分享:添加Ti對Fe22Cr5Al3Mo合金在500℃過熱蒸汽中腐蝕行為的影響
孫蓉蓉1, 姚美意,1, 林曉冬
,1, 張文懷1, 仇云龍2, 胡麗娟1, 謝耀平1, 楊健3, 董建新4, 成國光5
1.
2.
3.
4.
5.
利用真空非自耗電弧爐熔煉了3種Fe22Cr5Al3Mo-xTi (x = 0、0.5、1.0,質量分數,%)合金,在靜態高壓釜中進行500℃、10.3 MPa過熱蒸汽的腐蝕實驗。采用XRD、OM、FIB/SEM、EDS和TEM觀察分析腐蝕前后樣品的顯微組織、晶體結構和成分。結果表明,3種合金腐蝕不同時間形成的氧化膜均發生了分層現象,氧化膜外層均為Fe2O3,中間層均為hcp-Cr2O3,內層均為Al2O3;在靠近氧化膜和合金界面處的Al2O3膜中存在α-(Fe, Cr)。0Ti、0.5Ti和1.0Ti合金的Cr氧化膜厚度與氧化膜總厚度的比值(R)遵循R0.5Ti > R1.0Ti > R0Ti,這說明與0Ti和1.0Ti相比0.5Ti合金的耐腐蝕性能最優。添加Ti可抑制合金中Cr23C6第二相的析出,降低合金的氧化膜總厚度,提高保護性hcp-Cr2O3膜的厚度,從而提高合金的耐腐蝕性能。
關鍵詞:
鋯合金在失水事故工況下會發生反應Zr + 2H2O → ZrO2 + 2H2[1],從而引發氫爆,因此科研人員提出了發展事故容錯燃料(accident tolerant fuel,ATF)的設想,涉及核燃料和包殼。FeCrAl合金由于具有適中的熱中子吸收截面、與UO2相容性好、良好的導熱性能和抗高溫氧化性能等優點,被認為是比較有發展前景的ATF包殼材料[2?9]。
作為ATF包殼的候選材料之一,FeCrAl合金需要在事故工況下具有比傳統鋯合金包殼更加優異的抗氧化性能。Dolley等[10]研究了FeCrAl合金和鋯合金在1200℃不同氣氛(Ar氣、空氣和蒸汽)下的氧化行為,結果表明,上述氣氛下FeCrAl合金的抗氧化性能均優于鋯合金。Park等[11]研究發現,在1200℃蒸汽條件下Fe22Cr5.8Al (質量分數,%)合金的氧化速率遠低于Zr-4和ZIRLO 2種鋯合金。此外,Badini和Laurella[12]研究發現,FeCrAl合金在高達1300℃的溫度下仍具有優異的抗氧化性能。多數研究[13?15]認為,FeCrAl合金在高溫條件下會形成一層穩定、致密且具有保護性的Al2O3膜,這是其具有優異抗氧化性能的主要原因。
除事故工況外,FeCrAl合金還需在常規腐蝕環境中具有優異的耐腐蝕性能。在目前鋯合金的腐蝕研究中,常規腐蝕條件一般包括:360℃、18.6 MPa、0.01 mol/L LiOH水溶液,360℃、18.6 MPa去離子水,360℃、18.6 MPa、Li + B水溶液,400℃、10.3 MPa過熱蒸汽及500℃、10.3 MPa過熱蒸汽等。作為擬取代鋯合金的ATF包殼候選材料,FeCrAl合金在上述常規條件下的腐蝕行為也有必要進行深入研究。Ning等[16]研究發現,在360℃、Li + B條件下FeCrAl合金的耐腐蝕性能明顯優于商用的Zr-4合金。Park等[11]研究發現,FeCrAl合金在360℃、18.5 MPa去離子水中的腐蝕速率低于鋯合金。Rebak[13]研究發現,FeCrAl合金在模擬壓水堆(PWR)和沸水堆(BWR)水環境中由于形成富Cr的保護性氧化物而具有優異的耐腐蝕性能。可見,FeCrAl合金在高溫高壓水或Li + B水溶液中具有較為優異的耐腐蝕性能,然而其在過熱蒸汽條件下的腐蝕行為卻鮮有報道,所以有必要研究FeCrAl合金在過熱蒸汽中的腐蝕行為。
