分享:三維互穿結(jié)構(gòu)SiC晶須骨架增強(qiáng)鎂基復(fù)合材料制備及其力學(xué)性能
谷瑞成1,2, 張健2, 張明陽2, 劉艷艷2, 王紹鋼3, 焦大2, 劉增乾,2, 張哲峰
,2
1.
2.
3.
選用SiC晶須骨架作為增強(qiáng)相,利用重力輔助沉降、壓縮致密化、骨架燒結(jié)及無壓熔滲的方法制備了具有微觀三維互穿結(jié)構(gòu)的SiC晶須骨架增強(qiáng)鎂基復(fù)合材料,并對其微觀組織結(jié)構(gòu)與力學(xué)性能(特別是斷裂韌性)進(jìn)行了表征與分析。通過對SiC晶須骨架進(jìn)行預(yù)氧化處理,提高了增強(qiáng)相與基體之間的潤濕性,并通過調(diào)節(jié)預(yù)氧化溫度控制析出相含量和孔洞等缺陷,優(yōu)化了復(fù)合材料的彎曲強(qiáng)度與斷裂韌性,獲得了穩(wěn)定的裂紋擴(kuò)展行為(上升的R曲線)。相比于以純Mg為基體的復(fù)合材料,以AZ91D鎂合金為基體的復(fù)合材料中析出相含量高且發(fā)生粗化,使得材料強(qiáng)度提高的同時斷裂韌性降低。
關(guān)鍵詞:
在保證安全服役的前提下,實現(xiàn)結(jié)構(gòu)材料的輕量化不僅有助于節(jié)能降耗、減少環(huán)境污染,而且能夠采用更少的材料滿足實際應(yīng)用對材料力學(xué)性能的需求,從而促使材料得以更高效的利用。Mg是典型的輕質(zhì)金屬結(jié)構(gòu)材料,其比重僅為1.74 g/cm3,具有突出的比強(qiáng)度和比剛度以及良好的阻尼特性和切削性能[1~3],并且容易實現(xiàn)回收利用。但是,與鋼鐵、鋁合金、鈦合金等金屬結(jié)構(gòu)材料相比,Mg及鎂合金的絕對強(qiáng)度仍然偏低[2,3],特別是在高溫條件下容易發(fā)生蠕變[4],這些都限制了Mg及鎂合金作為結(jié)構(gòu)材料的實際應(yīng)用。
通過在基體中引入增強(qiáng)相制備復(fù)合材料是提高M(jìn)g及鎂合金強(qiáng)度的有效途徑[5~7],常用的增強(qiáng)相包括氧化物[8] (如Al2O3、TiO2)、氮化物[9,10] (如BN、AlN、TiN、ZrN)、硼化物[11] (如TiB2、ZrB2)、碳化物[12] (如B4C、SiC、TiC、ZrC)和金屬[13,14] (如Ti、Ni、NiTi)等。其中,SiC陶瓷具有模量高、硬度大、密度低、耐磨性和化學(xué)穩(wěn)定性好等優(yōu)點[15],是鎂基復(fù)合材料較為理想的增強(qiáng)相[16,17]。特別是,SiC晶須(SiCw)作為一種高度取向的SiC短纖維單晶體,因具有微納米尺度和較高的長徑比而能夠在復(fù)合材料中起到顯著的增強(qiáng)作用[18~23]。
目前SiCw/Mg復(fù)合材料主要通過粉末冶金、攪拌鑄造以及擠壓鑄造等方法制備而成[19~23],得到的復(fù)合材料相比于基體金屬表現(xiàn)出更高的強(qiáng)度、硬度和耐磨性。例如,Tsukamoto[19]利用等離子燒結(jié)的方法制備得到了以SiC晶須和SiC顆粒混雜增強(qiáng)的鎂基復(fù)合材料;Tayebi等[20]采用攪拌鑄造的方法制備得到了SiCw/ZK60鎂合金復(fù)合材料,并對其進(jìn)行擠壓和時效處理,使得復(fù)合材料的屈服強(qiáng)度、抗拉強(qiáng)度和彈性模量相比基體合金均顯著提高;Zheng等[21]采用擠壓鑄造的方法制備的SiCw/AZ91D鎂合金復(fù)合材料也達(dá)到了顯著的強(qiáng)化效果。然而,利用上述方法制備的SiCw/Mg復(fù)合材料在組織結(jié)構(gòu)與力學(xué)性能方面仍存在一定的局限性,主要包括:(1) 復(fù)合材料中SiCw體積分?jǐn)?shù)通常不超過20%,難以實現(xiàn)較高的增強(qiáng)相含量;(2) SiCw在Mg基體中呈分散分布,增強(qiáng)相在三維空間的連通性較差;(3) SiCw和Mg (及鎂合金)之間界面潤濕性較差,界面結(jié)合較弱,容易成為復(fù)合材料中優(yōu)先開裂的位置;(4) SiCw在Mg基體中往往隨機(jī)取向,使得其強(qiáng)化能力難以沿實際使用方向得以最大限度的利用。
