速推動(dòng)多尺度計(jì)算在高性能增材制造鋁合金開(kāi)發(fā)中的應(yīng)用進(jìn)行展望,并指出發(fā)展方向。
1 原子尺度計(jì)算/模擬在增材制造鋁合金中的應(yīng)用
1.1 第一性原理計(jì)算
第一性原理指的是量子力學(xué)原理。基于少數(shù)幾個(gè)基本假設(shè)的量子力學(xué)方法,同時(shí)增加了不同程度近似考慮的計(jì)算方法,統(tǒng)稱第一性原理計(jì)算方法。第一性原理計(jì)算考慮了原子和電子層次的相互作用,可提供合金結(jié)構(gòu)與性能關(guān)系之間的準(zhǔn)確信息[35]。
第一性原理計(jì)算能為增材制造鋁合金中固溶強(qiáng)化的元素選擇和添加量提供指導(dǎo)。如:Uesugi和Higashi[36]采用第一性原理計(jì)算,研究了55種Al-mX (m = 3.70、3.13、1.56和0.93,原子分?jǐn)?shù),%)固溶體的晶格常數(shù)變化以及溶質(zhì)原子引起的局部晶格畸變。計(jì)算的體積尺寸因子和錯(cuò)配應(yīng)變與文獻(xiàn)中可用的實(shí)驗(yàn)數(shù)據(jù)非常吻合。同時(shí),作者將錯(cuò)配應(yīng)變用于估算由固溶強(qiáng)化而增加的屈服應(yīng)力,計(jì)算得到的固溶強(qiáng)化程度與現(xiàn)有實(shí)驗(yàn)值吻合較好。如圖1a[37]所示,Michi等[37]總結(jié)了Al-X固溶體中各種元素能提供的固溶強(qiáng)化幅度,與Uesugi和Higashi[36]通過(guò)第一性原理估算的結(jié)果一致,該結(jié)果為增材制造鋁合金的固溶強(qiáng)化元素的選擇和添加量提供了理論指導(dǎo)。同時(shí),Michi等[37]還總結(jié)了Al-X固溶體中各元素的最大平衡固溶度和400℃下在Al中的擴(kuò)散系數(shù)的關(guān)系,如圖1b[37]所示,可以看出,低擴(kuò)散系數(shù)的溶質(zhì)有望在高溫下提供固溶強(qiáng)化效果,有利于尋找最優(yōu)的固溶元素,如具有低擴(kuò)散、高溶解度和高固溶強(qiáng)化效果的Mn。
圖1

圖1 Al-X固溶體中固溶強(qiáng)化效果隨溶質(zhì)濃度的變化,及Al-X固溶體中各元素的最大平衡固溶度與其在400℃下Al中擴(kuò)散系數(shù)的關(guān)系[37]
Fig.1 Plot of solid solution strengthening increment as a function of solute concentration (atomic fraction) in the matrix (a) and plot of diffusivity at 400oC vs maximum equilibrium solid solubility (atomic fraction) for selected solutes in Al (b)[37]
1.2 分子動(dòng)力學(xué)模擬
分子動(dòng)力學(xué)模擬(molecular dynamics simulation)通過(guò)計(jì)算機(jī)對(duì)原子核和電子所構(gòu)成的多體體系中微觀粒子之間的相互作用和運(yùn)動(dòng)進(jìn)行模擬,在此期間把每一原子核視為在其他全部的原子核和電子所構(gòu)成的經(jīng)驗(yàn)勢(shì)場(chǎng)的作用下按照Newton定律進(jìn)行運(yùn)動(dòng),進(jìn)而得到體系中粒子的運(yùn)動(dòng)軌跡,再按照統(tǒng)計(jì)物理的方法計(jì)算得出物質(zhì)的結(jié)構(gòu)和性質(zhì)等宏觀性能[38]。目前,分子動(dòng)力學(xué)在增材制造鋁合金中已有較為廣泛的應(yīng)用,諸如粉末顆粒合并和燒結(jié)頸生長(zhǎng)[39]、凝固過(guò)程中的均勻成核[40]、局部熔化和快速凝固[41]、不同晶粒形態(tài)的力學(xué)拉伸響應(yīng)[42]等方面。
Kurian和Mirzaeifar[41]利用分子動(dòng)力學(xué)建立了微型選區(qū)激光熔化(micro-selective laser melting,μ-SLM)過(guò)程的準(zhǔn)二維(2D)模型,模擬Al納米粉末床熔池內(nèi)部晶核的形成和生長(zhǎng),通過(guò)在空間和時(shí)間上直接控制熔池的溫度,模擬了熔池的局部加熱和快速凝固。如圖2[41]所示,熔池的快速凝固顯示了熔池中心等軸晶粒的均勻形核與冷卻速率相關(guān)。此外,沿著最高的熱流方向,可以觀察到相鄰激光軌道、前層和部分熔化的納米粉末在凝固熔池中的外延晶粒生長(zhǎng)。如果前一層重熔時(shí)的穿透深度小于等軸晶粒的深度,長(zhǎng)柱狀晶粒向頂層的生長(zhǎng)就會(huì)受到抑制。在對(duì)三層鋁納米粉末顆粒進(jìn)行10次激光束照射后得到的最終凝固的納米結(jié)構(gòu)中,觀察到遍布三層的長(zhǎng)柱狀晶粒、等軸晶粒、納米孔、孿生邊界和堆積斷層。
圖2

圖2 通過(guò)分子動(dòng)力學(xué)構(gòu)建的微型選區(qū)激光熔化(μ-SLM)模型處理Al納米粉末床的最終凝固結(jié)構(gòu)[41]
Fig.2 Finally solidified structures of the aluminum nano-powder bed processed by micro-selective laser melting (μ-SLM) model using molecular dynamics. Ten laser tracks have fused together a total of 453 nano-powders of average diameter 9.67 ?nm in three different layers shown in first layer (a), second layer (b), and third layer (c) (Dark semi-circles outline the contours of the melt-pool boundaries; the grains that span across the three layers are explicitly numbered in Fig.2c; the solidified nanostructure is dominated by epitaxially grown grains. Other important structural features such as equiaxed grains, nano-pores, twin boundaries, and stacking faults are labeled in Fig.2c)[41]
Zeng等[42]通過(guò)對(duì)單軸拉伸實(shí)驗(yàn)進(jìn)行一系列的分子動(dòng)力學(xué)模擬,研究了SLM制備的Al中胞狀結(jié)構(gòu)的力學(xué)變形,分析了柱狀晶的晶型、溫度和晶粒取向?qū)LM Al力學(xué)性能的影響。模擬結(jié)果表明:柱狀晶的SLM Al在不同溫度下的抗拉強(qiáng)度均低于單晶Al,但高于等軸晶Al。隨著溫度的升高,拉伸強(qiáng)度和Young's模量均呈近似線性下降。等軸晶和柱狀晶的變形機(jī)制包括位錯(cuò)滑移、晶界遷移和扭轉(zhuǎn),單晶的變形機(jī)制包括堆積斷層形成和非晶化。最后,研究了柱狀晶取向?qū)αW(xué)性能的影響,發(fā)現(xiàn)Young's模量幾乎與晶粒取向無(wú)關(guān)。柱狀晶取向?qū)鞆?qiáng)度影響較大。因此,合理控制晶粒取向可以提高SLM Al的抗拉強(qiáng)度。
2 介觀尺度計(jì)算/模擬在增材制造鋁合金中的應(yīng)用
2.1 計(jì)算熱力學(xué)
相圖是研究材料成分、工藝、結(jié)構(gòu)與性能之間關(guān)系的重要基礎(chǔ)[43]。由Kaufman和Bernstein[44]創(chuàng)立的CALPHAD方法作為重要的熱力學(xué)建模技術(shù),可用于開(kāi)發(fā)熱力學(xué)數(shù)據(jù)庫(kù)和計(jì)算多組元材料的相平衡關(guān)系。CALPHAD方法的實(shí)質(zhì)是根據(jù)目標(biāo)體系中各相的晶體結(jié)構(gòu)、磁性有序和化學(xué)有序轉(zhuǎn)變等信息,建立起各相的熱力學(xué)模型,并由這些模型構(gòu)筑各相的Gibbs自由能表達(dá)式,最后通過(guò)平衡條件計(jì)算相圖。CALPHAD往往與材料實(shí)驗(yàn)研究相結(jié)合,通過(guò)實(shí)驗(yàn)獲得不同物相影響材料力學(xué)、熱學(xué)、電化學(xué)等性能的基本規(guī)律,然后利用CALPHAD計(jì)算不同體系下的相圖,建立成分-物相-性能之間的關(guān)聯(lián)規(guī)律,從而實(shí)現(xiàn)成分優(yōu)化與性能提升。目前,CALPHAD方法已擴(kuò)展到多元體系的原子移動(dòng)性參數(shù)[45~47]、摩爾體積[48]、熱導(dǎo)率[49]、黏度[50]、Young's模量[51]、界面能[52]等各種材料參數(shù)的建模。計(jì)算熱力學(xué)驅(qū)動(dòng)的增材制造鋁合金設(shè)計(jì)策略流程如圖3[53]所示。基于可靠的熱力學(xué)數(shù)據(jù)庫(kù)和軟件/代碼的計(jì)算熱力學(xué),可以對(duì)影響增材制造鋁合金性能的不同因素進(jìn)行準(zhǔn)確預(yù)測(cè),包括可打印性[54,55]、晶粒細(xì)化[30,56,57]、過(guò)飽和固溶[15]和熱處理工藝[58]等,依此可以通過(guò)多目標(biāo)設(shè)計(jì)策略來(lái)實(shí)現(xiàn)合金成分的設(shè)計(jì)和熱處理機(jī)制的優(yōu)化。
