分享:冷軋變形對高性能Cu-Ni-Si合金組織性能與析出行為的影響
王長勝1,2, 付華棟,1,2,3, 張洪濤1,2, 謝建新
,1,2,3
1
2
3
采用DSC、TEM、導電率和力學性能等測試方法,研究了不同冷軋變形量對Cu-3.0Ni-0.60Si-0.16Zn-0.15Cr-0.03P (質量分數,%)合金組織性能與析出行為的影響,旨在通過工藝調控提升該合金的綜合性能。通過對比不同冷軋變形后合金的開始析出溫度和再結晶溫度以及時效后合金的組織性能,確定了高性能Cu-Ni-Si系合金的形變-時效工藝參數,明確了冷軋變形量對合金時效析出動力學的影響規律和強化相析出的調控機制;合金經過95%冷軋+ 450℃、60 min形變熱處理后獲得了顯著優于現有Cu-Ni-Si合金(如C70250)的性能,其抗拉強度為(841 ± 10) MPa,導電率為(52.2 ± 0.3)%IACS。
關鍵詞:
隨著集成電路制程和芯片封裝技術的快速進步,電子信息等戰略新興產業對下一代銅合金引線框架材料性能提出抗拉強度不小于800 MPa、導電率不低于50%IACS (IACS—international annealed copper standard)的要求[1~3]。Cu-Ni-Si系合金通過納米級δ-Ni2Si相的時效析出可獲得較高的強度與導電率,是集成電路引線框架用典型材料[4~9]。為滿足下一代銅合金引線框架材料更高性能的需求,研究者們通常采用微合金化[10,11]和優化形變熱處理工藝等[12,13]方法來促進合金析出相析出、調控析出相的形貌和分布,從而達到提高Cu-Ni-Si系合金的強度和導電率綜合性能的目的[12]。
在微合金化研究方面,Chen等[15]通過添加0.2% (質量分數)的Zn促進了Ni2Si相的析出,增強了析出強化效應并改善了釬焊界面性能;Zhang等[16]添加0.03% (質量分數)的P不僅凈化了Cu-Ni-Si基體,還能抑制析出相粗化,Ni3P相的析出同時提高了合金導電率和強度;Wang等[17]研究表明適量的Cr元素能與Si元素在時效時形成Cr3Si析出相,與δ-Ni2Si協同強化銅合金的同時提高合金導電率;彭麗軍等[18]、Xiao等[19]和馮桄波等[20]研究均發現Co能與Ni、Si形成(Ni, Co)2Si相,并能抑制時效過程中的調幅分解,加速第二相的析出,極大地提高Cu-Ni-Si合金的強度。另一方面,為解決微合金化元素選擇和含量確定等難題,本文作者等[21]提供了一種基于機器學習方法的解決思路,開發出機器學習設計系統(machine learning design system,MLDS)并以抗拉強度800 MPa、50%IACS為目標性能設計出了高性能的Cu-3.0Ni-0.6Si-0.16Zn-0.15Cr-0.03P (質量分數,%,下同)合金。
在形變熱處理工藝研究方面,形變強化與析出強化相結合可達到協同強化的目的[22~29]。Sun等[30]采用雙級液氮冷軋-時效工藝對Cu-1Cr-1Ni-0.6Si合金進行加工,合金抗拉強度(783.6 MPa)與導電率(48.3%IACS)分別比單級室溫軋制-時效提高了91.3 MPa和4.9%IACS;Lei等[31]的研究表明,聯合時效工藝能使Cu-6.0Ni-1.0Si-0.5Al-0.15Mg-0.1Cr合金獲得優異綜合性能,合金抗拉強度高達1155.8 MPa,導電率為25.2%IACS;Yang等[32]的研究表明,時效強化型Cu-0.32Cr-0.067Ti-0.032Si合金經過室溫冷軋、370℃低溫時效可獲得比420℃時效更高的力學性能,且能保留較高的位錯密度和織構強度。
目前,形變熱處理工藝研究更側重于優化時效工藝參數,對冷軋變形量的關注較少,而不同程度的冷軋變形往往會導致合金基體中位錯密度差異顯著,進而影響合金析出相形核與長大,最終對時效后合金的組織與性能產生顯著影響[24,26,29]。本工作以自主開發的Cu-3.0Ni-0.6Si-0.16Zn-0.15Cr-0.03P合金[21]為研究對象,重點關注軋制變形量對合金組織性能與析出行為的影響,為進一步提升該類合金的綜合性能提供理論參考與數據支撐。
1 實驗方法
