分享:基于不同 α / β 團簇式比例的Ti-Al-V合金的鑄態組織和力學性能
鈦合金主要的相組成為hcp α-Ti結構和bcc β-Ti結構[1]。目前已經發展出系列近α、α + β雙相和近β工業牌號,其成分來自大量工業實踐,長期以來人們一直希望澄清這些成分的結構載體,以期實現合金的高效率研發。顯然,成分載體必然隱含于固溶體的特征結構——化學近程序,其模型化是結構科學的重要挑戰。但是,目前的合金設計方法,如Mo當量和Al當量[2,3]、元素作用[4,5]、d-電子理論[6]乃至第一性原理計算[7]等,均無法回答工業合金牌號成分的理論根源。關鍵在于長期以來一直缺失描述合金近程序的結構分析方法。建立α + β雙相固溶體結構模型,是解決工業鈦合金成分的結構根源和優化材料成分的關鍵。本課題組[8]提出了描述化學近程序的團簇加連接原子模型,已被成功應用到多種工業合金體系的成分設計中。該模型認為,任意一個結構的近程序都可以簡化成第一近鄰團簇加上若干個位于次近鄰的連接原子,表示為團簇式:[團簇](連接原子)。該模型根據組元相互作用模式,從化學近程序結構單元的角度,揭示了合金特定成分的結構根源,包含了體系中幾乎所有的關鍵信息,比如化學成分、平均原子密度、原子間化學結合鍵等,類似于分子的特點,可以被認為是合金的類分子化學結構單元,承載著合金的成分信息[8~12]。
Ti-6Al-4V具有α + β雙相結構,呈現出極好的綜合性能以及良好的工藝性,同時液-固兩相區較小,適合于增材制造,在航空工業、深海工程、生物醫用領域中得到了廣泛應用,其用量占鈦合金的50%[13~16],是先進制造領域的主體材料之一。值得關注的是,經過近70年的工程實踐,Ti-6Al-4V化學成分保持了高度的穩定性,說明該特殊成分的合理性。本課題組[1]前期以該模型為指導完成了Ti-6Al-4V的成分式解析,可以精確表述為:α-{[Al-Ti12](AlTi2)}12 + β-{[Al-Ti14](V2Ti)}5,其中α和β 2相的基礎結構單元分別為α-[Al-Ti12](AlTi2)和β-[Al-Ti14](V2Ti),前者團簇為配位數12的hcp孿晶立方八面體(twinned cuboctahedron,圖1a)加3個連接原子,后者為配位數14的bcc菱形十二面體(rhombic dodecahedron,圖1b)加3個連接原子,2者均以Al為中心、Ti為近鄰殼層。針對雙相鈦合金的雙團簇式模型的提出,不僅為理解各類鈦合金的成分規律奠定了基礎,同時也為進一步提高鈦合金性能指出了優化方向。通過改變兩相結構單元的比例以及各自合金化,可以全面覆蓋各類鈦合金,為理解現有合金乃至發展新成分提供了全新路徑。
圖1

圖1 hcp和bcc結構的第一近鄰團簇,分別為配位數為12的孿晶立方八面體和配位數為14的菱方十二面體,后者的第一近鄰由2層構成
Fig.1 Twinned cuboctahedron with coordination number of 12 (a) and rhombic dodecahedron with coordination number of 14 (b) as the nearest-neighbor clusters of hcp and bcc structures, respectively. The nearest-neighbor shell of the latter cluster is composed of two sub-shells
本工作基于滿足α-{[Al-Ti12](AlTi2)}17 - n + β-{[Al-Ti14](V2Ti)}n 的通式,通過改變β結構單元的個數(n = 0~17),探索組織覆蓋α到β的Ti-(3.19~7.45)Al-(0~12.03)V (質量分數,%)體系,獲得組織和性能演化規律,并找到性能優于Ti-6Al-4V的新成分。
