分享:SiC顆粒增強Al-Zn-Mg-Cu復(fù)合材料的時效行為和力學(xué)性能
馬國楠1,2, 朱士澤1,2, 王東1(![]() |
1中國科學(xué)院金屬研究所 師昌緒先進材料創(chuàng)新中心 沈陽 110016 2中國科學(xué)技術(shù)大學(xué) 材料科學(xué)與工程學(xué)院 沈陽 110016 |
利用粉末冶金法制備了含15%SiC (體積分?jǐn)?shù)) 的SiC/Al-7.5Zn-2.8Mg-1.7Cu (質(zhì)量分?jǐn)?shù),%)復(fù)合材料及其合金,對比了復(fù)合材料及其合金的硬度、電導(dǎo)率和力學(xué)性能隨時效時間延長的變化規(guī)律,并提出了適用于SiC/Al-Zn-Mg-Cu復(fù)合材料的T6時效熱處理工藝。利用TEM和HRTEM技術(shù),對不同時效狀態(tài)下的納米析出相進行了定量分析。結(jié)果表明,SiC顆粒對復(fù)合材料的時效過程具有明顯的促進作用,相同人工時效工藝處理后,復(fù)合材料中析出相尺寸更大、密度更低。復(fù)合材料提前14 h達(dá)到硬度最大值(238 HV),且比未增強合金的硬度最大值高29 HV。復(fù)合材料晶界處無析出帶(PFZ)寬度與未增強合金相似,但粗大的第二相明顯增多,這些晶界相和界面反應(yīng)產(chǎn)物的形成均可消耗合金元素,降低晶內(nèi)沉淀相的密度。HRTEM結(jié)果表明,SiC顆粒沒有改變Al-Zn-Mg-Cu合金的時效析出序列,仍為過飽和固溶體(SSS)-GP區(qū)-η'-η相,其中過渡相η'是T6態(tài)復(fù)合材料的主要強化相。
關(guān)鍵詞:
顆粒增強鋁基復(fù)合材料(particulate reinforced aluminum matrix composites,PRAMCs)比傳統(tǒng)鋁合金具有更高的強度、模量、導(dǎo)熱性、尺寸穩(wěn)定性和耐磨性,成為傳統(tǒng)金屬材料以外的重要工程材料[1,2]。目前,以Al-Mg-Si和Al-Cu-Mg合金為基體的PRAMCs研究相對成熟,已被廣泛應(yīng)用于核電、航空航天和交通運輸?shù)阮I(lǐng)域[3~6]。然而,受基體合金強度的限制,以往研發(fā)的復(fù)合材料強度仍然較低,難以滿足新型裝備對承載結(jié)構(gòu)件的設(shè)計要求。Al-Zn-Mg-Cu合金作為可時效硬化鋁合金,具有更明顯的強度優(yōu)勢,其強度高于大多數(shù)SiC/Al-Mg-Si和SiC/Al-Cu-Mg復(fù)合材料[7,8]。因此,開發(fā)以Al-Zn-Mg-Cu合金為基體的復(fù)合材料,對提高PRAMC強度和促進結(jié)構(gòu)輕量化的發(fā)展具有重要意義。
遺憾的是,SiC顆粒對Al-Zn-Mg-Cu合金的強化效果一直不理想,甚至出現(xiàn)強度不升反降的現(xiàn)象[9~11],極大地限制了SiC/Al-Zn-Mg-Cu復(fù)合材料的研究與發(fā)展。影響SiC/Al-Zn-Mg-Cu復(fù)合材料力學(xué)性能的因素有很多,包括增強顆粒參數(shù)、基體合金成分和熱處理工藝等。選擇合理的基體成分配比,獲得高密度第二相,再結(jié)合適當(dāng)?shù)腡6熱處理工藝[12~14]可以將冶金過程形成的粗大相充分固溶,并在基體中重新析出細(xì)小、彌散分布的納米沉淀相,獲得最佳硬化效果,這些納米相可以有效地釘扎位錯,從而極大地提高復(fù)合材料拉伸強度[15~17]。相比于未熱處理SiC/7085Al復(fù)合材料[18],T6態(tài)復(fù)合材料的抗拉強度可以提高184 MPa,屈服強度提高138%。因此,采用合理的T6熱處理工藝,充分發(fā)揮沉淀相的強化作用是提高SiC/Al-Zn-Mg-Cu復(fù)合材料性能的關(guān)鍵。