添加合金元素對FeCrAl合金的顯微組織和性能具有重要影響。Kitajima等[17]研究發現,Mn、Nb或Ti的添加可以降低Fe20Cr10Al (原子分數,%)合金在900℃空氣中氧化625 h時氧化膜的褶皺程度。Huang等[18]研究發現,在1200℃的Ar-O2條件下,添加Ti可以改變FeCrAl合金氧化膜的生長機制。Schutze[19]研究發現,Ti有利于提高FeCrAlY合金表面Al氧化膜的黏附力。可見,在高溫條件下Ti的添加對FeCrAl合金的氧化膜存在影響,進而影響合金的抗氧化性能。黨杰等[20]研究發現,添加Ti和Nb可以降低低鉻鐵素體不銹鋼的腐蝕速率。有研究[21,22]發現,Nb、Ti對C、N元素的親和力大于Cr元素,Nb、Ti等元素的添加能夠有效固定合金中的C、N原子,抑制其與Cr生成Cr23C6第二相,從而提高鐵素體不銹鋼的耐腐蝕性能。可見,Ti對鐵素體不銹鋼的耐腐蝕性能有影響。
APMT (Kanthal,Fe22Cr5Al3Mo,質量分數,%)合金是在APM系列基礎上發展而來的一種FeCrAl型鐵素體不銹鋼,近年來對該合金或相似成分合金用于ATF包殼的相關研究也在開展之中。因此,本工作以APMT合金成分為參考,設計Fe22Cr5Al3Mo-xTi (x = 0、0.5、1.0,質量分數,%)合金,并在靜態高壓釜中進行500℃、10.3 MPa過熱蒸汽腐蝕實驗,研究Ti對Fe22Cr5Al3Mo合金耐腐蝕性能的影響。這有助于加深對合金元素影響FeCrAl合金腐蝕機理的認識,并為FeCrAl合金成分優化提供理論依據和指導。
1 實驗方法
以商用APMT合金成分為參考,通過添加不同含量的Ti元素制備成Fe22Cr5Al3Mo-xTi (x = 0、0.5、1.0,質量分數,%)合金,分別簡稱為0Ti、0.5Ti和1.0Ti合金。采用高純Fe、Cr、Al (純度均達99.99%,質量分數,下同)、MoFe (60%Mo)和海綿Ti (純度為99.7%)按設計成分配料,用真空非自耗電弧爐熔煉成約60 g的鈕扣錠。為保證鈕扣錠成分均勻,每個錠子翻轉熔煉6次。然后,對鈕扣錠依次進行1000℃熱壓,1050℃、30 min均勻化處理,1000℃、30 min熱軋,850℃、30 min退火,溫軋處理,制成厚度約1.5 mm的片狀樣品,最終進行850℃、30 min退火。用電感耦合等離子體原子發射光譜(ICP-AES)分析Cr、Al、Mo和Ti的含量,用LECO CS844型碳硫測定儀分析C的含量,用TC-436型氮氧測定儀分析N的含量。合金主要元素Cr、Al、Mo和Ti含量的分析結果與設計成分比較吻合,如表1所示。
表1 實驗用合金的成分 (mass fraction / %)
Table 1
Alloy | Cr | Al | Mo | Ti | C | N | Fe |
---|---|---|---|---|---|---|---|
0Ti | 22.90 | 5.25 | 3.64 | - | 0.0058 | 0.0089 | Bal. |
0.5Ti | 21.34 | 5.04 | 3.14 | 0.45 | 0.0064 | 0.0043 | Bal. |
1.0Ti | 21.99 | 4.59 | 3.44 | 0.98 | 0.0076 | 0.0045 | Bal. |
利用電火花線切割將3種Fe22Cr5Al3Mo-xTi合金切成尺寸約為10 mm × 10 mm × 1.5 mm的薄片樣品,依次采用800~2000號的水砂紙對其進行打磨、機械拋光,直至將樣品表面拋出鏡面效果;拋光好的樣品先用丙酮超聲清洗3次,然后在煮沸的去離子水中清洗并烘干,放入靜態高壓釜中進行500℃、10.3 MPa過熱蒸汽的腐蝕實驗,選取腐蝕3、500和1000 h的樣品進行表征分析。為了敘述方便,后文中用合金簡稱/腐蝕時間作為樣品編號,例如:“0Ti/3 h”表示0Ti合金在500℃、10.3 MPa過熱蒸汽中腐蝕3 h后的樣品。
