分享:增/降氧過程對高溫合金粉末表面特性和合金性能的影響:粉末存儲到脫氣處理
1
2
采用場發射掃描電鏡(FESEM)、X射線光電子譜(XPS)、高角環形暗場掃描透射電鏡(HAADF-STEM)以及程序升溫脫附與質譜聯用(TPD-MS)等表征手段研究了不同窄粒度范圍鎳基高溫合金粉末的原始表面狀態以及存儲和脫氣等增/降氧過程對合金組織和性能的影響。結果表明:不同粒度原始態粉末的表面組成均為NiO/Ni(OH)2、TiO2、CoO和Cr2O3,0~15 μm粒徑粉末(細粉)和150~180 μm粒徑粉末(粗粉)平均氧化膜厚度分別為3.32和10.90 nm。細粉和粗粉在空氣環境中存儲后氧含量逐漸增大,在3~10 d達到穩定值,分別約為250 × 10-6和40 × 10-6。存儲后0~53 μm粉末制備的塊體合金氧含量升高,室溫、650℃和750℃拉伸強度變化不大,但塑性下降,合金在650℃、890 MPa和750℃、530 MPa的持久性能均下降。0~15 μm細粉加熱過程中(室溫~1000℃)會發生氣體脫附,存在明顯脫附峰的氣體包括CO2、H2O和H2,粉末表面氣體的脫附溫度范圍主要在100~600℃,脫附峰主要集中在300~600℃溫度段,150~180 μm粗粉加熱過程脫附峰不明顯。0~53 μm的粉末采用300℃ + 600℃溫度組合方式除氣后制備的合金氧含量從初始狀態的195 × 10-6下降到113 × 10-6,合金力學性能更優,性能提升主要表現在合金的塑性升高。高溫合金粉末增氧機制主要包括表面氧化和表面吸附,而降氧機制主要為粉末表面吸附的含氧氣體的脫出。采用高溫合金粉末升溫脫附曲線中峰位所處溫度精確定制除氣保溫溫度組合,通過25℃ + 150℃ + 310℃ + 470℃低、中、高溫組合多級除氣處理使得空氣中存儲過的鎳基高溫合金粉末(0~53 μm)氧含量可進一步降低到(87~96) × 10-6。
關鍵詞:
鎳基高溫合金已廣泛應用于航空發動機和工業燃氣輪機[1,2]。粉末高溫合金因具有合金化程度高、良好的抗疲勞和蠕變性能以及優異的耐腐蝕和抗高溫氧化性能,使其成為當前先進航空發動機渦輪盤件的首選材料[3]。高溫合金粉末具有組織細小、偏析傾向低的特性,使其在制備高合金化厚大截面類零件(如渦輪盤)時具有明顯優勢,同時它也是高性能3D打印復雜構件的基礎材料。然而,高溫合金粉末也不可避免地會面臨一些問題,如粉末比表面積遠大于塊體材料,造成氧含量升高1~2個數量級。因此,合金的氧含量控制當以合金仍處于粉末狀態時入手最為有效。在粉末渦輪盤件和3D打印復雜構件的生產流程中,涉及粉末狀態的工序包括粉末制備、粉末篩分、粉末除氣以及銜接上述工序間的存儲與轉運。在存儲和轉運(增氧過程)中,粉末接觸環境介質導致氧含量升高。高溫合金粉末氧含量的升高會導致原始顆粒邊界缺陷(PPBs)的形成[4,5],從而對力學性能產生不利影響[6]。在粉末氧含量不可避免升高的背景下,后續通過適當的粉末除氣處理工藝(降氧過程),可再將氧含量降低,改善合金的力學性能,從而滿足零件的服役要求。因此,掌握在存儲/轉運和除氣過程中高溫合金粉末的氧化特性及其對合金組織和力學性能的影響,對于合金和零件制備過程的質量控制和工藝優化至關重要。
合金粉末的表面狀態會對粉末后續的固結或重熔凝固成形產生明顯影響[7,8],關于金屬粉末原始表面狀態在以往研究工作中多有報道[9~12]。高溫合金粉末在制備完成后一直到固結成形前始終保持粉末狀態,但其不可避免地會面臨轉運、存儲等過程。有關存儲條件對鋁合金和鈦合金粉末的影響已有研究[13,14],而對于后續熱加工和力學性能的影響少見報道。本課題組[15]針對單一較寬粒度段的高溫合金粉末開展了不同存儲介質(包括空氣、純O2、Ar氣和真空)和存儲時間(0~500 d)對粉末氧含量和合金熱加工性能影響的研究。結果表明,粉末存儲會使高溫合金粉末的氧含量升高,促進PPBs的形成,進而導致熱加工性能的下降,然而,對于經存儲的粉末固結成形后合金的組織和力學性能還有待研究。近期,本課題組[16]還針對潮濕和濕熱環境對粉末高溫合金組織和性能的影響開展了相關研究工作。合金粉末比表面積大,因此在存儲、轉運過程更容易氧化且在表面吸附含氧氣體造成氧含量的升高,后續是否能通過合適的處理工藝再將氧含量降低到可以接受的程度成為關注的重點。真空除氣處理是一種在動態真空條件下對合金粉末進行加熱進而實現粉末表面氣體脫附的處理工藝。粉末本征的氣體脫附行為決定了除氣的有效性和除氣效率,因此有必要開展相關的研究。