選用電解純Cu (99.99%)、電解純Ni (99.96%)、高純Si (99.99%)、純Cr塊(99.96%)、純Zn塊(99.99%)和Cu-14%P中間合金作為熔煉原料,按Cu-3.00Ni-0.60Si-0.16Zn-0.15Cr-0.03P名義成分進行配料,在Ar氣保護感應爐中熔煉并澆鑄成型,實測成分為Cu-3.28Ni-0.60Si-0.22Zn-0.11Cr-0.04P。將鑄錠切為20 mm × 60 mm × 100 mm坯料并在950℃保溫2 h后熱軋到10 mm厚;熱軋試樣在950℃保溫4 h后進行淬火處理,然后分別進行總變形量為65%、75%、85%和95%的冷軋變形;將不同變形量后的合金取樣,分別在400、450和500℃進行20、30、60、90、120、180、240、300和360 min時效處理,隨后測試樣品導電率、硬度和抗拉強度并觀察合金的析出相形貌。
采用Sigmma2008B渦流導電儀測量導電率,工作頻率500 kHz,每個試樣測試5次,取均值;采用HXD-1000TM/LCD型顯微硬度儀測試硬度,載荷0.05 kg,保持時間15 s,每個試樣測試5次,取均值;根據GB/T 228.1—2010標準,采用CTM2500微機控制電子萬能試驗機進行拉伸實驗,試樣形狀為狗骨狀,拉伸速率為0.5 mm/min,相同形變熱處理條件下的試樣各取3個進行測試,抗拉強度取均值;采用DSC25差示掃描量熱儀(DSC)測試不同冷軋變形后的標準樣品,溫度區間為20~550℃,升溫速率10℃/min;在Axio Imager顯微鏡(OM)上觀察顯微組織,試樣采用傳統的機械磨拋制備,腐蝕劑配方為5 g FeCl3 + 15 mL HCl + 100 mL H2O;在Tecnai G2 20型透射電鏡(TEM)上進行組織觀察以獲得TEM像及高分辨TEM (HRTEM)像,操作電壓為200 kV,TEM試樣經電解雙噴減薄,電解液為30%HNO3 + 20%H3PO4 + 50%CH3COOH (體積分數),溫度為-30~-10℃,電壓為10~15 V,電流為50 mA;采用EDAX 1071型能譜儀(EDS)分析強化相的成分組成。
2 冷軋變形量對合金析出與再結晶工藝窗口的影響
時效溫度是Cu-Ni-Si系合金時效工藝中重要的參數。時效溫度過低,析出緩慢,生產效率低;時效溫度過高,合金易發生再結晶與析出相長大,損害合金性能。一般為了優化合金的時效工藝,需要確定一個合理的時效溫度窗口(開始析出溫度與開始再結晶溫度區間)來盡量避免時效過程中發生再結晶行為。Cu-Ni-Si系合金開始析出溫度與開始再結晶溫度的DSC測試結果如圖1所示。
圖1

圖1 不同冷軋變形量下Cu-3.28Ni-0.60Si-0.22Zn-0.11Cr-0.04P合金的DSC測試結果
Fig.1 DSC test results of the Cu-3.28Ni-0.60Si-0.22Zn-0.11Cr-0.04P alloy by different cold-rolling deformations (ε)
(a) ε = 0% (b) ε = 65% (c) ε = 75% (d) ε = 85% (e) ε = 95%
(f) precipitation temperatures and recrystallization initial temperatures
圖1a為未經過冷軋變形試樣的DSC曲線,在測試溫度區間內只有一個明顯的開始析出溫度(348℃),未見再結晶現象,可以推斷出合金未變形時,再結晶溫度大于550℃;圖1b~e分別為冷軋變形量65%、75%、85%和95%的DSC曲線,曲線上有明顯的開始析出溫度和開始再結晶溫度。對比不同變形量下的開始析出和開始再結晶溫度可以發現,開始析出溫度始終低于開始再結晶溫度。開始析出溫度和開始再結晶溫度隨著變形量的增加呈現逐漸降低的趨勢:當變形量為65%時,開始析出溫度為335℃;當變形量為95%時,開始析出溫度降低了26℃,為309℃。與此同時,當變形量為65%時,開始再結晶溫度為508℃;當變形量為95%時,開始再結晶溫度降低了19℃,為489℃。
特別地,當變形量為85%時,如圖1f,合金的開始析出溫度下降8℃,開始再結晶溫度增加6℃,時效溫度窗口增大,說明在此變形量下合金基體中析出相對再結晶發生有明顯的阻礙作用。相比于變形量為75%的試樣,85%變形試樣的形變儲能大,由于較高的位錯密度能促進溶質原子形核,所以在相同的加熱速率下85%變形試樣先于75%試樣發生時效析出,故前者的開始析出溫度較后者低,而析出相又阻礙了晶界的遷移從而使再結晶開始溫度提高。同理,95%變形的試樣,由于變形的進一步提高,試樣基體內位錯密度高于85%,開始析出溫度同樣會降低,但是過高的形變儲能和位錯密度使試樣再結晶快速發生,析出相對晶界遷移的阻礙作用不明顯,甚至成為再結晶的形核點加速再結晶,導致開始再結晶溫度較85%試樣有所降低(具體原因有待進一步明確)。