然而,目前大部分SiC/Al-Zn-Mg-Cu復(fù)合材料采用的是與未增強合金相同的T6熱處理工藝[19],T6態(tài)復(fù)合材料中沉淀相尺寸更大、密度更低,沉淀強化能力明顯減弱,導(dǎo)致復(fù)合材料力學(xué)性能不佳。復(fù)合材料與未增強合金的時效行為的差異一直被忽略,2者在相同的熱處理條件下,可能處于不同的時效狀態(tài)。一方面,時效析出過程受合金中化學(xué)成分的影響。對于復(fù)合材料,SiC/Al界面反應(yīng)將改變基體中的化學(xué)成分[18,20],降低溶質(zhì)原子過飽和度,影響沉淀相的析出動力學(xué),從而改變最佳時效處理時間。另一方面,由于SiC與Al的熱膨脹系數(shù)不同[6],熱加工后在近界面處將產(chǎn)生大量的錯配應(yīng)力,應(yīng)力通過位錯增殖而松弛,這些位錯可以提高溶質(zhì)原子的擴散速率,影響沉淀相的析出和長大。因此,優(yōu)化SiC/Al-Zn-Mg-Cu復(fù)合材料的T6熱處理工藝,對提高復(fù)合材料的力學(xué)性能十分必要。此外,SiC/Al-Zn-Mg-Cu復(fù)合材料的硬度和強度,很大程度依賴于納米沉淀相的析出狀態(tài),而目前針對SiC/Al-Zn-Mg-Cu復(fù)合材料沉淀相演變規(guī)律的研究十分有限,SiC顆粒對Al-Zn-Mg-Cu合金沉淀相尺寸、種類、密度和分布的影響規(guī)律亟待厘清。
本工作采用粉末冶金法制備了含15%SiC (體積分?jǐn)?shù))的SiC/Al-7.5Zn-2.8Mg-1.7Cu (質(zhì)量分?jǐn)?shù),%,下同)復(fù)合材料以及Al-7.5Zn-2.8Mg-1.7Cu合金,通過對比2者的硬度、電導(dǎo)率和力學(xué)性能隨時效時間延長的變化趨勢,確定了其最佳峰時效處理工藝,闡明了SiC顆粒對SiC/Al-Zn-Mg-Cu復(fù)合材料時效行為的影響規(guī)律,旨在對SiC/Al-Zn-Mg-Cu復(fù)合材料時效熱處理工藝優(yōu)化提供指導(dǎo)。
1 實驗方法
基體合金名義成分為Al-7.5Zn-2.8Mg-1.7Cu。實驗用金屬粉末及磨料級SiC顆粒純度均在99.5%以上,SiC粉末粒徑約為7 μm,復(fù)合材料中SiC顆粒的體積分?jǐn)?shù)為15%。將粉末機械混合均勻后裝入模具內(nèi),通過真空熱壓燒結(jié)法制備坯錠,詳細(xì)的熱壓工藝見文獻(xiàn)[20]。坯錠在420℃下擠壓成棒材,擠壓比為17∶1。為了對比SiC顆粒添加前后材料組織演變特征差異,采用相同工藝另制備同成分下的未增強合金。2種材料的擠壓試棒均在470℃下固溶處理2 h,經(jīng)水淬后,置于120℃的電熱鼓風(fēng)干燥箱中進行不同時間的時效處理,從而獲得不同時效狀態(tài)的試樣。
利用電火花切割技術(shù),沿擠壓方向分別獲取2種材料的金相樣品,并經(jīng)水磨砂紙磨至2000號后進行機械拋光。經(jīng)化學(xué)試劑(1 mL HF + 16 mL HNO3 + 83 mL H2O + 3 g CrO3)腐蝕后,使用Axiovert 200 MAT金相顯微鏡(OM)觀察復(fù)合材料和未增強合金的微觀組織,并利用Image-Pro Plus軟件對其晶粒尺寸進行統(tǒng)計。使用TA-Q1000差示掃描量熱儀(DSC)在Ar氣保護下對固溶處理后的樣品進行分析。實驗條件為以10℃/min的升溫速率,從室溫升到500℃。采用HV-1000硬度測試儀和D60K電導(dǎo)率儀對時效樣品的顯微硬度和電導(dǎo)率演變規(guī)律進行分析。使用Tecnai G2 F20透射電鏡(TEM)觀察不同時效狀態(tài)復(fù)合材料及其合金中的析出相形貌,并對其尺寸進行統(tǒng)計。