以往文獻中報道了采用氣相色譜質譜聯用(GC-MS)[17,18]以及程序升溫脫附和質譜聯用(TPD-MS)研究合金粉末升溫過程中的氣體脫附規律[19~22],上述研究主要針對鋁合金粉末。近年來,TPD-MS開始被應用于高溫合金粉末升溫過程的脫氣行為研究,針對固溶強化型625合金、γ′強化型FGH96合金和γ′/γ′′強化型718合金開展了不同成分和粒度對高溫合金粉末氣體脫附行為的影響[23],以及FGH96粉末的脫氣行為研究[24],獲得了較寬粒度范圍典型成分高溫合金粉末的氣體脫附規律。然而,將高溫合金粉末氣體脫附規律用于指導實際粉末真空除氣工藝優化及其對力學性能的影響研究工作還有待開展。本工作擬采用程序升溫脫附質譜聯用高效確定高溫合金粉末從室溫到1000℃多種氣體的本征脫附曲線,再根據脫附峰的敏感溫度點有針對性地制定除氣工藝參數[25],以實現降低高溫合金粉末氧含量的目標。
高溫合金粉末不同的粒度范圍往往會對應不同的應用場景,如粉末冶金渦輪盤制備,因為夾雜尺寸控制的需要多采用相對較細粒度的粉末;而對于3D打印高溫合金制備中鋪粉工藝常采用細粉,為保證較好的粉末流動性,送粉工藝多采用相對較粗粒度的粉末。針對上述應用特征,不同的粉末粒度對于比表面積、氧含量乃至后續成形后合金力學的性能都會產生明顯影響。因此,識別不同粒度等級高溫合金粉末的關鍵影響因素,對于不同粒度范圍的粉末開展針對性的研究尤為重要。其中,介于氣霧化高溫合金粉末粒度分布具有一定范圍的特征,采用窄粒度范圍不同粒度粉末開展相關研究,對于規律性的發現更具優勢。本工作擬對窄粒度高溫合金粗粉和細粉分別開展原始粉末特性、氧含量、表面狀態、存儲條件的影響以及脫氣行為研究。針對存儲和脫氣后粉末固結成形制備的合金開展顯微組織和力學性能研究,揭示增/降氧過程對粉末表面特性的影響機制,指導粉末存儲條件和除氣工藝過程控制,優化高溫合金粉末處理工藝過程以及進一步提高合金力學性能。
1 實驗方法
實驗所用材料為粉末冶金鎳基高溫合金FGH96,通過真空感應熔煉Ar氣霧化(VIGA)制備合金粉末。原始粉末經過機械震動篩分為不同粒度范圍,分別為< 15 μm、< 53 μm、75~100 μm和150~180 μm。采用NAVA NanoSEM 450場發射掃描電鏡(FESEM)觀察粉末的表面形貌,運用Thermo Scientific Escalab 250Xi X射線光電子譜(XPS)分析粉末表面的氧化物組成和氧化膜厚。通過Helios Nanolab 600i雙束聚焦離子束(FIB)對單顆高溫合金粉末顆粒進行切片和薄膜制樣,采用Talos F200X高角度環形暗場掃描透射電子顯微鏡(HAADF-STEM)和能譜儀(EDS)對粉末表面附近的截面形貌和氧化層成分進行分析。采用PCA-1200型TPD-MS將高溫合金粉末按預定的升溫程序連續加熱到1000℃,腔室吹掃載氣為高純He,以獲得窄粒度范圍合金粉末表面多種氣體(O2、H2、H2O、CO和CO2)脫附曲線。研究不同存儲時間對固結成形后粉末高溫合金組織和性能的影響。首先將新制備的高溫合金粉末在空氣中存儲0~40 d,通過LECO TC600氣體分析儀測定存儲時間對窄粒度段高溫合金粉末的氣體含量的影響。將新粉和經過空氣中存儲90 d后的粉末通過熱等靜壓(HIP)固結成形制備塊體合金,采用配備電子背散射衍射(EBSD)探頭的OXFORD Symmetry場發射掃描電鏡(SEM)對比分析存儲前后粉末制備的高溫合金的顯微組織。以粉末表面氣體脫附曲線為依據,研究除氣參數對粉末高溫合金氣體含量、PPBs和力學性能的影響。采用DM6000M光學顯微鏡(OM)觀察PPBs缺陷。依據室溫拉伸標準(GB/T 228.1—2010)、高溫拉伸標準(GB/T 228.2—2015)和高溫持久標準(GB/T 2039—2012)分別對存儲前后和不同除氣參數制備的粉末高溫合金進行室溫、650℃和750℃溫度條件下的拉伸實驗以及650℃、890 MPa和750℃、530 MPa條件的持久實驗,并對不同條件下的斷口形貌進行分析。
2 實驗結果
2.1 高溫合金原始粉末表面特性
篩分為不同窄粒度范圍的FGH96高溫合金粉末的表面形貌如圖1所示。可以看到不同粒徑的粉末均為球形,而粒徑大的粉末(圖1b和c)有更多的衛星粉末。進一步觀察粉末表面形貌可以看出,幾種粒度的粉末均為細樹枝晶組織,0~15 μm細粉末的枝晶干不發達,有時呈現胞晶形態,而大粒徑粉末的表面枝晶更為發達。
圖1

圖1 不同窄粒度范圍FGH96高溫合金粉末的表面形貌