從以上關于合金在不同冷軋變形程度后DSC測得的開始析出溫度與開始再結晶溫度的變化趨勢與原因分析不難看出,合金的時效析出與再結晶之間互相競爭,相互影響[33]。一方面變形時在合金基體內產生的大量位錯成為析出原子的快速通道和形核位置,加快析出相長大,同時也是再結晶的驅動力和形核位置;另一方面時效析出的第二相能釘扎晶界從而影響再結晶的形核和生長,延緩再結晶。很顯然,當合金成分一定時,合金開始析出溫度取決于冷軋變形程度,而開始再結晶溫度不僅與變形程度息息相關,還與析出和再結晶進程的瞬時平衡緊密相關;同時也表明2者之間的交互作用對溫度也非常敏感。
DSC的實驗結果表明,隨著變形量的增加,Cu-Ni-Si-Cr-Zn-P合金時效工藝窗口總體呈減小的趨勢。在變形量一定時,應盡量選擇工藝窗口溫度較高的區間以減少能源消耗。合金經85%冷軋變形后能獲得較大的時效工藝窗口。因此,85%冷軋變形合金選擇在400~450℃下時效,既可以避免時效熱處理時發生再結晶而降低合金力學性能,同時又能保證較強的析出動力,促進析出相的大量析出,使合金保持優良的導電性能。
3 冷軋變形量對時效前合金組織和性能的影響
圖2為Cu-3.28Ni-0.60Si-0.22Zn-0.11Cr-0.04P合金分別經過65%、75%、85%和95%冷軋變形的顯微組織OM像。隨著冷軋變形量的增加,晶粒逐漸被壓扁、拉長。當變形量為65%時,在晶粒內部產生大量的滑移線,如圖2a所示,不同晶粒內滑移線的數量也不同,這與原始晶粒尺寸和取向有密切關系。當變形量為75%時,全部晶粒呈帶狀,部分晶粒變形不均勻導致晶內產生切變帶,如圖2b所示。當變形量為85%時,大部分拉長的晶粒內產生“人”字形切變帶,如圖2c所示。當變形量為95%時,晶界開始模糊,組織演變成纖維狀,局部已經很難分辨晶界,大量的切變帶存在于顯微組織中,如圖2d所示。
圖2

圖2 不同程度冷軋后合金顯微組織的OM像
(a) ε = 65% (b) ε = 75% (c) ε = 85% (d) ε = 95%
Fig.2 OM images of microstructures of the alloy after different cold-rolling deformations (RD—rolling direction, ND—normal direction)
Cu-3.28Ni-0.60Si-0.22Zn-0.11Cr-0.04P合金試樣經固溶處理及不同變形量冷軋后,試樣的硬度和導電率測試結果如圖3所示。由圖可知,固溶處理后合金樣品的導電率隨著冷軋變形量的增加而緩慢降低,冷軋總變形量為95%時樣品的導電率由固溶態下的33.2%IACS降低到28.9%IACS,僅降低了4.3%IACS。與此同時,樣品硬度隨冷軋變形量的增加而大幅提高,當總變形量為95%時,硬度由固溶態時的122.5 HV提高到175.5 HV,增加了53 HV。另外,冷軋變形量超過75%之后,試樣硬度隨著變形量的增加速度放緩:當冷軋總變形量為75%時,樣品硬度由變形量為65%時的151.5 HV提高到165.2 HV,增加了13.7 HV;當總形變量為85%、95%時硬度分別為170.1和175.5 HV,分別比前次變形增加4.9和5.4 HV。
圖3

圖3 不同程度冷軋變形對時效前合金導電率和硬度的影響
Fig.3 Effect of cold-rolling deformation reduction on electrical conductivity and hardness of the alloy before aging treatment
冷軋變形后的硬度和導電率測試結果表明:樣品硬度隨著冷軋變形量的增加而大幅升高,樣品導電率隨著冷軋變形量的增加而小幅度減小。這是因為樣品冷軋變形量越大,產生的晶體缺陷(位錯、亞晶界等)越多,硬度越高,但由此引起的電子散射相比異種原子固溶導致的電子散射幅度小很多,所以導電率降幅較小[34,35]。雖然提高Cu-Ni-Si合金的冷軋變形程度可在有限的范圍內提高合金樣品的力學性能,但遠不能滿足實際應用性能需求,在實際生產中形變強化往往與其他強化方式共同使用[36]。