圖3

圖3 計(jì)算熱力學(xué)驅(qū)動(dòng)的增材制造鋁合金設(shè)計(jì)策略流程[53]
Fig.3 Strategic workflow of alloy design approach for additive manufacturing aluminum alloys driven by computational thermodynamics[53] (HSI—hot susceptibility index or crack susceptibility index (CSI), ΔTCTR—craitical temperature range, Qtrue—growth restriction factor for true alloy system)
2.1.1 可打印性
在高強(qiáng)度鋁合金的增材制造過(guò)程中,凝固開(kāi)裂是一種常見(jiàn)的現(xiàn)象。對(duì)于AA2024、AA6061和AA7075等合金,其凝固過(guò)程中柱狀晶粒沿?zé)崽荻确较驍U(kuò)展,并沿晶界收縮,導(dǎo)致裂紋形成[15,59]。在凝固的最后階段,可以沿晶界觀察到凝固裂紋的形成和擴(kuò)展。凝固裂紋發(fā)生在凝固的最后階段,此時(shí)沒(méi)有足夠的流動(dòng)液體來(lái)填充凝固金屬之間的間隙,而凝固金屬所占的體積小于液體[55]。這種類型的裂紋與較大的凝固范圍和凝固末端的熔體的補(bǔ)縮能力有關(guān),常用脆性溫度范圍(brittle temperature range,ΔTBTR)[60]和裂紋敏感性因子(crack susceptibility index,CSI)[55]來(lái)考量熱裂紋敏感性(hot crack susceptibility,HCS)大小。
ΔTBTR[60]表示為:ΔTBTR = TZST - TZDT,其中TZST表示零強(qiáng)度溫度(zero strength temperature,ZST),TZDT表示零延性溫度(zero ductility temperature,ZDT)。當(dāng)溫度為TZST時(shí),力可以垂直于枝晶生長(zhǎng)方向傳遞,相應(yīng)的固體摩爾分?jǐn)?shù)fS一般大于0.65;當(dāng)溫度為TZDT時(shí),晶粒開(kāi)始發(fā)展延展性,TZDT對(duì)應(yīng)于0.98 < fS < 1,如圖4a[60]所示。脆性溫度范圍越寬,表示熱裂紋產(chǎn)生的趨勢(shì)越大。因此,常通過(guò)降低脆性溫度范圍來(lái)緩解熱裂問(wèn)題。基于熱力學(xué)數(shù)據(jù)庫(kù)和熱力學(xué)計(jì)算軟件,采用Scheil-Gulliver模型模擬合金的凝固路徑,可以有效計(jì)算ΔTBTR。Scheil-Gulliver模型中假設(shè)固/液界面處滿足熱力學(xué)平衡,且液相中的擴(kuò)散系數(shù)無(wú)限大,而固相中無(wú)擴(kuò)散[61]。因此,該模型十分適合高冷卻速率的凝固模擬。Dreano等[54]通過(guò)Scheil-Gulliver凝固模擬研究了AlSi10Mg、6061和7075 3種代表性合金的凝固路徑,并計(jì)算ΔTBTR表示合金的熱裂紋趨勢(shì),如圖4b和c[54]所示。計(jì)算結(jié)果表明:在3種合金中,AlSi10Mg合金具有最小的脆性溫度范圍,產(chǎn)生熱裂紋的趨勢(shì)最小。相比于AlSi10Mg,6061和7075合金產(chǎn)生熱裂紋趨勢(shì)很大,這很好地解釋了6xxx和7xxx合金在增材制造過(guò)程中極容易產(chǎn)生熱裂紋的特點(diǎn)。但實(shí)驗(yàn)中6xxx合金比7xxx合金更容易產(chǎn)生長(zhǎng)裂紋[62,63],僅通過(guò)ΔTBTR難以做出準(zhǔn)確的對(duì)比和預(yù)測(cè)。
圖4
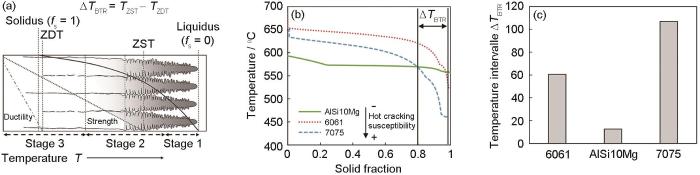
圖4 熱裂中具有特征溫度的凝固組織示意圖[60]及AlSi10Mg、6061、7075鋁合金的Scheil-Gulliver凝固模擬結(jié)果和脆性溫度范圍ΔTBTR的比較[54]
Fig.4 Solidification structure with characteristic temperatures in hot tearing[60] (a), and Scheil-Gulliver solidification simulations (b) and comparison of the calculated brittle temperature range ΔTBTR (ΔTBTR = TZST - TZDT) (c) for AlSi10Mg, 6061, and 7075 aluminum alloys[54] (TZST—zero strength temperature, TZDT—zero ductility temperature)
凝固范圍同樣對(duì)合金的熱裂紋敏感性有影響。寬廣的凝固范圍意味著合金將在半固態(tài)狀態(tài)下保持更長(zhǎng)的時(shí)間。為了理解凝固范圍對(duì)合金HCS的影響,將凝固范圍分成2部分更為實(shí)際:TZST之前的凝固范圍和TZST之后的凝固范圍。在達(dá)到TZST之前,由于固體懸浮在液體中,微觀結(jié)構(gòu)的液體滲透率通常較高[60]。因此,充足的液體補(bǔ)償了凝固收縮應(yīng)變,HCS在這個(gè)階段仍然很低。因此,高的初始凍結(jié)范圍對(duì)合金HCS的影響較小。相反,在凝固末期,寬的凝固范圍(高ΔTBTR)意味著合金在較長(zhǎng)的時(shí)間內(nèi)保持較低的韌性狀態(tài)。在這種狀態(tài)下,由于枝晶臂之間存在一層薄薄的液膜,收縮應(yīng)變不能被有效容納[60]。此外,由于液體分量的迅速減少和毛細(xì)管效應(yīng),任何裂縫可能不會(huì)被液體回填。因此,這個(gè)階段的HCS很高。隨著凝固的進(jìn)行,晶粒發(fā)展出延展性(fS> 0.98),收縮應(yīng)變可以被晶粒間的變形所容納。因此,在TZDT之后,HCS降低。
考慮裂紋通常發(fā)生在凝固的末期,即當(dāng)溫度達(dá)到固相線溫度(此時(shí)fS = 1)時(shí),裂紋通常沿著晶界開(kāi)始并在枝晶間液膜中擴(kuò)展。2015年,Kou[55]提出了3個(gè)預(yù)測(cè)開(kāi)裂的判據(jù):(1) 晶粒在橫向上因拉伸應(yīng)變而相互分離,從而導(dǎo)致開(kāi)裂;(2) 晶粒的橫向生長(zhǎng)將每個(gè)晶粒橋接在一起以抵抗開(kāi)裂;(3) 沿晶界的液體補(bǔ)縮以抵抗開(kāi)裂。如果局部應(yīng)變速率超過(guò)橫向生長(zhǎng)速率和液體進(jìn)料速率的總和,就會(huì)發(fā)生開(kāi)裂。Kou[55]提出了合金在凝固過(guò)程中裂紋敏感性因子CSI:當(dāng)(fS)1/2 = 1時(shí),CSI = |dT / d(fS)1/2|,其中T是溫度,fS此處指半固體中的固體摩爾分?jǐn)?shù)。Kou準(zhǔn)則已成功用于預(yù)測(cè)Al-Mg-Si、Al-Cu-Mg和Al-Cu-Si合金的裂紋敏感性[64],并且得到了實(shí)驗(yàn)驗(yàn)證[65]。如圖5a[55,66]所示,該因子的主要影響因素有2個(gè):(1) 2個(gè)相鄰晶粒相互橋接以抵抗開(kāi)裂的橫向生長(zhǎng)速率;(2) 液體補(bǔ)縮以抵抗開(kāi)裂的晶界液體通道的長(zhǎng)度。較高的CSI表示柱狀晶粒相互橋接并抵抗開(kāi)裂的橫向生長(zhǎng)速率較低,同時(shí)也意味著較長(zhǎng)的液體通道,這使得液體難以及時(shí)補(bǔ)縮,開(kāi)裂的趨勢(shì)較大。此外,Kou[67]研究了不同系列變形鋁合金的裂紋敏感因子,如圖5b[67]所示。通過(guò)Scheil-Gulliver模型模擬了不同系列變形鋁合金的凝固路徑,并計(jì)算相應(yīng)CSI,計(jì)算結(jié)果表明:6061 > 7075 > 2024 > 2014 > 2219,與Dowd[62]和Dudas等[63]的實(shí)驗(yàn)結(jié)果一致。相比于用ΔTBTR考量熱裂敏感性,CSI能對(duì)不同系列變形合金的裂紋敏感性做出更為準(zhǔn)確的預(yù)測(cè)。