Fig.1 Surface morphologies of FGH96 superalloy powders with different narrow particle size ranges
(a) 0-15 μm (b) 75-100 μm (c) 150-180 μm
窄粒度段的粗、細2種高溫合金粉末表面的XPS全譜如圖2所示。可以看到粉末表面均富C和O元素,同時含有少量的合金元素,包括Ni、Cr、Co、Ti、Mo,而窄粒度細粉末的峰更高。
圖2
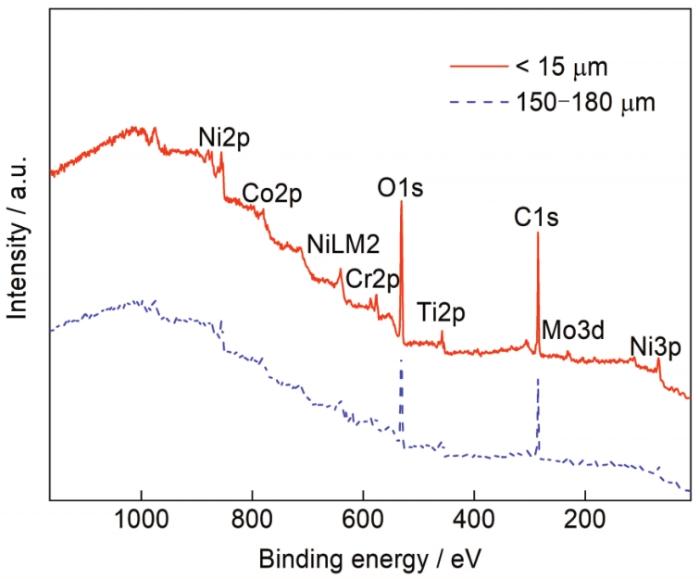
圖2 不同窄粒度范圍FGH96高溫合金粉末的XPS全譜
Fig.2 XPS survey spectra of FGH96 superalloy powders with different narrow particle size ranges
利用XPS得到FGH96高溫合金粗、細粉末最外表面的Ni2p、Ti2p、Co2p、Cr2p、C1s 和O1s高分辨精細譜如圖3所示。其中Ni元素在粉末最外表面以金屬態、NiO和Ni(OH)2的形式存在;Ti、Co和Cr元素在粉末表面存在狀態相似,主要以氧化物TiO2、CoO和Cr2O3的狀態存在,有很少量的金屬態。粉末表面的O和C元素主要以CO
圖3
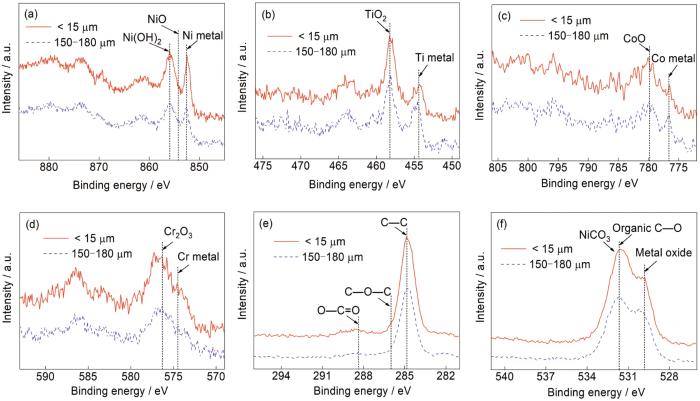
圖3 不同窄粒度范圍FGH96高溫合金粉末表面Ni2p、Ti2p、Co2p、Cr2p、C1s和O1s的XPS高分辨譜
Fig.3 Detailed XPS high-resolution spectra of Ni2p (a), Ti2p (b), Co2p (c), Cr2p (d), C1s (e), and O1s (f) on the surface of FGH96 superalloy powders with different narrow particle size ranges
不同粒度的FGH96高溫合金粉末表面經離子刻蝕不同深度后所對應的元素相對含量如圖4所示。可見,C、O以及合金基體元素Ni和活潑元素Ti的相對含量隨離子刻蝕深度的變化而顯著變化,特別是在粉末表面10 nm范圍內。窄粒度段細粉末從表面向粉末內部C和O元素相對含量的變化幅度較粗粉末更大。
圖4
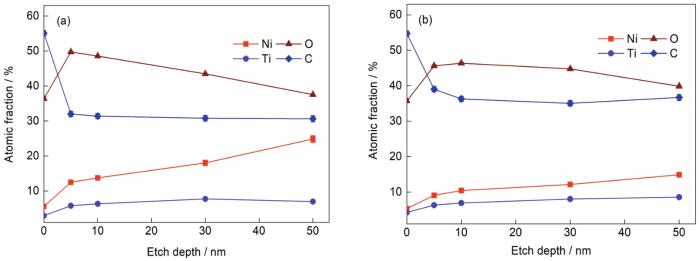
圖4 不同窄粒度范圍FGH96高溫合金粉末表面元素含量隨XPS刻蝕深度的變化
Fig.4 XPS etch depth analyses of different elemental concentrations for FGH96 superalloy powders with different narrow particle size ranges
(a) 0-15 μm (b) 150-180 μm
利用Ni和O元素的高分辨窄譜所得到的金屬Ni (Nimet)峰和O峰相對離子強度(I / Iω,其中,I和Iω 分別為元素在不同刻蝕深度處的離子強度和元素在50 nm刻蝕處的離子強度)隨刻蝕深度的變化曲線來估算粉末表面NiO/Ni(OH)2層的厚度[23],結果如圖5所示。可以看出,細粉末(0~15 μm)的表面氧化層厚度為3.32 nm,不及粗粉末表面膜厚(10.90 nm)的1/3。
圖5
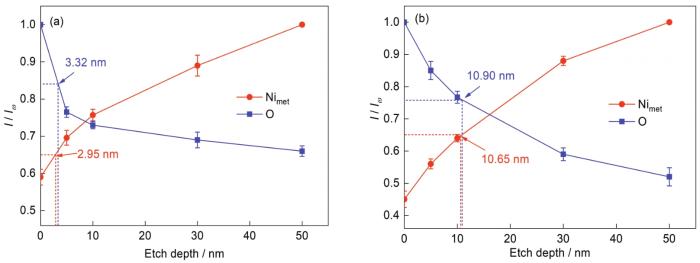
圖5 金屬Ni (Nimet)和O在離子刻蝕不同深度處的相對離子強度變化曲線
Fig.5 Relative intensity (I / Iω ) of Ni-metal (Nimet) and oxygen (O) with different ion etching depths by XPS, indicating surface NiO/Ni(OH)2 layer thickness of FGH96 superalloy powders with narrow particle size ranges of 0-15 μm (a) and 150-180 μm (b)(I—intensity of Nimet or O at different etch depth, Iω —intensity of Nimet or O at etch depth of 50 nm)