與人造材料相比,自然界中的貝殼、骨骼等天然生物材料由于具有獨(dú)特的微觀三維互穿結(jié)構(gòu)而表現(xiàn)出優(yōu)異的力學(xué)性能[24],它們的不同組元在三維空間中均各自保持連續(xù),并且相互嵌鎖交錯排列,這種結(jié)構(gòu)有利于促進(jìn)應(yīng)力在各自相內(nèi)部以及兩相之間有效傳導(dǎo),并實現(xiàn)它們性能優(yōu)勢的良好結(jié)合,該結(jié)構(gòu)能夠為復(fù)合材料的結(jié)構(gòu)設(shè)計提供靈感和指導(dǎo)。本工作基于重力輔助沉降與壓縮致密化的方法制備了具有一定擇優(yōu)取向排列的SiCw多孔骨架,然后對其進(jìn)行預(yù)氧化處理以改善界面潤濕,再利用無壓熔滲的方法使Mg或鎂合金填充骨架孔隙,制備得到了具有微觀三維互穿結(jié)構(gòu)的SiCw增強(qiáng)鎂基復(fù)合材料。研究了材料的制備工藝、組織結(jié)構(gòu)與力學(xué)性能,以期為SiCw/Mg復(fù)合材料的結(jié)構(gòu)設(shè)計、優(yōu)化制備與性能改進(jìn)提供指導(dǎo)。
1 實驗方法
1.1 復(fù)合材料制備
所用SiCw粉體純度為99.5% (質(zhì)量分?jǐn)?shù),下同),該粉體利用化學(xué)合成的方法使晶須形核并沿著軸向連續(xù)均勻生長制備而成,晶須直徑不超過2.5 μm,長徑比不小于20。以平均直徑分別為20和30 nm的Al2O3粉體和Y2O3粉體作為SiCw的燒結(jié)助劑[25],其中添加的Al2O3與Y2O3的質(zhì)量比為57∶43,SiCw與燒結(jié)助劑質(zhì)量比為9∶1。選用熔點為58℃的石蠟作為SiCw的分散介質(zhì),其中石蠟與陶瓷粉體(SiCw和燒結(jié)助劑之和)質(zhì)量比為12∶1。選用純度為99.95%的純Mg和AZ91D鎂合金作為基體。
具有微觀三維互穿結(jié)構(gòu)的SiCw/Mg復(fù)合材料的制備工藝如圖1所示。具體如下:首先將SiCw和燒結(jié)助劑Al2O3與Y2O3按照比例添加到150℃熔融石蠟中,使用JJ-1H型電動攪拌器以300 r/min的速率攪拌15 min,得到均勻分散的混合漿料,將漿料倒入溫度為150℃的不銹鋼模具中;在重力作用下,SiCw在漿料中緩慢自發(fā)沉降到模具底部,在此過程中,SiCw長軸傾向于在與重力方向垂直的水平平面內(nèi)發(fā)生擇優(yōu)取向排列,并且相互搭接,晶須之間留有空隙;待熔融的石蠟沿模具縫隙排出后,在150℃保溫條件下沿垂直方向?qū)悠芳訅褐?30 MPa并保壓30 min,促使多余的石蠟排出并進(jìn)一步增強(qiáng)SiCw在水平平面內(nèi)的擇優(yōu)取向排列,使得SiCw長軸更傾向于與二維層面方向平行,冷卻至室溫后卸壓得到SiCw坯體;將坯體在空氣中以2℃/min的速率升溫至700℃,保溫3 h后隨爐冷卻,以去除其中含有的石蠟,從而使SiCw骨架具有多孔結(jié)構(gòu);在流動Ar氣氣氛中,將樣品加熱至1800℃并保溫1 h進(jìn)行燒結(jié),隨爐冷卻后得到具有一定的強(qiáng)度且擇優(yōu)取向排列的SiCw多孔骨架。
圖1