根據(jù)時效硬度曲線,使用Instron 5848電子萬能試驗機對不同時效狀態(tài)下的樣品進行拉伸測試,應(yīng)變速率為1 × 10-3 s-1,試樣標(biāo)距為20 mm,寬約3.8 mm,厚約2.3 mm,拉伸方向與擠壓方向平行。為確保數(shù)據(jù)可靠性,每種時效狀態(tài)的材料測試5個拉伸樣品,并計算平均值。
2 實驗結(jié)果與討論
2.1 合金及其復(fù)合材料的金相組織
圖1a和b所示為擠壓態(tài)Al-7.5Zn-2.8Mg-1.7Cu合金和SiC/Al-7.5Zn-2.8Mg-1.7Cu復(fù)合材料顯微組織的OM像。2者均致密,且無明顯的冶金缺陷,如孔洞和裂紋等。經(jīng)擠壓變形后,未增強合金的晶粒有被拉長的趨勢,晶粒的長軸方向平行于擠壓方向(圖1a)。如圖1c所示,根據(jù)晶粒尺寸定量分析,未增強合金的平均晶粒尺寸約為3.4 μm,晶粒尺寸分布比較集中。復(fù)合材料中的SiC顆粒分布均勻(圖1b),無明顯團聚,熱擠壓過程中顆粒隨Al基體的塑性變形而發(fā)生轉(zhuǎn)動,其長軸趨向平行于擠壓方向分布。由于SiC顆粒變形與基體變形不一致,在顆粒周圍極易產(chǎn)生應(yīng)力集中,應(yīng)力通過位錯增殖而松弛,這些位錯可以誘導(dǎo)新晶界形成[21],導(dǎo)致靠近SiC顆粒以及顆粒間距較小的區(qū)域,晶粒尺寸也更小。如圖1d所示,復(fù)合材料平均晶粒尺寸與未增強合金相近,約為3.8 μm,但其晶粒尺寸均勻性較低。
圖1
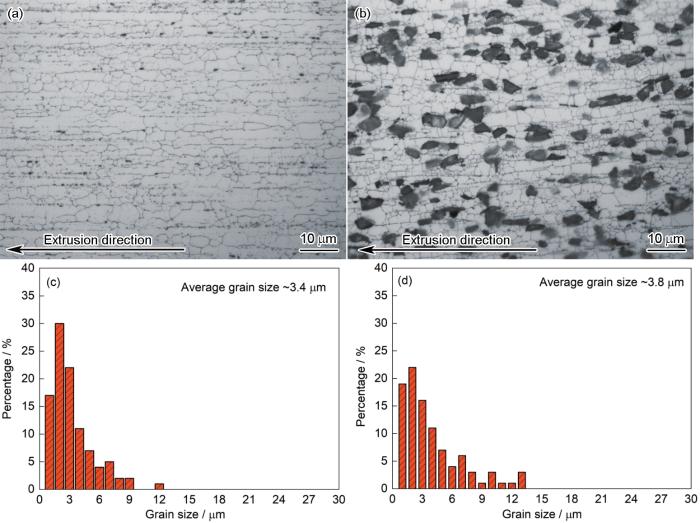
圖1 擠壓態(tài)未增強合金(Al-7.5Zn-2.8Mg-1.7Cu)及復(fù)合材料(SiC/Al-7.5Zn-2.8Mg-1.7Mn)棒材顯微組織的OM像和晶粒尺寸統(tǒng)計柱狀圖
Fig.1 OM images (a, b) and grain size statistic plots (c, d) of as-extruded Al-7.5Zn-2.8Mg-1.7Cu alloy (a, c) and SiC/Al-7.5Zn-2.8Mg-1.7Cu composite (b, d)
2.2 時效時間對材料硬度和電導(dǎo)率的影響
圖2為未增強合金和復(fù)合材料在120℃下時效0~48 h的硬度和電導(dǎo)率曲線。如圖2a所示,時效2 h的未增強合金硬化效果十分顯著,相比于未時效的合金,其硬度提高了26%。隨時效時間繼續(xù)延長,硬度緩慢升高,直到時效24 h硬度達(dá)到最大值209 HV。如圖2b所示,復(fù)合材料時效10 h硬度已經(jīng)達(dá)到最大值238 HV,比基體合金提前約14 h。時效10~24 h,復(fù)合材料始終保持較高的硬度,時效24 h復(fù)合材料硬度也為238 HV,且比未增強合金最大硬度高29 HV。時效24 h之后,復(fù)合材料和未增強合金的硬度均開始緩慢下降。SiC顆粒對復(fù)合材料時效進程起到明顯的促進作用,尤其在時效2~10 h,復(fù)合材料的電導(dǎo)率快速升高,說明已有相當(dāng)多的溶質(zhì)原子脫溶,而這個階段未增強合金的電導(dǎo)率變化十分微弱。未增強合金中沉淀相析出更接近于均勻形核,時效前期,固溶原子優(yōu)先形成密集的原子團簇和與Al基體共格的GP (Guinier-Preston zone)區(qū),對電導(dǎo)率的提升有限。時效10~24 h,未增強合金和復(fù)合材料的電導(dǎo)率均顯著升高,且在時效24 h時,2者的電導(dǎo)率均達(dá)到相對較高的值,時效時間繼續(xù)延長,電導(dǎo)率升高十分緩慢。