采用18 kW D/MAX2500 V+/PC型X射線衍射儀(XRD)分析未腐蝕樣品的晶體結構,確定合金中的物相。采用配比為15 mL HCl + 30 mL C2H5OH + 5 g FeCl3的刻蝕劑對樣品進行金相刻蝕,并用VHX-100光學顯微鏡(OM)對合金的顯微組織進行觀察。采用裝備有INCA能譜儀(EDS)的JEM-2010F型透射電子顯微鏡(TEM)觀察分析未腐蝕樣品的顯微組織、第二相的形貌和成分,通過選區電子衍射(SAED)確定第二相的晶體結構。用Helios-600i雙束型聚焦離子束/掃描電子顯微鏡(FIB/SEM)觀察氧化膜表面形貌,并制備TEM觀察用的氧化膜截面樣品。用帶有EDS的JEM-2100F型高分辨透射電子顯微鏡(HRTEM)觀察氧化膜顯微組織,拍攝高角環形暗場(HAADF)像和HRTEM像,使用設備自帶的Gatan Digital Micrograph軟件進行分析處理,通過SAED和Fourier變換(FFT)確定氧化物的晶體結構;用EDS面掃描和線掃描分析氧化物的成分。
2 實驗結果
2.1 合金的顯微組織
圖1為0Ti、0.5Ti和1.0Ti合金的OM像。可以看出,0Ti、0.5Ti和1.0Ti合金均發生了再結晶,平均晶粒尺寸分別約為44、47和45 μm。可見,不高于1.0%Ti (質量分數)的添加對FeCrAl合金晶粒尺寸的影響不大。
圖1

圖1 0Ti、0.5Ti和1.0Ti合金的OM像
Fig.1 OM images of 0Ti (a), 0.5Ti (b), and 1.0Ti (c) alloys
圖2為0Ti、0.5Ti和1.0Ti合金的XRD譜。表2列出了3種合金的XRD特征峰參數和晶格常數的平均值
圖2

圖2 0Ti、0.5Ti和1.0Ti合金的XRD譜
Fig.2 XRD spectra of 0Ti, 0.5Ti, and 1.0Ti alloys
表2 α-Fe、0Ti、0.5Ti和1.0Ti合金的XRD特征峰參數(衍射半角θ、晶面間距d)和晶格常數平均值(
Table 2
Alloy | Crystal plane index (hkl) |
|
|||||
---|---|---|---|---|---|---|---|
(110) | (200) | (211) | |||||
2θ / (°) | d / nm | 2θ / (°) | d / nm | 2θ / (°) | d / nm | ||
α-Fe | 44.67 | 0.20268 | 65.02 | 0.14332 | 82.33 | 0.11702 | 0.28664 |
0Ti | 44.15 | 0.20495 | 64.24 | 0.14487 | 81.45 | 0.11807 | 0.28960 |
0.5Ti | 44.18 | 0.20482 | 64.24 | 0.14487 | 81.42 | 0.11810 | 0.28956 |
1.0Ti | 44.28 | 0.20439 | 64.36 | 0.14463 | 81.42 | 0.11810 | 0.28920 |
圖3為0Ti、0.5Ti和1.0Ti合金中典型第二相的TEM像和SAED花樣。表3總結了3種合金中典型第二相的種類和尺寸信息。圖4為0.5Ti和1.0Ti合金在500℃、10.3 MPa過熱蒸汽中腐蝕1000 h后基體中TiN第二相的EDS面掃描圖,TiN第二相的尺寸信息見表3。從圖3、4和表3可知,合金中的第二相尺寸均較小,在50?400 nm范圍內。0Ti合金中只檢測到面心立方(fcc)結構的Cr23C6和正交(o)結構的Cr3C2、Fe3C等碳化物;0.5Ti和1.0Ti合金中除檢測到o-Cr3C2、o-Fe3C等碳化物外,還發現有密排六方(hcp)結構的Fe2Ti、簡單立方(c)結構的(Fe, Cr)、底心單斜(mc)結構的Al8Mo3和fcc結構的TiN等含Ti、Al和Mo的第二相,但沒檢測到Cr23C6第二相。這說明添加Ti可以抑制合金中Cr23C6第二相的析出[22],促進Al、Mo以第二相的形式析出。