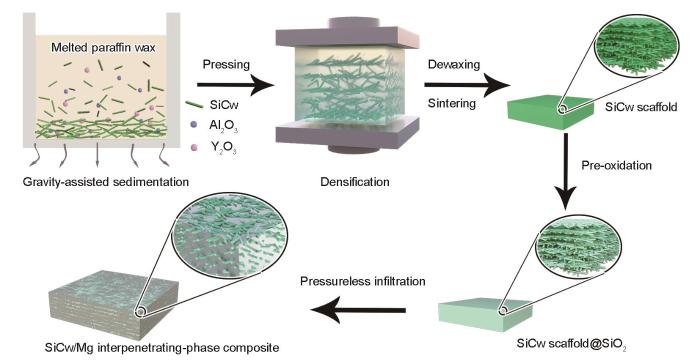
圖1 三維互穿結(jié)構(gòu)SiC晶須(SiCw)骨架增強(qiáng)鎂基復(fù)合材料的制備工藝流程示意圖
Fig.1 Schematics of the fabrication procedure for the Mg-based composites reinforced by SiC whisker (SiCw) scaffolds with three-dimensional interpenetrating-phase architecture
利用純Mg和AZ91D鎂合金對預(yù)氧化處理后的SiCw骨架進(jìn)行無壓熔滲處理,具體工藝為:將骨架置于石墨坩堝中,將純Mg或AZ91D鎂合金塊放置在骨架上方,采用SRYL-2300/9型石墨電阻爐在流動Ar氣氣氛中加熱至850℃并保溫30 min,然后隨爐冷卻,最終得到具有微觀三維互穿結(jié)構(gòu)的SiCw骨架增強(qiáng)鎂基復(fù)合材料。
1.2 組成與組織結(jié)構(gòu)表征
燒結(jié)SiCw骨架的孔隙率可以通過其表觀密度基于以下公式計算得到[30]:
式中,
式中,
采用D8 Advance型X射線衍射儀(XRD)對復(fù)合材料進(jìn)行物相分析;利用Inspect F50型場發(fā)射掃描電子顯微鏡(SEM)在20 kV加速電壓下觀察SiCw骨架和復(fù)合材料的微觀形貌,其中SiCw骨架在觀察之前進(jìn)行噴金處理以減少表面電荷累積;采用Xradia 800 Ultra型三維納米X射線顯微鏡在40 kV加速電壓下對復(fù)合材料的三維微觀結(jié)構(gòu)進(jìn)行X射線三維成像(XRT)掃描重建,實驗的原理和方法見文獻(xiàn)[32],具體操作為:利用水冷低速金剛石線切割機(jī)切取長和寬度皆為2 mm、厚度為4 mm復(fù)合材料試樣,且樣品的厚度方向與其層狀方向垂直。將樣品固定在JJ-1H型電動攪拌器上并以1000 r/min的速率勻速旋轉(zhuǎn),使用粒度為6.5 μm的砂紙對試樣進(jìn)行機(jī)械研磨并利用型號為VHX-1000E的超景深三維顯微系統(tǒng)測量尺寸,得到直徑約50 μm、長度不小于70 μm的圓柱形樣品,使樣品長軸平行于由X射線源和探測器組成的平面的法線方向;將樣品沿其長軸方向以0.4°/min的速率勻速旋轉(zhuǎn)180°,每隔0.2°采集一張二維投影圖像;然后,基于濾波反投影算法將二維投影圖像重建為三維圖像,三維圖像體素尺寸約為64 nm3;最后,利用Avizo Fire軟件對XRT數(shù)據(jù)進(jìn)行處理分析。
1.3 力學(xué)性能測試
在室溫下對復(fù)合材料進(jìn)行力學(xué)性能測試,所測試樣品通過水冷低速金剛石線切割機(jī)從熔滲得到的塊體中切取,并利用粒度為6.5 μm的砂紙對試樣表面進(jìn)行機(jī)械研磨。利用Instron E1000型力學(xué)試驗機(jī)進(jìn)行三點彎曲測試,加載方向垂直于復(fù)合材料中SiCw擇優(yōu)取向的平面,即平面的法線方向加載。根據(jù)ASTM C1161-13,樣品寬度為2.6 mm、厚度為1.95 mm、跨距為26 mm,加載速率為0.1 mm/min。
采用單邊缺口三點彎曲實驗測試復(fù)合材料的斷裂韌性,該實驗在JSM-6510型SEM腔體內(nèi)部的SERVO PULSER型原位力學(xué)試驗臺上完成,加載方向垂直于SiCw擇優(yōu)取向的平面。根據(jù)ASTM E1820-13,試樣寬度為2 mm、厚度為4 mm、跨距為16 mm,加載速率為3 μm/min,加載前利用水冷低速金剛石線切割機(jī)在試樣中心切出深度為1.8 mm的缺口,并利用蘸有2.5 μm粒徑水溶金剛石研磨膏的不銹鋼刀片對缺口尖端進(jìn)行銳化處理,使缺口總長度接近試樣厚度的一半(即2 mm)。通過原位掃描電子顯微觀察記錄裂紋擴(kuò)展長度(Δa),基于非線性彈性斷裂力學(xué)通過公式計算材料的