4 冷軋變形對時效后合金組織的影響
對比不同冷軋變形量下合金試樣在相同溫度和保溫時間時效后的金相組織能較完整地反映出冷軋變形量對時效組織的影響規律。為此,本工作選取60 min作為典型的保溫時間,觀察不同冷軋變形后的樣品在400、450和500℃下時效60 min的顯微組織,如圖4所示。圖4a~d表明,與冷軋后的合金顯微組織相比,經冷軋變形并在400℃下保溫60 min后,不同變形量合金試樣的顯微組織沒有明顯變化。冷軋變形后的試樣在450℃下保溫60 min后,如圖4e~h所示,合金試樣的顯微組織發生了明顯變化,85%冷軋變形試樣(圖4g)的原始晶界已經模糊不清但尚能分辨出少量的纖維狀原始晶粒,被變形帶分割出的亞晶呈魚鱗狀,少量的再結晶晶粒零散地分布在原始晶界處;95%冷軋變形樣品原始晶粒已難以分辨(圖4h),絕大多數亞晶成為新的細小晶粒分布在原始晶粒和變形帶周圍。圖4i~l為冷軋變形后的合金試樣在500℃下保溫60 min后的顯微組織,此時試樣均發生了明顯的再結晶,95%冷軋變形樣品已經完全再結晶。
圖4

圖4 不同程度冷軋樣品在400、450和500℃下時效60 min的顯微組織OM像
(a, e, i) ε = 65% (b, f, j) ε = 75% (c, g, k) ε = 85% (d, h, l) ε = 95%
Fig.4 OM images of microstructures of alloys with different cold-rolling reductions after aging for 60 min at 400oC (a-d), 450oC (e-h), and 500oC (i-l)
綜上分析可知,在較低溫度下(400℃)合金只發生回復幾乎不發生再結晶;而在較高溫度(450℃)下樣品在局部發生再結晶,其中85%冷軋變形樣品較好地保持變形組織形貌;在高溫(500℃)下樣品幾乎都發生了再結晶,除85%冷軋樣品外,其他變形量越大的樣品再結晶程度越明顯。
盡管OM觀察的結果也證實了Cu-3.28Ni-0.60Si-0.22Zn-0.11Cr-0.04P合金在85%冷軋變形后具有較寬的時效工藝窗口,但DSC測試的開始再結晶溫度與金相觀察結果有差異,例如:65%冷軋變形后的樣品在450和500℃下保溫60 min后出現了局部再結晶(如圖4e和i),再結晶溫度明顯低于DSC測量得出的508℃開始再結晶溫度。出現這一現象的原因主要有2方面:一方面,在DSC測試時,溫度是逐漸增加的(10℃/min),升溫過程中試樣會發生較為明顯的回復,消耗了一部分形變儲能降低了再結晶的動力,導致測量出的開始再結晶溫度偏高;另一方面,金相試樣在不同溫度下時效時,在極短的時間內就升溫到所設定的溫度且進行60 min保溫,在升溫過程中較少發生回復導致形變儲能較大,一旦保溫溫度超過再結晶臨界溫度,樣品就會再結晶,在時間累積效應下,通過金相就能觀察到再結晶現象。
為了進一步明確冷軋變形對Cu-3.28Ni-0.60Si-0.22Zn-0.11Cr-0.04P合金時效微觀組織的影響機制,本工作以85%冷軋變形后合金在450℃下時效微觀組織的演變為主要研究對象,研究冷軋變形對析出組織形貌和分布的影響,以此來理解合金性能提升機制,為制定合理的形變熱處理工藝提供依據。選擇85%冷軋變形試樣作為微觀組織研究對象,主要是考慮到85%冷軋變形后合金試樣具有較寬的時效工藝窗口,且相比于95%冷軋變形試樣具有更好的抗過時效性能,相比于65%和75%冷軋變形的試樣具有更高的時效析出動力。
Cu-3.28Ni-0.60Si-0.22Zn-0.11Cr-0.04P合金試樣經85%冷軋變形在基體內產生大量位錯并形成位錯纏結和胞壁,如圖5a所示,胞壁處位錯密度大大高于胞內的密度,會形成較多的溶質原子運動通道,在時效處理時易導致第二相優先在胞壁處析出[37,38];胞內由于位錯密度較低,第二相形核率小,從而使胞壁處第二相密度遠遠大于胞內。圖5b所示為冷軋85%的合金試樣在450℃下時效20 min時的HRTEM像。可見,在位錯附近有大量邊長約為4 nm的等邊三角形析出相(箭頭所指),在位錯胞內這樣的析出相明顯較少。圖5c進一步表明析出相與基體是共格關系,且在析出相附近有明顯的G.P.區存在[39,40]。圖5d為圖5c中三角形析出相區域Fourier變換后得到的δ-Ni2Si斑點(正交結構,a = 0.706 nm,b = 0.499 nm,c = 0.372 nm)。上述結果表明:在合金時效前期,位錯分布決定著析出形核點的分布,G.P.區與早期析出相共存于基體內,且與基體呈現共格關系。
