分享:激光熔化沉積TiB2 增強TiAl基合金涂層的組織及力學性能
采用激光熔化沉積在TC4合金表面制備出不同TiB2含量(0、10%、20%、30%,質量分數)的TiAl基合金涂層,利用XRD、OM、SEM、顯微硬度計、壓痕法(斷裂韌性)、磨損試驗機以及激光共聚焦顯微鏡等,系統研究了TiB2含量對涂層微觀組織與力學性能的影響。結果表明,涂層組織由底部沿厚度方向依次為平面晶、柱狀晶和等軸晶,隨著TiB2含量增加,柱狀晶高度逐漸降低。TiB2/TiAl復合涂層由TiAl合金基體相(γ + α2)以及TiB2增強相組成,直接添加的TiB2顆粒大多沒有熔化,但直接添加的TiB2顆粒外層與TiAl合金熔體發生溶解反應后原位析出初生TiB2和次生TiB2,初生TiB2呈塊狀,次生TiB2呈短棒狀和條帶狀。隨著TiB2含量由0增加至10%,涂層基體組織明顯細化,但繼續增加TiB2含量(20%、30%)并未產生進一步的細化作用。隨著TiB2含量由0增加至30%,涂層的表面硬度由530.5 HV增加至738.4 HV,斷裂韌性由7.75 MPa·m1/2降低至3.17 MPa·m1/2,磨損率由3.98 mg/mm2減少至0.42 mg/mm2,并且磨損面的磨損程度及其粗糙度也隨之降低。未添加TiB2時,涂層的磨損機制以顯微切削為主,多次塑性變形為輔;TiB2含量為10%時,涂層的磨損機制以顯微切削為主,微觀斷裂為輔;隨著TiB2含量增加,磨損機制逐漸轉向微觀斷裂;TiB2含量為30%時,涂層的磨損機制以微觀斷裂為主,顯微切削為輔。
關鍵詞:
TiAl基合金(TiAl基金屬間化合物)具有低密度、高比強度、耐腐蝕、優異的抗氧化以及抗蠕變等特性,是一種極具競爭力的新型輕質高溫結構材料,在航空航天、汽車工業等領域的應用潛力巨大[1,2]。然而TiAl基合金的室溫和高溫脆性大,難以加工成形,是限制其作為結構材料大規模推廣應用的主要瓶頸[3]。值得注意的是,采用表面工程技術在基材表面制備TiAl基合金涂層,即能充分發揮TiAl基合金的性能優勢,顯著提高基材表面耐高溫、耐腐蝕等性能,又能克服TiAl基合金加工困難的問題,是一種有效的應用途徑。目前制備TiAl基合金涂層的方法主要有:磁控濺射[4]、離子注入[5]、等離子噴涂[6]、電火花沉積[7]等。上述方法雖然拓展了TiAl基合金的應用領域,但也存在自身的局限性:磁控濺射和離子注入制備的涂層只能達到微米級,僅適合精密零件;等離子噴涂制備的涂層存在孔隙、夾雜、微裂紋等缺陷,并且與基材為機械結合,結合力較低;電火花沉積層的表面質量不易控制,工藝不穩定,生產效率尚有待提高。激光熔化沉積作為一種先進的表面強化技術,具有稀釋率低、組織致密且細小、基材變形小、涂層與基材結合強度高、粉末成分容易調節等優點[8],因此采用激光熔化沉積制備TiAl基合金涂層具有重要的研究價值和廣闊的應用前景。Carrullo等[9]利用激光熔化沉積在TC4合金表面制備出Ti-48Al-2Nb-2Cr (原子分數,%)合金涂層,涂層的高溫抗氧化能力相較于基材提高10倍。