式中,
在Ⅰ型平面應(yīng)變條件下,裂紋尖端與
式中,
2 實驗結(jié)果
2.1 組成與組織結(jié)構(gòu)
圖2為燒結(jié)處理前后SiCw骨架的SEM像以及燒結(jié)SiCw骨架和經(jīng)過不同溫度預(yù)氧化處理后骨架的XRD譜。由SEM像(圖2a~c)可以看出,燒結(jié)前SiCw骨架中晶須之間相互搭接交錯排列,經(jīng)燒結(jié)后SiCw在相鄰位置相互連接形成一個整體,得到具有微觀多孔結(jié)構(gòu)的SiCw骨架,經(jīng)測定孔隙率為58.2% ± 0.9%,可推導(dǎo)出SiCw的體積分?jǐn)?shù)約為41.8%,并且骨架中的SiCw以及孔隙均在三維空間各自保持連續(xù)并相互穿插,表現(xiàn)為與天然生物材料相似的微觀三維互穿結(jié)構(gòu);此外,SiCw骨架整體表現(xiàn)出一定的層狀結(jié)構(gòu)特征,并且層與層之間相互交錯,沒有明顯的界限,SiCw長軸傾向于與二維層面方向平行,而在層面內(nèi)則隨機(jī)取向排列,這是由于SiCw具有高的長徑比(≥ 20),在熔融石蠟中發(fā)生沉降時,其長軸傾向于在水平方向擇優(yōu)取向排列進(jìn)行鋪層[35]。在燒結(jié)前沿垂直于層面方向?qū)iCw坯體進(jìn)行壓縮致密化處理,可以進(jìn)一步促進(jìn)SiCw沿層面方向擇優(yōu)取向排列。由XRD譜(圖2d)可以看出,燒結(jié)后的SiCw骨架中,除SiC外,還含有少量的Y3Al2(Al2O4)3,該相由添加的燒結(jié)助劑Al2O3和Y2O3反應(yīng)生成[25]。對SiCw骨架進(jìn)行預(yù)氧化處理后,可以看到骨架中有氧化產(chǎn)物SiO2生成,并且隨著預(yù)氧化溫度的升高,SiO2衍射峰相對強(qiáng)度增大,說明其相對含量逐漸增加。燒結(jié)后的SiCw骨架在預(yù)氧化處理前后微觀形貌沒有明顯差異,這是由于在該處理溫度范圍,SiCw表面僅生成厚度約為幾納米的SiO2薄膜[26,27]。
圖2

圖2 燒結(jié)處理前后SiCw骨架的SEM像以及燒結(jié)SiCw骨架和經(jīng)過不同溫度預(yù)氧化處理后骨架的XRD譜
Fig.2 SEM images of the SiCw scaffolds before (a) and after (b, c) sintering treatment, and XRD spectra of the sintered SiCw scaffolds before and after pre-oxidation treatment at different temperatures (d)
圖3為經(jīng)不同溫度預(yù)氧化處理的SiCw骨架熔滲純Mg和AZ91D鎂合金得到的復(fù)合材料的XRD譜以及對應(yīng)1100和1300℃預(yù)氧化溫度的復(fù)合材料的SEM像。由XRD譜(圖3a)可以看出,SiCw/Mg復(fù)合材料中除Mg、SiC和SiO2外,還含有MgO和Mg2Si,說明骨架在熔滲純Mg過程中,SiCw表面的SiO2與Mg發(fā)生了
圖3
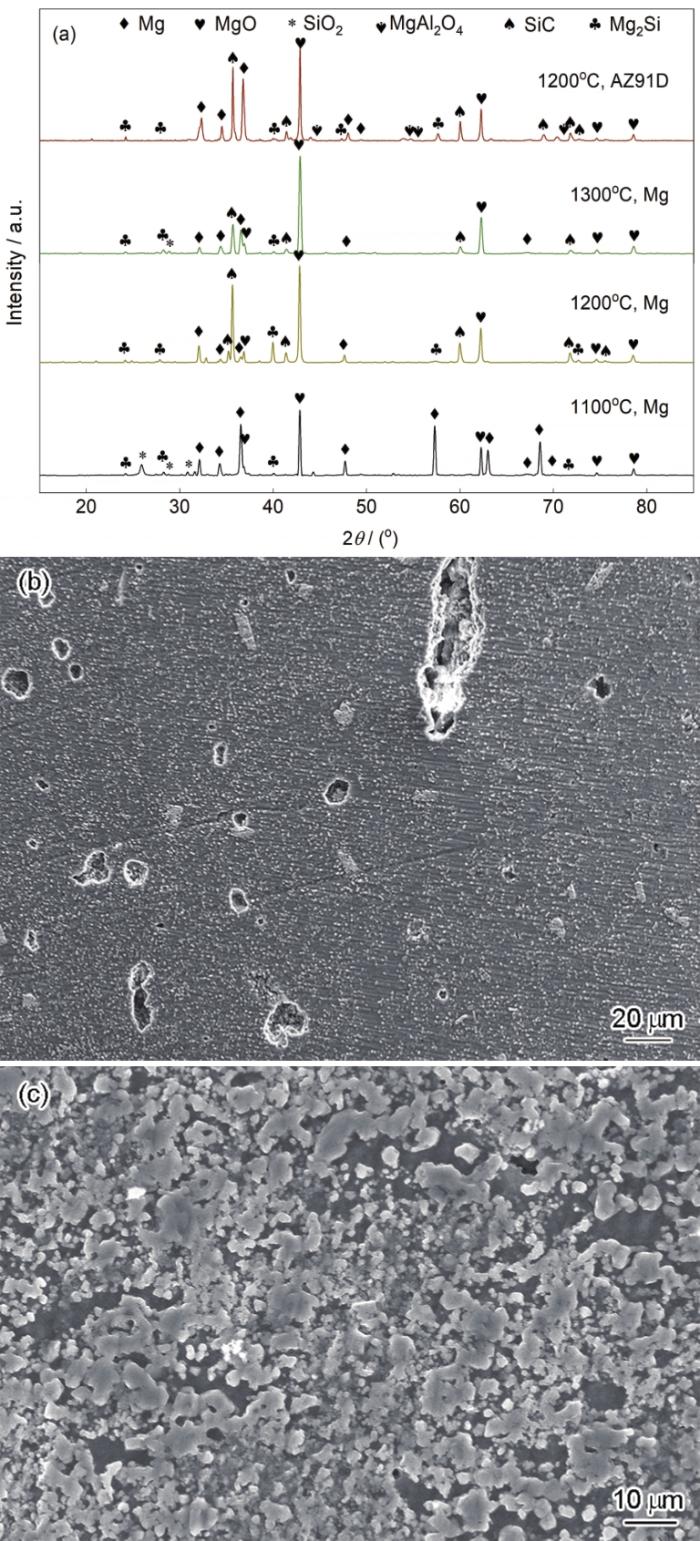
圖3 經(jīng)不同溫度預(yù)氧化處理的SiCw骨架熔滲純Mg和AZ91D鎂合金得到的復(fù)合材料的XRD譜以及對應(yīng)1100和1300℃預(yù)氧化溫度的復(fù)合材料的SEM像