1 實驗方法
1.1 成分設計
首先簡要總結Ti-6Al-4V成分式的解析流程[1]。依據不同退火溫度下α和β相成分,擬合出α相成分式為α-{[Al-Ti12](AlTi2)},共含有16個原子;β相成分式為β-{[Al-Ti14](V2Ti)},共含有18個原子。為進一步確定α和β結構單元的具體數目,將2種團簇視為2個半徑不同的硬球,合金結構視為2種硬球的空間堆垛,按照團簇共振模型,完成了Ti-6Al-4V的雙團簇式構建:α-{[Al-Ti12](AlTi2)}12 + β-{[Al-Ti14](V2Ti)}5,共包含有12個α-Ti結構和5個β-Ti結構,且結構單元的數目為17。所計算出的成分為Ti-6.05Al-3.94V,幾乎就是工業合金牌號的名義成分。
本工作設計了α-{[Al-Ti12](AlTi2)}17 - n + β-{[Al-Ti14](V2Ti)}n,采用改變n值 (具體見表1),初步探索了組織覆蓋α到β的Ti-(3.19~7.45)Al-(0~12.03)V系鈦合金的成分-組織-力學性能關系。在Ti-Al-V成分圖中,如圖2所示,所設計的合金成分精確位于α-{[Al-Ti12](AlTi2)}與β-{[Al-Ti14](V2Ti)}成分式之間的直線(紅色)上,區別在于合金成分由不同β團簇式個數所構成。表1給出了不同n時的實驗合金的名義化學成分(以下均為質量分數)、Mo當量和Al當量[3],以及通過JMatPro軟件模擬計算得到的合金液-固兩相溫度區間。由表1可以看出,隨β團簇式占比提升,即當n由0逐漸提升至17時,合金的Mo當量逐漸提高而Al當量則相應降低,并且合金的液-固兩相區范圍逐漸增大。合金液-固兩相區越小,表明該合金具有較高的熔體與固體結構的相容性,適合于增材制造[17]。本工作根據β結構單元的個數n的不同,試樣分別記為n0 (純α結構單元)、n1、n2、n3、n4、n5 (Ti-6Al-4V)、n7、n8、n12和n17。
表1 不同β團簇式個數n設計的合金化學成分以及Mo和Al當量、估算的液固兩相區
Table 1
Material code | n | Composition / (mass fraction, %) | [Mo]eq | [Al]eq | ?TL-S / oC |
---|---|---|---|---|---|
n0 | 0 | Ti-7.45Al | 0.0 | 7.5 | 4.9 |
n1 | 1 | Ti-7.16Al-0.82V | 0.6 | 7.2 | 4.9 |
n2 | 2 | Ti-6.87Al-1.62V | 1.1 | 6.9 | 4.7 |
n3 | 3 | Ti-6.60Al-2.41V | 1.4 | 6.6 | 4.5 |
n4 | 4 | Ti-6.32Al-3.19V | 2.1 | 6.3 | 9.4 |
n5 | 5 | Ti-6.05Al-3.94V | 2.6 | 6.1 | 13.3 |
n7 | 7 | Ti-5.53Al-5.45V | 3.6 | 5.5 | 20.7 |
n8 | 8 | Ti-5.28Al-6.14V | 4.1 | 5.3 | 24.3 |
n12 | 12 | Ti-4.30Al-8.87V | 5.9 | 4.3 | 31.8 |
n17 | 17 | Ti-3.19Al-12.03V | 8.0 | 3.1 | 35.1 |
圖2

圖2 Ti-Al-V成分圖,包含了設計成分、α-[Al-Ti12]Al1Ti2相成分式和部分β相成分式,其中所設計合金分布于連接α-Al2Ti14和β-Al1Ti15V2的直線上(紅色方塊)