隨著TiAl基合金激光沉積涂層應用的逐步開展,將不可避免地涉及到潤滑、摩擦和磨損等問題。但是,TiAl基合金涂層的耐磨性能較差,難以在惡劣、復雜的工況條件下長期服役[10],因此提高TiAl基合金涂層的耐磨性能顯得尤為重要。在TiAl基合金中引入硬質相可以有效提高材料的耐磨性能以及力學性能。例如,He等[11]通過在TiAl基合金中添加TiC硬質相的方法,顯著提高了合金的硬度和耐磨性。眾所周知,TiB2陶瓷硬質相具有硬度高、摩擦系數低、化學穩定性好等特點,并且TiB2與TiAl基合金具有相近的密度和熱膨脹系數以及良好的相容性[10],同時B元素又能顯著細化TiAl基合金的晶粒尺寸,因此TiB2是TiAl基合金復合材料中最具吸引力的硬質相之一。Cheng等[12]采用粉末冶金法制備TiB2/TiAl復合材料,隨著TiB2含量增加,其耐磨性能也隨之增加。然而截止目前,關于激光熔化沉積制備TiB2/TiAl基合金復合材料的研究尚未見報道,因此本工作以Ti-48Al-2Nb-2Cr合金作為基體材料,利用激光熔化沉積在TC4合金表面制備TiB2增強TiAl基合金復合涂層,為進一步探索TiAl基合金復合材料在表面工程中的應用提供理論參考和實驗范例。
1 實驗方法
沉積材料由Ti-48Al-2Nb-2Cr預合金粉末和TiB2顆粒組成,混合粉末中TiB2的加入量分別為0、10%、20%、30% (質量分數)。Ti-48Al-2Nb-2Cr預合金粉末采用電極感應熔煉氣霧化法制備,形狀主要為球形(見圖1a),粒徑范圍53~150 μm;TiB2顆粒為不規則的塊狀(見圖1b),粒徑范圍45~75 μm。基材為TC4合金,基材表面經砂紙逐級打磨后,用無水酒精和丙酮清洗以去除油污。實驗前將混合均勻的復合粉末以及基材放入100℃的干燥箱中烘干0.5 h,去除水分。
圖1

圖1 TiAl合金粉末和TiB2顆粒的SEM像
Fig.1 SEM images of TiAl powders (a) and TiB2 particles (b)
激光熔化沉積設備由六軸聯動機器人、IPG-YLS-6000光纖激光器、DPSF-2雙筒四路同軸送粉器、控制系統以及水冷系統等組成,其中IPG-YLS-6000光纖激光器的最大功率6 kW,波長1070 nm,保護氣和送粉氣均為高純Ar氣,沉積參數為:激光功率1400 kW,掃描速率5 mm/s,送粉率15.6 g/min,送粉氣流量為7 L/min,保護氣流量為15 L/min,預熱溫度為350℃。
用線切割切取金相試樣,試樣經磨光、拋光、Kroll試劑腐蝕后,在GX51型金相顯微鏡(OM)上分析涂層形貌。采用GeminiSEM 300型掃描電子顯微鏡(SEM)觀察試樣的微觀組織,并使用能譜儀(EDS)對涂層微區成分進行分析。物相結構分析在D8 Advance型X射線衍射儀(XRD)上完成。使用EM500-2A型顯微硬度計測量涂層截面的硬度分布,載荷500 g,持續時間10 s,同一深度的區域隨機選取3個點,取平均值。采用Vickers硬度壓痕法在涂層截面上誘發裂紋,載荷為30 kg,通過測量裂紋長度間接計算涂層的斷裂韌性[13]:
式中,KIC為斷裂韌性(MPa·m1/2),HV為Vickers硬度(N/mm2),FV為載荷(N),??L為4個壓痕尖角的裂紋總長度(mm)。通過
涂層的二體磨粒磨損實驗在ML-100型銷盤式磨損試驗機上進行,試樣直徑3 mm,載荷7 N,轉速120 r/min,進給量2 mm/r,磨損時間5 min,對磨材料為80 μm砂紙。使用FA2004型電子天平(精度0.1 mg)精確測量磨損失重量,同一成分涂層共進行3次磨損實驗,以磨損率評價涂層的耐磨性能:
式中,ω為磨損率(mg/mm2),m0為磨損前的質量(mg),m1為磨損后的質量(mg),s為磨損面積(mm2)。
采用Quanta650型掃描電鏡(SEM)觀察磨損形貌,分析磨損機理;采用VL2000DX-SVF17SP型3D激光共聚焦顯微鏡表征磨損表面的三維形貌,并計算粗糙度。
2 實驗結果與分析