圖5

圖5 Kou準(zhǔn)則中裂紋敏感因子示意圖[55,66]及其在變形鋁合金中的預(yù)測(cè)結(jié)果[67]與實(shí)驗(yàn)結(jié)果[62,63]對(duì)比
Fig.5 Schematic diagram of the crack susceptibility index (CSI) in the Kou criterion[55,66] (a) and comparison of the calculated CSI (CSI = |dT / d(fS)1/2|, when (fS)1/2 near 1)[67] and experimental crack susceptibility[62,63] of wrought Al alloys (b) (t is time, R is the characteristic radius of grain)
Li等[58]基于Kou模型,研究了SLM制造過(guò)程中Si對(duì)Al7075合金凝固開(kāi)裂的影響。采用Scheil-Gulliver模型模擬了不同Si添加量時(shí)Al7075變形鋁合金的凝固路徑(如圖6a[58]所示),并計(jì)算了相應(yīng)的CSI。如圖6b[58]所示,隨著Al7075合金中Si含量從0.17% (質(zhì)量分?jǐn)?shù))增加到8%,當(dāng)Si含量增加到2%時(shí),裂紋敏感性開(kāi)始降低;當(dāng)Si含量在3%~4%范圍內(nèi)時(shí),CSI達(dá)到最低水平,并且不隨Si含量的增加而顯著變化;隨后當(dāng)Si含量超過(guò)5%時(shí),CSI略微增加,并且在Si含量為8%時(shí)保持穩(wěn)定。Li等[58]根據(jù)凝固路徑,分析了CSI初始降低的原因在于合金共晶組織的組成中(S + T)相轉(zhuǎn)變?yōu)?Al2Cu + C15 Laves + Q)相。當(dāng)Si含量超過(guò)5%時(shí),CSI的增加是由于共晶組織中Si相的形成。因此,建議使用3%~4%的Si含量以實(shí)現(xiàn)低裂紋敏感性,從而能夠通過(guò)SLM進(jìn)行加工。Li等[58]通過(guò)實(shí)驗(yàn)發(fā)現(xiàn):SLM制備的Al7075合金容易發(fā)生凝固開(kāi)裂,打印態(tài)的Al7075樣品中的裂紋主要沿晶界存在,如圖6c和e[58]所示。開(kāi)裂機(jī)制如圖6g[58]所示。除了基于Kou模型討論的凝固行為外,其他材料和工藝相關(guān)因素也會(huì)影響凝固裂紋敏感性。Al7075合金的高熱膨脹系數(shù)導(dǎo)致凝固過(guò)程中產(chǎn)生較大的凝固收縮和熱收縮,也會(huì)進(jìn)一步導(dǎo)致凝固裂紋的產(chǎn)生。添加3.74%Si后,Al7075合金的裂紋得到消除,如圖6d和f[58]所示。進(jìn)一步對(duì)比SLM制備的Al7075合金和Si改性Al7075合金的微觀結(jié)構(gòu),電子背散射衍射(EBSD)圖的結(jié)果揭示了晶粒形態(tài)和尺寸方面的顯著差異。觀察到在Si改性合金中晶粒被細(xì)化并且外延晶粒生長(zhǎng)被顯著抑制。此外,由于在熔池邊界處存在等軸晶粒和在熔池內(nèi)存在柱狀晶粒,在Si改性Al7075合金中可以識(shí)別出熔池。而添加Si的晶粒細(xì)化主要?dú)w因于2個(gè)因素:即,共晶形成溶質(zhì)對(duì)晶粒生長(zhǎng)的限制和先前沉積層上的異質(zhì)形核。下文將進(jìn)一步深入分析引起晶粒細(xì)化的這2個(gè)因素。
圖6

圖6 Si改性Al7075合金凝固路徑、裂紋敏感性計(jì)算結(jié)果及SLM工藝制備合金的微觀組織形貌[58]
Fig.6 Calculational results of Scheil solidification and CSI of Si-modified Al7075 alloys, and grain morphologies of SLM processed Al7075 alloy (Al-5.10Zn-2.67Mg-1.55Cu, mass fraction, %) without and with Si[58]
(a) T vs (fS)1/2 curves of the Al7075 alloys with 0.17% to 8% Si additions (mass fraction), the dashed vertical line indicates (fS)1/2 = 0.99
(b) variation of crack susceptibility of Al7075 alloys as a function of Si additions (Insets show the defect morphologies of Si-modified SLM processed Al7075 alloy)
(c-f) grain morphologies of SLM processed Al7075 with solidification cracks (c, e), and crack-free Si-modified Al7075 alloy (Al7075-3.74Si%) processed by SLM (d, f) (BD—building direction)
(g, h) schematics of epitaxial growth of the Al7075 alloy (g) and the solidification cracking mitigation mechanism in the Si-modified Al7075 (h) (Tl is the liquidus temperature, Ts or Ts1 is the terminal temperature of solidification, Ts2 is the temperature of full columnar grains zone, ΔT is solidification temperature range (ΔT = Tl - Ts), //ΔGmax represents that the growth direction of columnar grains is preferentially oriented parallel to the direction of the maximum temperature gradient G)
2.1.2 細(xì)化晶粒
細(xì)化晶粒不僅能提高合金的強(qiáng)度和韌性,還能通過(guò)調(diào)整合金在凝固過(guò)程中的枝晶形貌和晶間殘余液相的分布來(lái)降低合金的熱裂傾向[68]。目前,關(guān)于晶粒細(xì)化的理論模型研究,包括:(1) 用生長(zhǎng)限制因子來(lái)判斷溶質(zhì)元素對(duì)晶粒生長(zhǎng)的抑制作用[56,57];(2) 用自由生長(zhǎng)模型預(yù)估形核顆粒尺寸及所需的臨界形核過(guò)冷度[69];(3) 相互依存理論,綜合考慮了異質(zhì)形核及溶質(zhì)元素的生長(zhǎng)限制效應(yīng)對(duì)晶粒尺寸的影響[70]。
溶質(zhì)效應(yīng)已被證明對(duì)有效的晶粒細(xì)化至關(guān)重要[71]。在合金的凝固過(guò)程中,固/液界面前沿會(huì)因溶質(zhì)偏析而產(chǎn)生成分過(guò)冷。當(dāng)溶質(zhì)偏析所提供的過(guò)冷度(ΔTC)大于形核所需要的臨界過(guò)冷度(ΔTn)時(shí),可以通過(guò)促進(jìn)新晶粒的形核以抑制原有晶粒的繼續(xù)生長(zhǎng)。為了衡量不同溶質(zhì)對(duì)晶粒細(xì)化的影響[57,72],定義生長(zhǎng)限制因子Q (growth restriction factor,GRF):
式中,i為不同的溶質(zhì)元素,mi 是液相線斜率,ci 是溶質(zhì)元素濃度,ki 是用于描述凝固過(guò)程中溶質(zhì)分配的平衡分配系數(shù)k = cs / cl,其中cs和cl分別是固/液界面處固相和液相的平衡溶質(zhì)濃度。隨著熱力學(xué)模型的發(fā)展,目前可以很好地評(píng)估和量化成分過(guò)冷度。目前實(shí)踐中最有說(shuō)服力的Q計(jì)算方法是Quested等[73]提出的采用成分過(guò)冷的初始速率來(lái)表示真實(shí)合金體系的生長(zhǎng)限制因子Qture:
式中,ΔTcs是成分過(guò)冷度。Men和Fan[74]提出了一種能準(zhǔn)確描述晶粒尺寸
式中,K為一個(gè)與合金成分和凝固條件相關(guān)的常數(shù)。Kotadia等[6]和Qi等[75]總結(jié)了常見(jiàn)Al-X二元系中生長(zhǎng)限制因子與初晶Al晶粒尺寸間的關(guān)系,Qtrue越大,表明該溶質(zhì)在固/液界面前沿產(chǎn)生成分過(guò)冷的能力越大,晶粒細(xì)化的效果越好。Schmid-Fetzer和Kozlov[76]進(jìn)一步證明Qtrue的計(jì)算同樣適用于多組元體系,包括初生相為金屬間化合物或陶瓷相的情況,并在含有細(xì)化劑TiB2和金屬間化合物TiAl3和τ1相的Al-Si-Ti-B四元系中進(jìn)行了驗(yàn)證,最終推薦采用Scheil-Gulliver凝固模擬結(jié)果計(jì)算多組元的Qtrue。