圖6為不同粒度FGH96高溫合金粉末外表面氧化膜的截面HAADF-STEM像及EDS面掃描圖。由圖可見,粗、細粉末表面均存在氧化層,其中細粉末的表面膜厚約3.1 nm,粗粉末表面氧化膜厚約11.3 nm。取樣和觀察區域的元素EDS面掃描結果表明,表面氧化層富O和Ti,而局部區域可以觀察到富Nb和Al的氧化物。
圖6
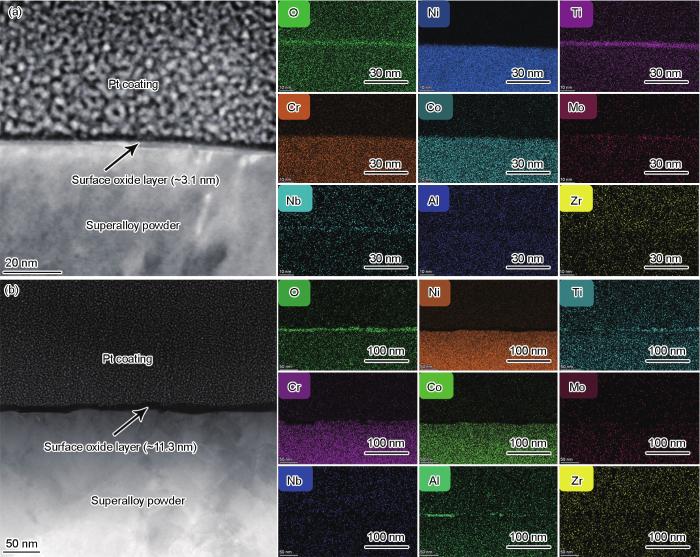
圖6 不同窄粒度范圍FGH96高溫合金粉末的表面氧化膜的截面HAADF-STEM像和EDS面掃描圖
Fig.6 Cross-sectional images of high-angle annular dark field scanning transmission electron microscopy (HAADF-STEM) (left) and energy dispersive spectrum (EDS) elemental mapping (right) on surface oxide layer of FGH96 superalloy powders with different particle size ranges
(a) 0-15 μm (b) 150-180 μm
2.2 存儲條件對粉末高溫合金氧含量、組織和性能的影響
圖7為不同窄粒度范圍的FGH96高溫合金粉末在恒溫恒濕(溫度20℃、濕度40%~50%R.H.)空氣條件下存儲不同時間的氧含量變化曲線。可以看出,在存儲的初始階段,粉末的氧含量均隨存儲時間的延長呈快速上升趨勢,細粉和粗粉分別在存儲3和10 d時氧含量達到最高值,隨后趨于穩定,直到40 d也基本不再發生明顯改變。0~15 μm窄粒度的細粉的氧含量從約150 × 10-6 (初始值)增加到存儲后的250 × 10-6左右,隨后趨于穩定。而150~180 μm粒度的粗粉氧含量初始值僅約為25 × 10-6,存儲后約達到40 × 10-6趨于穩定。
圖7

圖7 不同窄粒度范圍FGH96高溫合金粉末在大氣環境中(溫度20℃、濕度40%~50%R.H.)存儲不同時間的氧含量變化曲線
Fig.7 Curves of oxygen content of FGH96 superalloy powders with different narrow particle size ranges stored in ambient air (20oC, 40%-50%R.H.) for different time
對存儲前后< 53 μm粒度的FGH96粉末進行HIP (1170℃、150 MPa、4 h)固結成形,成形后塊體合金組織的SEM像、EBSD分析及晶粒尺寸分布如圖8所示。其中原始粉末制備的塊體合金(HIP-1)氧含量約為120 × 10-6,大氣環境存儲90 d后粉末制備的塊體合金(HIP-2)氧含量約為200 × 10-6。2種塊體合金的顯微組織中均出現明顯的PPBs缺陷(圖8a和d),但HIP-2塊體合金中的PPBs更明顯。2種塊體合金的晶粒組織如圖8b和e所示,其中HIP-2塊體合金的平均晶粒尺寸為4.69 μm,略大于HIP-1塊體合金(4.13 μm) (圖8c和f)。
圖8

圖8 原始態和大氣環境存儲90 d后< 53 μm粒度的FGH96高溫合金粉末經熱等靜壓(HIP)固結成形后顯微組織的SEM像、EBSD結果及晶粒尺寸分布
Fig.8 SEM images (a, d), EBSD images (b, e), and average grain sizes (c, f) of hot isostatic pressed (HIPed) bulk alloys consolidated from original (HIP-1, with oxygen content of about 120 × 10-6) (a-c) and stored (in the atmospheric environment for 90 d, HIP-2, with oxygen content of about 200 × 10-6) (d-f) FGH96 superalloy powders with particle size range of 0-53 μm (PPB—prior particle boundary)