2.1 涂層的物相結構
圖2為不同TiB2含量涂層的XRD譜。TiAl合金涂層主要由γ-TiAl相以及α2-Ti3Al相組成。添加TiB2后,復合涂層由TiAl合金基體相(γ + α2)以及TiB2相組成,在XRD的測試精度內沒有發現其他物相。隨著TiB2含量增加,TiB2衍射峰的強度逐漸增加,基體相(γ + α2)衍射峰的強度逐漸減弱,這說明TiB2含量增加,致使基體相(γ + α2)的相對含量不斷降低。
圖2

圖2 不同TiB2含量涂層的XRD譜
Fig.2 XRD spectra of coatings with different TiB2 contents
2.2 涂層中部的微觀組織
由TiAl合金涂層中部的OM像(圖3a)和背散射電子像(圖3b)可以看出,其微觀組織為樹枝晶,由白色枝晶組織和灰色枝晶間組織構成。添加TiB2顆粒后(圖4),復合涂層的微觀組織由TiAl合金基體相和不同形態的第二相組成,基體組織由粗大的樹枝晶轉變為尺寸較小的等軸晶,晶粒尺寸明顯細化,第二相形態主要包括尺寸不同的塊狀(尺寸在20~75 μm之間的大塊標記為A,尺寸在2~10 μm之間的小塊標記為B)、短棒狀(標記為C)以及彎曲的條帶狀(標記為D),并且隨著TiB2含量增加,第二相數量也逐漸增加。對上述第二相分別進行EDS分析,結果見表1。綜合EDS和XRD結果(圖2)可知,這些第二相為TiB2。大塊TiB2的尺寸(20~75 μm)和形狀接近原始顆粒,這說明在激光沉積條件下直接添加的TiB2顆粒大多沒有熔化。TiB2顆粒的熔點(3225℃)和熔化焓(83.94 kJ/mol)均較高,在激光束短暫的輻射過程中難以被迅速熔化。但是直接添加的TiB2顆粒的外層可以與TiAl合金熔體發生溶解反應[14]:TiAl合金熔體(L) + β + TiB2↔L + β (0.5%TiB2,1485℃),L + TiB2 ↔ L (1%TiB2,1600℃),使得溶解出來的Ti和B進入熔體。B在TiAl合金中的固溶度極低,在γ相和α相中的固溶度分別為0.011%和0.003%[15] (原子分數,后文所有元素含量均為原子分數),所以B在TiAl合金中大多以硼化物的形式存在,主要包括TiB和TiB2。TiAl合金中硼化物的類型與Al含量密切相關,當Al含量≤ 44%時,形成TiB,隨著B含量增加,硼化物由TiB逐漸向TiB2過渡,當Al含量> 44%時,僅形成TiB2[16]。本工作采用的TiAl合金屬于后一種情況,因此TiB2顆粒發生溶解反應后再次析出的硼化物為TiB2。綜上所述,塊狀(2~10 μm)、短棒狀及條帶狀TiB2從尺寸和形貌上都明顯區別于直接添加的TiB2顆粒,因此可以推斷其為“溶解-再析出”機制下原位合成的產物。
圖3
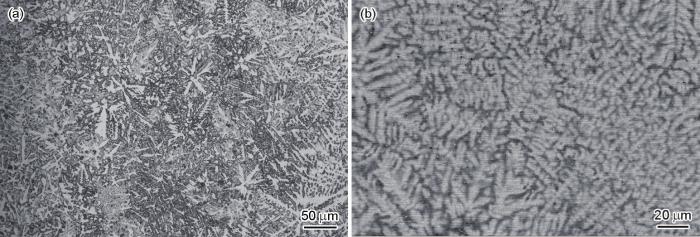
圖3 TiAl合金涂層中部的顯微組織
Fig.3 OM (a) and back-scaterred electron (BSE) (b) images of middle region of the TiAl alloy coating
圖4

圖4 不同TiB2含量涂層截面中部的背散射電子像
Fig.4 Low (a-c) and high (d-f) magnified BSE images of middle region of coatings with 10% (a, d), 20% (b, e), and 30% (c, f) TiB2
