分享:3Mn-0.2C中錳鋼形變誘導鐵素體動態相變機理
孫毅1,2, 鄭沁園2,3, 胡寶佳2,3, 王平,1, 鄭成武
,2,3, 李殿中2,3
1.
2.
3.
利用Gleeble熱模擬、SEM、EBSD和EPMA等方法,研究了3Mn-0.2C中錳鋼熱變形中發生的形變誘導鐵素體相變的組織轉變行為,分析了中錳鋼形變誘導超細晶組織的形成機理及其在熱變形后亞動態過程中的組織穩定性。結果表明,3Mn-0.2C中錳鋼在α + γ兩相區變形時會誘發形變誘導鐵素體相變,通過相變形成由超細晶鐵素體、細小殘余奧氏體和馬氏體組成的多相組織。形變誘導鐵素體以不飽和形核和有限生長的模式進行相變,這是導致鐵素體晶粒超細化的重要機理。同時,在超細晶鐵素體晶界及三叉晶界處形成的細小富Mn殘余奧氏體使形變誘導相變組織具有優異的組織穩定性。
關鍵詞:
輕量化和提高安全性是現代汽車工業發展的必然趨勢,這也對汽車用鋼的性能提出了更高要求,即具有更高強度的同時還需兼具高的塑性。但通常材料的強度和塑性是相互制約的,提高材料強度常常是以犧牲塑性為代價的[1]。因此,兼具高強度和高塑性的汽車用先進高強鋼(AHSS)一直是高性能鋼鐵材料研究的熱點[2~4]。目前,AHSS已發展了三代[5]。第一代AHSS主要是以bcc相為基體的低碳低合金鋼,包括雙相鋼、相變誘導塑性(TRIP)鋼和馬氏體鋼等,它們的成本較低,但強塑積普遍較低,通常低于20 GPa·%。第二代AHSS主要是通過添加大量奧氏體穩定化元素(主要為Ni和Mn)而制備出的奧氏體基鋼,包括奧氏體不銹鋼和孿生誘導塑性(TWIP)鋼等,具有非常優異的高強度和高塑性匹配,強塑積不低于50 GPa·%,但由于合金成本高、工藝性能差而限制了其廣泛應用。因此,成本接近第一代AHSS而性能接近第二代AHSS的低成本高強塑積(≥ 30 GPa·%)的第三代AHSS成為研發目標[6,7]。
Mn含量在3%~12% (質量分數)之間的中錳鋼(MMS)因在性能和成本之間的性價比上存在顯著的潛在優勢而成為第三代AHSS的優選鋼種[8,9]。通常中錳鋼的制備是通過臨界區奧氏體逆相變(ART)退火處理生成超細晶鐵素體與殘余奧氏體(RA)的復相組織[10],利用RA的TRIP效應獲得良好塑性,以此實現高強度與高塑性的配合[11,12],其中RA數量及穩定性控制是其關鍵所在[13,14]。目前對中錳鋼的研究也多聚焦于與ART相關的相變調控[15~20]及合金設計上[21~25]。從更實用的角度來看,基于奧氏體連續冷卻過程的制備工藝會更經濟,可充分利用傳統的控軋控冷(TMCP)的生產設備進行制備[26]。但因其Mn含量較高導致淬透性高,通常認為中錳鋼無法在連續冷卻過程中獲得達到強塑性要求的鐵素體、殘余奧氏體的復合多相組織。眾所周知,碳素鋼在臨界區實施熱變形時可大大促進其內鐵素體相變的發生[27],例如經典的形變誘導鐵素體相變(DIFT)已被證明是制備超細晶碳素結構鋼、微合金鋼的有效途徑[28~30]。最近也有學者提出通過DIFT途徑在淬火配分(Q&P)鋼中引入鐵素體而優化材料性能的思想[31],這也為中錳鋼的微觀組織設計提示了新的思路[32,33]。就DIFT而言,因其轉變過程涉及了形變與相變復雜的耦合作用,其相變模式迄今仍存在爭議[34,35],DIFT的微觀機理也有待進一步闡明。