圖5

圖5 85%冷軋變形后合金基體內位錯與早期析出相
Fig.5 Dislocation and early precipitates in 85% cold rolled alloy matrix
(a) TEM image of dislocation cell
(b) precipitates after aging for 20 min (indicated by arrows)
(c) HRTEM image of G.P. zone and early precipitates
(d) Fourier transform of speckles analysis of early precipitates
圖6a所示為85%冷軋變形試樣時效40 min后的HRTEM像,圖6b所示為圖6a中析出相區域經Fourier變換后的衍射花樣,δ-Ni2Si析出相與基體之間存在半共格關系。圖6c為85%冷軋變形試樣時效60 min后的TEM像,粗化后的析出相分布在位錯線附近。圖6d為85%冷軋變形試樣時效90 min后的TEM像,此時析出相已經長大,殘留位錯胞逐漸向亞晶轉變,長大的析出相能阻礙位錯與亞晶界的遷移,抑制后續再結晶的形成,使合金保持較高力學性能。
圖6

圖6 85%冷軋變形合金時效中期析出相分布與形態
Fig.6 Distribution and morphologies of precipitates in the middle aging stage of 85% cold rolled wrought copper alloy
(a) 40 min aging (b) partial enlarged detail of Fig.6a and Fourier transform of precipitated phase
(c) 60 min aging (d) 90 min aging
在后續時效中,由于胞壁位錯密度大,為附近析出相提供了形核位置和析出驅動力,提高了析出相粗化速率;基體內位錯密度的差異使得析出相形核、長大存在差異,導致析出相分布不均勻。與此同時,隨著時效時間的延長,基體內部發生回復,由冷軋變形積累的位錯逐漸重新排列或形成亞晶結構降低晶體缺陷,造成析出驅動力降低,使析出速率降低;三角形析出相逐漸長大成為球狀,與基體之間的共格關系也演變為半共格、非共格關系。
85%冷軋變形樣品時效120 min后出現了Cr3Si析出相,如圖7所示。圖7a為析出相的TEM像,圖中黑色的長棒狀析出相為Cr3Si,其長約為350 nm,寬約為120 nm;其他析出相彌散分布,形貌呈球狀,直徑約為100 nm。圖7b為棒狀析出相的EDS,Cr與Si原子比約為3;圖7c為Cr3Si析出相的選區電子衍射(SAED)花樣分析,Cr3Si析出相為bcc結構,a = b =c = 0.4558 nm[25,41];圖7d為δ-Ni2Si析出相的SAED分析。時效120 min的試樣基體中位錯墻消失,出現了大量長大的δ-Ni2Si析出相和少量的退火孿晶。
圖7

圖7 85%冷軋變形合金時效120 min后析出相形貌、EDS及選區電子衍射(SAED)花樣
Fig.7 Precipitated phase morphology, EDS, and SAED patterns of 85% cold-rolling deformed alloy after aging for 120 min
(a) bright-field TEM image of precipitated phase
(b) EDS of Cr3Si (c) Cr3Si SAED pattern (d) δ-Ni2Si SAED pattern
5 冷軋變形量對時效后合金性能的影響
不同冷軋變形量的Cu-3.28Ni-0.60Si-0.22Zn-0.11Cr-0.04P樣品在400、450和500℃時效0~360 min后,樣品的導電率和硬度結果如圖8所示。
圖8

圖8 冷軋變形+不同溫度時效后合金的硬度與導電率
Fig.8 Electrical conductivities (a, c, e) and hardnesses (b, d, f) of the alloy after cold-rolling deformation and aging at different temperatures