圖2
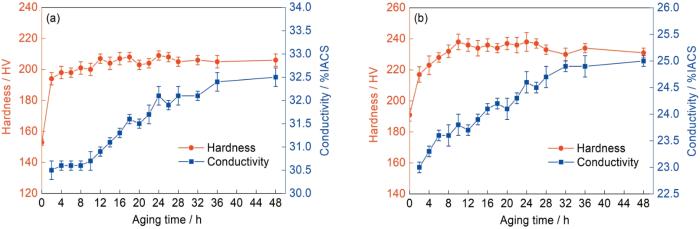
圖2 120℃單級時效未增強合金和復(fù)合材料樣品的硬度和電導(dǎo)率曲線
Fig.2 Aging hardness and electrical conductivity curves of the single-stage aged Al-7.5Zn-2.8Mg-1.7Cu alloy (a) and SiC/Al-7.5Zn-2.8Mg-1.7Cu composite (b) at 120oC (IACS—international annealed copper standard)
2.3 不同時效狀態(tài)下材料的力學(xué)性能
圖3為120℃時效0、2、8、10、24和48 h的未增強合金和復(fù)合材料的拉伸性能。如圖3a所示,時效2 h未增強合金的抗拉強度(UTS)和屈服強度(YS)均大幅度提高,而延伸率(EL)明顯下降。隨時效時間繼續(xù)延長,UTS和YS提升緩慢,直到時效24 h,UTS (662 MPa)和YS (637 MPa)同時達(dá)到了最大值,此時EL為10.0%。延長時效時間,UTS、YS和EL均下降。拉伸性能測試結(jié)果與硬度曲線基本吻合,結(jié)合硬度、電導(dǎo)率和力學(xué)性能確定120℃時效24 h為Al-7.5Zn-2.8Mg-1.7Cu合金的T6熱處理工藝。如圖3b所示,復(fù)合材料的力學(xué)性能變化規(guī)律與基體合金基本一致。時效0~2 h,復(fù)合材料快速強化,UTS提高了37%;在時效8~10 h階段,復(fù)合材料強塑性一直處于較高水平,且變化微弱。時效8 h復(fù)合材料的UTS已經(jīng)達(dá)到了650 MPa,繼續(xù)時效至第一次硬度最高點(120℃、10 h),復(fù)合材料YS達(dá)到了最大值(625 MPa);時效至第二次硬度最高點(120℃、24 h),復(fù)合材料UTS達(dá)到了最大值(663 MPa)。由于SiC顆粒對Al-Zn-Mg-Cu基體沉淀相的析出有促進作用,導(dǎo)致復(fù)合材料比未增強合金提前14 h達(dá)到最大硬度和最高屈服強度。然而,如圖2b所示,時效10~24 h,電導(dǎo)率持續(xù)升高,說明仍有較多溶質(zhì)原子繼續(xù)脫溶,已形成的沉淀相可能逐漸粗化,導(dǎo)致復(fù)合材料屈服強度略有降低,但是復(fù)合材料加工硬化能力提高使得UTS進一步提升。根據(jù)硬度和UTS達(dá)到最高值的時效時間點定義,SiC/Al-7.5Zn-2.8Mg-1.7Cu復(fù)合材料的T6熱處理工藝應(yīng)為120℃保溫24 h。
圖3

圖3 未增強合金和復(fù)合材料在120℃下時效0、2、8、10、24和48 h的力學(xué)性能
Fig.3 Tensile properties of Al-7.5Zn-2.8Mg-1.7Cu alloy (a) and SiC/Al-7.5Zn-2.8Mg-1.7Cu composite (b) aged at 120oC for 0, 2, 8, 10, 24, and 48 h (UTS—ultimate tensile strength, YS—yield strength, EL—elongation)
2.4 合金及其復(fù)合材料析出相的析出行為