基于此,本工作對中錳鋼過冷奧氏體在臨界區熱變形時發生的微觀組織演變開展研究。選用合金元素含量較低的3Mn-0.2C中錳鋼,利用電子背散射衍射(EBSD)和電子探針(EPMA)對中錳鋼在α + γ兩相區熱變形中發生的形變誘導鐵素體相變的微觀組織特征、合金元素分布及其演變規律進行分析,闡述中錳鋼中DIFT發生的微觀機理及其變形后亞動態過程中的組織穩定性。
1 實驗方法
實驗采用Fe-3Mn-0.2C中錳鋼(3Mn-0.2C MMS),化學成分(質量分數,%)為:C 0.2,Mn 2.9,Si 1.45,Fe余量。利用Thermo-Calc軟件計算得到其平衡相變轉變溫度Ae1 (鐵素體、奧氏體、滲碳體共存的最低溫度)和Ae3 (鐵素體、奧氏體共存的最高溫度)分別為650和797℃。3Mn-0.2C MMS采用真空感應爐冶煉,鑄錠經1200℃保溫2 h后鍛造成截面尺寸為40 mm × 40 mm的方坯,終鍛溫度不低于850℃。鍛坯經1200℃均勻化處理后水冷至室溫,隨后加工成直徑8 mm、高12 mm的圓柱形壓縮試樣。為研究中錳鋼在熱變形中發生的形變誘導鐵素體動態相變的組織演變行為,在Gleeble 3800熱模擬試驗機上進行等溫熱壓縮實驗,實驗方案如圖1a所示。先將試樣以10℃/s的速率加熱至850℃,保溫300 s后以1℃/s的速率冷卻至660℃,均溫60 s后以不同應變速率(
圖1

圖1 3Mn-0.2C中錳鋼(MMS)形變誘導鐵素體相變實驗及等溫鐵素體相變實驗的工藝示意圖
Fig.1 Schematics showing the thermal-mechanical cycles used for the deformation induced ferrite transformation (a) and the isothermal ferrite transformation (b) of the 3Mn-0.2C medium Mn steel (MMS) (Ae3 is the highest temperature at which ferrite and austenite phases can coexist in equilibrium. Ae1 is the lowest temperature at which ferrite, cementite, and austenite phases can coexist in equilibrium in the steel)
將淬火后的試樣沿平行于壓縮軸的方向對剖,分別利用Inspect F50熱場發射掃描電子顯微鏡(SEM)及EBSD對試樣剖面中心區域進行微觀組織表征,操作電壓為20 kV。利用JXA-8530F場發射EPMA分析合金元素的分布,操作電壓為15 kV。SEM和EPMA試樣經機械研磨拋光后,利用4% (體積分數) 的硝酸酒精進行腐蝕。EBSD試樣先經機械研磨拋光后,再使用振動拋光去除其表面的應力層。EBSD表征在搭載Symmetry EBSD探測器的Crossbeam550型SEM上進行,操作電壓為20 kV, 并利用AZtecCrystal軟件進行后續數據處理。
2 實驗結果
2.1 中錳鋼形變誘導鐵素體相變的微觀組織演變
圖2a為3Mn-0.2C MMS在應變速率
圖2

圖2 3Mn-0.2C MMS在660℃、0.001 s-1條件下變形的真應力-真應變曲線及不同應變時微觀組織的EBSD像