除了元素的成分過(guò)冷效應(yīng)外,異質(zhì)形核也對(duì)鋁合金晶粒細(xì)化非常關(guān)鍵。凝固理論認(rèn)為:顆粒的異質(zhì)形核效力與顆粒/基體界面的界面能緊密相關(guān)。顆粒與基體之間的晶格錯(cuò)配度越小,則兩相界面能越低,顆粒的異質(zhì)形核效力越強(qiáng)[77]。目前,鋁合金應(yīng)用中常見(jiàn)的有效異質(zhì)形核劑主要包括:(1) 通過(guò)添加元素Ti、Zr、Sc等,原位生成彌散細(xì)小的初晶Al3X金屬間化合物,作為(Al)相的異質(zhì)形核質(zhì)點(diǎn);(2) 原位或離位添加的陶瓷相顆粒,如硼化物(TiB2、LaB6、CaB6)、碳化物(TiC、SiC)、氮化物(TiN、Si3N4、BN、AlN)、ZrH2等[26]。
Al3X (X = Ti、Zr、Sc)相通常會(huì)與液相發(fā)生包晶反應(yīng)生成(Al)。Nie等[23]根據(jù)Al-Zr相圖,研究了0、0.6%、1%、1.5%、2%和2.5% (質(zhì)量分?jǐn)?shù)) Zr的添加對(duì)SLM工藝下Al-4.24Cu-1.97Mg-0.56Mn (質(zhì)量分?jǐn)?shù),%)合金成形性、微結(jié)構(gòu)和力學(xué)性能的影響。結(jié)果發(fā)現(xiàn):Zr添加會(huì)生成初晶相Al3Zr,能極大地細(xì)化(Al)晶粒,將柱狀晶轉(zhuǎn)變?yōu)榧?xì)小的等軸晶,消除熱裂紋。隨著Zr的添加,晶粒尺寸得到不斷細(xì)化。根據(jù)力學(xué)性能和熱導(dǎo)率測(cè)量結(jié)果來(lái)確定,當(dāng)Zr的添加量為2%,該合金具有最佳的力學(xué)性能和最低的熱導(dǎo)率。Li等[24]采用計(jì)算熱力學(xué)方法研究了Mn、Cu、Mg添加對(duì)Al-Cu-Mg-Mn體系的熱裂敏感性的影響,并篩選出具有較低裂紋敏感性的Al-4.40Cu-1.51Mg-1.15Mn (質(zhì)量分?jǐn)?shù),%)合金,但其計(jì)算結(jié)果顯示Zr的添加對(duì)其熱裂敏感性因子影響不大。Li等[24]通過(guò)SLM工藝制備了添加不同含量Zr (1%、1.98%、3.72%,質(zhì)量分?jǐn)?shù))的Al-4.40Cu-1.51Mg-1.15Mn合金,結(jié)果表明:Zr的添加會(huì)生成Al3Zr而不斷細(xì)化晶粒,當(dāng)Zr的添加量在1%~1.98%時(shí),微結(jié)構(gòu)中柱狀晶和等軸晶共存;當(dāng)添加量為3.72%時(shí),微結(jié)構(gòu)完全由等軸晶構(gòu)成,且具有最佳的強(qiáng)度和塑性。然而,目前對(duì)于不同體系合金中最佳X (X = Ti、Zr、Sc)元素等添加量仍需要通過(guò)實(shí)驗(yàn)來(lái)確定,缺少理論計(jì)算輔助設(shè)計(jì)。
最近,本文的2個(gè)研究小組合作,采用計(jì)算熱力學(xué)方法,通過(guò)相圖、裂紋敏感性和生長(zhǎng)抑制因子研究了Ti對(duì)Al-2.25Cu-1.8Mg (質(zhì)量分?jǐn)?shù),%)合金的影響,綜合考慮了Al3Ti的原位生成、Ti對(duì)裂紋敏感性影響和Ti對(duì)晶粒生長(zhǎng)的抑制作用,開(kāi)發(fā)了適用于增材制造的新型抗裂紋、高性能鋁合金[21]。如圖7a~c[21]所示,計(jì)算結(jié)果表明:Ti的添加會(huì)形成Al3Ti相,并作為初晶相,隨后發(fā)生包晶反應(yīng):Liquid + Al3Ti→(Al)。Ti的添加對(duì)凝固路徑的末端影響不大,因此對(duì)裂紋敏感性影響不大,但Ti的加入能顯著提高Qture。添加1.5%Ti (質(zhì)量分?jǐn)?shù))的Al-2.25Cu-1.8Mg合金的平均晶粒尺寸僅為不添加Ti的1/3,能極大地細(xì)化晶粒;當(dāng)Ti的添加量超過(guò)1.5%后,細(xì)化效果提升變緩。因此,最佳的Ti添加量設(shè)計(jì)為1.5%。圖7d[21]為Al-Cu-Mg合金的裂紋機(jī)制示意圖。通過(guò)實(shí)驗(yàn)方法,證實(shí)了Ti對(duì)SLM工藝制備的Al-Cu-Mg合金零件裂紋形成的抑制作用。如圖7e~h[21]所示,Ti的加入有效地促進(jìn)了Al-Cu-Mg合金的晶粒細(xì)化和柱狀晶向等軸晶的轉(zhuǎn)變。與柱狀晶粒相比,等軸晶粒具有以下優(yōu)勢(shì):(1) 更容易旋轉(zhuǎn)以適應(yīng)應(yīng)變,從而抑制了相鄰晶粒之間的相干性;(2) 細(xì)等軸結(jié)構(gòu)中每單位體積內(nèi)更多的界面也能夠更好地消除熱應(yīng)力;(3) 等軸細(xì)晶粒還可以改善快速凝固過(guò)程中的液相流動(dòng),從而在很大程度上避免形成熱撕裂裂紋;(4) 與粗大柱狀晶粒的平坦邊界相比,在細(xì)等軸微結(jié)構(gòu)中提供了更曲折的裂紋路徑,從而抑制了裂紋擴(kuò)展。因此,與Al-Cu-Mg合金的粗大柱狀顯微組織相比,Ti添加形成的細(xì)等軸組織顯著降低了產(chǎn)生裂紋的可能性,且當(dāng)Ti的添加量為1.5%時(shí),力學(xué)性能達(dá)到最佳。
圖7
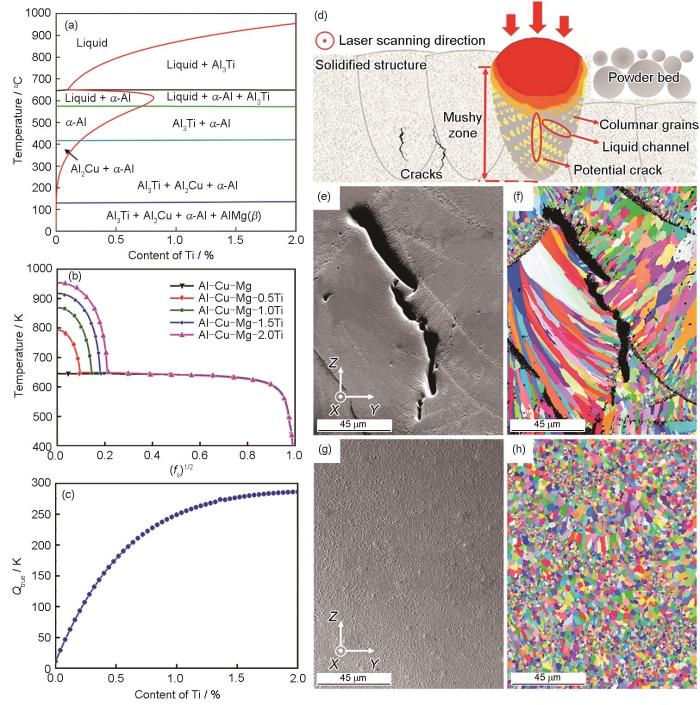
圖7 一種用于SLM的新型無(wú)裂紋Ti改性Al-Cu-Mg合金設(shè)計(jì)流程[21]
Fig.7 A novel crack-free Ti-modified Al-Cu-Mg alloy design flow for SLM[21]
(a) vertical section of Al-2.25Cu-1.8Mg-xTi alloys (mass fraction, %)
(b) Tvs (fS)1/2 curves of Al-Cu-Mg-xTi alloys with Ti contents ranging from 0 to 2%
(c) calculated Qtrue values in Ti/Al-Cu-Mg alloys for constrained L→α-Al solidification with Ti contents ranging from 0 to 2% (Metastable solidification conditions are used at higher values of Ti content to suppress the formation of intermetallic phases)
(d) schematic of cracking mechanism in the Al-Cu-Mg alloy
(e, f) SEM image (e) and inverse pole figure (IPF) (f) showing the microstructure in the cracked zone of Al-Cu-Mg alloy
(g, h) SEM image (g) and IPF (h) of Ti/Al-Cu-Mg alloy consisting of fine equiaxed grains without cracks
2.1.3 固溶強(qiáng)化
金屬增材制造過(guò)程溫度梯度大,冷卻速率極高(103~107 K/s),極容易形成過(guò)飽和固溶體[78]。表1[79]列出了平衡條件和快速凝固條件下(約106 K/s)的二元鋁合金中溶質(zhì)的溶解度極限。過(guò)飽和溶質(zhì)原子通過(guò)扭曲晶格產(chǎn)生相當(dāng)大的彈性應(yīng)力場(chǎng),與傳統(tǒng)方法制造的合金相比,產(chǎn)生了相對(duì)更強(qiáng)的位錯(cuò)運(yùn)動(dòng)屏障,并實(shí)現(xiàn)了相應(yīng)的固溶強(qiáng)化效果。例如,SLM制備的AlSi10Mg合金具有比傳統(tǒng)鑄造合金更高的強(qiáng)度,主要貢獻(xiàn)來(lái)自于快速凝固條件下形成的細(xì)晶帶來(lái)的細(xì)晶強(qiáng)化和α-Al相過(guò)飽和固溶體的固溶強(qiáng)化[10,80]。Cauwenbergh等[10]通過(guò)實(shí)驗(yàn)研究了SLM制備的AlSi10Mg微結(jié)構(gòu),通過(guò)掃描透射電鏡-能譜儀(STEM-EDX)測(cè)定了α-Al相和共晶組織中Si和Mg的溶度。結(jié)果表明:在SLM工藝下(冷速約為105 K/s),α-Al相中Si的濃度為2.7% (質(zhì)量分?jǐn)?shù)),明顯高于平衡凝固(1.0%~1.6%)和Scheil-Gulliver凝固模擬(1.2%~1.5%)計(jì)算中Si在α-Al相的濃度。受高冷速的影響,Si元素的分配系數(shù)k (0.27)強(qiáng)烈偏離了Al-Si合金中的平衡分配系數(shù)ke (0.13)。