圖4所示為不同時效狀態(tài)未增強合金沿[110]Al方向觀察的析出相形貌。如圖4a所示,在120℃時效2 h后未增強合金的析出相尺寸較小,分布十分均勻。η'相在三維空間中是具有一定厚度的圓盤狀,時效過程中,優(yōu)先沿直徑方向生長,而厚度幾乎保持恒定[22]。由于沉淀相與Al基體有多種取向關(guān)系,因此[110]Al平面上η'相的投影可以表現(xiàn)為圓盤狀或短棒狀[23] (圖4a)。如圖4b和c所示,隨著時效時間的延長,時效10和24 h后未增強合金中析出相的形態(tài)、尺寸和密度并無明顯差異,說明在不升高時效溫度的條件下,析出相的長大是非常緩慢的。因此,在較長的時效時間里,未增強合金能保持高硬度和高強度(圖2a和3a)。為了進一步分析析出相尺寸的變化規(guī)律,對各狀態(tài)下合金的析出相尺寸進行統(tǒng)計(圖4d~f)。時效2、10和24 h未增強合金的析出相平均尺寸分別約為2.88、2.97和4.02 nm。隨時效時間的延長,析出相尺寸緩慢增大,且尺寸分布均比較集中。
圖4
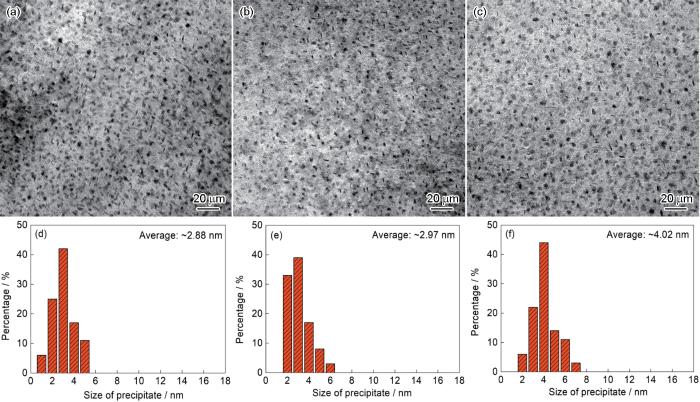
圖4 不同時效狀態(tài)未增強合金沿[110]Al方向的析出相形貌和尺寸統(tǒng)計柱狀圖
Fig.4 Precipitation morphologies (a-c) and size statistic plots (d-f) of Al-7.5Zn-2.8Mg-1.7Cu alloy under different aging treatment conditions taken along [110]Al zone axis (a, d) under-aged (120oC, 2 h) (b, e) under-aged (120oC, 10 h) (c, f) T6-treated (120oC, 24 h)
圖5為不同時效狀態(tài)復(fù)合材料沿[110]Al方向觀察的析出相形貌。復(fù)合材料中析出相的形態(tài)與未增強合金的基本相似,而相同時效條件下復(fù)合材料析出相的尺寸和兩相之間距離均比基體合金的更大(圖5a~c),說明SiC顆粒對沉淀相的析出和長大具有明顯的促進作用。如圖5d~f所示,在120℃時效2、10和24 h后復(fù)合材料析出相的平均尺寸分別約為4.01、5.45和6.87 nm。各時效狀態(tài)下復(fù)合材料析出相的尺寸分布均比未增強合金更加分散。一方面,SiC顆粒與Al基體之間的熱膨脹系數(shù)不同,熱變形加工或熱處理后可能在近界面基體內(nèi)引入錯配位錯,導(dǎo)致位錯增殖[24],位錯線可以引起析出相的異質(zhì)形核和優(yōu)先長大[25],導(dǎo)致析出相尺寸不均勻。另一方面,SiC顆粒也能引起基體中Mg元素分布不均勻[18],在Mg含量較高的區(qū)域,溶質(zhì)原子的高含量有利于MgZn2相的長大,也可能導(dǎo)致析出相尺寸不均勻。
圖5
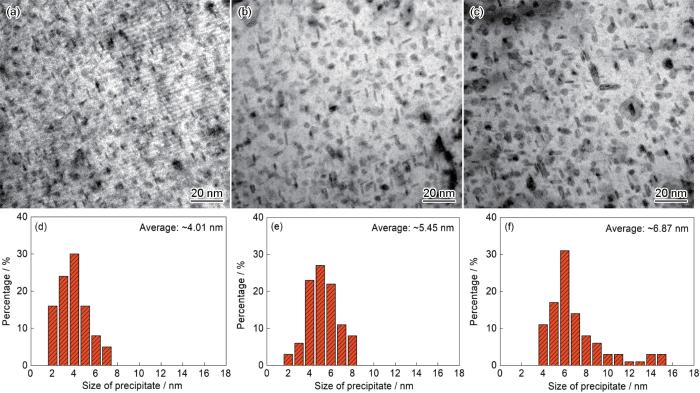
圖5 不同時效狀態(tài)復(fù)合材料沿[110]Al方向的析出相形貌和尺寸統(tǒng)計柱狀圖
Fig.5 Precipitation morphologies (a-c) and size statistic plots (d-f) of SiC/Al-7.5Zn-2.8Mg-1.7Cu composite under different aging treatment conditions taken along [110]Al zone axis (a, d) under-aged (120oC, 2 h) (b, e) under-aged (120oC, 10 h) (c, f) T6-treated (120oC, 24 h)