Fig.2 True stress-true strain curve of the 3Mn-0.2C MMS (a) and corresponding EBSD maps at strains of ε = 0.22 (b), 0.51 (c), and 0.92 (d) at temperature of T = 660oC and strain rate of
圖3對比了相同溫度下(660℃)等溫保持1800 s后與
圖3
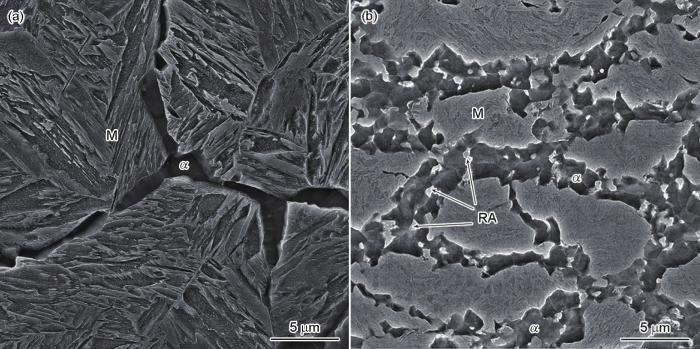
圖3 3Mn-0.2C MMS在T = 660℃保溫1800 s后和相同溫度下以應變速率
Fig.3 SEM images of 3Mn-0.2C MMS soaking at T = 660oC for 1800 s (a) and deformed to ε = 0.51 with
為了更清楚地認識中錳鋼中發生的形變誘導鐵素體相變的微觀組織演變,對T = 660℃、
圖4

圖4 3Mn-0.2C MMS在T = 660℃、
Fig.4 EBSD images of the 3Mn-0.2C MMS at ε = 0.22 (a), 0.51 (b), and 0.92 (c) with the hot deformation under T = 660oC and
圖5

圖5 3Mn-0.2C MMS在T = 660℃、
Fig.5 SEM image of the 3Mn-0.2C MMS deformed to ε = 0.92 under T = 660oC and
2.2 熱變形后保溫過程中形變誘導鐵素體的穩定性
為了評估中錳鋼形變誘導鐵素體相變微觀組織的穩定性,對T = 660℃、
圖6

圖6 3Mn-0.2C MMS在T = 660℃、
Fig. 6 EBSD images of the 3Mn-0.2C MMS deformed to ε = 0.92 under T = 660oC and
圖7
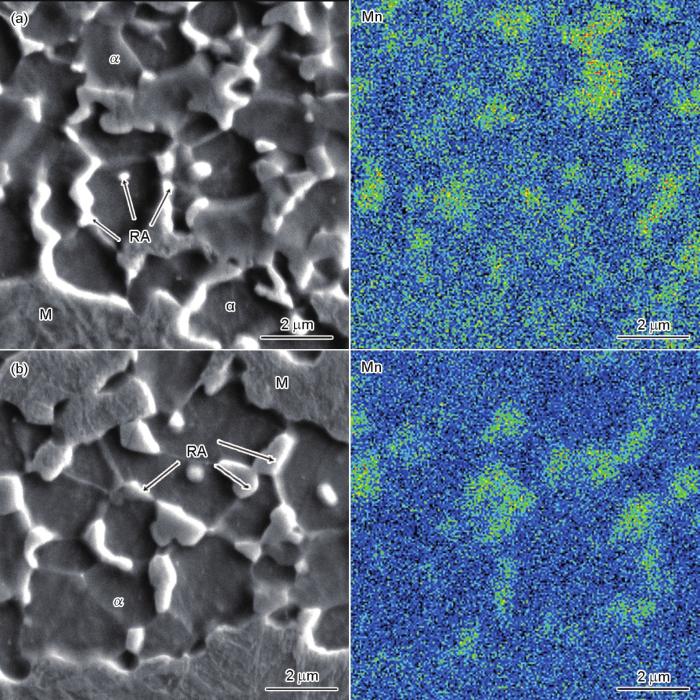
圖7 3Mn-0.2C MMS在T = 660℃、
Fig.7 SEM images and the distributions of Mn of the 3Mn-0.2C MMS deformed to ε = 0.92 under T = 660oC and
2.3 應變速率對中錳鋼形變誘導鐵素體相變的影響
圖8為0.2C-3Mn MMS在T = 660℃以不同應變速率熱變形至ε = 0.92時的微觀組織。由圖可以看出,應變速率對中錳鋼形變誘導鐵素體相變的影響非常明顯:應變速率越高,所形成的鐵素體晶粒越細,但體積分數越小。提高應變速率縮短相變發生的時間,會抑制形變誘導鐵素體晶粒的生長。盡管3種應變速率下所形成的鐵素體的晶粒尺寸和轉變分數差別很大,但形變誘導鐵素體晶粒的形核模式相同:(1) 形核均優先在原始奧氏體晶界處發生,晶粒之間極易發生碰撞;(2) 除在原始晶界形核外,形變誘導鐵素體超細晶均可在γ/α相界面前沿形核,之后以層狀逐漸向晶粒內部推進。結果還顯示,低應變速率下形成的殘余奧氏體的晶粒尺寸較大,體積分數也較高,而在
圖8
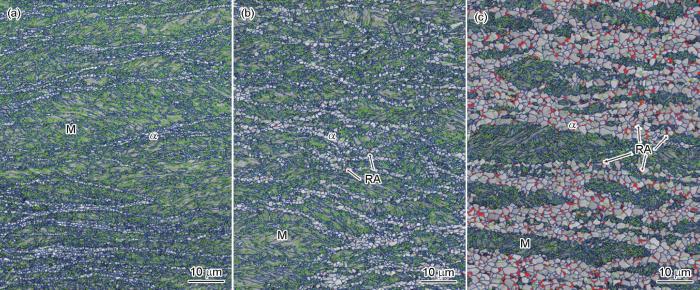
圖8 3Mn-0.2C MMS在T = 660℃下以不同應變速率變形至ε = 0.92時微觀組織的EBSD像