Fig.3 XRD spectra of the SiCw/Mg composites fabricated by infiltrating pure Mg and AZ91D Mg alloy into the SiCw scaffolds that were pre-oxidized at different temperatures (a), and SEM images of the composites infiltrated with pure Mg into SiCw scaffolds pre-oxidized at 1100oC (b) and 1300oC (c)
圖4
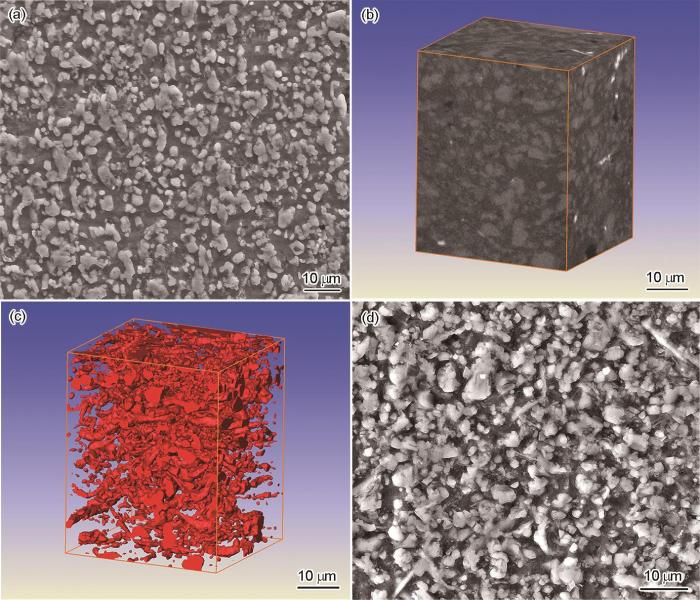
圖4 經(jīng)1200℃預(yù)氧化處理的SiCw骨架熔滲純Mg得到的復(fù)合材料的SEM像、XRT體積渲染圖和將Mg基體透明化后的SiCw增強(qiáng)相的XRT體積渲染圖,以及熔滲AZ91D鎂合金得到的復(fù)合材料的SEM像
Fig.4 SEM image (a) and XRT volume renderings (b) of the SiCw/Mg composite fabricated by infiltrating pure Mg into the SiCw scaffold pre-oxidized at 1200oC, XRT volume renderings of the SiCw scaffold within the composite after making the Mg matrix transparent (c), and SEM image of the composite infiltrated with AZ91D Mg alloy into the SiCw scaffold pre-oxidized at 1200oC (d)
基于上述結(jié)果,SiCw骨架的最佳預(yù)處理溫度選定為1200℃。在此基礎(chǔ)上,本工作選用強(qiáng)度更高、工程應(yīng)用更為廣泛的AZ91D鎂合金作為基體,將其熔滲入經(jīng)1200℃預(yù)氧化處理的SiCw骨架中制備得到了SiCw/AZ91D鎂合金復(fù)合材料。從XRD譜(圖3a)可以看出,該復(fù)合材料中除MgO和Mg2Si外,還含有MgAl2O4相,說明除了
利用Archimedes排水法測得經(jīng)1200℃預(yù)氧化處理的SiCw骨架熔滲純Mg和AZ91D鎂合金得到的復(fù)合材料的密度分別為(2.26 ± 0.05)和(2.45 ± 0.04) g/cm3,盡管與基體金屬相比有所增大,但相比鋁合金、鈦合金等常用的金屬結(jié)構(gòu)材料仍然較小,復(fù)合材料保留了輕質(zhì)的優(yōu)勢。
2.2 力學(xué)性能
圖5a為經(jīng)不同預(yù)氧化溫度處理的SiCw骨架熔滲得到的復(fù)合材料的典型彎曲應(yīng)力-應(yīng)變曲線。可以看出,對應(yīng)1100℃預(yù)氧化溫度的復(fù)合材料在(181 ± 5) MPa應(yīng)力處發(fā)生屈服,然后進(jìn)入加工硬化階段,在(237 ± 19) MPa應(yīng)力處發(fā)生斷裂。材料彎曲強(qiáng)度較低,但表現(xiàn)出一定的塑性變形能力,這與Mg基體相對含量較多有關(guān),并且材料內(nèi)部存在的微觀孔洞也限制了其強(qiáng)度。對應(yīng)1200和1300℃預(yù)氧化溫度的復(fù)合材料沒有發(fā)生塑性變形,而是在應(yīng)力達(dá)到最高點后瞬間斷裂。其中,對于1300℃預(yù)氧化溫度,復(fù)合材料的強(qiáng)度在122~244 MPa范圍內(nèi)表現(xiàn)出較大的分散性,這是由于材料中反應(yīng)產(chǎn)物較多,尺寸粗大并且相互連接,導(dǎo)致材料脆性偏大,對缺陷較為敏感,因而強(qiáng)度的穩(wěn)定性較差。