為了進一步分析各沉淀相的演變規(guī)律,固溶處理(470℃、2 h)后未增強合金和復(fù)合材料的DSC曲線如圖6所示。在23~500℃溫度區(qū)間內(nèi),未增強合金存在6個明顯的特征峰,而復(fù)合材料只有5個明顯的特征峰,這些峰對應(yīng)的溫度列于表1。
圖6
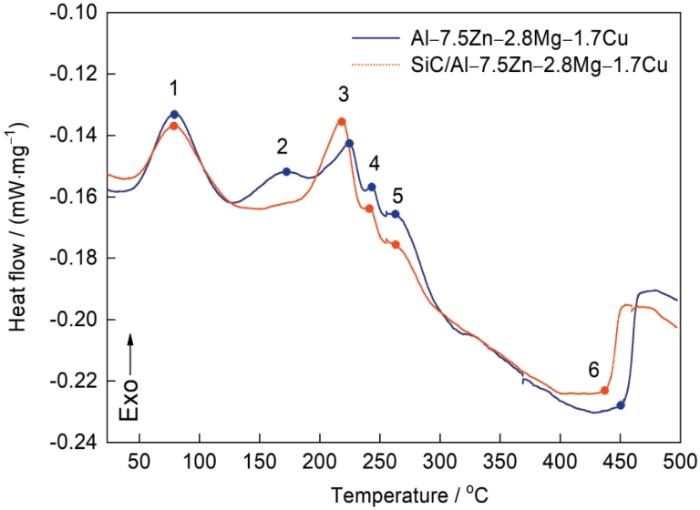
圖6 固溶態(tài)未增強合金和復(fù)合材料的DSC曲線
Fig.6 DSC curves of the solution treated (470oC, 2 h) unreinforced alloy and composite
表1 固溶態(tài)未增強合金和復(fù)合材料DSC曲線中各峰值點(見圖6)的溫度 (oC)
Table 1
Peak | Unreinforced alloy | Composite |
---|---|---|
1 | 79 | 79 |
2 | 172 | - |
3 | 224 | 218 |
4 | 243 | 240 |
5 | 262 | 262 |
6 | 450 | 438 |
根據(jù)已有研究報道[26,27],未增強合金中,峰1和峰2分別與GP區(qū)和η'相的形成有關(guān);峰3和峰4對應(yīng)的是2種類型η相的析出;對于峰5的分析目前沒有明確的結(jié)論,但是普遍認(rèn)為其可能與S相的形成有關(guān);峰6則是由η相溶解吸熱所形成的。與基體合金相比,復(fù)合材料中峰1有輕微的削弱,說明形成GP區(qū)的含量略有降低。峰2幾乎消失,說明復(fù)合材料中η'相的析出量極低,甚至可能沒有。但這與以往的研究結(jié)果不符,Wu等[28]認(rèn)為B4Cp/Al-Zn-Mg-Cu復(fù)合材料的時效析出序列依然與Al-Zn-Mg-Cu合金一致,即過飽和固溶體(SSS)-GP區(qū)-η'相-η相。也有研究[29]表明,部分η相的形核可以不經(jīng)過η'相,而是由SSS直接轉(zhuǎn)變而成,因此時效析出序列可能會被改變。而在SiC/Al-Zn-Mg-Cu復(fù)合材料中,η'相的析出進程很可能被加速,使得低溫時已有部分η'相形核。η'相以均勻的速度在復(fù)合材料中析出,集中放熱的現(xiàn)象被減弱,導(dǎo)致峰2不明顯。復(fù)合材料的峰3和峰6均向左平移,說明η相的形成和溶解動力學(xué)均被加速。
圖7所示為T6態(tài)(120℃、24 h)復(fù)合材料沿[110]Al方向的析出相HRTEM像和典型析出相的快速Fourier變換(FFT)花樣。在圖7a~c中,方框標(biāo)出的析出相與Al基體是非共格關(guān)系,該相為η相[7,26],其形貌為圓盤狀或粗棒狀。圖7d、f和g是對應(yīng)圖7a~c中指定區(qū)域的FFT花樣,可以明顯觀察到花樣中除Al基體的斑點以外還存在η相的斑點[30]。析出相形成過程中可能存在層錯,使得斑點有拉絲現(xiàn)象(圖7f)。橢圓標(biāo)出的析出相與Al基體是半共格關(guān)系,該相為η'相[26,30],其形貌多為細(xì)長的棒狀。圖7e為η'相的FFT花樣,由于η'相是過渡相,與Al基體的晶格錯配角較小,因此η'相的斑點較微弱[31],但是在η'相的高分辨像中可以觀察到晶格畸變和錯配現(xiàn)象(圖7a)。圖7c中圓圈標(biāo)出的析出相是與Al基體完全共格的GP區(qū),其形貌為小圓盤狀。圖7h顯示的是GP區(qū)的FFT花樣,花樣中只有Al基體的斑點,且GP區(qū)的高分辨點陣與Al基體完全共格。