圖3

圖3 0Ti、0.5Ti和1.0Ti合金中典型第二相粒子的TEM像和SAED花樣
Fig.3 TEM images (a1-a6) and SAED patterns of P1-P6 (b1-b6) of typical second phase particles in 0Ti (a1, a2), 0.5Ti (a3, a4), and 1.0Ti (a5, a6) alloys (fcc—face centered cubic, o—orthorhombic, hcp—hexagonal close packed, c—primitive cubic, mc—base centered monoclinic)
表3 0Ti、0.5Ti和1.0Ti合金中典型第二相的尺寸統計 (nm)
Table 3
Alloy | fcc-Cr23C6 | o-Cr3C2 | o-Fe3C | hcp-Fe2Ti | c-(Fe, Cr) | mc-Al8Mo3 | fcc-TiN |
---|---|---|---|---|---|---|---|
0Ti | 100-200 | 100 | 300 | - | - | - | - |
0.5Ti | - | 100-200 | 80 | 100-150 | 150 | 150 | 350 |
1.0Ti | - | 70-120 | 50-100 | - | 120 | 250-400 | 240 |
圖4

圖4 0.5Ti和1.0Ti合金500℃、10.3 MPa過熱蒸汽中腐蝕1000 h時基體中TiN第二相的EDS面掃描圖
Fig.4 EDS mappings of TiN in the matrix of 0.5Ti (a) and 1.0Ti (b) alloys corroded in 500oC and 10.3 MPa superheated steam for 1000 h
2.2 氧化膜表面形貌
圖5是0Ti、0.5Ti和1.0Ti合金腐蝕3、500和1000 h的氧化膜表面顯微組織SEM像。腐蝕3 h時,3種合金表面均覆蓋一層細小的氧化物顆粒,但含Ti合金表面的氧化物顆粒更加細小(圖5a1[24]~c1);腐蝕500 h時,0Ti合金表面出現稀疏分布的大顆粒氧化物(圖5a2),而含Ti合金表面仍為細小的氧化物顆粒(圖5b2和c2),但相較于3 h時尺寸略有增加;腐蝕1000 h時,0Ti合金表面的大顆粒氧化物明顯增多,幾乎覆蓋整個表面,但氧化物顆粒的棱角沒有500 h時明顯(圖5a3),含Ti合金表面也出現了大顆粒氧化物,但分布較稀疏(圖5b3和c3)。這一結果表明,Ti的添加可以延緩合金外層大顆粒氧化物的形成。
圖5

圖5 0Ti、0.5Ti和1.0Ti合金在500℃、10.3 MPa過熱蒸汽中腐蝕3、500和1000 h的氧化膜表面顯微組織SEM像
Fig.5 SEM images of surface morphologies of oxide films formed on 0Ti (a1[24]-a3), 0.5Ti (b1-b3), and 1.0Ti (c1-c3) alloys corroded in 500oC and 10.3 MPa superheated steam for 3 h (a1[24]-c1), 500 h (a2-c2), and 1000 h (a3-c3)