表1 平衡和快速凝固條件(約106 K/s)下二元鋁合金中溶質(zhì)的溶解度極限值[79] (atomic fraction / %)
Table 1
Solute |
Element |
Equilibrium | Maximum extended solubility | |
---|---|---|---|---|
Maximum solubility | Ce or Cp | |||
Eutectic | Zn | 66.4 | 88.5 | 38-43.5 |
Ag | 23.8 | 37.0 | 25-40 | |
Mg | 16.3 | 36.4 | 36.8-40 | |
Cu | 2.5 | 17.5 | 17-18 | |
Si | 1.6 | 12.0 | 10-16 | |
Mn | 0.9 | 0.95 | 6-10 | |
Fe | ~0.02 | 0.9 | 4-6 | |
Co | < 0.01 | 0.45 | 0.5-5 | |
Ni | ~0.02 | 2.8 | 1.2-7.7 | |
Ce | ~0.01 | 2.6 | 1.9 | |
Peritectic | Ti | 0.6 | 0.06 | 0.2-2 |
Cr | 0.4 | 0.19 | 5-7 | |
V | 0.25 | 0.05 | 1.4-2 | |
Zr | 0.09 | 0.03 | 1.2-1.5 | |
Mo | 0.07 | 0.03 | 1.0-1.5 | |
W | 0.02 | 0.01 | 0.9-1.9 |
如前所述,Scheil-Gulliver模型[61]廣泛用于討論增材制造合金的凝固路徑,以及計(jì)算元素添加對(duì)合金裂紋敏感性和對(duì)晶粒的生長(zhǎng)限制作用。Scheil-Gulliver假設(shè)在固/液界面存在熱力學(xué)平衡,液相中擴(kuò)散無(wú)限快和在固相無(wú)擴(kuò)散:
式中,CL代表液相的成分。在金屬增材制造過(guò)程中,存在溫度梯度大、冷卻速率極高等特點(diǎn),金屬凝固時(shí)固/液界面推移速率大幅提高,導(dǎo)致固相和液相內(nèi)部的溶質(zhì)來(lái)不及充分?jǐn)U散,界面上的溶質(zhì)遷移極大地偏離平衡位置,使更多的溶質(zhì)溶入固相,出現(xiàn)嚴(yán)重的溶質(zhì)截留現(xiàn)象[81]。該現(xiàn)象會(huì)導(dǎo)致固/液界面的分配系數(shù)k偏離ke。Aziz等[82~84]提出了連續(xù)生長(zhǎng)模型(continuous growth model,CGM),推導(dǎo)了隨凝固速率V變化的偏析系數(shù)k(V):
式中,
2.1.4 熱處理工藝設(shè)計(jì)
對(duì)于傳統(tǒng)的鑄造合金和變形合金,熱處理能改善微觀組織的不均勻性,進(jìn)一步提高合金的力學(xué)性能。可熱處理的鋁合金體系包括:Al-Si(-Mg)、Al-Cu、Al-Zn-Mg、Al-Mg-Sc(-Zr)等[86]。傳統(tǒng)的熱處理工藝包括:固溶自然時(shí)效處理(T4)、穩(wěn)定化處理(T5)、固溶人工時(shí)效處理(T6)等,其中,固溶處理的主要目的是使材料中的第二相或其他可溶成分(Mg、Cu、Si等)充分溶解到Al基體,形成過(guò)飽和固溶體。時(shí)效處理的主要目的是使第二相粒子從過(guò)飽和固溶體中析出,彌散分布在α-Al晶粒內(nèi)部和晶界處,從而產(chǎn)生強(qiáng)化作用(析出強(qiáng)化),進(jìn)一步提高合金的力學(xué)性能。常用熱力學(xué)性質(zhì)圖來(lái)優(yōu)化鋁合金的熱處理工藝[53,87]。
由于3D打印存在內(nèi)稟熱循環(huán)特點(diǎn),對(duì)制造具有均勻性能的金屬構(gòu)件提出了嚴(yán)峻挑戰(zhàn)。例如,SLM成形具有逐層疊加的特點(diǎn),通常會(huì)導(dǎo)致已經(jīng)熔覆的金屬材料經(jīng)歷反復(fù)的熱循環(huán)過(guò)程,類似在打印過(guò)程進(jìn)行了“原位熱處理”,造成制造出的構(gòu)件具有自上而下的顯微組織和性能的不均勻性,從而可能導(dǎo)致部件在服役過(guò)程出現(xiàn)難以預(yù)測(cè)的失效。為此,許多研究者[19,80,86]開(kāi)展了熱處理對(duì)增材制造鋁合金微結(jié)構(gòu)和性能的影響研究。
Li等[11]研究了固溶熱處理對(duì)SLM制備的Al-12Si合金中微結(jié)構(gòu)和元素的影響。結(jié)果表明:固溶處理導(dǎo)致明顯的Si球化。在打印態(tài)下,Al基體中的Si含量為7% (質(zhì)量分?jǐn)?shù)),遠(yuǎn)遠(yuǎn)超過(guò)平衡狀態(tài)下的Si在Al中的溶解度極限(1.6%)。然而,在固溶處理后,Al基體中的Si含量在15 min后迅速下降至2%,然后在30 min后降至1.6%的平衡濃度。且在非常短的固溶處理時(shí)間(15 min)后,過(guò)飽和的Si從Al中沉淀出來(lái),形成微小的共晶硅顆粒,合金的強(qiáng)度也降到最低,延伸率達(dá)到最高(25%)[11]。更長(zhǎng)的固溶處理時(shí)間對(duì)Al中的Si含量沒(méi)有影響,仍為1.6%,且對(duì)應(yīng)的性能基本保持不變。
Takata等[80]比較了SLM制備的各種Al-Si基合金與傳統(tǒng)鑄造合金的拉伸強(qiáng)度。結(jié)果表明:對(duì)SLM制備的Al-Si合金采用傳統(tǒng)的熱處理工藝T6,其強(qiáng)度降到和鑄造合金同水平,說(shuō)明SLM工藝的優(yōu)勢(shì)完全消除。主要原因在于傳統(tǒng)的固溶處理消除了合金在快速凝固條件下形成的超過(guò)飽和固溶體,導(dǎo)致強(qiáng)度大幅下降。因此,考慮到3D打印工藝制備會(huì)形成超過(guò)飽和固溶體的特點(diǎn),可選擇對(duì)打印態(tài)合金采用直接時(shí)效處理。許多研究者[10,19]開(kāi)展了直接時(shí)效對(duì)打印態(tài)合金的影響研究,結(jié)果表明:對(duì)打印態(tài)合金直接進(jìn)行時(shí)效處理,合金在析出第二相的同時(shí),Al基體還保持了一定的過(guò)飽和度,能最大程度地提升合金的強(qiáng)度,且對(duì)塑性的影響較小。
2.2 相場(chǎng)模擬
相場(chǎng)法是以Ginsberg-Landau相變理論為基礎(chǔ),以序參量(order parameter)來(lái)描述相變時(shí)對(duì)稱破缺(symmetry breaking),以微分方程描述擴(kuò)散、有序化勢(shì)和熱力學(xué)驅(qū)動(dòng)的綜合作用[88]。相場(chǎng)變量Φ反映了系統(tǒng)內(nèi)部的有序化程度,其值在固相中為1,表示體系內(nèi)部高有序化狀態(tài);在液相中為0或-1,表示體系內(nèi)部低有序化狀態(tài)。金屬凝固過(guò)程中相變意味著體系內(nèi)部有序化程度的改變。
增材制造過(guò)程中溫度梯度高、冷卻速率大,工件經(jīng)歷快速的加熱冷卻循環(huán),極度偏離平衡狀態(tài),微觀組織與傳統(tǒng)制造不同。由于這一特點(diǎn),在生成具有強(qiáng)取向性柱狀晶的同時(shí),會(huì)產(chǎn)生細(xì)小的、具有過(guò)飽和固溶的等軸晶,有利于減少工件裂紋的形成,提高工件的性能[89]。因此,對(duì)增材制造微結(jié)構(gòu)的演變進(jìn)行研究對(duì)提高材料的性能有重要的意義。相場(chǎng)法避免了對(duì)復(fù)雜界面位置進(jìn)行追蹤,能夠?qū)崿F(xiàn)微結(jié)構(gòu)的二維和三維模擬,是微結(jié)構(gòu)模擬的有效工具。此外,相場(chǎng)法的另一個(gè)優(yōu)勢(shì)在于,它可以將其他外場(chǎng)(如流場(chǎng)、溫度場(chǎng)、溶質(zhì)場(chǎng)等)與相場(chǎng)方程耦合,從而將微觀尺度場(chǎng)與宏觀物理場(chǎng)結(jié)合,更加真實(shí)地描述工程實(shí)際問(wèn)題,使微觀組織模擬更加準(zhǔn)確可靠。目前,應(yīng)用較多的是WBM模型[90]、KKS模型[91]、多相場(chǎng)模型[92],以及由Steinbach和Zhang[93,94]發(fā)展的有限界面耗散相場(chǎng)模型。主要用于研究增材制造中孔隙率和密度[95]、溫度場(chǎng)演化[96]、增強(qiáng)顆粒對(duì)晶粒演化的影響[97]、微結(jié)構(gòu)演變[98]等。