與上述材料相比,對應(yīng)1200℃預(yù)氧化溫度的復(fù)合材料彎曲強(qiáng)度最大,為(316 ± 19) MPa,這是由于材料中不存在明顯的微觀孔洞等缺陷,并且增強(qiáng)相及反應(yīng)產(chǎn)物組織細(xì)小均勻。與純Mg相比,熔滲AZ91D鎂合金的復(fù)合材料表現(xiàn)出更高的彎曲強(qiáng)度,為(411 ± 13) MPa,但同樣沒有塑性變形,這是因為一方面AZ91D鎂合金強(qiáng)度比純Mg更高,另一方面復(fù)合材料中的脆性增強(qiáng)相與反應(yīng)產(chǎn)物更多。
圖5
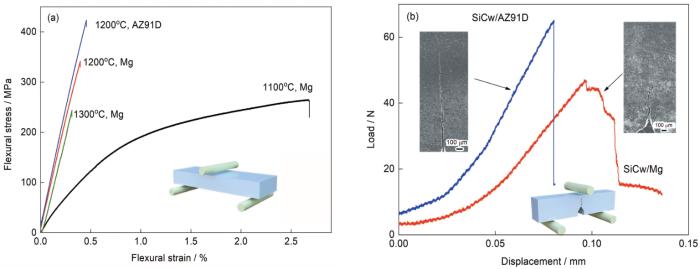
圖5 經(jīng)不同預(yù)氧化溫度處理的SiCw骨架熔滲純Mg和AZ91D鎂合金得到的復(fù)合材料的典型彎曲應(yīng)力-應(yīng)變曲線,以及對應(yīng)1200℃預(yù)氧化溫度的以純Mg和AZ91D鎂合金為基體的復(fù)合材料單邊缺口三點彎曲的典型載荷-位移曲線及裂紋擴(kuò)展形貌
Fig.5 Representative flexural stress-strain curves of the SiCw/Mg composites fabricated by infiltrating pure Mg or AZ91D Mg alloy into the SiCw scaffolds pre-oxidized at different temperatures (Inset shows the loading configuration of samples for flexural test) (a), representative load-displacement curves for single-edge notched bending tests for the composites infiltrated with pure Mg and AZ91D Mg alloy into SiCw scaffolds pre-oxidized at 1200oC (The insets show the representative SEM images of the samples with distinctly different crack propagation behaviors and the loading configuration of samples for toughness measurement) (b)
式中,
圖6
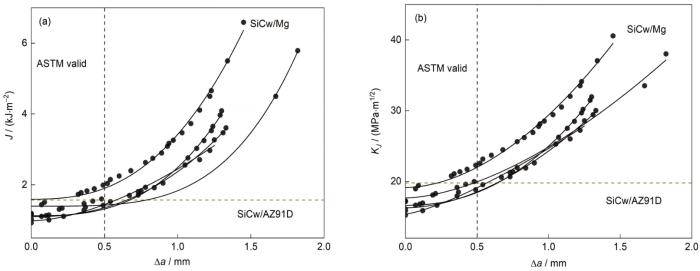
圖6 經(jīng)1200℃預(yù)氧化處理得到的以純Mg和AZ91D鎂合金為基體的SiCw/Mg復(fù)合材料的J積分和相對應(yīng)的應(yīng)力強(qiáng)度因子(
Fig.6 Curves of
由圖6可以看出,隨著裂紋的擴(kuò)展,復(fù)合材料的
圖7為經(jīng)1200℃預(yù)氧化處理得到的以純Mg為基體的復(fù)合材料側(cè)面的裂紋擴(kuò)展形貌以及斷后樣品的斷面形貌。可以看出,裂紋在擴(kuò)展過程中在微觀尺度上發(fā)生了連續(xù)的偏轉(zhuǎn),偏轉(zhuǎn)后的裂紋面兩側(cè)相互搭接形成橋聯(lián),在裂紋的張開過程中,構(gòu)成連接橋的SiCw與基體之間發(fā)生相對滑移(如圖7a中箭頭所示),并且逐漸從基體中拔出,從而能夠阻礙裂紋的張開與擴(kuò)展。同時,復(fù)合材料的斷面在微觀上凹凸不平,存在明顯的凹坑(如圖7b中箭頭所示),這是由于斷裂時SiCw從基體中拔出造成的,該過程也有助于消耗能量,阻礙裂紋擴(kuò)展和最終斷裂,從而提高復(fù)合材料的斷裂韌性。