(a, b) 400oC (c, d) 450oC (e, f) 500oC
由圖8a、c和e中可知,不同變形量的樣品在時效初期導電率都快速升高,達到一個較高值后緩慢增加。在相同溫度下時效,變形量越大的樣品,導電率也越大,樣品達到相同導電率所需要的時間亦越短。這是因為在時效初期,Cu基體過飽和度高,變形引入的形變儲能和位錯等晶體缺陷會加速析出相析出,凈化Cu基體,從而使導電率快速升高。從圖8c中可知,變形量為95%的樣品在450℃下時效6 h后導電率最高(62.7%IACS)。
由圖8b和d可知,在400℃下時效時,變形量為65%、75%、85%和95%的樣品硬度達到峰值所需要的時間分別為240、240、240和90 min,如圖3b所示。在450℃下時效時,變形量為65%、75%、85%和95%的樣品硬度達到峰值所需要的時間分別為300、360、60和60 min,如圖3d所示。在相同溫度下時效時,變形量越大,達到峰值時效所需時間越短,這是因為在時效初期,Cu基體過飽和度高,位錯密度高使得第二相析出動力大,析出速率快,使硬度迅速上升到峰值。
由圖8f可知,在500℃時效時,未變形的試樣硬度隨著保溫時間的延長逐漸升高,保溫300 min后試樣硬度達到158 HV,之后基本保持不變;變形65%的試樣硬度在60 min時達到峰值硬度178 HV后也基本保持不變;變形75%的樣品在時效20 min時達到峰值硬度185 HV后開始緩慢下降,180 min后硬度開始急劇下降,300 min時硬度僅為145 HV;變形85%的樣品在時效40 min后達到峰值201 HV,隨后逐漸下降,直到90 min后才開始急劇下降;而變形95%的樣品在時效前具有較高的硬度,但在時效期間硬度一直在下降,直到180 min時才保持基本不變,僅維持在130 HV左右。相比于400和450℃,500℃下不同變形量樣品的硬度變化較為復雜,其中變形量為95%的樣品在時效初期迅速發生再結晶導致硬度迅速下降,析出強化對硬度的貢獻遠不抵再結晶造成的軟化;而變形量85%的樣品,20~180 min時效期間硬度和抗過時效能力(穩定性)均高于其他變形量試樣;造成這一現象的原因主要是85%變形樣品析出動力較65%和75%強,析出相長大發生在再結晶前,粗化的析出相不僅釘軋位錯運動,還抑制了晶界的遷移使再結晶延遲。總體而言,變形量65%、75%和85%樣品的硬度在達到峰值后逐漸下降,變形量越大,下降速率越快,這是因為在高溫時,樣品回復時間較短,大量位錯形成再結晶核心,形變儲存能驅使再結晶迅速發生,以及析出相在高溫下迅速長大共同導致合金硬度下降。在500℃時,形變量越大再結晶的時間越早,位錯等晶體缺陷的散逸消失越快,導致析出動力減弱,析出相減少,因此樣品導電率相比450℃較低。
圖8中樣品導電率隨時效時間的延長持續升高,這表明在時效過程中溶質原子不斷析出;在相同時效溫度和時效時間下,冷軋變形量越大樣品的導電率越高,表明冷軋變形程度越大促進析出的動力越強。樣品在未發生再結晶前,在400和450℃時效時,變形量大的樣品到達硬度峰值所用的時間短;當時效溫度為500℃時,變形量越大的樣品越容易發生再結晶。
根據以上實驗結果與分析,時效前的冷軋變形不僅可以提高Cu-Ni-Si-Zn-Cr-P合金的力學性能,還幾乎不損失導電性能。合理的冷軋變形與時效制度能很好地平衡合金的力學性能與導電性能[33]。當冷軋變形量為85%時,較佳的時效工藝為450℃、60 min;當冷軋變形量為95%時,較佳的時效工藝為400℃、90 min和450℃、60 min。
圖9a為Cu-3.28Ni-0.60Si-0.22Zn-0.11Cr-0.04P合金試樣經過85%冷軋變形后在450℃時效0~360 min的拉伸變形工程應力-應變曲線。時效60 min后達到峰值時效,抗拉強度為(786 ± 12) MPa,延伸率為7.4% ± 0.8%,此時導電率為(47.5 ± 0.9)%IACS。圖9b為合金試樣經過95%冷軋變形后在400℃時效0~360 min的工程應力-應變曲線,時效90 min后達到峰值時效,抗拉強度為(825 ± 16) MPa,延伸率為10.1% ± 0.7%,此時導電率為(45.3 ± 0.6)%IACS。圖9c為合金試樣經過95%的冷軋變形后在450℃時效0~360 min的工程應力-應變曲線,時效60 min后達到峰值時效,抗拉強度為(841 ± 10) MPa,延伸率僅為3.4% ± 0.4%,此時導電率為(52.2 ± 0.3)%IACS。