分別將HIP-1和HIP-2塊體合金進行室溫(25℃)、650℃和750℃高溫條件下的拉伸實驗,結果如圖9所示。由圖可見,在室溫和高溫拉伸過程中,HIP-2塊體合金的塑性均有一定程度的降低(圖9a)。在室溫條件下拉伸時,HIP-2塊體合金的屈服強度和抗拉強度略有上升,延伸率和斷面收縮率略有下降(圖9b),但影響不明顯。在650℃拉伸時,隨著氧含量的增加,合金的屈服強度和抗拉強度略有升高,但伸長率和斷面收縮率明顯降低,下降幅度分別達到12.0%和9.2% (圖9c)。在750℃拉伸時,合金屈服強度和抗拉強度小幅升高,伸長率和斷面收縮率下降幅度分別達到7.9%和4.8% (圖9d)。粉末存儲造成的氧含量變化對HIP態高溫合金的拉伸強度影響不明顯,而對塑性影響明顯,隨著氧含量的增加延伸率和斷面收縮率明顯降低。以上氧含量對粉末高溫合金力學性能的影響規律與以往研究中鑄造鎳基高溫合金類似[26]。
圖9
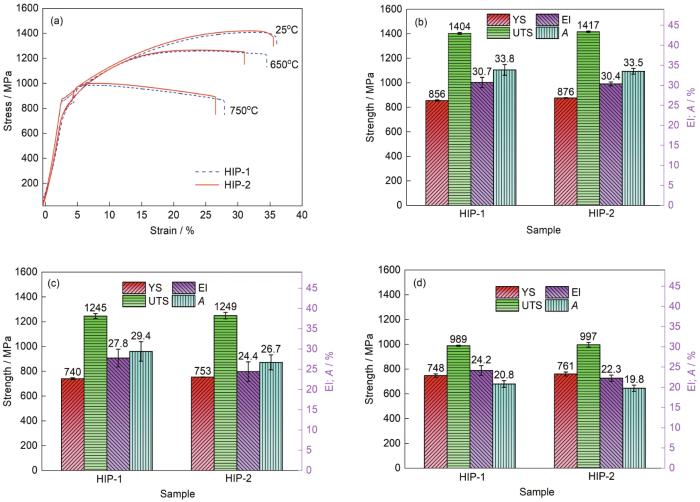
圖9 HIP-1和HIP-2塊體合金分別在室溫(25℃)、650℃和750℃條件下的拉伸應力-應變曲線及力學性能
Fig.9 Tensile stress-strain curves (a) and mechanical properties of HIP-1 and HIP-2 bulk alloys at ambient temperature (25oC) (b), 650oC (c), and 750oC (d) (YS—yield strength, UTS—ultimate tensile strength, El—elongation, A—reduction of area)
對室溫和高溫拉伸后的試樣斷口進行分析,結果如圖10所示。由圖可見,所有的拉伸斷口呈塑性斷裂特征,斷口上有大量韌窩和少量準解理狀小平面,隨著拉伸溫度的升高,韌窩數量減少,但尺寸增大,同時準解理狀小平面增多,在750℃拉伸斷口上可找到沿晶二次裂紋。值得注意的是,這里出現的準解理小平面,是拉伸過程中處于軟取向的晶粒產生廣泛滑移造成滑移面脫開而形成的相對平坦的小平面,其尺寸范圍通常不超過晶粒尺寸。隨著溫度升高,參與這類變形的晶粒數目越來越多,因此高溫拉伸的小平面遠多于室溫,本質上仍屬于塑性斷口特征。
圖10

圖10 HIP-1和HIP-2塊體合金分別在室溫(25℃)、650℃和750℃條件下的拉伸斷口形貌
Fig.10 Low (left) and high (right) magnified SEM images of tensile fracture surfaces of HIP-1 (a, c, e) and HIP-2 (b, d, f) bulk alloys at ambient temperature (25oC) (a, b), 650oC (c, d), and 750oC (e, f)
分別將HIP-1和HIP-2塊體合金在650℃、890 MPa和750℃、530 MPa條件下進行高溫持久實驗,結果如表1所示。可見,在2種條件下,與HIP-1塊體合金相比,HIP-2塊體合金的持久壽命、延伸率和斷面收縮率均不同程度地降低。
表1 HIP-1和HIP-2塊體合金分別在650℃、890 MPa和750℃、530 MPa條件下的持久性能
Table 1
Stress rupture condition | Alloy | Rupture life / h | El / % | A / % |
---|---|---|---|---|
650oC, 890 MPa | HIP-1 | 29.1 ± 1.2 | 27.7 ± 1.1 | 25.2 ± 0.9 |
HIP-2 | 22.0 ± 0.5 | 22.5 ± 1.9 | 21.6 ± 1.2 | |
750oC, 530 MPa | HIP-1 | 32.4 ± 0.8 | 14.1 ± 0.3 | 16.3 ± 0.4 |
HIP-2 | 28.1 ± 0.6 | 10.1 ± 1.7 | 10.9 ± 1.3 |
2.3 脫氣行為對粉末高溫合金氧含量、組織和性能的影響
采用TPD-MS測定不同窄粒度范圍高溫合金粉末的氣體脫附曲線,如圖11所示。可以看到有脫附峰的氣體主要包括CO2、H2O和H2。從圖中還可以看出,0~15 μm的窄粒度細粉(圖11a)的脫附峰較150~180 μm粗粒度粉末(圖11b)更明顯。高溫合金粉末表面氣體的脫附溫度范圍主要在100~600℃,脫附峰主要溫度段集中在300~600℃。
圖11
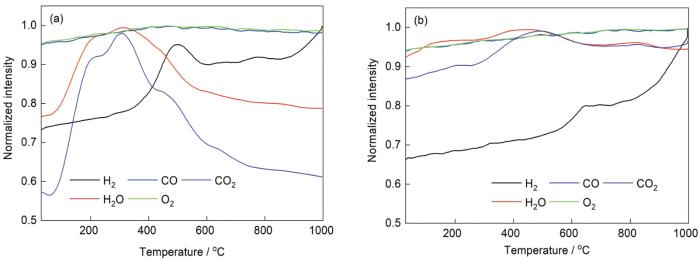
圖11 不同窄粒度范圍FGH96高溫合金粉末的氣體脫附曲線