圖7
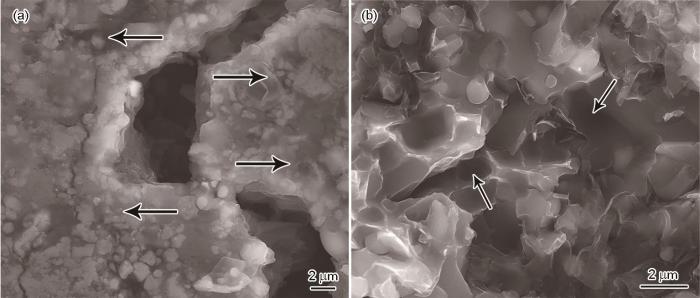
圖7 經(jīng)1200℃預(yù)氧化處理得到的以純Mg為基體的復(fù)合材料側(cè)面的裂紋擴(kuò)展形貌及斷后樣品的斷面形貌
Fig.7 SEM images of the SiCw/Mg composite corresponding to pre-oxidation temperature of 1200oC showing the tortuous cracking paths and the ligament bridges at crack faces on the lateral surface (The arrows indicate relative slip between SiCw and matrix at the crack faces) (a) and the micro dimples on the fracture surface caused by the pull-out of SiCw from the matrix (The arrows indicate the pull-out of SiCw from the matrix) (b)
3 分析討論
將SiCw在二維層面內(nèi)擇優(yōu)定向排列是本工作中構(gòu)筑微觀三維互穿結(jié)構(gòu)的關(guān)鍵,這里主要是通過分散在液態(tài)石蠟中的SiCw在重力作用下自發(fā)沉降以及后續(xù)的壓縮致密化來實現(xiàn)的。由于SiCw具有高的長徑比(≥ 20),在熔融石蠟中發(fā)生沉降時,SiCw長軸傾向于沿水平方向相互搭接進(jìn)行鋪層,從而實現(xiàn)一定的擇優(yōu)取向排列。在燒結(jié)前,沿垂直于層面方向?qū)iCw坯體進(jìn)行壓縮致密化處理,可以使SiCw長軸向?qū)用娣较蚱D(zhuǎn),從而進(jìn)一步促進(jìn)擇優(yōu)取向排列。將SiCw坯體中的石蠟去除并燒結(jié)后,SiCw骨架中形成了在三維空間中相互連通的微觀孔隙,熔滲時Mg或鎂合金填充這些孔隙,得到具有微觀三維互穿結(jié)構(gòu)的SiCw骨架增強(qiáng)鎂基復(fù)合材料。另外,在制備過程中,可以通過調(diào)節(jié)工藝參數(shù)對增強(qiáng)相的體積分?jǐn)?shù)加以調(diào)節(jié)。例如,在壓縮致密化處理過程中,通過增大壓力,可以提高增強(qiáng)相的體積分?jǐn)?shù),此外,通過升高骨架燒結(jié)溫度或延長燒結(jié)時間,也可以促使SiCw骨架燒結(jié)更加致密,從而提高最終得到的復(fù)合材料中增強(qiáng)相的體積分?jǐn)?shù)。復(fù)合材料中SiCw骨架強(qiáng)度高于Mg基體,相對較軟的基體和相對較硬的增強(qiáng)相在三維空間中均各自保持連續(xù),并且相互嵌鎖交錯排列,使得基體對增強(qiáng)相的粘結(jié)作用進(jìn)一步的增強(qiáng),提高SiCw骨架和Mg基體之間的摩擦力,有利于促進(jìn)應(yīng)力在各自相內(nèi)部以及兩相之間有效傳導(dǎo)[39,40],而SiCw的擇優(yōu)取向排列也有利于沿層面方向獲得較高的強(qiáng)化效率,使得復(fù)合材料的強(qiáng)度相比于基體得以明顯提高(鑄態(tài)純Mg和AZ91D鎂合金的彎曲強(qiáng)度分別約為95[41]和211 MPa[42])。