在T6態(tài)復(fù)合材料中,GP區(qū)、η'相和η相同時存在,且根據(jù)各相數(shù)量分析,其主要強化相為η'相。然而DSC曲線中代表η'相析出的放熱峰2十分微弱,這與在HRTEM下觀察到大量η'相的結(jié)果不符。由于SiC顆粒加入鋁合金基體中,引入了大量的界面和錯配位錯[6],為沉淀相提供形核質(zhì)點,促進異質(zhì)形核[18,22]。因此,部分GP區(qū)可能以異質(zhì)形核的方式優(yōu)先析出,隨溫度升高,另一部分GP區(qū)以均質(zhì)形核的方式析出,先后形成的GP區(qū)分別長大,并向η'相轉(zhuǎn)化。GP區(qū)向η'相的轉(zhuǎn)化過程被分散,導(dǎo)致復(fù)合材料DSC曲線峰2不明顯,但復(fù)合材料的時效析出序列未改變,仍為SSS-GP區(qū)-η'相-η相。
圖7
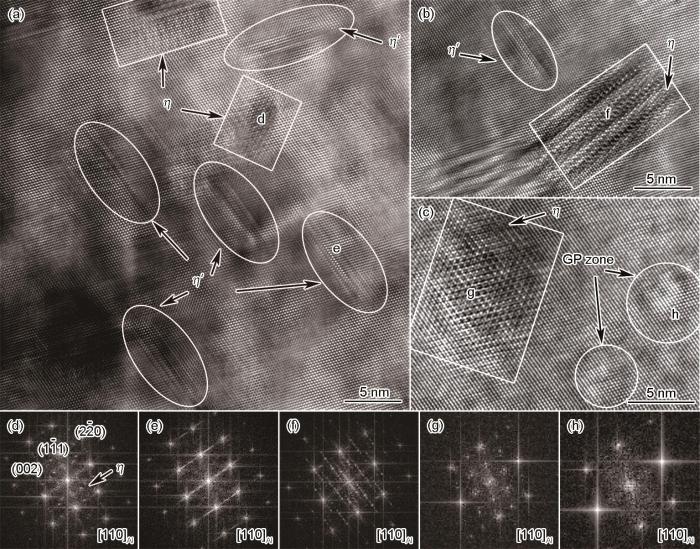
圖7 T6態(tài)復(fù)合材料沿[110]Al方向的析出相高分辨透射照片和快速Fourier變換花樣
Fig.7 HRTEM images (a-c) of the precipitation in the T6 treated composite taken along [110]Al zone axis, and the fast Fourier transformation (FFT) patterns (d-h) of the marked zone in the HRTEM images in Figs.7a-c
圖8顯示的是不同時效狀態(tài)未增強合金和復(fù)合材料晶界的TEM明場像。如圖8a和c所示,時效2 h的基體合金和復(fù)合材料晶界上均有明顯的第二相析出,且復(fù)合材料晶界相的數(shù)量更多一些。由于時效時間較短,晶界相的尺寸均較小。如圖8b和d所示,在時效24 h的未增強合金和復(fù)合材料中,晶界處無析出帶(PFZ)開始形成,其寬度分別約為41和38 nm。晶界相均是非連續(xù)的,且與欠時效態(tài)(120℃、2 h)材料相比,其尺寸和數(shù)量都有明顯增加。隨時效時間的延長,晶界相不斷長大。各時效狀態(tài)下,復(fù)合材料與未增強合金晶界的PFZ寬度差異不大,但是復(fù)合材料晶界相的數(shù)量明顯更多,這可能是由于晶界能量較高,容易引起析出相優(yōu)先析出和元素的偏聚[18],而復(fù)合材料中的錯配位錯加速了溶質(zhì)原子擴散,促進了晶界相的形核和長大[25,32]。晶界相的長大需要消耗周圍的溶質(zhì)原子,使得晶界附近溶質(zhì)原子貧化而形成具有一定寬度的PFZs。復(fù)合材料中溶質(zhì)原子擴散速率快,溶質(zhì)原子的補償能力強,因此在復(fù)合材料晶界相更多的情況下,PFZ寬度依然略低于未增強合金。晶界相(圖8d)的形成和SiC/Al界面反應(yīng)都將消耗部分溶質(zhì)原子,是復(fù)合材料晶粒內(nèi)部析出相密度降低的主要原因(圖4)。
圖8
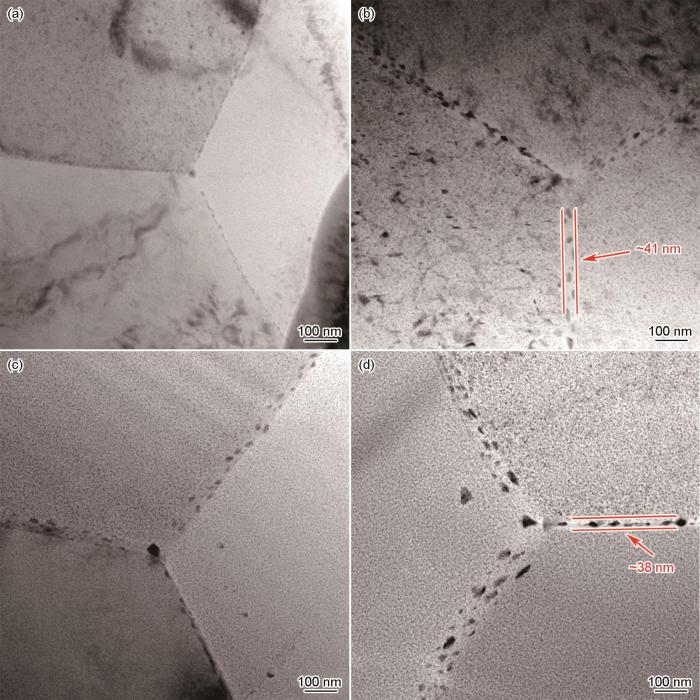
圖8 未增強合金和復(fù)合材料不同時效處理后晶界的TEM明場像
Fig.8 Bright-field TEM images of grain boundaries of the unreinforced alloy (a, b) and the composite (c, d) (a, c) aging 2 h at 120oC (b, d) T6-treated (120oC, 24 h)