表1 圖4復合涂層中第二相的EDS結果 (atomic fraction / %)
Table 1
Mass fraction of TiB2 / % |
Position | Ti | B* |
---|---|---|---|
10 | A | 20.82 | 79.18 |
B | 18.74 | 81.26 | |
C | 15.76 | 84.24 | |
D | 14.99 | 85.01 | |
20 | A | 15.87 | 84.13 |
B | 17.75 | 82.25 | |
C | 16.84 | 83.16 | |
D | 15.81 | 84.19 | |
30 | A | 14.73 | 85.27 |
B | 15.44 | 84.56 | |
C | 17.69 | 82.31 | |
D | 16.14 | 83.86 |
TiB2為六方晶系,在理想狀態下生長成以(0001)為底面、{1010}為棱面的六棱柱狀形貌[17]。而本工作所得原位生成TiB2的形態呈現塊狀、短棒狀及條帶狀,這主要歸因于Ti-Al-B合金的成分以及激光熔化沉積的快速凝固過程。本工作所選基體合金的初生相為β相,其凝固路徑為[18]:L → L + β → α → α + γ → α2 + γ。根據Ti-Al-B三元相圖液相面的部分投影圖[16]可知,Ti-Al-B合金熔體在降溫過程中會發生共晶反應:L → β + TiB2,由于本工作所選基體合金的Al含量為48%,因此平衡條件下基體合金發生上述共晶反應的B含量大致為1%。在實際凝固過程中,TiB2/TiAl復合涂層激光熔池中總是存在成分起伏、結構起伏以及能量起伏。由前文可知,直接添加的TiB2顆粒外層會與TiAl合金熔體發生溶解反應,釋放出的B原子不斷進入TiAl合金熔體。凝固初期,由于熔體中B含量較高,并且B在TiAl合金熔體中擴散能力較差,極易在固/液界面前沿富集[19],此時容易析出初生TiB2。這些形核較早的初生TiB2晶核具有較長的生長時間,并且周圍的溫度梯度、溶質條件等動力學因素較為穩定,生長環境近似自由生長,其生長形態主要由TiB2的晶體結構決定,因此生長成近似六棱柱狀形貌,其斷面呈塊狀(圖4中的B)。隨著凝固的進行,B原子不斷被消耗,當B含量降低至1%時,發生共晶反應L → β + TiB2,析出次生TiB2,次生TiB2與基體β相共同耦合生長,其生長受到β相的限制,最終形成短棒狀(圖4中的C)和條帶狀(圖4中的D)。研究[16]表明,在快速冷卻條件下,TiAl合金中的TiB2多呈現彎曲的條帶狀,因此涂層中條帶狀TiB2的出現與激光熔化沉積的快速凝固過程也密不可分。綜上所述,TiB2/TiAl復合涂層中TiB2的析出路徑為:L→L +初生TiB2→初生TiB2 + β +次生TiB2,在此路徑下,初生TiB2在熔池中自由生長,呈現塊狀;熔池中剩余的B原子以次生TiB2的形式與β相共同耦合生長,呈現短棒狀和條帶狀。
對比TiAl合金組織(圖3b)和TiB2/TiAl復合涂層的基體組織(圖4a~c)可以看出,隨著TiB2含量由0增加至10%,復合涂層中部的基體組織由粗大的樹枝晶轉變為尺寸較小的等軸晶,晶粒明顯細化,但繼續增加TiB2含量(20%、30%)并未產生進一步的細化作用。Han等[20]在研究真空電弧爐制備不同含量TiB2的TiAl合金時也發現類似現象,并認為TiB2對TiAl合金的細化作用存在一個閾值,當TiB2含量低于閾值時,沒有明顯的細化作用,當TiB2含量超過閾值時,晶粒細化明顯,但TiB2含量繼續增加對晶粒的影響不大。