2.3 氧化膜截面的顯微組織
圖6是0Ti、0.5Ti和1.0Ti合金腐蝕3、500和1000 h的氧化膜截面顯微組織HAADF像(其中,0Ti合金腐蝕3和500 h的HAADF像來自文獻[24])。由于大顆粒氧化物在氧化膜表面稀疏分布,不能代表合金氧化膜的真實厚度,所以本工作測量氧化膜厚度時未包括大顆粒氧化物的厚度。表4列出了3種合金腐蝕不同時間的氧化膜厚度。由圖6和表4可知,腐蝕3 h時,0Ti、0.5Ti和1.0Ti合金的氧化膜厚度均較薄且氧化膜/基體(O/M)界面不平整,分別為(250 ± 100) nm、(60 ± 25) nm和(60 ± 20) nm,且含Ti合金的氧化膜厚度小于0Ti合金;腐蝕500 h時,3種合金的氧化膜厚度分別增加至(600 ± 30) nm、(180 ± 85 nm)和(230 ± 65) nm;腐蝕1000 h時,3種合金氧化膜厚度分別增加至(720 ± 50) nm、(330 ± 80) nm和(370 ± 50) nm,但含Ti合金的氧化膜厚度仍小于0Ti合金。可見,添加Ti可降低合金氧化膜厚度(不包括大顆粒氧化物的厚度)。
圖6

圖6 0Ti、0.5Ti和1.0Ti合金在500℃、10.3 MPa過熱蒸汽中腐蝕3、500和1000 h的氧化膜截面HAADF像
Fig.6 HAADF images of the cross-sectional oxide films formed on the 0Ti (a1[24], a2[24], a3), 0.5Ti (b1-b3), and 1.0Ti (c1-c3) alloys corroded in 500oC and 10.3 MPa superheated steam for 3 h (a1[24]-c1), 500 h (a2[24]-c2), and 1000 h (a3-c3)
表4 0Ti、0.5Ti和1.0Ti合金在500℃、10.3 MPa過熱蒸汽中腐蝕3、500和1000 h時氧化膜的厚度 (nm)
Table 4
Alloy | 3 h | 500 h | 1000 h |
---|---|---|---|
0Ti | 250 ± 100 | 600 ± 30 | 720 ± 50 |
0.5Ti | 60 ± 25 | 180 ± 85 | 330 ± 80 |
1.0Ti | 60 ± 20 | 230 ± 65 | 370 ± 50 |
由于3種合金腐蝕不同時間的氧化膜均具有相似的多層結構,故以0.5Ti合金腐蝕1000 h的氧化膜為例進行說明。圖7是0.5Ti合金腐蝕1000 h的氧化膜截面的HAADF像和EDS面掃描圖。可以看出,氧化膜主要分為3層,從外到內依次是Fe氧化物區域(A層)、Cr氧化物區域(B層)和Al氧化物區域(D層),在B層和D層之間存在Cr和Al的混合氧化物區域(C層)。
圖7
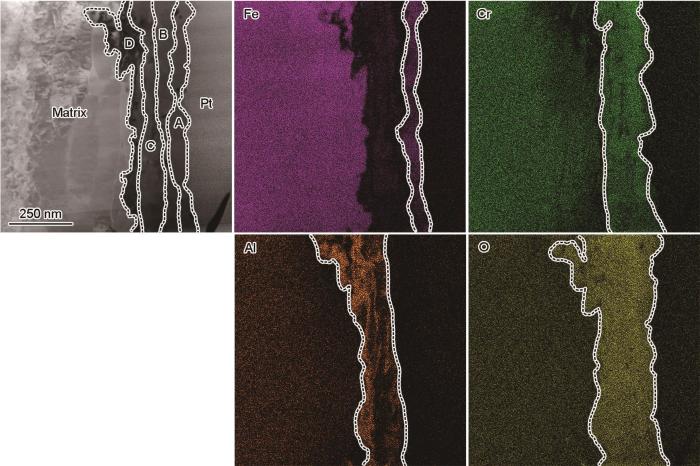
圖7 0.5Ti合金在500℃、10.3 MPa過熱蒸汽中腐蝕1000 h時氧化膜截面的HAADF像和EDS面掃描圖
Fig.7 HAADF image and EDS mappings of cross-sectional oxide film formed on 0.5Ti alloy corroded in 500oC and 10.3 MPa superheated steam for 1000 h