Fig.2 Ti-Al-V ternary composition chart, where are marked the compositions of the designed series, α-[Al-Ti12]Al1Ti2, and some β formulas. The resigned alloy series lie along the straight line (in red) linking α-Al2Ti14 and β-Al1Ti15V2
1.2 材料的制備
實驗以純Ti (99.9%)、純Al (99.99%)和純V (99.99%)為原材料。第一步:首先將原材料放入超聲儀中進行酸洗和酒精清洗去除雜質后,采用Mettker Toledo AL204-IC型精密秤按比例稱重,隨后放置入ZHF-500型非自耗真空熔煉爐中,在高純Ar氣保護下,以工作電流為75~300 A進行熔化,反復熔煉5次,得到合金鑄錠。第二步:將合金鑄錠放置入ZHF-500型非自耗真空熔煉爐中,在高純Ar氣保護下,真空銅模吸鑄成直徑為6 mm的棒材。
1.3 表征方法
采用BX51光學顯微鏡(OM)和Supra 55掃描電子顯微鏡(SEM)進行顯微組織分析。OM和SEM試樣腐蝕劑為3%HF + 7%HNO3 + 90%H2O。采用D8 Focus X射線多晶衍射儀(XRD)進行物相分析,工作電壓和電流分別為40 kV和40 mA,掃描角度20°~80°,掃描速率4°/min。采用JMatPro軟件計算得到合金的液-固兩相溫度區間。采用XS64型密度計進行密度測試,測試結果取3次的平均值。采用Image-Pro Plus軟件對OM和SEM形貌圖(至少3張)進行α'馬氏體和β相體積分數的統計分析。
采用UTM5504-G電子萬能試驗機進行室溫拉伸實驗,加載速率為0.25 mm/min。試樣為標準拉伸試樣(標距為15 mm,直徑為3 mm)。測試結果取至少3個試樣的平均值。采用HVS-1000型Vickers顯微硬度儀進行硬度測試,載荷300 g,保載時間15 s,測試結果取至少12個位置的平均值。
2 實驗結果與分析
2.1 顯微組織
圖3為鑄態Ti-Al-V合金的XRD譜。可以看出,當n = 0~4時,僅觀察到α-Ti對應衍射峰,沒有發現β-Ti衍射峰。當n = 5時,Ti-6Al-4V合金的XRD譜中開始出現了β相衍射峰,由此可見,該合金位于顯著出現β相的臨界點。隨著n值逐漸增大,β相衍射峰逐漸增強,尤其是n12和n17合金的β相衍射峰十分明顯。這主要是因為該合金中含有較多的β相穩定元素V,促使在快速冷卻過程中大量β相在基體中得以保留。與淬火過程類似,在真空銅模吸鑄快冷條件下,原始β相完全轉變為α相+ α'馬氏體,隨著n增大,即β團簇式占比提升,α相逐漸減少而α'馬氏體數量顯著上升。當n = 12時,合金組織中α相完全消失,僅為β相和少量α'馬氏體。可見,該成分處于α相完全消失的臨界成分點。當n = 17時,合金此時已加入了大量β相穩定元素V (12%),而Al含量小于3.2%,可以使得高溫β相完全保留至室溫。相比于n0 (純α結構單元)合金,n17 (純β結構單元)合金中由于β結構單元完全取代了α結構單元,導致n17合金主要為單一β相,而n0合金以單一α為主。
圖3
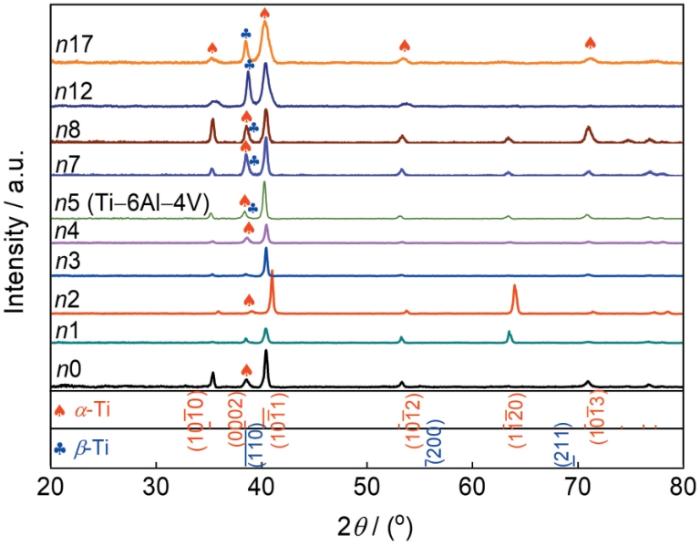
圖3 鑄態Ti-Al-V合金的XRD譜
Fig.3 XRD spectra of as-cast Ti-Al-V alloys