分析認為,本工作中TiB2顆粒細化TiAl合金的機制主要包括:(1) TiB2與β相之間的錯配度為11%,TiB2作為β相異質形核核心的有效性為中等[21]。未熔化的TiB2以及初生TiB2領先于β相存在于熔池中,在凝固過程中可以有效提高β相的形核率,起到細化晶粒的作用。(2) 次生TiB2與β相共同耦合生長,次生TiB2對β相的長大具有阻礙作用,進一步細化了晶粒。(3) B在TiAl合金熔池中緩慢的擴散速率以及B在固、液兩相中溶解度的差異,導致B容易在固/液界面前沿產生成分過冷[19],并在固/液界面前沿聚集形成富B的邊界層,該邊界層能夠阻礙β相晶粒長大,進而細化組織。
2.3 涂層界面附近的微觀組織
圖5為不同TiB2含量涂層界面附近的OM像。可以看出,4種涂層的組織致密,未發現裂紋、氣孔等冶金缺陷,基材與涂層之間存在一條連續的白亮結合帶,結合帶下方為TC4合金基材的熱影響區,上方為涂層的柱狀晶區,基材與涂層實現了良好的冶金結合。由于激光熔化沉積特殊的快速加熱、快速冷卻特點,涂層組織形態呈現明顯快速凝固生長特征,由底部沿厚度方向依次為平面晶、柱狀晶和等軸晶。根據凝固理論[22],涂層的組織形態受控于溫度梯度(G)與生長速率(R)之比(G / R)。熔池底部,由于基材的激冷作用,使得G極大,但該處的瞬時R趨近于零,因此G / R極大,晶體以穩定的平面狀態生長,進而形成平面晶;隨著凝固的進行,熔池的G逐漸減小,R逐漸增大,G / R逐漸降低,并且溶質元素富集導致成分過冷區域不斷擴大,致使組織形態逐漸轉變為柱狀晶甚至等軸晶。
圖5
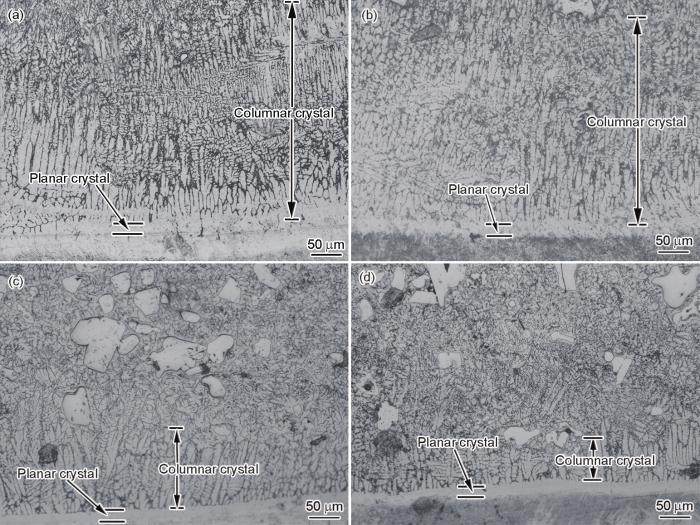
圖5 不同TiB2含量涂層界面附近的OM像
Fig.5 OM images near the interface of coatings with different TiB2 contents
(a) 0 (b) 10% (c) 20% (d) 30%
由圖5還可以看出,隨著TiB2含量增加,界面附近柱狀晶高度逐漸降低。究其原因:(1) 隨著TiB2含量增加,未熔化的TiB2以及初生TiB2數量增加,異質形核作用增強,等軸晶數量上升。當大量等軸晶位于柱狀晶前沿時,能夠阻礙柱狀晶生長,促進柱狀晶轉變為等軸晶[23]。(2) 隨著TiB2含量增加,熔池中B含量升高,使得液相中更多的B被排斥到固/液界面前沿,造成溶質濃度增加,成分過冷區域擴大,晶體自由生長能力增強,以致柱狀晶不能持續長大而在尖端出現分叉,逐漸轉變為等軸晶。(3) 隨著TiB2含量增加,涂層與基材間的G減小,G / R降低,弱化了柱狀晶的生長趨勢。激光沉積過程中涂層與基材間的G可以表示為[24]:
式中,K為材料的熱導率,T為熔體的液相線溫度,T0為基材溫度,η為激光吸收率,P為激光功率。隨著TiB2含量增加,在相同工藝參數下熔化相同厚度涂層所需要的激光能量降低,使得熔池溫度上升,T0也隨之升高,進而導致G降低(
2.4 TiB2 含量對涂層顯微硬度的影響
圖6為不同TiB2含量涂層截面顯微硬度分布曲線。可見,硬度由涂層至基材呈現階梯式分布,分別對應涂層、熱影響區以及基材。隨著TiB2含量增加,涂層硬度逐漸增加,其中表面硬度由530.5 HV增加至738.4 HV。分析認為,其強化機理主要包括:(1) Orowan強化,不同形態的TiB2分布在TiAl合金基體上可以阻礙位錯運動,導致位錯在增強相附近形成堆積和纏結,使得位錯開動的外應力增加,硬度得以提高;(2) 細晶強化,添加TiB2顆粒后,基體合金的晶粒明顯細化。依據Hall-Petch效應,晶粒越小,晶界越多,合金硬度也越高。此外,從圖6可以看出,TiB2/TiAl復合涂層的硬度均出現一定幅度的波動,而TiAl合金涂層的硬度卻相對平穩,這主要歸因于TiB2在復合涂層深度方向上分布的不均勻。