Fig.8 EBSD images of the 3Mn-0.2C MMS deformed to ε = 0.92 at T = 660oC with
圖9

圖9 3Mn-0.2C MMS在T = 660℃以不同應變速率變形至ε = 0.92時的SEM像及C、Mn元素的分布
Fig.9 SEM images and the distributions of C and Mn of the 3Mn-0.2C MMS deformed to ε = 0.92 at T = 660oC with
3 分析討論
形變誘導鐵素體相變是碳素結構鋼中發生的一種經典固態相變過程。傳統的形變誘導鐵素體相變通常選擇在Ac3 (加熱時奧氏體相變結束的溫度)附近實施熱變形,通過形變與相變的復合作用誘導γ-α相變加速發生,可在不添加合金元素的情況下將鐵素體晶粒細化至1 μm以下且組織均勻[28,30]。因其細化晶粒效果顯著且成本低廉,形變誘導鐵素體相變在20世紀90年代曾受到了非常廣泛的研究,已證明是制備超細晶低碳鋼、低碳低合金鋼及微合金鋼的有效途徑[30,34],但僅限于Mn含量在2%以下的碳素鋼。由于Mn是奧氏體穩定化元素,提高碳素鋼中的Mn含量在熱力學上即不利于鐵素體相變的發生。此外,因替換型元素Mn的擴散系數遠小于間隙型元素C的擴散系數,合金中Mn含量較高時,鐵素體的生長受Mn元素擴散控制致其相變速率極慢[36]。因此,通常認為Mn含量較高的碳素鋼中不利于形變誘導鐵素體相變的發生。
但本工作結果表明,形變誘導鐵素體相變可以在3Mn-0.2C MMS中發生,通過臨界區熱變形中發生的形變誘導鐵素體相變可在中錳鋼中形成由超細晶鐵素體、細小殘余奧氏體及馬氏體組成的多相微觀組織,如圖4所示。除了超細晶鐵素體之外,中錳鋼的DIFT組織中還形成了大量細小殘余奧氏體晶粒,這是中錳鋼DIFT組織有別于普通碳素鋼的典型特征。最近Shibata等[37]在利用原位中子散射(In situ neutron diffraction)研究0.1C-2Mn鋼中發生的DIFT機理時,提出鐵素體動態再結晶是DIFT超細晶形成的主要機理,但基于鐵素體動態再結晶的機理顯然無法解釋中錳鋼DIFT鐵素體三叉晶界處大量細小殘余奧氏體的殘留。如前所述,這些細小的殘余奧氏體晶粒主要是由于DIFT相變過程中Mn在這些區域的局部富集而得以殘留至室溫的,因此需進一步從DIFT形核路徑及元素配分的角度分析其轉變機理。
Zheng等[38,39]基于介觀尺度元胞自動機模擬對普碳鋼中發生的DIFT動態相變生成超細晶鐵素體的機理進行了闡述,提出了DIFT相變過程中因C在相界面前沿富集導致鐵素體晶粒限制生長和“不飽和形核”的機理。在γ-α相變中,因鐵素體在晶界處形核所需的形核功低,形核將優先在原始奧氏體晶界處發生。但當原始奧氏體晶界被新生鐵素體晶粒完全占據后,鐵素體形核會因其形核位置被消耗而達到“飽和”,其后的相變過程將由鐵素體的生長控制,如圖3a所示。而在DIFT中,新形成的γ/α相界前沿因位錯的持續累積也會成為鐵素體的優先形核位置,如圖8所示。這種情況下,雖然原始奧氏體晶界的形核位置已飽和,形變誘導鐵素體晶粒仍可在γ/α相界前沿處繼續形核,并以項鏈狀不斷向奧氏體晶粒內部推進,而使形核變得“不飽和”。可見,中錳鋼DIFT的形核也是以“不飽和形核”的模式進行的,此過程可用圖10所示的示意圖來描述。