圖4為6種典型鑄態Ti-Al-V合金顯微組織的OM像。可以看出,隨n值增大,即β團簇式占比提升,α'馬氏體數量呈先上升后下降的趨勢,其形態由板條狀逐漸轉變為細片狀和針狀。這些真空銅模吸鑄快冷生成的α'馬氏體,其組織形態主要與合金元素含量有關。鄧安華[18]總結發現了鑄造快冷條件下鈦合金的α'馬氏體主要有2種組織形態,當合金元素濃度較低時,α'馬氏體形貌呈大板條狀;合金元素濃度較高時,α'馬氏體形貌呈針狀。這是由于β相穩定元素越高,導致相變過程中晶格重構的阻力越大,相變所需的過冷度也越大,越有利于針狀α'馬氏體的形成。從圖4b~d可以看出,β相主要分布于α'馬氏體相界,其形貌呈黑色短棒狀,基體α相呈白色帶狀。當n = 5時(圖4c)可以明顯觀察到黑色短棒狀β相。當n進一步提升至12和17時,α'馬氏體數量大幅下降,β相數量逐漸增多。圖4e和f的統計結果表明,n12和n17合金中β相的體積分數分別約為91%和98%。尤其當n = 17時,合金幾乎為單一β相組織。
圖4

圖4 典型鑄態Ti-Al-V合金的OM像
Fig.4 OM images of typical Ti-Al-V alloys of n1 (a), n2 (b), n5 (c), n8 (d), n12 (e), and n17 (f)
圖5為典型鑄態Ti-Al-V合金的SEM像。當n = 1時(圖5a),統計結果表明合金α'馬氏體體積分數小于1%。當n = 2~8時(圖5b~d),α'馬氏體含量則逐漸增加,其形貌由粗大板條狀(n2,圖5b)逐漸細化為細片狀(n5,圖5c)和細針狀(n8,圖5d),這與OM觀察結果一致。此外,n5合金(圖5c)的α'馬氏體相界處可以明顯觀察到β相。
圖5

圖5 典型鑄態Ti-Al-V合金的SEM像
Fig.5 SEM images of typical as-cast Ti-Al-V alloys of n1 (a), n2 (b), n5 (c), and n8 (d)
2.2 力學性能
圖6為所設計合金的室溫拉伸力學性能。其中,圖6a為室溫拉伸工程應力-應變曲線。從圖6b可以看出,當n從0逐漸提升至17,即β團簇式占比逐漸提升,合金的強度呈現先上升而后下降的趨勢,而塑性變化趨勢則相反。當n = 8時,合金的強度達到最大,抗拉強度(UTS)約為1019 MPa,屈服強度(YS)約為867 MPa,伸長率(δ)約為4.1%,其強度相比于n5合金提升了90 MPa,為n5合金的1.1倍,而伸長率則基本保持一致。這說明n5合金不是體系中最高強的點。當n為5~8時,包括n5合金在內的合金強度處于整個體系的高峰區;當n位于5~8兩側,即當n小于5或大于8時,合金則具有較高的塑性,越接近兩端,塑性則越高,n0 (純α結構單元)合金和n17 (純β結構單元)合金伸長率大于13%,是n5合金的3倍,強度則略降低。
圖6

圖6 鑄態Ti-Al-V合金的室溫拉伸力學性能
Fig.6 Room-temperature mechanical properties of as-cast Ti-Al-V alloys
(a) engineering stress-strain curves
(b) ultimate tensile strength and elongation
圖7為本工作鑄態合金與其他熱處理態Ti-6Al-4V合金[19,20]的性能對比。可以看出,本工作鑄態Ti-6Al-4V合金的室溫拉伸強度為925 MPa,與其他傳統熱處理態Ti-6Al-4V合金基本一致,但伸長率(4.3%)較差,這主要是因為該合金未經過任何熱處理,且真空銅模吸鑄快冷,導致形成較多的α'馬氏體,降低了合金塑性。此外,從圖7還可以看出,鑄態n7和n8合金的拉伸強度優于傳統熱處理態Ti-6Al-4V,尤其是鑄態n8合金具有最高的抗拉強度(UTS > 1000 MPa),有望發展出性能優于Ti-6Al-4V的新型高強合金。
圖7

圖7 鑄態Ti-Al-V鈦合金的室溫拉伸性能與其他熱處理態Ti-6Al-4V材料[19,20]對比