圖8為3種合金腐蝕不同時間的氧化膜典型區域的SAED花樣標定結果。表5總結了3種合金氧化膜的晶體結構。需要說明的是,根據EDS結果(圖7) 3種合金的氧化膜均存在分層現象,但由于部分區域的氧化膜較薄且不致密,在進行SAED分析時束斑容易擊穿氧化膜,難以獲得SAED花樣,因此表5中部分區域未能確定晶體結構。結合圖8和表5可知,3種合金氧化膜外層均為hcp-Fe2O3;中間層均為hcp-Cr2O3;內層均為Al2O3,包括hcp結構、o結構和單斜(m)結構,說明腐蝕形成的氧化膜結構較為復雜。含Ti合金在腐蝕3 h時便可標定出較致密的hcp-Cr2O3,而0Ti合金腐蝕1000 h才可標定出hcp-Cr2O3,說明Ti的添加可以促進較致密的保護性hcp-Cr2O3膜的形成。此外,在O/M界面附近的氧化膜中(圖7中的D層)存在富Fe相,由圖8f的SAED花樣標定結果可知該富Fe相是α-Fe。通過對該富Fe相進行EDS分析,發現該富Fe相中固溶有少量的Cr和Mo,但未檢測到Al。
圖8

圖8 0Ti、0.5Ti和1.0Ti合金在500℃、10.3 MPa過熱蒸汽中腐蝕500和1000 h的氧化膜截面不同區域的TEM像及SAED花樣
Fig.8 TEM images and SAED patterns of different areas (insets) in the cross-sectional oxide films formed on 0Ti (a), 0.5Ti (b-f), and 1.0Ti (g) alloys corroded in 500oC and 10.3 MPa superheated steam for 500 h (a-c, g) and 1000 h (d-f) (m—monoclinic, bcc—body centered cubic)
表5 0Ti、0.5Ti和1.0Ti合金在500℃、10.3 MPa過熱蒸汽中腐蝕3、500和1000 h時的氧化膜晶體結構
Table 5
Alloy | Oxide position | 3 h | 500 h | 1000 h |
---|---|---|---|---|
0Ti | O | hcp-Fe2O3 | hcp-Fe2O3 | hcp-Fe2O3 |
M | - | - | hcp-Cr2O3 | |
I | - | m-Al2O3 | - | |
0.5Ti | O | hcp-Fe2O3 | hcp-Fe2O3 | hcp-Fe2O3 |
M | hcp-Cr2O3 | hcp-Cr2O3 | hcp-Cr2O3 | |
I | hcp-Al2O3 | o-Al2O3 | o-Al2O3 | |
1.0Ti | O | - | - | hcp-Fe2O3 |
M | hcp-Cr2O3 | hcp-Cr2O3 | hcp-Cr2O3 | |
I | - | hcp-Al2O3 | hcp-Al2O3 |
3 分析討論
3.1 FeCrAl合金在500℃過熱蒸汽中的腐蝕過程
3種合金腐蝕不同時間的氧化膜均存在分層現象,即氧化膜從外到內依次是Fe、Cr、Al的氧化物,而且Al氧化物層與Cr氧化物層之間存在混合氧化物區域(圖7中C區域),O/M界面附近的鋁氧化膜中存在富Fe相(圖8f)。這一現象在空氣或Li + B條件下也有報道[16,25,26]。根據上述結果,FeCrAl合金在500℃過熱蒸汽中的腐蝕過程示意圖如圖9所示。在腐蝕初期,水吸附在合金表面,分解成OH-、O2-和H+[27],由于FeCrAl合金直接與水接觸,Fe、Cr、Al均發生氧化,在合金外表面會形成一層非常薄的原始混合氧化物膜。隨著腐蝕的進行,氧化性離子向內擴散,鐵離子、Cr3+和Al3+向外擴散,由于鐵離子的擴散速率遠高于Cr3+和Al3+ [16],鐵離子會優先在合金外表面與氧化性離子反應生成Fe的氧化物(圖9a)。