圖6

圖6 不同TiB2含量涂層截面的顯微硬度
Fig.6 Microhardness distributions of coatings with different TiB2 contents
2.5 TiB2 含量對涂層斷裂韌性的影響
圖7為載荷30 kg下不同TiB2含量涂層壓痕的形貌。壓痕裂紋長度采用IPP軟件進行統計,并利用
圖7
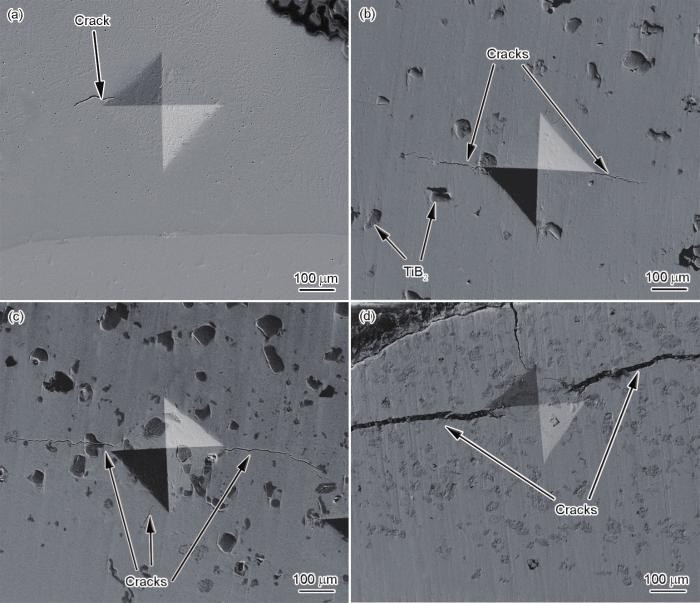
圖7 不同TiB2含量涂層的壓痕形貌
Fig.7 Indentation morphologies of coatings with different TiB2 contents
(a) 0 (b) 10% (c) 20% (d) 30%
表2 不同TiB2含量涂層的斷裂韌性(壓痕法)
Table 2
Mass fraction of TiB2 / % | Average crack length / mm | Fracture toughness / (MPa·m1/2) |
---|---|---|
0 | 0.195 | 7.75 |
10 | 0.545 | 5.02 |
20 | 1.204 | 3.49 |
30 | 1.672 | 3.17 |
2.6 TiB2 含量對涂層耐磨性的影響
2.6.1 TiB2含量對磨損率的影響
圖8為不同TiB2含量涂層的磨損率。可見,隨著TiB2含量增加,涂層的磨損率逐漸降低。未添加TiB2時,涂層中不含硬質相,無法有效阻礙磨粒的切削作用,耐磨性較差,磨損率高達3.98 mg/mm2。隨著TiB2含量增加,涂層中硬質相數量增加,硬質相在二體磨粒磨損過程中可以充當耐磨骨架的作用,有效抵抗磨粒的切削作用,耐磨性能顯著提高,TiB2含量為30%時,涂層的磨損率降低至0.42 mg/mm2,僅為TiAl合金涂層磨損率的11%,展現出優異的耐磨性能。
圖8

圖8 不同TiB2含量涂層的磨損率
Fig.8 Wear rates of coatings with different TiB2 contents
2.6.2 TiB2含量對磨損機制的影響
圖9為不同TiB2含量涂層的磨損形貌。圖9a為TiAl合金涂層的磨損形貌,磨損面存在大量連續平行且深而寬的犁溝,部分犁溝邊緣出現層狀折痕(如箭頭所示),這說明涂層以顯微切削為主,多次塑性變形為輔。當磨粒以滑動方式劃過合金表層時,由于涂層硬度較低且沒有硬質相的保護,磨粒在壓應力與切應力的共同作用下,容易在涂層表面產生推擠變形和碾壓變形,形成犁溝狀磨損劃痕。此外,由于磨粒的反復磨損與加載,材料的加工硬化效應不斷增加,當材料無法通過塑性變形吸收能量時便會誘發裂紋,在隨后的磨損過程中裂紋擴展導致材料脫離磨損面產生磨屑,同時在犁溝邊緣形成層狀折痕,層狀折痕是多次塑性變形后的典型形貌。
圖9

圖9 不同TiB2含量涂層的磨損形貌
Fig.9 Wear morphologies of coatings with different TiB2 contents
(a) 0 (b) 10% (c) 20% (d) 30%