考慮到金屬增材制造過(guò)程中存在溫度梯度大、冷卻速率極高等特點(diǎn),熔池微結(jié)構(gòu)通常由沿熔池溫度梯度方向的粗大柱狀晶和熔池芯部的等軸晶構(gòu)成。定量相場(chǎng)模擬的目的是重現(xiàn)凝固過(guò)程中微觀組織演化,用于分析不同凝固條件(溫度梯度G,凝固速率V,冷卻速率CR)對(duì)微觀組織的影響,掌握凝固條件對(duì)微觀組織的影響規(guī)律,實(shí)現(xiàn)對(duì)熔池不同位置晶粒形態(tài)和取向的控制。有限界面耗散的多相場(chǎng)模型[93,94],能夠有效地描述極端非平衡條件下(快速凝固過(guò)程)的溶質(zhì)截留效應(yīng),被認(rèn)為是最適合描述增材制造制備過(guò)程的相場(chǎng)模型[99]。Karayagiz等[100]將有限界面耗散模型應(yīng)用于探究激光粉床熔覆打印Ni-Nb合金過(guò)程中的微結(jié)構(gòu)演變研究,并給出了不同溫度梯度和冷卻速率下的凝固圖譜。O'Toole等[101]采用有限界面耗散模型,以動(dòng)力學(xué)為基礎(chǔ)考慮跨相界面的擴(kuò)散,取代了平衡分配假設(shè),證實(shí)了利用擴(kuò)散動(dòng)力學(xué)結(jié)合CALPHAD預(yù)測(cè)增材制造條件下AlSi10Mg合金體系凍結(jié)微觀組織的能力。本課題組[102]將該模型用于研究三元Al-Cu-Li體系在快速凝固條件下的溶質(zhì)分布,并構(gòu)建三元Al-Cu-Li體系的動(dòng)力學(xué)相圖。圖8a[102]展示了通過(guò)該模型計(jì)算的Al-Cu體系中3種界面移動(dòng)速率(即:凝固速率)的相場(chǎng)模擬穩(wěn)態(tài)濃度曲線。圖8b[102]展示了Al-1.1%Cu (原子分?jǐn)?shù))體系中相場(chǎng)模擬的溶質(zhì)偏析系數(shù)和凝固溫度與界面移動(dòng)速率的關(guān)系,計(jì)算結(jié)果再現(xiàn)了實(shí)驗(yàn)測(cè)量的溶質(zhì)偏析系數(shù)。通過(guò)相場(chǎng)模擬可以很好地描述Al-Cu、Al-Li、Al-Cu-Li快速凝固過(guò)程中的溶質(zhì)截留現(xiàn)象,并且再現(xiàn)了實(shí)驗(yàn)測(cè)量或理論模型中獲得的結(jié)果。如圖8c[102]所示,根據(jù)預(yù)測(cè)的動(dòng)力學(xué)相圖發(fā)現(xiàn),隨著界面移動(dòng)速率的增加,液相線和固相線之間的間隙逐漸減小,說(shuō)明了溶質(zhì)截留效應(yīng)和無(wú)擴(kuò)散凝固的趨勢(shì)。由于進(jìn)行實(shí)驗(yàn)測(cè)量極其困難,因此通常不存在不同凝固速率下的動(dòng)力學(xué)相圖,但通過(guò)相場(chǎng)模擬計(jì)算得到的動(dòng)力學(xué)相圖卻對(duì)于指導(dǎo)新型合金制備具有重要意義。然而,目前關(guān)于相場(chǎng)模擬在增材制造鋁合金中的應(yīng)用仍較少。
圖8

圖8 有限界面耗散模型用于研究快速凝固條件下Al-Cu體系的溶質(zhì)截留現(xiàn)象及動(dòng)力學(xué)相圖[102]
Fig.8 Solute trapping and kinetic phase diagram of the Al-Cu system under rapid solidification conditions using phase-field model with finite interface dissipation[102]
(a) phase-field simulated steady-state concentration profiles with three different interface moving velocities (or solidification rate) V in Al-Cu system (The red dash line denotes the phase field, the bule solid lines denote the overall concentrations, while the dotted lines denote the liquid concentrations)
(b) phase-field simulated solute segregation coefficient and solidification temperature as a function of interface velocity (or solidification rate) in Al-1.1%Cu (atomic fraction) alloy
(c) model-predicted kinetic phase diagrams at different interface velocities (or solidification rate) due to the 1-D phase-field simulation using the time-elimination relaxation scheme of the Al-Cu system
與增材制造過(guò)程類似的激光焊接過(guò)程同樣存在快速凝固行為。Jiang等[98]建立了一個(gè)多物理場(chǎng)多尺度模型研究5083鋁合金激光焊接過(guò)程中的復(fù)雜凝固過(guò)程。該模型結(jié)合了傳熱傳質(zhì)的宏觀模型、多晶合金凝固的微觀相場(chǎng)模型和異質(zhì)形核的連續(xù)Gaussian形核分布模型,從熔池剖面、晶粒結(jié)構(gòu)和枝晶結(jié)構(gòu)3個(gè)方面與實(shí)驗(yàn)結(jié)果進(jìn)行對(duì)比驗(yàn)證,取得了良好的一致性。通過(guò)分析溫度場(chǎng)、濃度場(chǎng)和成分過(guò)冷場(chǎng)的演變,研究了激光熔池中從平面生長(zhǎng)到細(xì)胞生長(zhǎng)、柱狀枝晶生長(zhǎng)和等軸枝晶生長(zhǎng)的整個(gè)凝固過(guò)程,如圖9[98]所示。特別是,其定量預(yù)測(cè)了凝固前沿前液體中的成分過(guò)冷分布。論證了成分過(guò)冷度分布與等軸晶粒的形核/生長(zhǎng)之間的關(guān)系,揭示了激光焊縫中不同位置的柱狀晶粒和等軸晶粒的選擇性生長(zhǎng)行為。因此,將微/介觀的相場(chǎng)模型與其他宏觀物理模型結(jié)合來(lái)完整描述復(fù)雜的快速凝固行為將是相場(chǎng)模擬的主流發(fā)展方向之一。
圖9

圖9 激光熔池凝固過(guò)程中晶粒結(jié)構(gòu)隨時(shí)間的演變[98]
Fig.9 Evolutions of the grain structure during solidification process in the laser molten pool with time[98]
(a) t = 0 ms (b) t = 25.0 ms (c) t = 50.0 ms
3 宏觀尺度模擬在增材制造鋁合金中的應(yīng)用
在激光與原材料相互作用過(guò)程中,材料經(jīng)歷了快速熔化與凝固、能量的傳輸與散射、金屬熔體流動(dòng)及相變等一系列復(fù)雜的物理化學(xué)過(guò)程,應(yīng)力和組織演變十分復(fù)雜。增材制造成形各類材料時(shí),可通過(guò)調(diào)整工藝參數(shù)來(lái)調(diào)控熔池的熱力學(xué)和動(dòng)力學(xué)行為,從而優(yōu)化工藝窗口、調(diào)控顯微組織、控制殘余應(yīng)力。反之,若要揭示增材制造構(gòu)件的組織性能演化規(guī)律,則必須明晰成形過(guò)程中零件的熱歷史和熱行為。然而,增材制造熔池尺度較小、冶金行為變化復(fù)雜且迅速,現(xiàn)有的高速攝像等在線監(jiān)控方法難以實(shí)現(xiàn)增材制造過(guò)程的細(xì)致觀察與準(zhǔn)確測(cè)量。有限元等數(shù)值模擬可以對(duì)增材制造中的熱作用[103]、成形控制[32]、組織演變[104]、殘余應(yīng)力分布[105]和力學(xué)行為[106]等進(jìn)行預(yù)測(cè)和研究,具有低成本、高效率、理論性強(qiáng)及易于指導(dǎo)工藝優(yōu)化等特點(diǎn)。
華中科技大學(xué)宋波團(tuán)隊(duì)聯(lián)合愛(ài)爾蘭圣三一大學(xué)殷碩教授團(tuán)隊(duì),通過(guò)熔池溫度場(chǎng)、應(yīng)力場(chǎng)和速度場(chǎng)的數(shù)值模擬與微觀組織表征,揭示了2xxx變形鋁合金SLM過(guò)程中熔池冶金行為的演變機(jī)制以及球化、孔隙和裂紋等冶金缺陷的形成機(jī)理[32]。最后,從材料設(shè)計(jì)和工藝創(chuàng)新的角度討論了冶金缺陷的抑制方法,為理解SLM成形高強(qiáng)鋁合金的致密化行為,實(shí)現(xiàn)粉末材料與工藝的有效設(shè)計(jì)提供了重要參考。
(1) 從熔池溫度場(chǎng)、流動(dòng)場(chǎng)角度揭示了SLM成形變形鋁合金的孔隙形成機(jī)制。激光能量密度是決定樣品孔隙率的關(guān)鍵因素。熔池溫度場(chǎng)、流動(dòng)場(chǎng)模擬結(jié)果顯示:能量密度過(guò)低時(shí),金屬粉末熔化不充分,掃描軌跡不連續(xù)或不穩(wěn)定;能量密度過(guò)高時(shí),過(guò)高的流速導(dǎo)致大量熔體飛濺,熔池狀態(tài)不穩(wěn)定,造成過(guò)度球化與過(guò)燒,且熔池表面湍流卷入氣體,最終形成孔隙[32]。