SiCw與Mg熔體之間的潤濕性對于利用熔滲工藝制備復(fù)合材料至關(guān)重要。研究[43]表明,SiC與Mg潤濕性有限,只有少量SiC可以作為初生Mg的異質(zhì)形核位點,因而表現(xiàn)出較差的潤濕性。本工作對SiCw骨架進(jìn)行預(yù)氧化處理,使SiCw表面生成一層SiO2薄膜,利用SiO2與基體Mg或AZ91D鎂合金熔體之間發(fā)生如
本工作中SiCw/Mg復(fù)合材料的斷裂韌性與其微觀三維互穿結(jié)構(gòu)密切相關(guān)。Somekawa和Mukai[46]通過對純Mg在不同溫度進(jìn)行擠出處理,得到的最高斷裂韌性為17.8 MPa·m1/2;而AZ91D鎂合金的強(qiáng)度高于同等狀態(tài)的純Mg,其擠壓鑄造態(tài)的斷裂韌性約為15 MPa·m1/2 [47]。本工作經(jīng)1200℃預(yù)氧化處理得到的復(fù)合材料中裂紋擴(kuò)展較為穩(wěn)定,表現(xiàn)出上升的R曲線行為,斷裂韌性可達(dá)19.6 MPa·m1/2,這是由于裂紋傾向于沿相對較軟的Mg基體相發(fā)生偏轉(zhuǎn),同時擇優(yōu)取向排列的SiCw在裂紋面兩側(cè)形成橋聯(lián),在裂紋擴(kuò)展過程中,這些連接橋與基體之間發(fā)生相對滑移并逐漸從基體中拔出,從而阻礙裂紋的張開與擴(kuò)展[48]。與微觀塑性變形等直接作用于裂紋尖端的材料本征增韌機(jī)制(intrinsic toughening mechanisms)[49]不同,裂紋偏轉(zhuǎn)、橋聯(lián)以及連接橋的拔出等微觀過程主要發(fā)生在裂紋尾部,屬于外在增韌機(jī)制(extrinsic toughening mechanisms)[49~51],在裂紋擴(kuò)展過程中,這些機(jī)制能夠承擔(dān)載荷并且消耗能量,從而對作用于裂紋尖端的外加應(yīng)力起到一定的屏蔽作用,降低裂紋尖端的有效應(yīng)力強(qiáng)度因子,從而提高復(fù)合材料的斷裂韌性。與純Mg相比,以AZ91D鎂合金為基體的復(fù)合材料盡管彎曲強(qiáng)度有所提高,但裂紋一開始擴(kuò)展便發(fā)生斷裂,沒有上升的R曲線行為,這是由于復(fù)合材料中界面反應(yīng)產(chǎn)物過多并發(fā)生粗化、連接,引起裂紋偏轉(zhuǎn)、橋聯(lián)等增韌機(jī)制失效,使得復(fù)合材料明顯脆化。
4 結(jié)論
(1) 利用SiCw在熔融石蠟中的重力輔助沉降以及后續(xù)的壓縮致密化處理,實現(xiàn)了SiCw在二維層面內(nèi)擇優(yōu)取向排列;通過對SiCw骨架預(yù)氧化處理,改善了SiCw與Mg基體之間的潤濕性,從而利用無壓熔滲方法獲得了致密的SiCw/Mg復(fù)合材料。
(2) SiCw骨架的最佳預(yù)氧化溫度為1200℃,該溫度處理得到的SiCw/Mg復(fù)合材料中沒有明顯的微觀孔洞等缺陷,同時避免了界面反應(yīng)產(chǎn)物過多以及粗化、連接,得到的復(fù)合材料表現(xiàn)出相對最高的彎曲強(qiáng)度,并且兼具一定的斷裂韌性。
(3) 經(jīng)1200℃預(yù)氧化處理得到的微觀三維互穿結(jié)構(gòu)SiCw/Mg復(fù)合材料中裂紋擴(kuò)展較為穩(wěn)定,表現(xiàn)出上升的R曲線行為,這是由于復(fù)合材料中存在裂紋偏轉(zhuǎn)、橋聯(lián)以及連接橋拔出等增韌機(jī)制,對作用于裂紋尖端的外加應(yīng)力起到一定的屏蔽作用,從而阻礙裂紋的擴(kuò)展。
(4) 與以純Mg為基體的復(fù)合材料相比,以AZ91D鎂合金為基體的復(fù)合材料中界面反應(yīng)產(chǎn)物過多并發(fā)生粗化、連接,因此盡管彎曲強(qiáng)度有所提高,但不存在裂紋偏轉(zhuǎn)、橋聯(lián)以及連接橋拔出等增韌機(jī)制,引起復(fù)合材料明顯脆化,沒有上升的R曲線行為。