(a) 0-15 μm (b) 150-180 μm
Fig.11 Temperature programmed desorption with mass spectrometry (TPD-MS) degassing curves of FGH96 superalloy powders with different narrow particle size ranges at heating rate of 20oC/min
根據上述TPD-MS的結果選取氣體脫出較為集中的溫度范圍(300~600℃),選取實際除氣工藝參數如表2所示,對存儲15 d后的高溫合金粉末在真空除氣爐中進行實際除氣實驗,選擇的除氣保溫溫度分別25、300和600℃,加熱速率為20℃/min,除氣真空度控制在10-3 Pa以內,配合保溫時間,分別采取單一除氣和組合除氣工藝進行對比研究。
表2 FGH96高溫合金粉末(0~53 μm)的除氣實驗工藝參數設定和所制備合金的氧含量
Table 2
Sample | Degassing parameter | Oxygen content / 10-6 |
---|---|---|
25oC degassing | 25oC, 2 h | 195 |
300oC degassing | 25oC, 2 h + 300oC, 5 h | 140 |
600oC degassing | 25oC, 2 h + 600oC, 5 h | 124 |
300oC + 600oC degassing | 25oC, 2 h + 300oC, 5 h + 600oC, 5 h | 113 |
按照上述不同的真空除氣參數對粒度< 53 μm的FGH96高溫合金粉末進行真空除氣處理,之后在1170℃、150 MPa、4 h的條件下對粉末進行HIP固結,所得合金的氧含量如表2所示。可以看到,在合金粉末脫氣敏感溫度附近(300和600℃)進行真空除氣的合金較室溫除氣工藝氣體含量明顯下降,從195 × 10-6下降到(124~140) × 10-6,而采用敏感溫度區間組合除氣(300℃ + 600℃)的方式氧含量進一步下降至113 × 10-6。
不同除氣工藝后HIP制備的合金拋光態的顯微組織如圖12所示。合金組織中可看到典型的PPBs缺陷,PPBs的嚴重程度按照25℃ > 300℃ > 600℃ > 300℃ + 600℃的規律逐漸減弱,與氧含量的變化趨勢一致。空氣環境存儲粉末經25℃真空除氣處理后,PPBs為2~3級之間;經300℃ + 600℃真空除氣處理后,PPBs降低至1級。可以看出在上述除氣溫度中,經300℃ + 600℃組合溫度真空除氣處理的氣體脫附效果更優,氧含量明顯降低,PPBs缺陷嚴重程度降低。
圖12
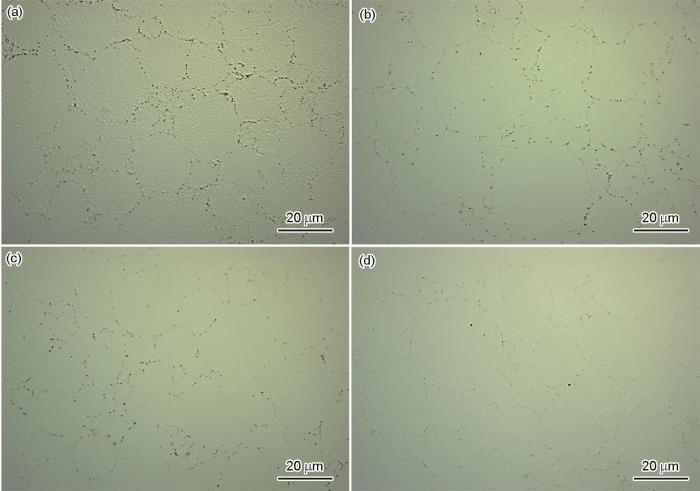
圖12 不同除氣工藝下FGH96高溫合金粉末經HIP固結成形后合金的顯微組織
Fig.12 Microstructures of HIPed alloys consolidated from FGH96 superalloy powders with different degassing processes, indicating the severity of PPBs defects
(a) 25oC degassing (b) 300oC degassing (c) 600oC degassing (d) 300oC + 600oC degassing
經不同真空除氣工藝處理后制備的合金的室溫(25℃)和高溫(650、750℃)拉伸性能如圖13所示。結果表明,真空除氣處理主要影響合金的塑性,合金的延伸率和斷面收縮率按照25℃ < 300℃ < 600℃ < 300℃ + 600℃的規律逐漸升高。而合金的屈服強度和抗拉強度隨著除氣溫度的升高略微降低,最大降幅僅5%。300℃ + 600℃的真空除氣處理對塑性的提升效果最明顯,不同溫度拉伸后合金的延伸率和斷面收縮率明顯提高,其中750℃拉伸后的延伸率(21.2%)和斷面收縮率(29.5%)增幅最大。
圖13
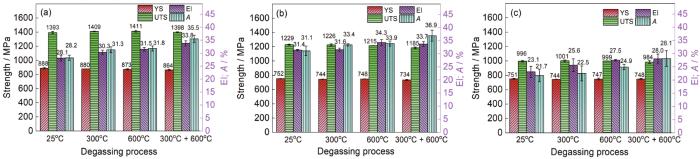
圖13 不同除氣工藝處理的FGH96高溫合金粉末經HIP固結成形后合金的室溫和高溫拉伸性能
Fig.13 Tensile properties of FGH96 alloy at ambient temperature (25oC) (a), 650oC (b), and 750oC (c) HIP consolidated from powders with different degassing processes