圖9

圖9 冷軋變形試樣時效后的拉伸性能及合金性能分布[7,10,11,13,15,16,28,34]
Fig.9 Engineering stress-strain curves of the alloy after aging and alloys' properties distribution
(a) ε = 85%, 450oC (b) ε = 95%, 400oC
(c) ε = 95%, 450oC (d) properties distribution[7,10,11,13,15,16,28,34]
對比上述3種形變-熱處理后合金的工程應力-應變曲線可以看出:① 抗拉強度呈現先增加后降低的趨勢,延伸率呈現與抗拉強度此消彼長的趨勢;② 85%冷軋變形的合金試樣雖然峰值抗拉強度稍小于冷軋變形量為95%的合金試樣,但是前者比后者具有更優的抗過時效能力,這一點與DSC實驗結果相符;③ 95%冷軋變形的試樣能在較短的時效時間內達到峰時效狀態,但易過時效導致抗拉強度在時效后期急劇下降。
圖9d[7,10,11,13,15,16,28,34]給出了近期關于Cu-Ni-Si系列合金通過微合金化和優化形變熱處理工藝后得到的峰值性能分布。可以看出,Cu-Ni-Si合金的抗拉強度和導電率分布跨度較大,抗拉強度從550 MPa到850 MPa,導電率從35%IACS到52%IACS,這說明微合金化和形變熱處理工藝對Cu-Ni-Si合金的性能影響十分重要。本工作的Cu-3.28Ni-0.60Si-0.22Zn-0.11Cr-0.04P合金最佳時效性能比已有報道的合金抗拉強度和導電率都高。
由此可見,以抗拉強度800 MPa、導電率50%IACS為設計目標由MLDS給出的合金成分經過熔煉、均勻化、熱軋、固溶后,85%冷軋變形、450℃時效60~180 min后,合金能夠獲得650~786 MPa的抗拉強度、(47.5~52.4)%IACS的導電率;95%冷軋變形、400~450℃時效60~180 min后,合金能夠獲得610~841 MPa抗拉強度、(47.7~54.8)%IACS導電率。上述結果表明:通過MLDS方法設計高性能銅合金成分是可行的,且由其設計的合金能通過較寬的工藝范圍實現設計性能。
6 冷軋變形量對合金時效動力學的影響
由Cu-3.28Ni-0.60Si-0.22Zn-0.11Cr-0.04P合金時效過程中微觀組織和性能的變化不難看出,溶質原子在時效過程中源源不斷地從Cu基體中析出形成第二相,其中第二相的體積分數、析出相形貌和分布決定著合金的力學性能和導電率。上述形變熱處理實驗結果說明不同程度的冷軋變形對合金的時效析出促進程度有明顯差別。同時,時效熱處理過程中析出相體積分數的可預測、模型化對指導生產研發有一定實用價值。定量研究Cu-3.28Ni-0.60Si-0.22Zn-0.11Cr-0.04P合金時效前變形量對析出動力學的影響,能為合理安排形變熱處理工藝和平衡合金最終力學性能與導電性能提供數據參考。為此,本工作采用傳統的Avrami方程來分析不同冷軋變形程度和時效溫度對合金的時效動力學的影響規律。
6.1 合金析出相體積分數計算
由于合金的導電率對時效析出相體積比非常敏感,通過測量樣品時效過程中導電率的變化可間接計算出析出相體積分數[42,43]。合金析出相體積分數定義為:
其中,φ為樣品某一時刻的體積分數,V為樣品單位體積內在某一時刻析出相的體積,V'為樣品最大析出時單位體積內析出相的體積。合金時效足夠長時間后導電率不再明顯上升時,此時認為合金析出完全,導電率達到最大值ψmax,φ = 1;而未開始時效時,V = 0,導電率為初態導電率ψ0,φ = 0。
合金導電率ψ與φ之間關系密切,體積分數越大,電導率越高。φ與時效時間t之間遵循相變動力學Avrami經驗方程[44]:
其中,b、n為常數;b取決于時效溫度、原始相的成分和晶粒大小等因素,n取決于相變類型和形核位置。由
而當析出終了時,ψ = ψmax,φ = 1,則A = ψmax - ψ0,因此只要測量合金在各個溫度下各時刻的導電率就可計算出相應時刻的φ。據此方法并利用實驗測得的導電率計算出Cu-3.28Ni-0.60Si-0.22Zn-0.11Cr-0.04P合金新析出相的體積分數。