Fig.7 Comparison of mechanical properties between data (this work, as-cast, room temperature) with those of heat-treated Ti-6Al-4V materials[19,20]
Ti-Al-V合金強度的提高主要與固溶強化和第二相強化等強化效應有關。特別是,n8合金的顯微組織出現了大量細小的針狀α'馬氏體,這種細小針狀α'馬氏體不利于位錯滑移[14],有利于提高合金的強度,但會導致合金塑性較差。相比而言,n0和n1合金的組織幾乎呈現出單一α相(α'馬氏體體積分數小于1%);n17合金的組織幾乎呈現出單一β相(β相體積分數大于98%)和少量α'馬氏體組織。這種單相的α相或β相固溶體組織有利于提高合金的塑性,使得Ti-Al-V合金的伸長率大于12%。
圖8為彈性模量(E)變化趨勢圖。隨著n值從0逐漸增大至17時,E從140.2 GPa逐漸下降至77.8 GPa。n1、n2、n3和n4合金的E分別為130.7、126.0、125.5和124.9 GPa,均高于n5合金的117.6 GPa。一般而言,高的彈性模量表明這類合金具有較強的抵抗彈性變形能力,可以減少零部件的彈性變形。因此,n0合金具備高的塑性和高彈性模量(E > 140 GPa),可潛在應用于航空輕質薄壁金屬結構件。彈性模量隨n值增大而趨于下降與加入β穩定元素有關[21]。
圖8
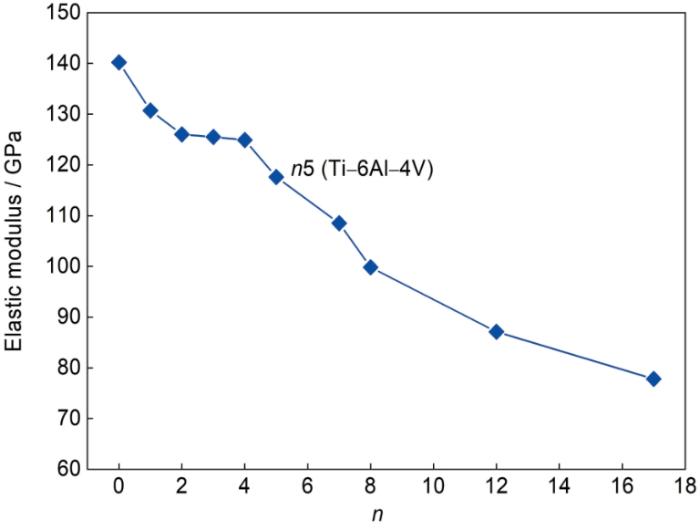
圖8 鑄態Ti-Al-V鈦合金的彈性模量
Fig.8 Elastic modulus (E) of as-cast Ti-Al-V alloys
圖9為鑄態Ti-Al-V鈦合金的Vickers硬度和質量密度以及相應比硬度(硬度/密度)和比強度(抗拉強度/密度)圖。從圖9a和c可以看出,Vickers硬度和比硬度隨n增大均呈先上升后下降的趨勢。其中,當n為8時,合金的Vickers硬度和比硬度均達到最高,分別為343 HV和0.76 GPa·cm3/g,相比于n5合金的硬度和比硬度(分別約為320 HV和0.72 GPa·cm3/g),該合金的Vickers硬度和比硬度分別提升了7%和5%。這主要是因為n8合金出現了大量細小的針狀α'馬氏體,而n5合金的組織主要為細片狀α'馬氏體,這種大量細小的針狀α'馬氏體組織可以有效提升合金的Vickers硬度。此外,Ti-Al-V合金的Vickers硬度變化規律與抗拉強度變化規律一致,2者數值關系近似滿足:抗拉強度(MPa) = 2.9H (H為Vickers硬度,HV)。
圖9

圖9 鑄態Ti-Al-V鈦合金的Vickers硬度和密度以及比硬度和比強度
Fig.9 Vickers hardnesses (a), mass densities (b), specific hardnesses (c), and specific strengthes (d) of Ti-Al-V alloys (Specific hardness denotes the hardness-over-density ratio, and specific strength denotes the ultimate tensile strength-over-density ratio, respectively)
從圖9b可以看出,理論質量密度和實驗質量密度值比較接近(誤差小于0.2%)。合金的理論質量密度(ρ)可以通過計算原子密度(ρa)獲得[22]:
從圖9d可以看出,比強度隨著n的增大呈先上升后下降的趨勢。鑄態n8合金的比強度最高達到了230 kN·m/kg,相比于同樣鑄態Ti-6Al-4V合金比強度(約為211 kN·m/kg),該合金的比強度提升了9%。此外,相比于文獻報道的擠壓態、軋制態鎂及稀土鎂合金[23]、軋制態鋁基復合材料[24]和熱處理態鋁合金[25]等各種輕質航空金屬結構材料(比強度小于180 kN·m/kg),鑄態n8合金的比強度是此類合金的1.3~3.4倍。
2.3 斷口形貌
圖10為鑄態Ti-Al-V合金的室溫拉伸斷口形貌。可以看出,各鑄態Ti-Al-V合金室溫拉伸斷口表面均呈現由解理斷裂、韌窩和撕裂棱組成的混合斷裂特征,而微裂紋主要沿解理面和撕裂棱的邊界分布。當n = 1時(圖10a和b),合金斷口存在較多的韌窩區,韌窩的產生可以有效釋放材料內部的內應力,合金表現出較高的塑性[26]。相比而言,n5 (圖10c和d)和n8 (圖10e和f)合金的斷口表面存在粗大的撕裂棱,而且撕裂棱分布相對集中。撕裂棱邊界容易產生位錯塞積,是微裂紋形核的主要形核點,將會導致材料的塑性降低。因而,n5和n8合金的塑性較差。當n = 12時,如圖10g和h所示,合金斷口的韌窩數量增加,而撕裂棱數量則明顯減小,合金的塑性得以提高。
圖10

圖10 鑄態Ti-Al-V鈦合金的室溫拉伸不同倍數斷口形貌
Fig.10 Low (a, c, e, g) and high (b, d, f, h) magnified fracture morphologies of as-cast Ti-Al-V alloys
(a, b) n1 (c, d) n5 (e, f) n8 (g, h) n12
3 結論
(1) 在團簇式框架內,在前期解析Ti-6Al-4V的雙團簇式通式α-{[Al-Ti12](AlTi2)}17 - n + β-{[Al-Ti14](V2Ti)}n 的基礎上,采用改變n值的方法,研究了Ti-(3.19~7.45)Al-(0~12.03)V系鈦合金成分-組織-力學性能關聯。隨n值增大,鑄態組織由單一α相逐漸轉變為α + α'馬氏體相、α + α'馬氏體+少量β相及β +少量α'馬氏體相。其中,α'馬氏體數量呈先上升而后下降的趨勢,且其形態由板條狀逐漸轉變為細片狀和針狀。當n為8時,α'馬氏體數量最多且其形態主要呈針狀;當n為5時開始出現β相,其數量隨n增大而逐漸增多;當n為12時為α相完全消失的臨界成分點。
(2) 隨β團簇式占比增大,室溫拉伸強度呈先上升后下降的趨勢,塑性的變化趨勢則相反,這源自細小針狀α'馬氏體提升強度而降低塑性的作用。當n為8時,合金的強度達到最大。當n為5~8時,包括Ti-6Al-4V (n5)合金在內的合金強度處于整個體系的高峰區;當n小于5或大于8時,合金具有較高的塑性,n0 (純α結構單元)和n17 (純β結構單元)合金的伸長率大于13%,是Ti-6Al-4V (n5)合金伸長率的3倍。
(3) 隨β團簇式占比增大,比強度和比硬度均呈先上升后下降的趨勢,彈性模量逐漸降低而密度逐漸增大。n8合金的比強度和比硬度均最高,分別達到了230 kN·m/kg和0.76 GPa·cm3/g,相比于Ti-6Al-4V (n5)合金分別提升了9%和5%。
(4) Ti-6Al-4V組織為α +細片狀α'馬氏體+少量β相,其UTS、YS、E及硬度分別約為925 MPa、793 MPa、117.6 GPa和320 HV,液-固兩相區約為13.3℃,密度約為4.38 g/cm3。相比而言,n8合金組織為α +大量針狀α'馬氏體+少量β相,其UTS、YS、E及硬度分別約為1019 MPa、867 MPa、99.8 GPa和343 HV,液-固兩相區約為24.3℃,密度約為4.42 g/cm3,特別是該合金的強度相比于Ti-6Al-4V (n5)合金提高了90 MPa,而伸長率與之持平,約為4%。
來源;金屬學報