圖14給出了粉末經25℃和300℃ + 600℃真空除氣后HIP固結成形合金的拉伸斷口形貌。由圖可知,經25℃真空除氣處理后HIP合金在室溫(25℃)和高溫(650、750℃)拉伸后的斷口可以觀察到一定原始顆粒邊界的形貌特征,高倍放大圖中存在少量韌窩,同時伴有少量微裂紋。經300℃ + 600℃真空除氣處理后,斷口組織中呈現出大量韌窩,隨著溫度的升高,斷口平面的凹凸程度和韌窩深度有所增加,符合塑性斷裂特征。
圖14
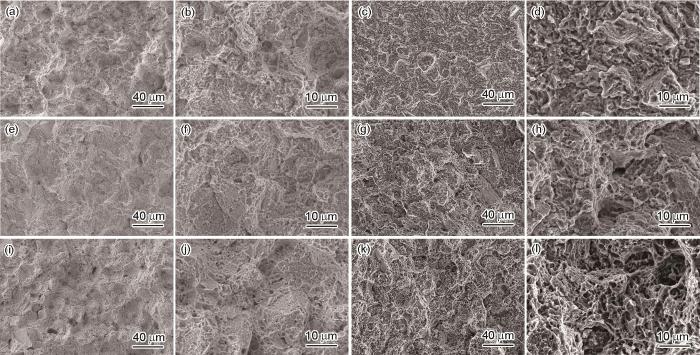
圖14 空氣環境存儲粉末經25℃和300℃ + 600℃真空除氣處理后HIP態FGH96合金的拉伸斷口形貌
Fig.14 Tensile fracture surfaces of HIPed FGH96 alloy consolidated from air stored powders after 25oC (a, b, e, f, i, j) and 300oC + 600oC (c, d, g, h, k, l) degassing
(a-d) 25oC tensile (e-h) 650oC tensile (i-l) 750oC tensile
3 分析討論
3.1 高溫合金粉末降氧處理工藝的精確定制
粉末在固結成形前,盡量避免其與環境介質接觸是減少氧含量上升的有效手段之一。本課題組之前的研究[15,16]表明,采用不同的存儲介質氧含量都會不可避免地上升并最終達到一個相對穩定值,與常規大氣環境以及相對惡劣存儲介質(純O2和高濕空氣)相比,保護性存儲介質(如Ar氣和真空)下存儲高溫合金粉末,其氧含量相對較低,但達到最終穩定值后與大氣環境存儲的粉末氧含量區別不大。因此,后續的粉末真空除氣處理成為降低高溫合金粉末氧含量的重要途徑。在以往研究和實際工程應用場景中,高溫合金粉末除氣工藝多采用經驗設定工藝參數,較多采用單一或階梯溫度的除氣保溫溫度。在本工作中,通過TPD-MS實驗一次高效獲得室溫到1000℃高溫合金表面的多種氣體脫附敏感溫度范圍,再根據該溫度范圍有針對性地制定組合溫度保溫除氣工藝(300℃ + 600℃),較傳統單一溫度工藝(300℃)氧含量從140 × 10-6左右降到113 × 10-6左右,而組合溫度除氣工藝制備的合金力學性能也更優。
在上述研究基礎上,進一步尋求提升高溫合金粉末(特別是含濕粉末)真空除氣降氧工藝優化的空間,實現工藝參數的精確定制。對鎳基高溫合金窄粒度細粉進行TPD-MS實驗,觀察氣體脫附曲線涉及多種含氧氣體的脫出峰,峰位溫度就是對應含氧氣體的脫出峰值溫度,其中水蒸氣(H2O)以雙峰(150℃、300℃)形式脫出,CO2和CO也分別在310和470℃呈現明顯的脫出峰。將粒徑< 53 μm的經過空氣暴露存儲365 d后的鎳基高溫合金粉末除氣保溫溫度設定為上述不同峰值溫度的組合,除氣保溫溫度和時間為室溫(25℃)下抽真空1 h + 150℃保溫3 h + 310℃保溫3 h + 470℃保溫3 h,保溫時真空度保持在10-3 Pa以下,具體工藝如圖15所示。粉末隨后進行標準的封焊、包套和HIP固結成形,測得合金的氧含量僅為(87~96) × 10-6。由此可見,鎳基高溫合金粉末在采用上述低溫(150℃)、中溫(310℃)、高溫(470℃)組合多級真空除氣更有利于粉末特別是潮濕粉末表面含氧氣體脫出,所制備的合金氧含量可控制在100 × 10-6以內(圖15),實現了高溫合金粉末降氧處理工藝的精確定制。
圖15
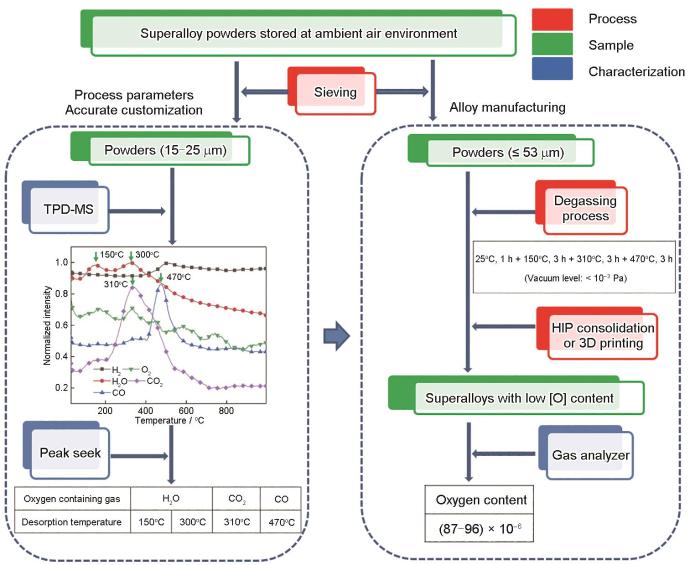
圖15 鎳基高溫合金粉末多級除氣工藝參數的優化精確定制與制備合金的氧含量
Fig.15 Optimization and precise customization of multi-stage degassing process parameters for Ni-based superalloy powders and oxygen content of the manufactured alloys
3.2 高溫合金粉末表面氧的存在形式及粉末的增/降氧機制
3.2.1 高溫合金粉末表面氧的存在形式