隨著氧化性離子向內擴散,Cr3+和Al3+分別與氧化性離子反應生成Cr2O3和Al2O3,由于Cr和Al的擴散速率相近且Cr2O3和Al2O3可以互相固溶[28,29],所以此時會形成Cr和Al的混合氧化物區(圖9b)。根據氧勢圖[14]可知,Fe、Cr、Al發生氧化時的氧分壓為Al < Cr < Fe,由于Cr和Al的混合氧化物區的形成會阻礙氧化性離子的擴散,導致O/M界面處的氧分壓降低。因此,鐵離子只能繼續向外擴散至鐵氧化物膜/Cr和Al的混合氧化物區界面處才會形成Fe的氧化物;Cr和Al原子優先在O/M界面處發生氧化生成Cr、Al的氧化物,使Cr和Al的混合氧化層變厚(圖9b)。當厚度達到一定程度時,O/M界面處的氧分壓低至不能使Cr發生氧化時,此時其會繼續向外擴散至Cr和Al的混合氧化物區/鐵氧化物界面處并氧化形成鉻氧化物膜,而Al則在O/M界面處發生氧化形成鋁氧化物膜(圖9c)。有研究表明,部分FeCrAl合金腐蝕形成的鐵氧化物是Fe2O3,部分合金形成的是Fe3O4[11,28,30],而本工作中3種合金腐蝕不同時間最外層形成的鐵氧化物均是Fe2O3 (表5),這主要是因為3種合金具有較高的Cr和Al含量,導致腐蝕過程中更易形成Cr和Al的混合氧化物區、Cr氧化物膜和Al氧化物膜,并阻礙鐵離子的向外擴散,導致氧化性離子過剩,從而形成Fe2O3。
圖9
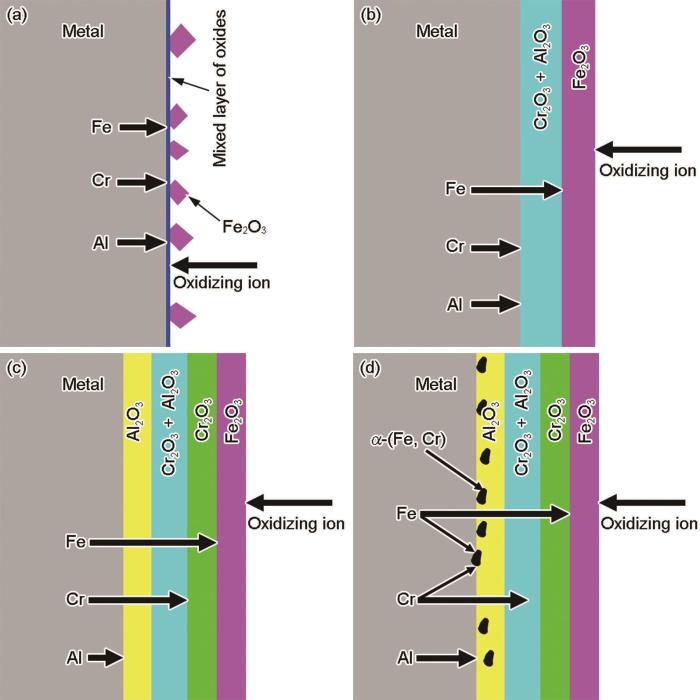
圖9 FeCrAl合金在500℃過熱蒸汽中的腐蝕過程示意圖
Fig.9 Schematics of corrosion process of FeCrAl alloys in 500oC and 10.3 MPa superheated steam
(a) Fe2O3 is preferentially formed on the thin original mixed layer of oxides
(b) the mixed oxide region of Cr and Al is formed
(c) Cr2O3 formed at the interface between Fe2O3 and the mixed oxide region of Cr and Al, while the Al2O3 formed at the O/M interface
(d) unoxidized Fe and Cr near O/M interface exist in the form of α-(Fe, Cr)
隨著腐蝕的進行,鋁氧化物層和鉻氧化物層的厚度均增加,鐵離子、Cr3+和Al3+的向外擴散速率和氧化性離子的向內擴散速率均進一步降低,導致O/M界面附近的部分Fe和Cr未發生氧化,并以α-(Fe, Cr)的形式存在(圖9d)。另外由于Al的含量較低,其在O/M界面處便可與向內擴散的氧化性離子發生氧化,所以α-(Fe, Cr)中并沒有Al的殘留(圖7和8)。
3.2 Ti對FeCrAl合金耐腐蝕性能的影響
添加Ti不僅可以抑制Cr23C6第二相的形成(圖3和表3),同時還可以促進較致密的保護性hcp-Cr2O3膜的形成(圖8和表5),這對合金的耐腐蝕性能均存在有利影響。由于Ti對C、N元素的親和性比Cr元素強,因此Ti能夠有效固定合金中的C、N原子,抑制其與Cr生成Cr23C6第二相[21,22]。表3中含Ti合金中沒檢測到Cr23C6第二相,這也驗證了添加Ti可以抑制Cr23C6第二相的形成。Cr23C6是造成合金晶間腐蝕的主要原因,所以Ti的添加可降低合金的晶間腐蝕傾向,提高合金的耐腐蝕性能。