6.2 析出動力學方程與導電率方程
析出動力學方程常常用Avrami經驗方程(
將t和φ代入
圖10

圖10 時效時間與析出相體積分數之間的關系
(a) 400oC (b) 450oC (c) 500oC
Fig.10 Relationships between aging time (t) and volume fraction (φ) of precipitated phase
表1 不同時效溫度下合金Avrami方程系數n和b的值
Table 1
Deformation / % | 400oC | 450oC | 500oC | |||
---|---|---|---|---|---|---|
n | b | n | b | n | b | |
0 | 0.47697 | 0.196816 | 0.53149 | 0.143992 | 0.60633 | 0.093694 |
65 | 0.70726 | 0.089045 | 0.50174 | 0.184944 | 0.66154 | 0.075043 |
75 | 0.59424 | 0.122617 | 0.57403 | 0.100221 | 0.59698 | 0.116676 |
85 | 0.52762 | 0.161306 | 0.53865 | 0.103705 | 0.53706 | 0.170424 |
95 | 0.66998 | 0.088510 | 0.54447 | 0.118476 | 0.46226 | 0.283687 |
根據
圖11

圖11 不同溫度時效時合金導電率實驗值與計算值
(a) 400oC (b) 450oC (c) 500oC
Fig.11 Experimental and calculated values of electrical conductivity of alloys at different temperatures
6.3 合金析出動力學S曲線
將不同溫度下的n和b值代入
圖12
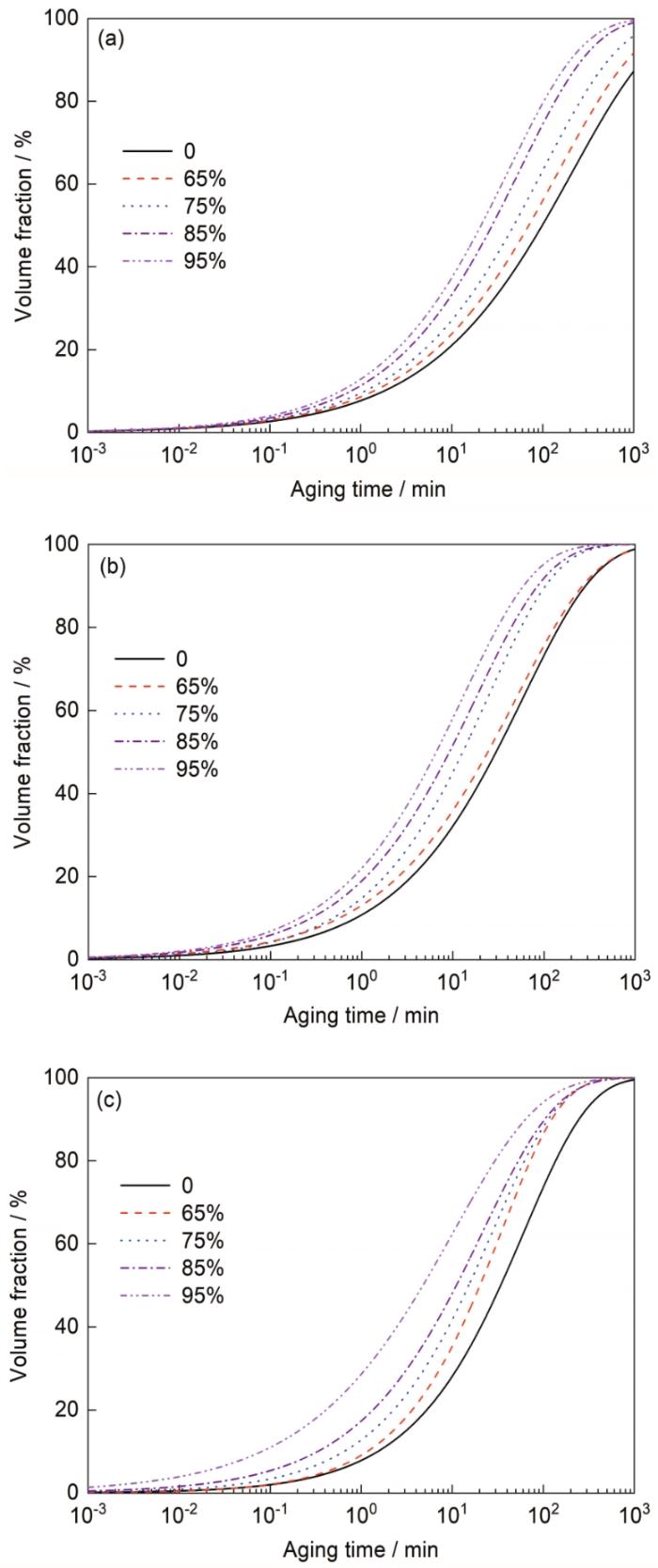
圖12 冷軋變形量對不同溫度下時效析出動力學S曲線的影響
(a) 400oC (b) 450oC (c) 500oC
Fig.12 Influence of cold-rolling deformation on S curve of precipitation kinetics at different temperatures
從圖12a中可知,樣品在400℃時效時,析出相體積分數達到50%時,變形量為65%、75%、85%和95%的樣品用時分別約為70、48、27和20 min,而未變形的樣品用時約為100 min。從圖12b中可知,樣品在450℃時效時,析出相體積分數達到50%時,變形量65%、75%、85%和95%的樣品用時分別約為24、14、10和7 min,而未變形的樣品用時約為30 min。從圖12c中可知,樣品在500℃時效時,析出相體積分數達到50%時,變形量65%、75%、85%和95%的樣品用時分別約為18、12、9和5 min,而未變形的合金樣品用時約為28 min。可以看出:時效溫度越高、變形量越大,樣品中析出相同體積分數的析出相所需要的時間越短。因此,時效前對合金進行較大程度的冷變形,在相同的時效溫度下可以提高析出動力,加速合金析出,有效縮短峰值時效時間;同理,在變形量相同的情況下,時效溫度越高合金時效析出動力越強,析出速率越快。
7 結論
(1) 隨著冷軋變形量增大,合金開始析出溫度和再結晶溫度總體呈降低的趨勢;僅當變形量為85%時,合金的開始析出溫度下降8.5℃,開始再結晶溫度反而上升6.6℃,時效窗口增加約15℃。
(2) 85%冷軋變形的樣品在450℃時效20 min后,大量邊長約為4 nm的等邊三角形δ-Ni2Si相在位錯附近析出;時效40 min后,δ-Ni2Si析出相與基體之間存在半共格關系;時效120 min后在基體中觀察到少量的Cr3Si析出相。
(3) 合金經過85%冷軋變形后在450℃下保溫60 min后獲得抗拉強度峰值性能為(786 ± 12) MPa,導電率為(47.5 ± 0.9)%IACS;冷軋變形量為95%的試樣450℃時效60 min后獲得的抗強度峰值(841 ± 10) MPa,導電率為(52.2 ± 0.3)%IACS。
來源--金屬學報