高溫合金粉末存儲(增氧)和脫氣(降氧)過程中氧的存在形式會對粉末及其固結成形后合金的性能產生明顯影響。高溫合金中氧的溶解度很低,其存在形式主要包括化合態的氧和自由態的氧。而本工作中涉及的主要是指高溫合金粉末表面的氧,包括表面氧化膜和不連續分布的氧化物,以及粉末表面吸附的多種含氧氣體。
3.2.2 粉末的增氧過程
粉末高溫合金最大的優勢就是在制備厚大截面的部件(如航空發動機渦輪盤件)時可以減少元素偏析,但是粉末也具有一定的局限性,那就是因為較塊體合金更大的比表面積而使得氧含量激增。從粉末制備出來到固結成形至塊體材料前,都會處于這種大比表面積的狀態,而從粉末制備到粉末處理再到包套封焊這些工序間轉運過程和存儲過程,不可避免地會接觸到環境介質,造成氧含量的升高。氧含量可以在很短的時間內就達到平衡不再進一步升高,這使得氧在粉末高溫合金制備流程中遺傳進入塊體合金和零部件中,對力學性能造成不利影響。高溫合金粉末制備完成后,在與環境介質接觸的過程中表面會快速生成一定厚度的氧化物/水合物層,同時其極大的比表面積還會吸附空氣中的O2、水蒸氣以及黏附一些含有C、O的有機物。在后續存儲過程中,隨著時間的增加,表面的氧化物/水合物層會增厚,同時表面吸附的氣體也會增加,宏觀表現為粉末氧含量的增加。上述結果中,窄粒度細粉和粗粉在表面氧化層厚度和表面吸附氣體的含量會有明顯的不同,其中單顆粗粉具有更厚的氧化層厚度,而細粉因為數量多、比表面積大,其氧含量會明顯高于粗粉。
3.2.3 粉末的降氧過程
高溫合金粉末在工藝流程中不可避免地會造成氧含量的增加,后續通過真空除氣降氧處理工藝可將氧含量降低。在真空除氣的升溫和保溫過程中,粉末外表面吸附的O2會持續脫出,而水蒸氣(H2O,物理吸附)在150℃左右為脫出峰值;金屬碳酸鹽或有機物加溫后會形成為CO2或CO并脫出(如NiCO3→NiO + CO2↑)(310℃,化學吸附);表面水合物在加熱后會發生反應放出水蒸氣(如Ni(OH)2→NiO + H2O↑)(300℃,化學吸附),新生成的H2O與粉末表面原始吸附的H2O一樣也會在溫度的作用下脫出。上述含氧氣體脫出后會使粉末氧含量降低,在后續的HIP固結成形過程中保持較低氧含量,并將這一低氧特征遺傳進入塊體合金或部件中,進而提高合金的力學性能。
4 結論
(1) 150~180 μm粗粉和0~15 μm細粉粉末表面的氧化物組成沒有明顯區別,均存在NiO/Ni(OH)2、TiO2、CoO、Cr2O3和NiCO3。但表面氧化層的厚度存在明顯區別,粗粉和細粉氧化膜厚度分別約為11和3 nm。
(2) 細粉和粗粉在空氣環境中存儲不同時間(0~40 d)后的氧含量逐漸增大,粉末經歷增氧過程,在3~10 d達到穩定值,分別約為250 × 10-6和40 × 10-6。存儲前后粉末(<53 μm)制備的高溫合金均存在原始顆粒邊界缺陷(PPBs),空氣存儲后的粉末制備的合金PPBs更明顯,平均晶粒尺寸略大。存儲后粉末制備的合金氧含量升高,室溫、650℃和750℃拉伸強度變化不大,但塑性下降,合金650℃、890 MPa和750℃、530 MPa持久性能均下降。
(3) 0~15 μm細粉加熱過程中(室溫~1000℃)有脫附峰的氣體包括CO2、H2O和H2,粉末表面氣體的脫附溫度范圍主要在100~600℃,脫附峰主要溫度段集中在300~600℃,而150~180 μm粗粉加熱過程未見明顯的脫附峰。在脫附峰集中的溫度范圍進行粉末(< 53 μm)真空除氣,采用組合溫度(300℃ + 600℃)除氣方式,合金的氧含量從初始狀態的195 × 10-6左右下降到113 × 10-6,粉末經歷降氧過程。組合脫氣后制備的合金力學性能更優,性能提升主要表現在合金的塑性指標。采用高溫合金粉末升溫脫附曲線中峰位所處溫度做為除氣保溫溫度組合,通過25℃ + 150℃ + 310℃ + 470℃多級低溫-中溫-高溫組合多級真空除氣處理,使得空氣中存儲過365 d的高溫合金粉末(< 53 μm)氧含量可進一步降低至(87~96) × 10-6,實現高溫合金粉末真空除氣工藝參數的精確定制。
(4) 高溫合金粉末增氧機制主要包括表面氧化和表面吸附。表面氧化是在粉末的表面形成氧化膜和不連續分布的氧化物,氧化膜隨著粉末在空氣中的暴露逐漸增厚,到一定程度鈍化停止。表面吸附O2、H2O等含氧氣體,其中細粉吸附氣體程度較粗粉更大。粉末降氧過程主要是在持續抽真空的條件下升溫保溫,粉末表面物理吸附的氣體在各自的脫出敏感溫度脫附,同時表面化學吸附物質發生Ni(OH)2→NiO + H2O↑和NiCO3→NiO + CO2↑等反應釋放出含氧氣體,最終實現粉末表面氧含量的有效降低。
來源--金屬學報