對于含Ti合金,腐蝕初期鐵氧化物以及Cr和Al的混合氧化物區形成,O/M界面處的氧分壓較低,Ti在O/M界面處表現為+2價,降低了O/M界面附近的陽離子空位濃度[18],導致鐵離子、Cr3+和Al3+通過氧化物膜的擴散速率減慢。同時,由于氧化膜/蒸汽界面處氧分壓較高,Ti表現為+4價,降低了該處的陰離子空位濃度[18],導致氧化性離子通過氧化膜的擴散速率減慢。因此,含Ti合金形成的鐵氧化物膜以及Cr和Al的混合氧化物區均較薄。由于含Ti合金形成的Cr和Al的混合氧化物區較薄,導致該區域對向外擴散的Cr3+的阻礙作用降低,從而使Cr3+更容易擴散至Cr和Al的混合氧化物區/鐵氧化物層界面處,進而形成較厚的鉻氧化物膜。與0Ti合金相比,含Ti合金氧化膜外表面的氧化性離子通過氧化膜的擴散速率較慢,從而使氧化性離子不易擴散至O/M界面,進而導致形成的Al氧化物層較薄(表6)。
表6 0Ti、0.5Ti和1.0Ti合金在500℃、10.3 MPa過熱蒸汽中腐蝕500 h時鐵氧化物膜、鉻氧化物膜、鋁氧化物膜以及Cr和Al的混合氧化物區的厚度 (nm)
Table 6
Alloy | Iron oxide | Chromium oxide | Aluminum oxide | Overlap area |
---|---|---|---|---|
0Ti | 220 | 40 | 80 | 260 |
0.5Ti | 60 | 65 | 32 | 23 |
1.0Ti | 80 | 65 | 60 | 25 |
FeCrAl合金具有優異的耐腐蝕性能,是由于合金表面可以形成保護性的氧化膜。在較低溫度下(900℃),hcp-Cr2O3膜是FeCrAl合金的保護性氧化膜[13,31]。由于本工作的實驗溫度為500℃,所以hcp-Cr2O3膜為合金的保護性氧化膜。因此采用鉻氧化物膜厚度與氧化膜總厚度的比值(R)可以定性地描述FeCrAl合金的耐腐蝕性能。由表7可知,0Ti、0.5Ti和1.0Ti合金的R存在如下關系:R0.5Ti > R1.0Ti > R0Ti,這可以定性地說明0.5Ti合金的耐腐蝕性能最優,1.0Ti合金的次之,0Ti合金的最差。因此,添加Ti不僅可以促進較致密的保護性hcp-Cr2O3膜的形成,還可以提高合金中鉻氧化物膜的厚度,進而提高了合金的耐腐蝕性能。
表7 0Ti、0.5Ti和1.0Ti合金在500℃、10.3 MPa過熱蒸汽中腐蝕3、500和1000 h時Cr氧化物膜厚度/氧化膜總厚度的比值
Table 7
Time / h | 0Ti | 0.5Ti | 1.0Ti |
---|---|---|---|
3 | ~0 | 0.133 | 0.083 |
500 | 0.067 | 0.361 | 0.283 |
1000 | 0.09 | 0.348 | 0.176 |
4 結論
(1) 0Ti合金中只檢測到面心立方結構的Cr23C6和正交結構的Cr3C2、Fe3C等碳化物;0.5Ti和1.0Ti合金中除檢測到正交結構的Cr3C2和Fe3C等碳化物外,還發現有密排六方結構的Fe2Ti、簡單立方結構的(Fe, Cr)、底心單斜結構的Al8Mo3和面心立方結構的TiN等含Ti、Al和Mo的第二相,但沒檢測到Cr23C6第二相;Ti的添加可以抑制合金中Cr23C6第二相的析出。
(2) 3種合金在500℃、10.3 MPa過熱蒸汽中腐蝕不同時間形成的氧化膜均發生了分層現象,外層均為Fe2O3 (密排六方結構),中間層均為Cr2O3 (密排六方結構),內層均為Al2O3 (包括密排六方、正交和單斜結構);靠近O/M界面的Al氧化物膜中存在α-(Fe, Cr)。
(3) 添加Ti可降低FeCrAl合金的氧化膜總厚度(不包括大顆粒氧化物的厚度),但可以提高作為保護性氧化膜的hcp-Cr2O3膜的厚度,從而提高合金的耐腐蝕性能。
來源-金屬學報