(2) 從熔池應(yīng)力場(chǎng)、晶粒組織結(jié)構(gòu)角度揭示了SLM成形變形鋁合金的裂紋形成機(jī)制。SLM成形變形鋁合金時(shí),熔池邊緣與熱影響區(qū)形成應(yīng)力集中,誘導(dǎo)的應(yīng)力超過(guò)了變形鋁合金的強(qiáng)度極限,造成基體撕裂形成裂紋。此外SLM熔池內(nèi)極高的溫度梯度導(dǎo)致粗大柱狀晶組織的形成,柱狀晶間的殘余液膜在凝固末期發(fā)生凝固收縮或熱收縮,在晶界處形成大量硬脆屬性的網(wǎng)狀析出物,引發(fā)裂紋,如圖10[32]所示。
圖10

圖10 Al-Cu-Mg合金裂紋形成機(jī)理[32]
Fig.10 Crack formation mechanism of Al-Cu-Mg alloy[32]
(a) simulated stress distribution of molten pool
(b) grain morphology in experimental molten pool
(c) schematic of solidification process and crack formation
4 機(jī)器學(xué)習(xí)在增材制造鋁合金中的應(yīng)用
機(jī)器學(xué)習(xí)是人工智能和計(jì)算科學(xué)的分支。基于統(tǒng)計(jì)學(xué)方法,機(jī)器學(xué)習(xí)使計(jì)算機(jī)能夠識(shí)別數(shù)據(jù)中的模式,并通過(guò)分類或回歸在輸入和目標(biāo)之間建立非參數(shù)但定量的關(guān)系,針對(duì)目標(biāo)屬性的閾值進(jìn)行搜索、篩選和優(yōu)化來(lái)擴(kuò)展?jié)撛诘臎Q策空間[107]。機(jī)器學(xué)習(xí)不需要基于現(xiàn)象學(xué)理解來(lái)顯式求解復(fù)雜方程,其預(yù)測(cè)精度主要取決于數(shù)據(jù)質(zhì)量和算法復(fù)雜度,因此能夠?qū)崿F(xiàn)對(duì)復(fù)雜問(wèn)題的快速求解。
金屬增材制造過(guò)程需要對(duì)大量參數(shù)進(jìn)行設(shè)置,包括熱源的功率和速率、掃描模式、樣品幾何形狀等。參數(shù)的選擇會(huì)影響凝固過(guò)程的溫度梯度、冷卻速率,進(jìn)而影響熔池的形貌以及材料微觀結(jié)構(gòu),最終導(dǎo)致了材料內(nèi)部缺陷和宏觀性能的演變[108]。傳統(tǒng)方法通過(guò)對(duì)大范圍工藝參數(shù)進(jìn)行試錯(cuò)來(lái)制造高質(zhì)量的零件,時(shí)間和經(jīng)濟(jì)成本高,且難以針對(duì)目標(biāo)性能對(duì)工藝進(jìn)行設(shè)計(jì)。而機(jī)器學(xué)習(xí)則可以通過(guò)分析大量實(shí)驗(yàn)數(shù)據(jù),對(duì)影響成形質(zhì)量的工藝參數(shù)和過(guò)程參數(shù)進(jìn)行識(shí)別、分類,建立不同合金體系由工藝到性能的定量關(guān)系[89]。不僅如此,隨著流程智能化和算法精度的提升,機(jī)器學(xué)習(xí)技術(shù)逐步能夠在過(guò)程規(guī)劃[109]、參數(shù)優(yōu)化[110]、微結(jié)構(gòu)調(diào)控[111]和缺陷消除[33]等金屬增材制造工藝全流程優(yōu)化中提供可靠支持。
Caiazzo和Caggiano[112]基于圖像識(shí)別和人工神經(jīng)網(wǎng)絡(luò),對(duì)2024 Al激光金屬沉積過(guò)程工藝參數(shù)與沉積金屬跡線的輸出幾何參數(shù)之間的相關(guān)性進(jìn)行了研究。結(jié)果表明,基于神經(jīng)網(wǎng)絡(luò)的機(jī)器學(xué)習(xí)方法能夠準(zhǔn)確估計(jì)獲取特定幾何形狀金屬沉積跡線的工藝參數(shù)。在微結(jié)構(gòu)調(diào)控方面,Liu等[111]開(kāi)發(fā)了一種基于Gaussian過(guò)程回歸的機(jī)器學(xué)習(xí)方法對(duì)AlSi10Mg合金SLM的工藝窗口進(jìn)行優(yōu)化。模型訓(xùn)練和預(yù)測(cè)結(jié)果表明,在SLM工藝中,存在更寬廣的工藝窗口能夠?qū)崿F(xiàn)全致密AlSi10Mg合金(即相對(duì)密度≥ 99%)的制備。同時(shí),預(yù)測(cè)出的新的優(yōu)化工藝參數(shù)為合金微結(jié)構(gòu)的設(shè)計(jì)調(diào)控提供了巨大的空間,從而實(shí)現(xiàn)了增材制造鋁合金高強(qiáng)度和高延展性綜合性能的協(xié)同提升。進(jìn)一步地,機(jī)器學(xué)習(xí)結(jié)合傳統(tǒng)機(jī)械模型的計(jì)算結(jié)果,能夠加速工藝優(yōu)化過(guò)程。針對(duì)金屬增材制造中的開(kāi)裂問(wèn)題,Mondal等[33]提出了一種基于物理信息的機(jī)器學(xué)習(xí)方法,系統(tǒng)研究了6061Al、2024Al和AlSi10Mg等體系的裂紋發(fā)生機(jī)制,確定了裂紋形成與機(jī)械變量的相關(guān)性。如圖11[33]所示,首先基于傳熱和流體模型計(jì)算“冷卻速率”、“溫度梯度與凝固生長(zhǎng)速率比值”、“凝固應(yīng)力”以及“易損和弛豫時(shí)間比”4個(gè)變量,并結(jié)合文獻(xiàn)報(bào)道中的工藝參數(shù)、熱物性數(shù)據(jù)和實(shí)驗(yàn)結(jié)果作為輸入,采用決策樹(shù)、支持向量機(jī)和邏輯回歸對(duì)裂紋形成的條件進(jìn)行預(yù)測(cè),并比較了4個(gè)變量對(duì)于開(kāi)裂的影響層級(jí);最后根據(jù)預(yù)測(cè)結(jié)果,繪制了裂紋敏感性隨工藝參數(shù)變化的關(guān)系圖。與實(shí)驗(yàn)結(jié)果對(duì)比顯示,該方法提供的裂紋敏感性圖能夠準(zhǔn)確預(yù)測(cè)SLM制備鋁合金過(guò)程中的開(kāi)裂行為。上述研究表明,機(jī)器學(xué)習(xí)在金屬增材制造質(zhì)量監(jiān)控、工藝優(yōu)化、產(chǎn)品性能提升等技術(shù)領(lǐng)域發(fā)揮著重要作用。
圖11

圖11 基于物理信息的機(jī)器學(xué)習(xí)方法設(shè)計(jì)無(wú)裂紋3D打印件流程圖[33]
Fig.11 A physics-informed machine learning towards crack-free printing[33]. Computed values of cooling rate and solidification morphology (indicated by the ratio of temperature gradient and solidification growth rate) at the trailing edge of the melt pool, the ratio of vulnerable and relaxation times, and solidification stress are used in a physics informed machine learning to accurately predict cracking during SLM of aluminum alloys. The combination of machine learning and mechanistic modeling gives a cracking susceptibility index, process maps for crack-free printing, the comparative influence of the important variables, and a decision tree to predict crack formation[33] (PBF-L—powder bed fusion- laser)
5 總結(jié)與展望