這種“不飽和形核”會引入更多的鐵素體晶核,使形核密度大大提高,同時使新形成的鐵素體晶粒在后續生長中極易發生碰觸。鐵素體長大過程中,C原子會不斷由新生鐵素體轉移至奧氏體,使奧氏體內的C濃度不斷升高(圖10a和b)。細晶鐵素體之間發生碰撞之前,γ/α相界前沿的C濃度場會先發生碰觸,導致相界前沿奧氏體域內的C濃度急劇升高(圖10c),形變誘導鐵素體的生長會因此受到抑制。與此同時,當γ/α相界的遷移速率降低時,Mn元素會跨越γ/α相界面由鐵素體向奧氏體配分,使這些奧氏體的局部區域逐漸富Mn。于是在超細晶鐵素體晶界及三叉晶界處保留了大量富Mn的細小未轉變奧氏體區(圖10d),而超細晶鐵素體晶界的大量存在也為Mn元素的局部再分配提供了快速擴散通道。這些富Mn奧氏體區域的存在會進一步限制鐵素體晶界的遷移,從而抑制DIFT鐵素體晶粒的生長及粗化;同時,Mn的富集提高了這部分奧氏體的穩定性,使其能殘留至室溫而形成大量且細小的殘余奧氏體片/島。
圖10
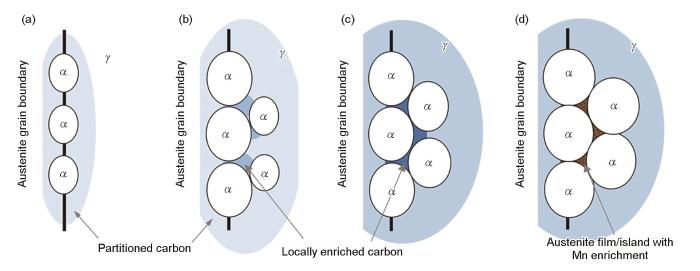
圖10 中錳鋼中形變誘導鐵素體相變的微觀組織演變示意圖
Fig.10 Schematics of the microstructure evolution during the deformation induced ferrite transformation of the medium Mn steel (a-d)
如前所述,中錳鋼在發生DIFT形成超細晶鐵素體的同時也易形成富Mn的殘余奧氏體片/島,這也是中錳鋼DIFT組織與普碳鋼DIFT組織的不同之處。中錳鋼中較高的Mn含量使其在發生鐵素體相變時易于在相界面發生配分而形成局部富Mn的區域,這些位于鐵素體晶界及三叉晶界處的富Mn細小未轉變奧氏體區的存在會釘扎鐵素體晶界的移動,阻礙其粗化,這也是超細晶鐵素體形成的原因之一;同時,這些富Mn細小未轉變奧氏體的穩定性很高,雖經長時間等溫保溫也不易分解,不僅能阻礙形變誘導鐵素體在后續熱處理中發生逆相變,而且會持續釘扎鐵素體晶界,使鐵素體晶粒能在長時間等溫處理中仍保持細小且等軸,如圖6b所示。正因為如此,中錳鋼的DIFT微觀組織表現出優異的穩定性,這也為高強塑性中錳鋼的制備提示了新的思路。
4 結論
(1) 3Mn-0.2C中錳鋼α + γ兩相區變形中可發生形變誘導鐵素體相變,通過相變可形成由超細晶鐵素體、細小殘余奧氏體和馬氏體組成的多相微觀組織。中錳鋼DIFT優先在原始奧氏體晶界形核,其后繼續在新形成的α/γ相界面前沿形核,并以項鏈狀不斷向奧氏體晶粒內部推進,表現為“不飽和”形核模式。同時,鐵素體晶粒之間易發生大規模碰觸,限制了鐵素體晶粒在相變過程中的生長。鐵素體的不飽和形核和有限生長是中錳鋼形變誘導鐵素體相變的2個特征,也是使晶粒超細化的重要原因。
(2) 中錳鋼DIFT可形成彌散分布在超細晶鐵素體晶界和三叉晶界的大量細小的片狀/島狀富Mn未轉變奧氏體。它們的形成會釘扎鐵素體晶界的遷移,使超細晶鐵素體在DIFT過程中及相變后的保溫過程中不易粗化,使DIFT組織具有優異的組織穩定性。同時,這些富Mn奧氏體易殘存至室溫形成細晶殘余奧氏體,對提高中錳鋼的力學性能有利。
(3) 中錳鋼DIFT受應變速率的影響明顯。提高應變速率使形變誘導體素體晶粒細化,但鐵素體轉變分數降低。降低應變速率使相變時間延長,有利于Mn配分的發生,大大促進殘余奧氏體的形成。形變誘導鐵素體相變組織中殘余奧氏體的形成與Mn元素的局部配分直接相關。