對比圖9b~d可以發現,隨著TiB2含量增加,犁溝的數量、深度以及寬度逐漸減小,犁溝邊緣并未出現層狀折痕,但磨損面均出現剝落坑,這表明TiB2/TiAl復合涂層的磨損機制為顯微切削和微觀斷裂,而不存在多次塑性變形。上述剝落坑的尺寸和形狀接近未熔化的TiB2顆粒,并且數量隨著TiB2含量的升高而增加,這說明磨粒磨損條件下產生的剝落坑與未熔化的TiB2顆粒密切相關。為了探明剝落坑是否歸因于未熔化TiB2顆粒的斷裂或剝落,對磨粒磨損條件下出現的剝落坑進行高倍SEM觀察,如圖10所示。可見,剝落后的區域形成了較深的孔洞,未發生剝落的表面沒有明顯劃痕,也未發生塑性變形,斷口為平整的小平面(I處)。對未發生剝落的表面(I處)進行EDS分析發現,其具體成分(原子分數)為:Ti 23.23%,B 76.77%。綜上可以判定剝落坑的產生主要歸因于未熔化TiB2顆粒與基體的剝離,少數是由于顆粒本身的脆性斷裂。TiB2的硬度和耐磨性均大于基體,基體率先被磨損,導致TiB2凸出于基體,在后續的磨損過程中充當耐磨骨架的作用。首先,未熔化的TiB2顆粒是直接添加進去的,與基體的界面處存在較多缺陷,結合強度較低,在磨損過程中容易在界面處誘發微裂紋,導致未熔化的TiB2與基體發生剝離形成剝落坑,而原位析出的TiB2與基體的界面純凈,且存在固定的取向關系,結合強度較高[20],在磨損的過程中很難發生剝離。其次,未熔化的TiB2顆粒為硬脆相,在磨粒反復的磨削作用下,容易萌生微裂紋,裂紋擴展后發生脆性斷裂形成剝落坑。
圖10

圖10 磨粒磨損條件下產生的剝落坑的高倍形貌
Fig.10 High power morphology of the spalling pit produced by abrasive particles under abrasive conditions
研究[26]表明,材料發生顯微切削磨損時,磨損率與硬度呈負相關,磨損率與硬度之間的關系為[26]:
式中,WC為顯微切削造成的磨損率,FN為載荷,θ為圓錐形磨粒尖角角度的一半,
式中,WF為微觀斷裂造成的磨損率,d為磨粒直徑。
綜上所述,TiB2/TiAl復合涂層的磨粒磨損過程是顯微切削和微觀斷裂共同作用的結果,復合涂層由于TiB2含量的不同而導致其硬度和斷裂韌性有所差異,因此2種磨損機制所占權重也不同。TiB2含量為10%時,涂層具有低硬度、高斷裂韌性的特點,因而磨損機制以顯微切削為主,微觀斷裂為輔;隨著TiB2含量增加,涂層硬度增加,斷裂韌性降低,因此顯微切削造成的磨損減少,微觀斷裂造成的磨損增加,磨損機制轉向微觀斷裂;TiB2含量為30%時,涂層的磨損機制以微觀斷裂為主,顯微切削為輔。
由前文分析可知,TiB2含量是決定復合涂層耐磨性的關鍵因素。其原因是:(1) 硬度是衡量耐磨材料的一項重要指標,擁有更高硬度的材料通常具有更優異的耐磨粒磨損性能[26],隨著TiB2含量增加,涂層硬度逐漸增加,使得磨粒難以刺入復合涂層表面進行犁削運動,磨損程度隨之降低;(2) TiB2具有較高的硬度和耐磨性,鑲嵌在基體上可以阻礙磨粒的壓入與切削,承擔主要的載荷,起到耐磨骨架的作用,避免大量磨粒與基體的直接接觸,降低2者之間的接觸面積,減少磨粒對基體的磨損。TiB2的耐磨骨架作用與其平均間距密切相關。當TiB2含量較低時,TiB2的平均間距大于磨粒尺寸,磨粒容易刺入合金表面,進行長距離的犁削運動,形成大量深而寬的犁溝,隨著TiB2含量增加,其分布更加均勻,平均間距也進一步減小,使得磨粒難以刺入合金表面,即使部分鋒利且迎角合適的磨粒刺入合金表面,在其犁削一段距離后便會遇到堅硬的TiB2,迫使其離開犁溝,從而抑制犁溝的進一步擴展,顯著降低磨損率。