綜上所述,相同時效條件下復(fù)合材料的時效析出進程明顯比未增強合金更快,SiC顆粒的加入促進析出相的析出和長大。時效2 h復(fù)合材料的沉淀相平均尺寸已達(dá)到4.01 nm,接近時效24 h未增強合金沉淀相水平。時效2~10 h,復(fù)合材料電導(dǎo)率上升明顯快于未增強合金,GP區(qū)向η'相的轉(zhuǎn)化速率被加快。由于GP區(qū)具有均質(zhì)形核和異質(zhì)形核2種形成方式,其析出過程存在先后差異,先形成的GP區(qū)迅速長大并向η'相轉(zhuǎn)化,η'相形成過程被分散,導(dǎo)致復(fù)合材料DSC曲線中η'相形成的放熱峰弱化,而在HRTEM下卻可以觀察到大量η'相。在未增強合金中,需要足夠高的溫度為原子的擴散和沉淀相的長大提供驅(qū)動力,各相的轉(zhuǎn)變過程受溫度影響明顯,且比較集中,沉淀相尺寸均勻性更高。而在復(fù)合材料中,錯配位錯加速了原子的擴散和相的轉(zhuǎn)變[25,32],使得低溫下GP區(qū)就有向η'相轉(zhuǎn)變的趨勢,短時間時效的沉淀相就可以快速長大。時效10 h,復(fù)合材料中固溶原子大量脫溶,達(dá)到了最佳硬化效果,屈服強度也達(dá)到最高值。延長時效時間,已形成的沉淀相繼續(xù)長大,也有少量新的GP區(qū)形成,沉淀相粗化和新相形成相互制約,使得時效10~24 h復(fù)合材料硬度存在波動。隨著溶質(zhì)原子的消耗,時效24 h的復(fù)合材料硬度達(dá)到了第二次峰值,由于沉淀相粗化,復(fù)合材料屈服強度略有降低,但此時沉淀相析出更充分,材料可以容納更多位錯,加工硬化能力的提升使得復(fù)合材料抗拉強度達(dá)到最大值。然而,在相同的時效條件下,與未增強合金相比,復(fù)合材料晶界處的第二相數(shù)量更多、尺寸更大,這些優(yōu)先形核并長大的第二相和SiC/Al界面反應(yīng)產(chǎn)物均可以減少基體晶粒內(nèi)部溶質(zhì)原子數(shù)量,抑制均勻形核,導(dǎo)致復(fù)合材料析出相密度降低。在本實驗中,T6態(tài)復(fù)合材料的強度與基體合金的相似,SiC顆粒并未表現(xiàn)出以往在2000和6000系基體合金中應(yīng)有的強化效果[33~35]。此前在低Mg的SiC/7085Al復(fù)合材料研究[18]中發(fā)現(xiàn),SiC/Al界面反應(yīng)消耗了基體中的Mg,減弱了復(fù)合材料沉淀強化作用,使得最終T6態(tài)復(fù)合材料強度低于7085Al合金。雖然本實驗中所選擇的基體Mg含量更高一些,SiC顆粒對復(fù)合材料沉淀強化的負(fù)作用被削弱,但是相比于未增強合金,T6態(tài)復(fù)合材料中析出相的密度較低,尺寸均勻性較差,仍然使得復(fù)合材料的強度優(yōu)勢不明顯。
3 結(jié)論
(1) SiC顆粒對復(fù)合材料的時效過程具有促進作用,復(fù)合材料的時效硬化速率比未增強合金更快,并且在時效10和24 h兩次達(dá)到其硬度最大值(238 HV),時效24 h的復(fù)合材料具有最高抗拉強度(663 MPa)。120℃時效24 h是適用于復(fù)合材料的T6熱處理工藝。
(2) SiC顆粒沒有改變Al-Zn-Mg-Cu合金的時效析出序列,仍為SSS-GP區(qū)-η'-η相,且在T6態(tài)復(fù)合材料中3種沉淀相同時存在,其中過渡相η'相是主要強化相。
(3) 粗大的晶界相和界面反應(yīng)產(chǎn)物均使得復(fù)合材料晶粒內(nèi)部溶質(zhì)原子被消耗,析出相密度降低。SiC顆粒引入的錯配位錯將促進析出相的形核和長大。因此,與T6態(tài)未增強合金相比,復(fù)合材料的析出相密度更低,尺寸更大。