本文綜述了目前國(guó)內(nèi)外不同尺度計(jì)算方法(原子尺度、介觀尺度和宏觀尺度模擬及機(jī)器學(xué)習(xí))輔助增材制造鋁合金開(kāi)發(fā)的研究思路與現(xiàn)狀。不同尺度計(jì)算方法已成功用于增材制造鋁合金的設(shè)計(jì)與開(kāi)發(fā)中,有效減少材料設(shè)計(jì)與開(kāi)發(fā)的時(shí)間和成本,實(shí)現(xiàn)了高性能增材制造鋁合金的高效設(shè)計(jì):原子尺度的第一性原理計(jì)算可為增材制造鋁合金中固溶強(qiáng)化的元素選擇和添加量提供指導(dǎo);原子尺度的分子動(dòng)力學(xué)模擬對(duì)增材制造鋁合金的局部熔化、快速凝固過(guò)程以及組織的力學(xué)響應(yīng)等進(jìn)行預(yù)測(cè),為合金制備過(guò)程的工藝選擇和組織優(yōu)化提供指導(dǎo);介觀尺度的計(jì)算熱力學(xué),從合金打印性、晶粒細(xì)化、固溶強(qiáng)化、析出強(qiáng)化和熱處理等方面實(shí)現(xiàn)無(wú)裂紋增材制造鋁合金的成分設(shè)計(jì)和工藝優(yōu)化;介觀尺度的相場(chǎng)模擬,能對(duì)增材鋁合金制備過(guò)程中微觀組織演化進(jìn)行研究,探討工藝參數(shù)對(duì)微觀組織的影響,為合金制備過(guò)程的工藝優(yōu)化和組織優(yōu)化提供指導(dǎo);宏觀尺度的有限元模擬,對(duì)增材制造鋁合金制備過(guò)程中熱作用、成形控制、缺陷形成等進(jìn)行預(yù)測(cè)和研究,易于指導(dǎo)工藝優(yōu)化。基于大量實(shí)驗(yàn)數(shù)據(jù)驅(qū)動(dòng)的機(jī)器學(xué)習(xí)方法,可對(duì)影響成形質(zhì)量和性能的工藝參數(shù)和過(guò)程參數(shù)進(jìn)行識(shí)別、分類,建立不同合金體系由工藝到性能的定量關(guān)系,實(shí)現(xiàn)金屬增材制造合金的質(zhì)量監(jiān)控、工藝優(yōu)化,提升產(chǎn)品綜合性能。
然而,當(dāng)前不同尺度計(jì)算方法往往僅針對(duì)增材制造鋁合金“成分-工藝-組織-性能”的部分環(huán)節(jié),嚴(yán)重制約了多尺度計(jì)算在增材制造領(lǐng)域的應(yīng)用。為此,未來(lái)可從以下2個(gè)方面來(lái)實(shí)現(xiàn)高性能增材制造鋁合金的高效開(kāi)發(fā)。
第一,建立增材制造鋁合金的集成計(jì)算材料工程框架。旨在集成不同尺度的計(jì)算方法為一個(gè)整體系統(tǒng),建立增材制造鋁合金“成分-工藝-組織-性能”的定量關(guān)系。
Mishra和Thapliyal[113]提出了適用于增材制造合金設(shè)計(jì)的集成計(jì)算材料工程框架及不同尺度計(jì)算在其中的應(yīng)用。將計(jì)算熱力學(xué)和第一性原理計(jì)算結(jié)合,建立合金從“成分-工藝-微結(jié)構(gòu)”的定量關(guān)系,有利于無(wú)裂紋的高性能增材制造鋁合金的成分設(shè)計(jì)。分子動(dòng)力學(xué)、相場(chǎng)模擬和有限元模擬相結(jié)合,可對(duì)增材制造過(guò)程中的溫度場(chǎng)、應(yīng)力場(chǎng)和微結(jié)構(gòu)演變進(jìn)行定量模擬,建立合金“工藝-微結(jié)構(gòu)”的定量關(guān)系,為合金制備工藝的優(yōu)化提供準(zhǔn)確高效的指導(dǎo)。機(jī)器學(xué)習(xí)和實(shí)驗(yàn)相結(jié)合,建立合金“工藝-微結(jié)構(gòu)-性能”間的定量關(guān)系,為金屬增材制造的質(zhì)量監(jiān)控、工藝優(yōu)化、產(chǎn)品性能提升提供指導(dǎo)。最終,不同尺度計(jì)算相結(jié)合,實(shí)現(xiàn)增材制造鋁合金從“成分-工藝-組織-性能”的整體設(shè)計(jì)。
需指出的是,高效可靠的集成計(jì)算材料工程框架強(qiáng)烈依賴于更加合理的計(jì)算方法以及高通量計(jì)算的支持。一方面,不同尺度計(jì)算方法還有待發(fā)展,比如:上文提到的改進(jìn)Scheil-Gulliver模型中,已考慮了快速凝固對(duì)溶質(zhì)偏析的影響,但對(duì)實(shí)際多元多相體系在快速凝固條件下部分穩(wěn)定相被抑制的預(yù)測(cè)仍存在偏差[21,24],因此有必要進(jìn)一步改進(jìn)該模型;在相場(chǎng)模型方面,有限界面耗散的多相場(chǎng)模型[93,94]能夠定量描述極端非平衡條件下(快速凝固過(guò)程)的溶質(zhì)截留效應(yīng),但要實(shí)現(xiàn)增材制造過(guò)程微結(jié)構(gòu)演變的定量模擬,還需耦合可靠的溫度場(chǎng)和流場(chǎng)方程。另一方面,高通量計(jì)算將進(jìn)一步提升合金設(shè)計(jì)的效率。高通量計(jì)算是實(shí)現(xiàn)“材料按需設(shè)計(jì)”的基礎(chǔ),可以有效縮小實(shí)驗(yàn)的范圍,為實(shí)驗(yàn)提供科學(xué)依據(jù)。目前,高通量計(jì)算較為耗時(shí),計(jì)算任務(wù)的高效管理和計(jì)算結(jié)果的后處理仍然具有挑戰(zhàn)性。實(shí)現(xiàn)高通量計(jì)算的方法主要包括并行計(jì)算和分布式計(jì)算,本文作者等[114]前期開(kāi)發(fā)了一種機(jī)器學(xué)習(xí)加速的分布式任務(wù)管理系統(tǒng)(Malac-Distmas),實(shí)現(xiàn)了高通量計(jì)算和各種數(shù)據(jù)的存儲(chǔ)。該系統(tǒng)嵌入機(jī)器學(xué)習(xí)技術(shù),可對(duì)輸出數(shù)據(jù)進(jìn)行增密,減少計(jì)算量,實(shí)現(xiàn)高通量計(jì)算的加速。通過(guò)將Malac-Distmas與不同的熱力學(xué)計(jì)算軟件耦合,實(shí)現(xiàn)了Gibbs自由能、相圖、Scheil-Gulliver模擬、擴(kuò)散模擬、析出模擬以及熱物性參數(shù)等的高通量計(jì)算。此外,Malac-Distmas不限于實(shí)現(xiàn)熱力學(xué)、動(dòng)力學(xué)和熱物理性質(zhì)的高通量計(jì)算,還可與其他計(jì)算/模擬軟件/代碼進(jìn)行耦合,實(shí)現(xiàn)高通量計(jì)算/模擬[114]。
第二,發(fā)展高性能增材制造鋁合金的多目標(biāo)設(shè)計(jì)方法與優(yōu)化策略/技術(shù)。基于集成材料工程建立增材制造鋁合金“成分-工藝-組織-性能”定量關(guān)系,針對(duì)不同應(yīng)用背景與材料性能需求,開(kāi)發(fā)對(duì)應(yīng)的多目標(biāo)(如:無(wú)裂紋高強(qiáng)高導(dǎo)電、無(wú)裂紋高強(qiáng)高韌等)設(shè)計(jì)方法,實(shí)現(xiàn)增材制造新型高性能鋁合金的高效設(shè)計(jì)與開(kāi)發(fā)。
綜合性能是衡量材料能否滿足工程應(yīng)用的前提。但由于材料性能影響因素眾多,性能間交互作用復(fù)雜,如材料的強(qiáng)度與塑性/韌性,強(qiáng)度與電導(dǎo)率等,往往相互沖突,呈此消彼長(zhǎng)的矛盾關(guān)系。因此,設(shè)計(jì)研發(fā)平衡材料各類性能最優(yōu)值、實(shí)現(xiàn)綜合性能最優(yōu)的材料,一直是材料領(lǐng)域的難題[115]。在多目標(biāo)設(shè)計(jì)方法方面,Yi等[53]前期通過(guò)結(jié)合計(jì)算熱力學(xué)、實(shí)驗(yàn)和機(jī)器學(xué)習(xí),建立稀土/堿土改性鑄造鋁合金“成分-工藝-組織-性能”定量關(guān)系,從鑄造性、晶粒細(xì)化、共晶改性、固溶強(qiáng)化、析出相特性和熱處理等多方面出發(fā),對(duì)合金的強(qiáng)度和塑性進(jìn)行多目標(biāo)設(shè)計(jì),成功開(kāi)發(fā)出高強(qiáng)高韌的稀土/堿土改性鑄造鋁合金。在多目標(biāo)優(yōu)化策略方面,主要包括逐層篩選優(yōu)化、多目標(biāo)轉(zhuǎn)單目標(biāo)優(yōu)化、Pareto前沿協(xié)同優(yōu)化等優(yōu)化策略。最近,Dai等[116]將三維定量相場(chǎng)模擬和分級(jí)多目標(biāo)優(yōu)化策略相結(jié)合,通過(guò)對(duì)物理氣相沉積(PVD)工藝中TiN涂層生長(zhǎng)過(guò)程進(jìn)行了大量的三維相場(chǎng)模擬,獲得了模型參數(shù)、微觀結(jié)構(gòu)和各種涂層性能之間的參數(shù)關(guān)系。基于定量相場(chǎng)模擬和關(guān)鍵實(shí)驗(yàn)數(shù)據(jù),提出了一種分級(jí)多目標(biāo)方法來(lái)設(shè)計(jì)多種涂層性能。隨后,根據(jù)對(duì)各種目標(biāo)組合的Pareto前沿的識(shí)別,對(duì)邊際效用進(jìn)行了研究。以分級(jí)的方式對(duì)模型/工藝參數(shù)進(jìn)行過(guò)濾,最終找到與實(shí)驗(yàn)結(jié)果一致的最佳TiN涂層性能窗口。針對(duì)不同應(yīng)用背景與材料性能需求,將上述方法合理應(yīng)用于增材制造新型鋁合金設(shè)計(jì),有望實(shí)現(xiàn)綜合性能優(yōu)異鋁合金的高效開(kāi)發(fā)。
來(lái)源--金屬學(xué)報(bào)“推薦閱讀”
【責(zé)任編輯】:國(guó)檢檢測(cè)版權(quán)所有:轉(zhuǎn)載請(qǐng)注明出處