2.6.3 TiB2含量對磨損面粗糙度及其三維形貌的影響
利用3D激光共聚焦顯微鏡觀察涂層磨損后的表面形貌,并計算粗糙度Ra和Rz,用于表征磨損程度(其中,Ra為輪廓算術平均偏差粗糙度,反映輪廓偏離基準面的程度,常用于表示表面粗糙度;Rz為輪廓微觀不平度10點高度,即測量范圍內5個最大輪廓谷深yvi與5個最大輪廓峰高ypi的平均值之和,反映輪廓的最大高度[28])。一般而言,Ra和Rz數值越小,說明磨損表面越光滑,磨損程度越小。不同TiB2含量涂層的Ra和Rz見圖11。可以看出,TiB2含量為0時,Ra和Rz最大,分別達到3.797和77.256 μm,磨損程度最為嚴重;隨著TiB2含量增加,Ra和Rz數值逐漸減小,磨損程度逐漸降低,TiB2含量為30%時,Ra和Rz分別降低至2.067和19.110 μm,磨損程度最小,與前文磨損實驗結果相吻合。
圖11

圖11 不同TiB2含量涂層磨損表面的粗糙度
Fig.11 Roughnesses of wear surface of coatings with different TiB2 contents (Ra—contour arithmetic mean deviation, Rz—ten-point height average)
為了更加直觀地反映磨損形貌,采用3D激光共聚焦顯微鏡對磨損表面的三維形貌進行表征,結果見圖12。紅色代表磨損輪廓的峰高區域,藍色代表磨損輪廓的谷深區域,顏色差異越大,表示磨損程度越嚴重。可見,隨著TiB2含量增加,磨損面的顏色差異逐漸減小,磨損程度逐漸降低,這說明復合涂層中的TiB2可以有效抵抗磨粒的切削作用,顯著提升TiAl合金的耐磨性能。
圖12

圖12 不同TiB2含量涂層磨損表面的3D形貌
Fig.12 3D morphologies of wear surface of coatings with different TiB2 contents
(a) 0 (b) 10% (c) 20% (d) 30%
3 結論
(1) 采用激光熔化沉積在TC4合金表面成功制備出TiB2/TiAl復合涂層,涂層組織形態由底部沿厚度方向依次為平面晶、柱狀晶和等軸晶,隨著TiB2含量增加,柱狀晶高度逐漸降低。
(2) TiB2/TiAl復合涂層由TiAl合金基體相(γ + α2)以及TiB2增強相組成,直接添加的TiB2顆粒大多沒有熔化,但直接添加的TiB2顆粒外層與TiAl合金熔體發生溶解反應后原位析出初生TiB2和次生TiB2,其析出路徑為:L→L +初生TiB2→初生TiB2 + β + 次生TiB2,初生TiB2在熔池中自由生長,呈現塊狀,次生TiB2與β相進行耦合生長,呈現短棒狀和條帶狀。
(3) 隨著TiB2含量由0增加至10%,涂層中部的基體組織由粗大的樹枝晶轉變為尺寸較小的等軸晶,晶粒明顯細化,但繼續增加TiB2含量(20%、30%)并未產生進一步的細化作用。
(4) 隨著TiB2含量由0增加至30%,涂層的表面硬度由530.5 HV增加至738.4 HV,斷裂韌性由7.75 MPa·m1/2降低至3.17 MPa·m1/2,磨損率由3.98 mg/mm2減少至0.42 mg/mm2,并且磨損面的磨損程度及其粗糙度也隨之降低。
(5) 未添加TiB2時,涂層的磨損機制以顯微切削為主,多次塑性變形為輔;TiB2含量為10%時,涂層的磨損機制以顯微切削為主,微觀斷裂為輔;隨著TiB2含量增加,磨損機制逐漸轉向微觀斷裂;TiB2含量為30%時,涂層的磨損機制以微觀斷裂為主,顯微切削為輔。
來源--金屬學報